快速换模的反思实践:快速换模在中小铸造企业的应用
Bikram Jit Singh和Dinesh Khanduja
国家技术学院,古鲁格舍德拉,印度
摘要
目的—本文的目的是发现快速换模在压铸铸造企业中的意义。
设计/方法/方法 -在不忽视铸造实际约束条件下,给出建立标准化设置程序的指示和指引。它以一个中等规模的活塞的铸造作为个案研究,产生一个设置减少的方法,利用工业工程的基本工具-快速换模技术,来实现更快的设置。它描述了快速换模方法在中小铸造企业实施的可行性。最后,本文进行快速换模经济效益实证分析。
结果 -准备活动是生产任何产品的产品提前期中的重要部分,因此影响到整体产品的成本。帕累托分析,因果分析和方法研究等这些工具已被用来分析现有生产过程。SMED方法可以帮助消除不必要的活动,外化内部活动,通过简化工序和标准化来减少活动。如5S,Poke-York和其他的一些方法的应用可以进一步减少操作时间。
意义- 本文通过SMED的实际应用证明了SMED方法对中小型铸造厂生产力的提高有很大的作用。
关键词 提前期,铸造工程,中小型企业,生产率,案例分析
简介
在这个全球化时代,实现“制造卓越”是任何国家的经济增长和生存的必要条件。 “工业时代”在上个世纪已经让位给“信息时代”,这在制造方面表现为提高产能(班纳吉,2000)和降低产品生产周期(CT)的(佩和Sohal,2001)。新技术的发展,精良的高生产系统和生产线的发展带来了新的生产时代。竞争,生产率和利润率成为与此技术相关的流行词。高技术成本要与高生产率和高柔性相适应。经济的持续增长刺激了产品的持续性产出,从而控制资源的投入和增加产品产出。换模时间是任何制造业的重要参数之一,也是每一台机器或者工作站必要的投入。因为前期准备是产品生产前的一系列准备活动,所以通过减少换模时间可以增加一台机器的生产时间。制造商需要更好地响应客户需求动态,以维持其对他人(Burman和格什温,1996)的竞争力。因此,“规模较小的经济生产批量”应该是一个关键的战略,以实现灵活和更短的生产前置时间。这只有在换模快速高效的前提下才可以实现。据Pannesi(1995年),更短的换模时间能给生产系统带来以下影响:
l 使小批量的生产变得可行;
l 减少配置浪费;
l 减少人工费用;
l 增加生产系统柔性;
l 降低产品的交货时间
l 提高产量和资产利用率
l 降低制造成本。
每一个设置有一个基本的“工作内容”,这是一个不可约活动的顺序组合。但与此同时,基本设置时间是根据生产的产品类型和生产系统的限制而定。忽视这个时间是不可能的,但是在实际中总是有更多的活动,如缺乏标准化的设置作为一个因素时,太接近公差,机械设计,参数设定,管理缺陷和人的局限。对于这些因素的存在,常见原因有:
l 不太重视这项设置区域,在生产计划和调度阶段的影响较少,多是在订单的执行中,在车间的生产过程中。
l 缺乏标准化的程序。在许多组织中,每个人往往按自己的方式进行生产 - 破坏了产品的质量和数量的成本。
l 关于快速转换技术的意识薄弱。还有一个关于知识的成本效益分析技术普遍缺乏。
l 内部管理和清洁的水平差。这是需要(尤其在模具铸造车间)推广5S概念。
l 需要花费很多时间来寻找工具,这造成了不必要的时间浪费和延迟。一个工具包应具有所有必要的工具,夹具和他们使用的具体管理条例。
据Womack和Jones(1996),为产品定制的要求会导致每一位顾客想要他的“个性化“的产品,所以只有能够满足这些市场变化的制造商才能生存。基于柔性制造和精益生产的对于一台机器或产线的转换时间缩短是具有成本效益的(长庚和Studel,1990)。
从量上看,每台机器的转换时间可以由以下三部分组成:方法,组织和生产的限制。“方法”是指在其中设置执行,应该由设计师提出的方法。标准化和简化,是一种理想的设置过程的特点。为了减少设置时间和非增值活动,线上活动应该调整为线下活动。为有效和高效的设置,明确的组织人力需要,以便在这些关键活动的每一个人都对他们各自的工作有所了解。
快速换模(SMED):转换时间减少的基本技术
Shingo,日本工业工程师,在1987年首创了SMED技术,当他将这个技术应用在马自达汽车成型压力机上时,成功的是换模时间缩短了57%。现在,SMED正在成为一个普遍的方法,它可以适用于任何行业,在其他一些工业工程工具的配合之下(赫尔利,2000;金,1997)。Shingo(2000)解释说,在将SMED应用到任何资源(机器或设备等)时,有必要分析目标资源是不是瓶颈资源。如果SMED应用到一个非瓶颈资源,那是因为非瓶颈资源已经过剩的生产能力闲置,并与工作价值有限。 SMED只应适用于瓶颈资源,具有较低的容量比要求,需要立即引起注意。在确定机器或设备的瓶颈,目前有关数据转换的时间,方法,设备或在设置窗口中使用的工具应该被收集。
SMED的三个步骤是:
1.在前一种产品生产后前期的准备活动就应该实施。为了改善这种状况,减少设置时间,活动应该分为离线和在线活动。脱机活动期间可进行产品的生产或事先随着目前的产品的生产进行活动。然后就节约了线上活动的时间。Shingo谈到(2000年),这一步通常可以产生一个比原先设定时间30-50%的缩减。
2.这一步的时候设置的分相动作已移交的工装模具或当卸载和一个新的阶段,是在给定的机器上安装开始。在这里,工作的重点是尽量外化线上活动。为达到这个目的主要是通过开展技术,修改设置。结果发现,这种做法可以减少75%的操作时间。
3.这是最后一步,最大限度地减少和简化在线和离线活动。 SMED可以用方法研究,价值流图,因果图分析或帕累托图等工业工程工具,以简化和规范所有后续活动(赵,2001)。这一步将生成一个标准的设置过程,它可以减少的设置停机时间占以前停机时间的百分之九十。
上述方法可以成功地应用到单机或者单个操作者。它不能被应用到工作站,两个或两个以上的操作者在同一台机器上工作或单个操作者在两个或更多的机器工作。例如,当两名工人在同一台机器上工作,工作需要这些人之间的平衡。如果一个工人工作时间的50%被简化,那么这并不意味着,该机器的整体停机时间就能够减少50%,因为剩余的活动都需要重新分配其他可用的人。在这种情况下,这只可能导致节约25%的时间。在这种情况下,我们需要活动图表,帕累托分析,因果分析等更多的工业工程技术与与SMED技术的集成。
将SMED应用到生产管理:以中小铸造企业为例
在印度制造业,工业产品中百分之九十五是在中小型企业(SME)生产的却,只有百分之四十的产值(印度时报,2002),这些企业的生产力水平低得惊人,由于很多的问题。制造业的生产的平均增长速度4.95%,而中国的是7.31%,新加坡为9.45%,巴基斯坦的为8.65%(印度时报,2005)。这反映了生产能力水平低,这包括故障处理和减少设置时间。在印度的典型行业的研发投入少于0.6%,而世界平均水平为2.5%(Garg等,2003)。在一个小单位,它在农业和机械行业的投资不足千万卢比(Singh等人,2003),生产力和盈利能力是必不可少的,以评估一个组织的绩效。 Singh等人 (2004)在他们的研究已经发现,成本和产品废品率因素是小企业的主要压力。这些单位缺乏竞争力的主要原因是技术和人员不足,专业知识(阿姆斯特朗和科伊尔,1999年)和资源匮乏削弱了它们的能力和国际化水平(摩恩,1999)。据普拉拉德和哈梅尔(1990)报告,一个单位的核心竞争力是建立在资产和无形资产上的,查斯顿也得到了这样的结论(2001年)。相关因素包括生产力,人力资源和全面质量管理(TQM)。在大多数中小型单位的业主,从一切可能的资源中投入资金,因此迫切希望增加各项盈利比率。不同于大型行业组织,增加利润和生产效率高成为了小型企业的唯一目标。诺布尔(1997)认为,目前小型和中等规模的企业有着与以往不同的目标。
一个个案研究,在Escort’s Piston Foundry at Bhadurgarh, India (a medium scale unit)开展的,以减少循环时间通过应用SMED,结果非常令人鼓舞。
方法
每月每台压铸机的数据类型设置回收时间从生产报告或部分从模具修理工作卡。设置了所有的同类机器的时间(表一),以便被机器识别。
总设置根据每月机种的时间而定。由此看来,平均设置时间为连续3个月。然后再次平均值设定为从设置有3个月特别值机器上发现。此值将移动贴近现实,从这个参数中可以找到瓶颈(图1)。我们观察到的MG -9机(16号),需要的最大时间(57.7%的总时间用于设置)为每月(表二)设置时间。在识别出瓶颈机后,我们着手了解设置程序。MG-9号机的研究任务被分配到每个人。时间研究是用来确定行动的实际时间。主要活动分为轻微活动和子活动。一台机器的设置一样转换成四个主要活动,换模活动,工艺参数设置,试运行及模具重新调整活动。这些主要活动是更小的活动和工作内容。从这个研究中,实际建立时间而定。会议决定,时间应进行研究,至少在两个个案,然后找到一个平均值作为实际时间。

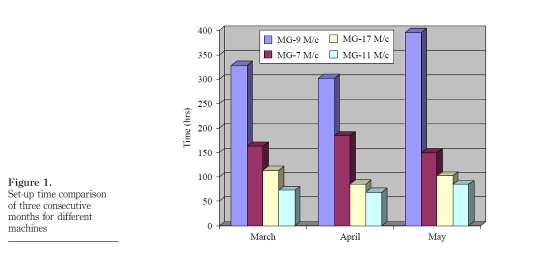
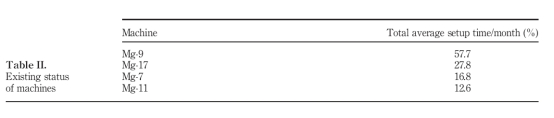
成本分析
MG-9机的总设置成本,包括劳动力成本,生产成本和能源成本。成本分析如下:
平均天数/月= 25天(大约)
平均设置时间= 342小时/月(57.7%)
= 342/ 8 *3 =14.2天/月或14天/月:
(1)劳工成本(见表三):
总劳动设置成本/月=14 *2388* 3 = 100296
(2)遗失的生产成本。总成本费用,机器计算为1136520/月。这个成本如下图所示:
l平均每班铸造活塞数= 66(对Mg- 9机)
平均每天铸造活塞数= 66* 3 =198
生产损失(由于设置)=198 *14 =2772活塞
一个活塞的平均费用(MG- 9)=410
2772活塞活塞的总费用113.652万
(3)能源成本。 1高频电(65千瓦)的消费为120单位/班,所以10小时高频在一天消耗3600单位。作为一个单位成本3.8,因此,能源成本为3.8 *3600* 14,即191520卢比/月。液化石油气成本10736卢比/月。电力设备运行费用是每月8778卢比,在一个以消费为55个单位转移成本3.8卢比/unit。因此,总能量消耗卢比 211034。因此,净成本=100296++211034+113.652万=1447850卢比/月,这是一个很大的设置对于MG- 9机的成本。因此,这些机器都理所当然地确定一个时间削减计划。
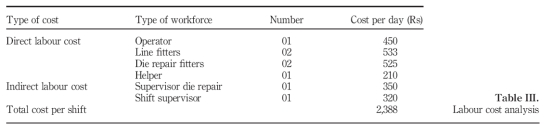
设置分析
该设置MG-9半自动压铸机,就是一个连续的过程,涉及的活动和次活动。这些都是大致分为三大类:在时间,关断时间和改善时间活动。上一次活动是那些可以被执行,当机器已经停止或等待。关断时间的活动可以进行,而机器正在工作。改善时间的活动是关断时间的活动后,机更换为新的产品类别。在设置MG- 9机程序的情况下,关断时间设置的活动包括在初始阶段,模具的加工参数验证检查。上一次交流活动,包括零部件及工艺参数和改进活动设置时间试运行,机器的变量调整组成。详细秒表两个设置案件进行了研究并作出一个明确的迹象,其中活动或子活动需要多少时间。数据还收集了有关哪个部门各自的活动,机器状态,责任人及工具/机械用于执行上述各项活动。
为了分析在基层的现行程序,综合分析表的目的是要区分每个在它的概率被淘汰活动,简化和/或外部化。这SMED分析载于附录1,表人工智能。从SMED分析,这些活动需要立即引起注意,可以给突破成立时间缩短,也可以确认。
图2显示了明显的信息就在不同的时间设置的消费活动。这个帕累托图,找出瓶颈,应被视为第一优先的活动和所有的设置应采取的,因为他们,各自设置时间照顾活动。此图还表明,活塞模具转换活动采取十项平均12小时,这一点必须减少。二,模具的调整需要过程,因为它的笨拙和不规范的维修活动需要八到十小时。然后,试运行,并围绕四个3.5小时,分别需要的参数设置。据研究发现,人类的随意性由于缺乏激励和监督控制也产生约1.5-2.5小时的时间浪费。
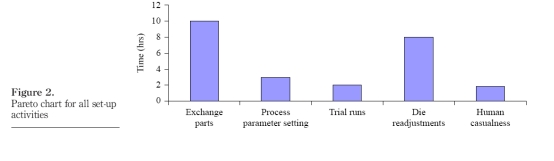
这需要为工人和主管制订适当的培训方案,以帮助他们树立减少安装时间的意识。
在对活塞的交接活动,重点对MG- 9机模具,转换分为可行的分项活动,如图3所示。模具有五个主要部分,分别有自己的安装方法。帕累托图给出了时间的价值需要做的每个转换,每一个模具部分。
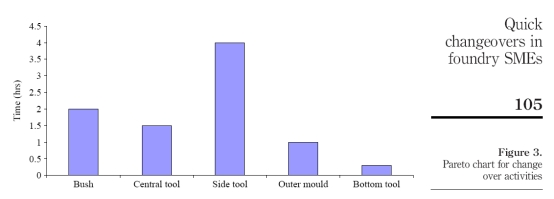
为了减少更换时间,很显然,端工具装配装修和程序中插入的床身中部套圈应予改善。为了更深入地对活动进行分析,一个根本原因分析可以帮助确定(并降低)不想要的设定时间,由于现有程序的技术限制,或因为未受过训练的操作者。
结果
通过SMED表帮助活动的分析表明。一组,不同的图形表示转换的UPS模具零件有助于清楚地表明需要立即关注的领域,并帮助确保在表四所示的成就。

这些结果可节省时间为48%左右,可显着只有在取得了不同的模具零件转换。
第二大集活动是模具重新调整,这关系到总设置时间的那8-10个小时。这是一个进步阶段设置,其中包括分必须符合前缀过程和产品规格的活动。模具安装后,五个活塞铸造作为试运行。第五活塞发送到各种维和铸造缺陷检查部门核查。对检查报告的基础上进一步调整压铸活动计划。这可能需要更少的时间,如果一个缺陷是可以预防的钳工阶段,否则可能需要九至十个小时,如果需要进行重大重新的模具调整。然后换模具,需要发送到初步分析的缺陷及其处理模具修复部分。同样,在第五个活塞的报告,决定是否要修理的机器模具或将其发送到进一步必要的模具修理部分。这个过程一直持续到模具由检验部门通过。各种内部和外部参数,这给贡献的设置过程,在做模具,调整活动,也分析了一个根本原因的结论是研究和总结于表五
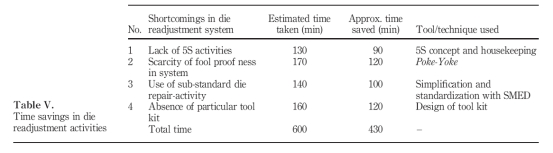
所需设备
为了验证并集产品和工艺参数,需要下列设备:
仪器和仪表,联系测温仪,浸泡高温计,游标卡尺,塞尺,螺距规,磨床,钻床(电动/气动),转速表,润滑剂和高度计(如果可能的话)等备件。备件的压铸机,U型耦合器,垫片,坩埚,柔性管,水管,接头,继电器,螺线管阀,液压缸密封件,O型圈,连接shimes缸杆,冲头,老板销(准备适合),管件,减速机,工会,六角耦合,单向阀,压力控制阀等
紧固件。螺栓 -M8的,M10的,M12的,M13的,M15中,M20的;铆钉(钢和塑料),木钉,管钳等这个集合将被证明是一个完整的工具包就换模设置程序是基于半自动压铸机关注。这将确保由钳工很方便拿到所需物品。这将节省一个或一个半小时,每天工作时平均法计算。
73%的模具调整时间的节约。
与现有的设置比较
从表六,据观察,这是可行的,应用SMED获得了48%的时间节约。经过目前的设定步骤逐步分析,以更有效和高效率的方式做设定同同一台机器换模(在大约一半的时间)的UPS可以识别。建议的系统提供比现有的设置系统的显着优势,显著提高生产率。
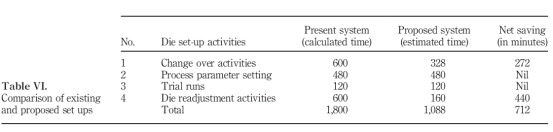
结论
为了实现“卓越制造“,中小企业必须利用一切可用的决策支持系统,以提高生产力,补充生产计划。由于生产力和盈利能力应该在当今的动态和竞争环境的可持续发展水平的主要指标,SMED提供了很大的潜力来降低循环时间以及提高竞争力。为了使这样的改进,如时间学习,帕累托图,因果分析,成本效益的技术,工业工程等工具可以用来识别所需的更改,淘汰赛和设置活动externalizations,然后更仔细的调校可开发以节省生产时间。附录2,表的AII给出了用于改善现有的设置提出了一些补救措施的各种技术的详细说明。有显著的节约整体的循环时间,这提高了该组织的生产力和盈利水平。