REFLECTIVE PRACTICE
SMED: for quick changeovers
in foundry SMEs
Bikram Jit Singh and Dinesh Khanduja
National Institute of Technology,
Kurukshetra, India
Abstract
Purpose – The purpose of this paper is to uncover the significance of quick changeovers in die-casting foundry environments.
Design/methodology/approach – The paper gives set-up instructions and guidelines to prepare the standardized set-up procedure without ignoring actual constraints in foundries. It uses a case study in a medium scale piston foundry to generate an integrated set-up reduction approach, utilizing single minute exchange of die (SMED)-based industrial engineering tools to achieve faster set-ups. It describes the feasibility of quick changeovers in foundry small and medium enterprises based on a “SMED” approach. Finally, the paper carries out empirical analysis of the financial/non-financial benefits incurred from set-up reductions.
Findings – Set-up activities are a vital part of the production lead-time of any product and so affect overall product cost. Tools like Pareto analysis, root-cause analysis and method study have been used to analyze the existing procedure of set-ups . A SMED approach can help eliminate unwanted activities, externalize the internal activities, if possible and reduce them by simplification or standardization. The application of other tools such as 5S, Poke-Yoke and specific tool-kits are suggested to further reduce set-up times.
Originality/value – The paper demonstrates the practical application of SMED showing how it can bring real breakthroughs in productivity to small and medium scale foundries.
Keywords Lead times, Foundry engineering, Small to medium-sized enterprises, Productivity rate
Paper type Case study
Introduction
Achieving “manufacturing excellence” is essential to survival and economic growth for any country in this age of globalization. The “industrial age” of the last century has given way to the “information age” which in manufacturing terms enhances capability (Banerjee, 2000) and reduces product cycle times (CTs) (Perry and Sohal, 2001). The development of new technology, sophisticated high-production systems and assembly lines has ushered in a new era in manufacturing. Competition, productivity and profitability are the buzz words associated with this technological turbulence. High technology costs are to be justified with higher rates of productivity and flexibility. Productivity can be enhanced by exercising economy at all levels of the organization, thereby controlling the quantity of resource inputs as well as by increasing outputs with the same or reduced levels of inputs. Set-up time is one of the vital parameters used in any manufacturing industry and is a form of necessary input to every machine or workstation. Because set ups are a collection of sequence dependent changeover activities which are carried out before starting the production of any product, so productive time for a machine can be increased by reducing its set-up time. Manufacturers need to be more responsive to the dynamic customer demands to maintain their competitive edge over others (Burman and Gershwin, 1996). So “economical production of smaller lot sizes” should be a key strategy to achieve flexible and shorter production lead-times. This is possible only if changeover becomes quick, efficient and foolproof. According to Pannesi (1995), shorter set-ups bring the following impacts to any type of production system:
l make feasible the production of smaller lots;
l reduce set-up scrap;
l decrease set-up labour cost;
l make production system flexible;
l reduce product lead time;
l enhance productivity and utilization of assets;
l reduce manufacturing cost.
Every set-up has a basic “work content” which is a combination of sequence of irreducible activities. The time this takes is known as basic set-up time and depends upon the type of product to be manufactured and its production system constraints. It is not possible to escape from this time, but in actual practice there are almost always additional activities, which inflate the set-up time as a result of factors such as lack of standardization, too close tolerance, design of machine, measurability of set-up parameters, management fallacies and human limitations. Common reasons for the existence of these factors are:
l Less emphasis is being paid to this set-up area and consequently less effort is made at the production planning and scheduling stage, resulting in haphazard way of execution of different orders in the shop floor.
l Lack of standardized procedures for set-ups. In many organizations, every person tends to do the set-up in his own way – undermining the cost of quality and quantity of product.
l There is little awareness about the quantitative techniques that can be used to calculate requirements of having shorter changeovers. There is a lack of knowledge on the part of concerned persons about the impact and importance of shorter setups. There is also a general scarcity of knowledge about the technique of cost-benefit analysis.
l Poor level of house keeping and cleanliness. It is needed to implement the 5S concepts on shop floor especially in die-repair section of foundry.
l The non-existence of special tool-kits for set-up fitters causes unwanted and unexpected delay in set-ups. A tool kit having all necessary tools, fixtures and spares managed in specific sequence of their use is urgently needed to make available the required set-up tooling on time.
According to Womack and Jones (1996), a requirement for heavy customization of product causes every customer to want his “bells and whistles” on the product, so only those manufacturers who can meet these ever-changing demands from the market can survive. The reduction of set-up times of a machine or line is a cost effective contribution to flexible and lean manufacturing (Gung and Studel, 1990).
Quantitatively, set up time for every machine can be defined as the function of three major elements: method, organization and production constraints. “Method” refers to the way in which the set-up is performed and should be suggested by the designer. Standardization and simplification are the characteristics of an ideal set-up procedure. To reduce set-up time, non-value adding activities should be avoided and online activities should be externalized to off line. For effective and efficient set-ups, clear organization of manpower is needed so that everybody involved in these crucial activities knows about their respective jobs and authorities.
Single minute exchange of die (SMED): basic technique for set-up time reduction
Shingo, a Japanese Industrial Engineer, developed the sophisticated technique of SMED in 1987 when he applied this technique to large body molding presses at Mazda Automobile Industry and successfully achieved 57 per cent of set-up time reduction. Now, SMED is becoming a universal approach, which can be made compatible to any type of industry with the use of some additional industrial engineering tools (Hurley, 2000; Kim, 1997). Shingo (2000) explained that before applying SMED to any resource (machine or equipment, etc.) it is necessary to analyze the targeted resource from the theory of constraints point of view which distinguishes the given resource as a bottleneck or non-bottleneck resource. If SMED is applied to a non-bottleneck resource, then it is of limited value because non-bottleneck resources are already idle and working with excess capacities. SMED should only be applied to bottleneck resources that have lower capacity than required and need immediate attention. After identifying the bottleneck machine or equipment, data regarding present changeover duration, method, equipment or tools used during set-ups should be collected.
Three steps in SMED are:
1. Often all set-up activities are carried out after the production of prior product. To improve this situation and reduce set-up times, activities should be divided into off-line and online activities. Off-line activities can be carried out during the production of prior product or along with the production of present product and off-line activities are performed after production of prior-product. Then set-up down time is restricted to the time taken to carry out these online activities. According to Shingo (2000), this step can typically yield a reduction in set-up time from 30 to 50 per cent of the previous set-up time.
2. This step commences when set-up moves from split phase to transferred phase of tooling or when a die is uninstalled and a new die is installed on the given machine. Here, effort is focused on externalizing the online activities as far as possible. This is achieved mostly by carrying out technical modifications to set-up processes. It is found that reduction in set-up times can go up to 75 per cent with such an approach.
3. It is the final step, which minimizes and streamlines the online and off-line activities. SMED can use some industrial engineering tools like method study, value stream mapping, cause and effect analysis or Pareto charts to simplify and standardize all the set-up activities (Chao, 2001). This step generates a standard set-up procedure, which may reduce set-up downtime up to 90 per cent of total previous set-up time.
The above approach can be successfully applied to single machine and single operator situations. It cannot be applied to a workstation, where two or more operators are working on the same machine or a single operator is working on two or more machines. For example, when two workers are working on the same machine, work is required to be balanced between these persons. If 50 per cent of the time needed by one worker is eliminated, then it does not mean that overall downtime of the workstation is reduced by 50 per cent, because the remaining activities are needed to be re-assigned among available persons. In this case, this can lead to a reduction of 25 per cent only. In such situations, we need integration of industrial engineering tools like multi-activity charts, Pareto analysis, cause and effect analysis, etc. with SMED technology.
Implementing SMED for productivity management: a case study of foundry SME
In India, 95 per cent of industrial units are in the small and medium enterprises (SME) sector with 40 per cent value addition in the manufacturing sector (Times of India, 2002) and in these units productivity levels are alarmingly low due to a host of problems. Average growth rate of productivity in manufacturing for India has been 4.95 per cent in comparison to 7.31 per cent for China, 9.45 per cent for Singapore and 8.65 per cent for Pakistan (Times of India, 2005). This reflects a low utilization of productive capacity and this includes a failure to address and reduce set-up times. A typical industry in India spends less than 0.6 per cent on average, of its turnover on R&D as against the world average of 2.5 per cent (Garg et al., 2003). In a small unit, which has investment in plant and machinery of less than rupees 10 million (Singh et al., 2003), productivity and profitability are indispensable to assess the performance of an organization. Singh et al. (2004) in their study have observed that a reduction in cost and product rejection rate are among the main pressures on small units. The main barriers to being competitive for these units are inadequate technologies and poor human expertise (Armstrong and Coyle, 1999) and scarcity of resources impairs their ability to internationalize (Moen, 1999). According to Prahlad and Hamel (1990) core competencies of a unit are built on intangible assets and as per Chaston et al. (2001), basic related areas are unit productivity, human resources and total quality management (TQM). The owners, in most of the small and medium units, invest money from all possible resources and hence are desperate to increase various profit ratios. Unlike for big industrial organizations, increased profits and high production rate become the only primary objectives for most of the small units. Noble (1997) suggests that present small and medium scale industries have different objectives than those in the past.
A case study was carried out at Escort’s Piston Foundry at Bhadurgarh, India (a medium scale unit) to reduce product CT by implementing SMED technique in the integrated manner and the results were highly encouraging.
Methodology
Set up time data for each type of die casting machine per month was recovered from the production reports or from the job cards of die repair section. Total set-up time of all the machines of same kind (Table I) are added and the availability of machines for production is identified.
The total set-up time of one kind of machine per month is identified. From this, the average set-up time for the specific machine is calculated for consecutive three months. Then again the average value of set-up for a particular machine from the set-up values of three months is found out. This value will move close to reality and from this parameter the bottleneck machine can be identified (Figure 1). It is observed that MG-9 machine (16 nos.) takes maximum time (57.7 per cent of total production time) as a set up time per month (Table II). After identifying the bottleneck machine, we set about understanding the set-up procedure. The whole set up activity of MG-9 machine is divided in terms of time phases. Time study was is used to identify actual times for operations. Major activities are divided into minor activities and sub activities. The set-up of a machine is divided into four major activities like changeover activities, process parameters setting, trial runs and die re-adjustment activity. These main activities are sub divided into a number of smaller activities and work contents. From this study, the actual set-up time is identified. It was decided that the time study should be undertaken on at least two cases and then an average value found out for actual set-up time.

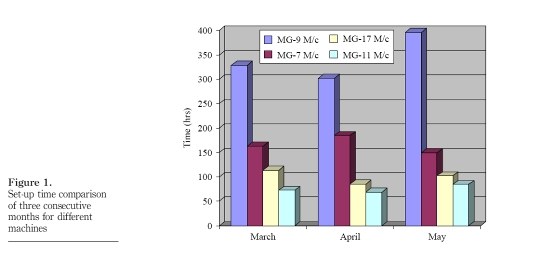
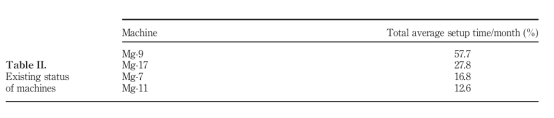
Cost analysis
The total set-up cost has been calculated for Mg-9 machines, which is a function of set-up labour cost, lost production cost and energy cost. The cost analysis is as under:
Average number of days/month=25 days (approx.)
Average set up time=342 hours/month (57.7 percent)
= 342/8*3=14.2 days/months or 14 days/month:
(1) Labour cost (see Table III):
Total labour set-up cost/month =14 *2,388 *3=Rs. 100,296.
(2) Lost production cost. The total cost incurred due to lost production on Mg-9
machines was calculated to be 1,136,520/month. The breakup of this cost is
shown as below:
l Average number of pistons casted per shift=66 (on Mg-9 machines).
l Average number of pistons casted per day = 66 * 3=198.
l Lost production (due to set up) =198 *14 = 2,772 pistons.
l Average cost of one piston (cost an Mg-9) =410.
l Average cost of 2,772 pistons= Rs. 1,136,520.
(3) Energy cost. Electricity consumption of 1 H.F. (65 kilowatt) is 120 units/shift, so
10 H.Fs consume 3,600 units in a day. As one unit costs Rs. 3.8, so energy cost
for set up would be 3.8 * 3,600 * 14, i.e. Rs. 191,520/month. LPG cost is
estimated as Rs. 10,736/month. Electricity cost to run machines per month is
estimated at Rs. 8,778 taking consumption in one shift as 55 units and cost as
Rs. 3.8/unit. So total energy cost is Rs. 211,034.
Therefore, net cost = 100,296+ 1,136,520 + 211,034 =Rs. 1,447,850/month and this
is a considerable set-up cost for MG-9 machines. So, these machines are rightly identified for a set-up time reduction programme.
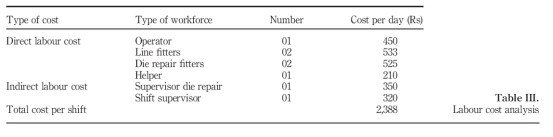
Set-up analysis
The set-up of Mg-9 semi-automatic die casting machines is a sequential process involving a number of activities and sub-activities. These are broadly divided into three major categories: On-time, off-time and improvement-time activities. On-time activities are those which can be executed when the machine has to stop or wait. Off-time activities can be performed while the machine is working. Improvement time activities are a sort of off-time activity after changeover of machine to new product. In case of set-up procedure of Mg-9 machines, off-time set-up activities include die checking at initial stage and verification of machine parameters. On-time activities include exchanging of parts and setting of process parameters and improvement time activities consist of trial runs and readjustment of machine or die variables. Detailed stop-watch study of two set-up cases was carried out and the data give a clear indication of which activity or sub-activity takes how much time. Data were also collected relating to which department was involved in the respective activities, machine status, persons responsible and tool/machinery used to perform these various activities.
To analyze the existing procedures at the grass-root level, a comprehensive analysis table was designed to differentiate each and every activity on the probability of it being eliminated, simplified and/or externalized. This SMED analysis is shown in Appendix 1, Table AI. From the SMED analysis, activities which need immediate attention and can give breakthrough reduction in set up time can also be recognized.
Figure 2 shows obvious information regarding the consumption of time during different set-up activities. This Pareto chart tends to find out the bottleneck activities which should be treated first and prioritizes all set-up activities which should be taken care of because of their-respective set-up times. This chart also shows that changeover activities of piston dies take an average of ten to 12 hours and this must be reduced. Second, die readjustment requires eight-ten hours because of its clumsy procedure and non standardized die repair activities. Then the trial runs and setting of parameters required around four and 3.5 hours, respectively. It has been found from time studies that human casualness due to lack of motivation and supervisory control also generates the time wastage of around 1.5-2.5 hours.
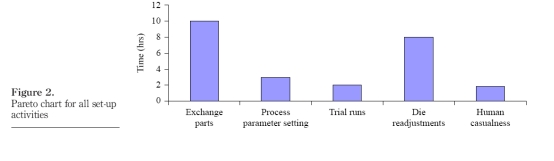
This requires an appropriate training programme for workers and supervisors, to help make them aware of the significance of setup time reduction.
In focusing on the changeover activities of piston dies on MG-9 machines, changeover is divided into feasible sub-activities as shown in Figure 3. Die has five major parts, which have their own methods for installations. This Pareto chart gives the value of time needed to do the changeover of each and every die part.
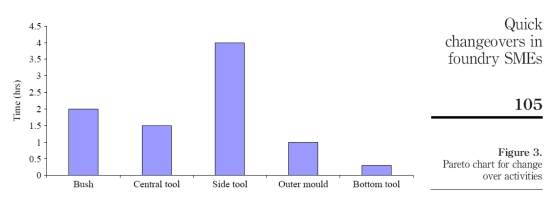
To reduce exchange time, it is clear that Side tool assembly fitment and procedure to insert ring in central bush of machine bed should be improved. For deeper analysis of sub activities, a root cause analysis can be performed to help identify (and reduce) the unwanted set-up time due to the technical constraints of existing procedure or simply because of untrained operators.
Results
Analysis of set-up activities with the help of the SMED-table suggests further analysis. A graphical representation of set-ups of different changeover die parts helps to clearly indicate the areas needing immediate attention and helped secure the achievements shown in Table IV.
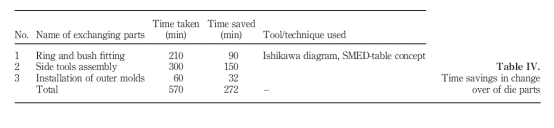
These results are quite significant as around 48 per cent of saving in time can be
achieved only in changeover of different die parts.
The second largest set-up activity is die re-adjustment, which contributes around eight to ten hours of total set-up time. It is an improvement phase of set-up which includes sub-activities required to meet prefixed process and product specifications. After die installation on machine, five pistons are casted as a trial run. The fifth piston is sent to the inspection department for verification of various dimensional and foundry defects. On the basis of the inspection report further die-readjustment activities are planned. It may take less time if a defect is preventable at line fitter stage otherwise it may take up to nine to ten hours if it requires major re-adjustment in die. Then the die is sent to the die-repair section for initial analysis of the defect and its treatment. Similarly on the report of the fifth piston, it is decided whether to repair die right on to the machine or to send it to the die repair section for further necessary treatment. This process continues until the die is passed by the inspection department. Various internal and external parameters, which give contribution to the set-up process while doing die-readjustment activities, are also analyzed with a root-cause study and the conclusions are summarized in Table V.
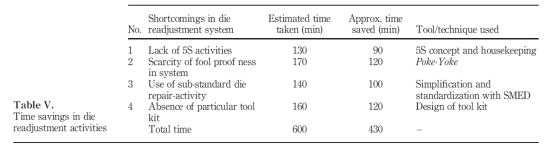
Equipment needed
In order to verify and set product and process parameters, the following equipment is needed:
. Instruments and gauges. Contact pyrometer, immersion pyrometer, vernier caliper, filler gauge, pitch gauge, baby grinder, drill (electrical/pneumatic), tachometer, lubricator and height gauge (if possible), etc.
. Spare-parts. Spares of casting machines, U-shape couplers, spacers, crucibles, flexible pipes, water-pipe, couplings, shimes of different widths, relays, solenoidal valves, hydraulic cylinder seals, O-rings, connecting cylinder rods, punches, boss pins (ready to fit), pipe fittings, reducer, union, hexagonal coupling, check valves, pressure control valves, etc.
. Fasteners. Bolts – M8, M10, M12, M13, M15, M20; rivets (steel and plastic), dowel, pipes clamps, etc.
This collection would prove to be a complete tool kit as far as die set-up procedure is concerned on semi automatic die casting machines. This will ensure the easy access of badly needed items by fitters. It will save up to one-and-a-half hours in daily working when calculated on average basis.
A total of 73 per cent saving in time in die readjustment activities has been estimated.
Comparison of proposed setup with existing setup
From Table VI, it is observed that it is feasible to attain up to 48 per cent (max.) of set-up time reduction with the positive utilization of SMED methodology integrated with various industrial engineering tools. After a stepwise analysis of present set-up procedure, more effective and efficient way to do set-ups of same die on given machine (in approximate half the time) can be identified. The proposed system offers a significant advantage over the existing set-up system and offers significantly enhanced productivity.
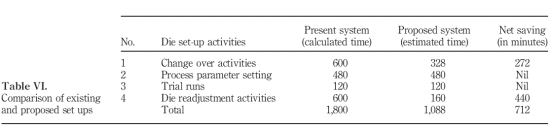
Conclusions
To achieve “manufacturing excellence”, SMEs must exploit all available decision-support-systems to supplement production planning for greater productivity. Since levels of productivity and profitability ought to be the major indices for sustainability in today’s dynamic and competitive environment, techniques like SMED offer a great potential to reduce product CT and so aid competitiveness. To make such improvements, industrial engineering tools like time study, Pareto charts, cause and effect analysis, cost-benefit techniques, etc. can be used to identify required changes, eliminations and externalizations of set-up activities and then more refined set-ups can be developed to save production time. Appendix 2, Table AII gives a detailed account of the various techniques used to improve the existing set up by proposing some remedial measures. There is significant saving in overall product CT and this improves the productivity and profitability levels of the organization.