摘 要
生产线作为制造型企业生产活动的主体,很容易因工作量分配不均而产生瓶颈工位和能力过剩工位,进而影响生产效率。对于大多数企业而言,生产线的投资成本比较高,因此对生产线的现有流程进行优化,提高生产线的平衡率、在保证产品质量的前提下降低生产成本、按时完成客户需求的订单就显得尤为重要。
本文以C公司电池包生产线的28节电池包生产流程为研究对象,结合秒表测时法收集各工位的作业内容和生产节拍,并计算出其平衡率。在此基础上,使用5W1H提问技术、ECRS原则、人-机作业分析等方法优化各工位的作业内容,提高生产线平衡率。改善后各工位的作业时间均低于客户需求的节拍时间,在满足客户订单需求的同时,平衡了各工位的工作量,生产线直接作业人员优化了5人,电池包材料成型段平衡率提高11.21%,电池组装段平衡率提高14.18%,生产周期时间降低了162.1s,并且通过对人员的优化,不仅提高了产线的生产效率和员工作业积极性,也为产线的持续改善奠定了基础。
关键字:生产线平衡;秒表测时;ECRS原则;人-机作业分析
目 录
1 绪论 1
1.1研究背景及意义 1
1.1.1研究背景 1
1.1.2研究意义 1
1.2国内外研究现状 2
1.2.1国外研究状况 2
1.2.2国内研究状况 3
1.3研究内容及方法 4
1.3.1研究内容 4
1.3.2研究方法 4
2 理论综述 5
2.1生产线平衡理论 5
2.1.1生产线平衡的相关概念 5
2.1.2生产线平衡的评价指标 6
2.2基础IE方法 6
2.2.1方法研究 6
2.2.2作业测定 7
3 C公司电池包生产线现状分析 10
3.1公司概况 10
3.2电池包生产流程 11
3.3电池包生产线改善前相关数据 12
3.3.1工时测定 12
3.3.2改善前生产线平衡分析 18
3.4电池包生产线存在的主要问题 19
4 电池包生产线的改善方案及效果分析 22
4.1确定改善方案 22
4.1.1原材料来料改善 22
4.1.2贴标签优化 22
4.1.3人-机作业优化 23
4.1.4其他工位优化 24
4.2作业人员改善 25
4.2.1员工绩效管理 25
4.1.2多能工培养 25
4.3改善效果分析 26
4.3.1改善后各工位工作状态统计 26
4.3.2改善后生产线平衡分析 27
4.3.3改善效果确认 29
5 总结展望 30
5.1总结 30
5.2展望 30
参考文献 31

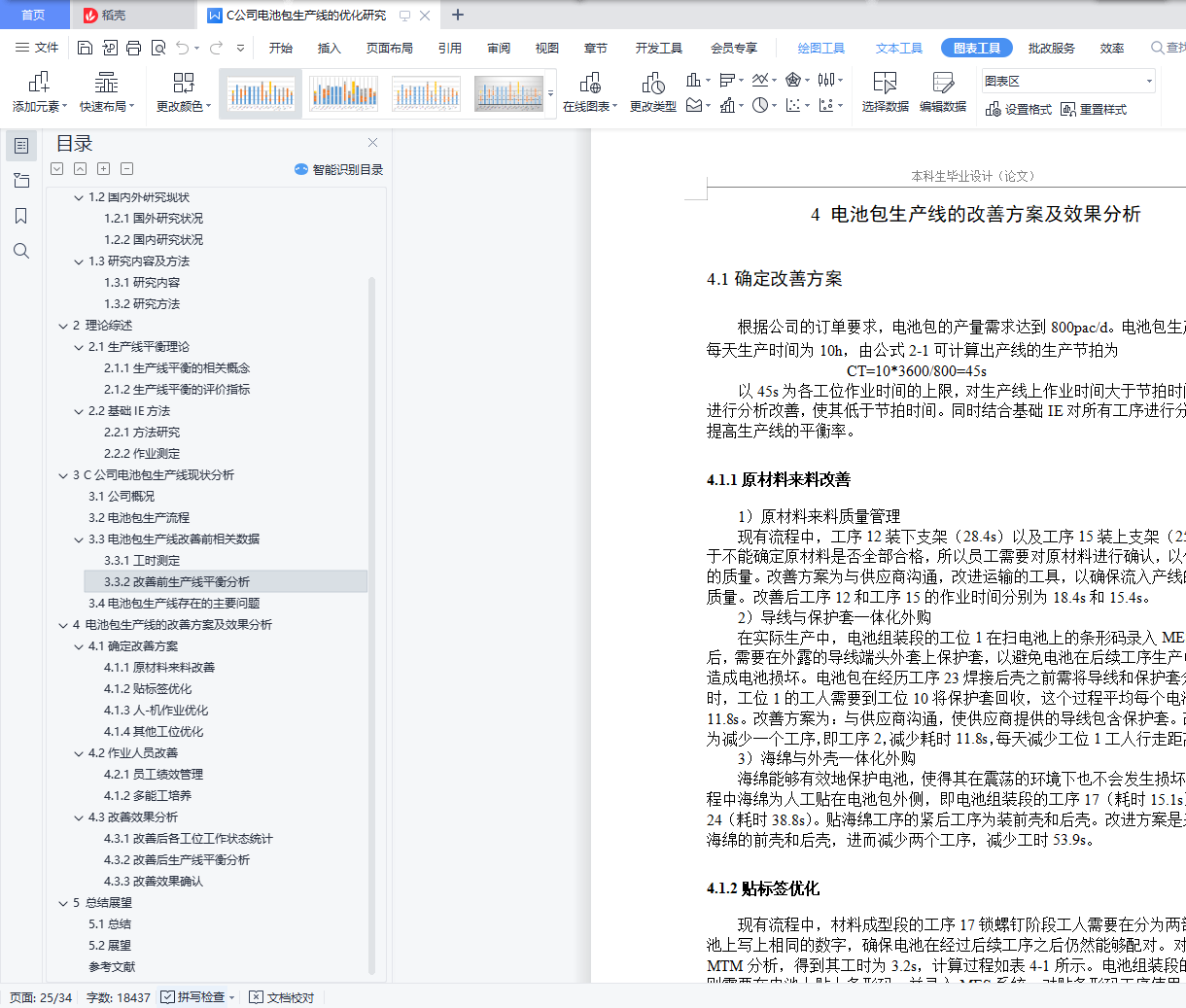
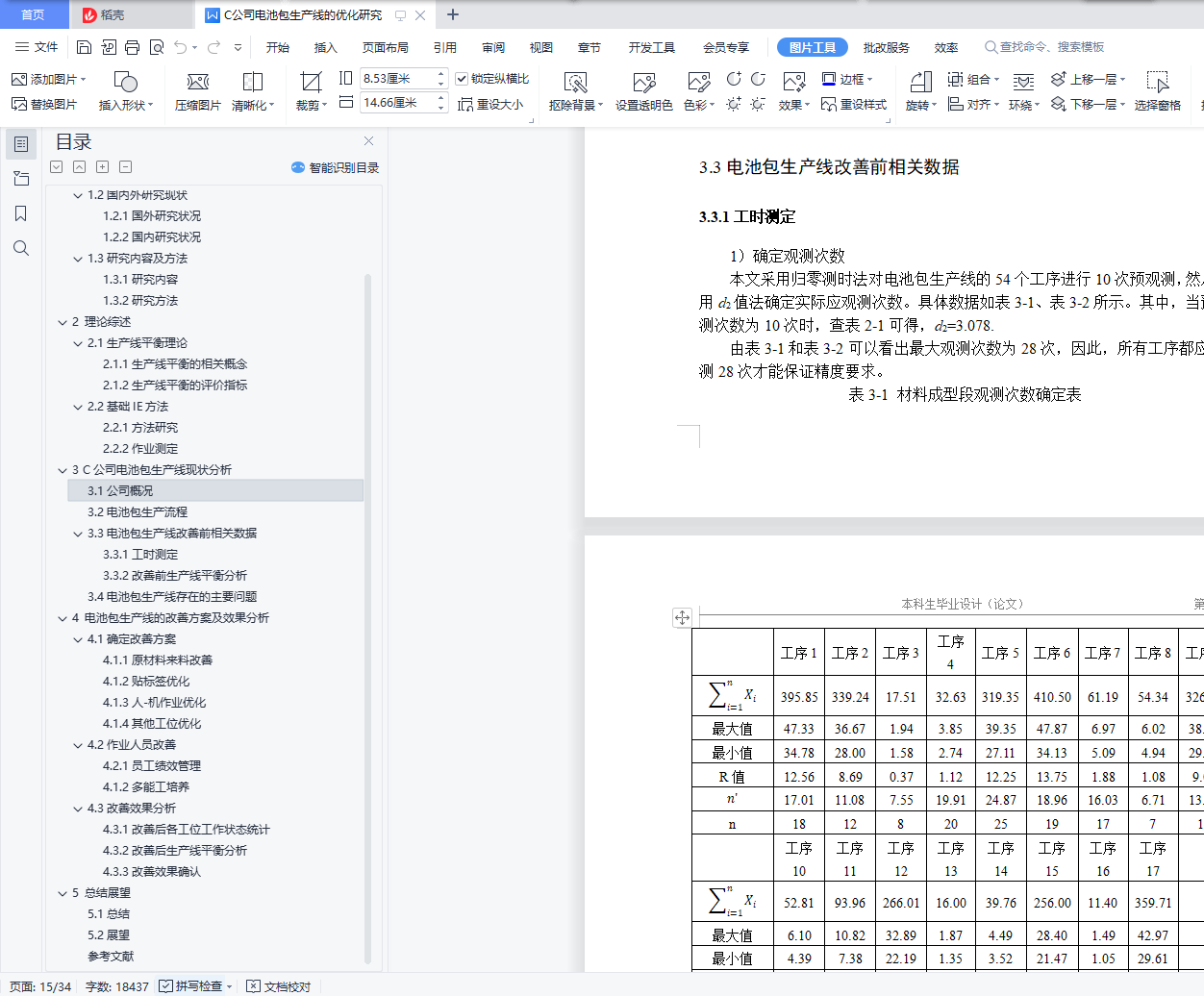
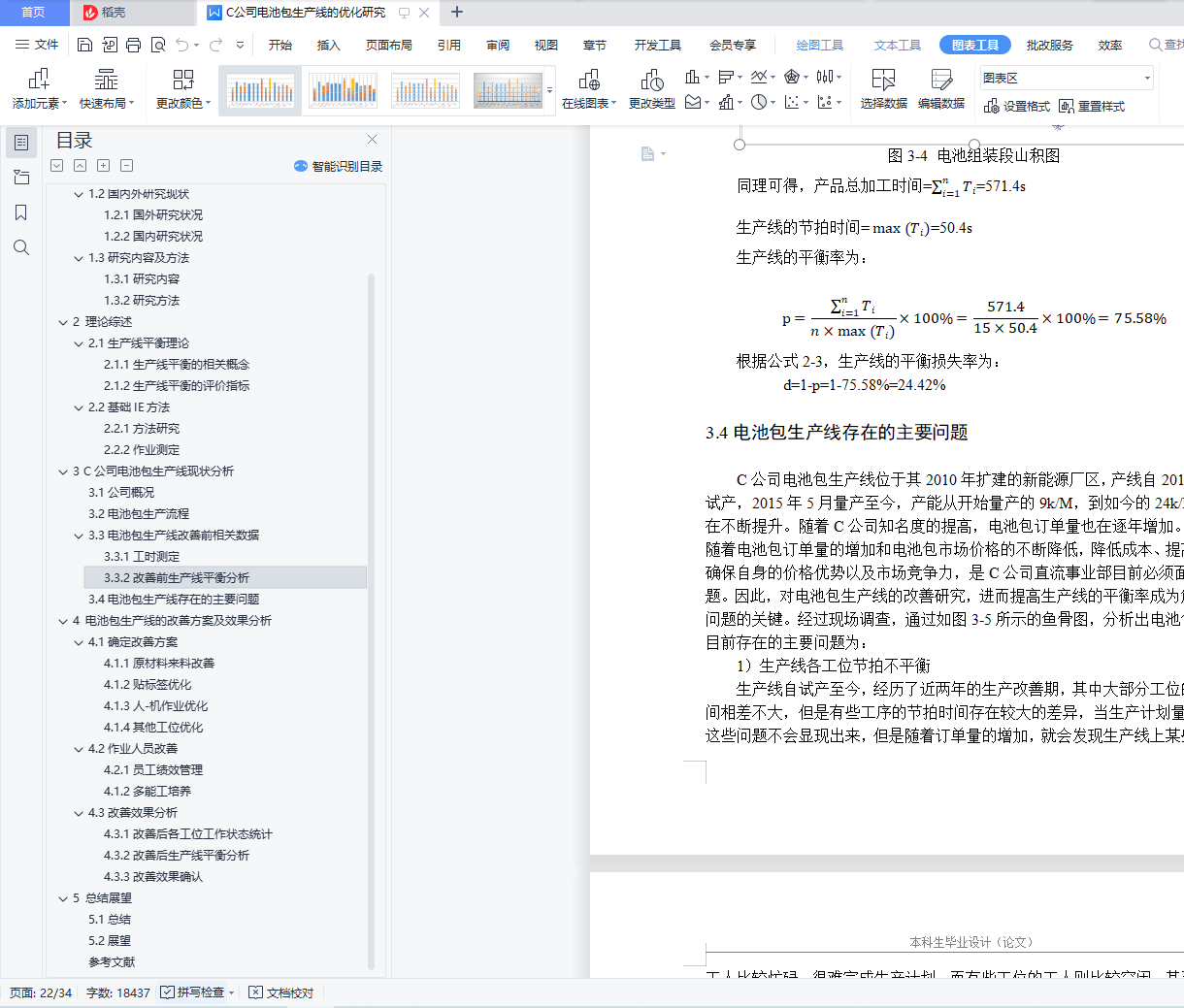
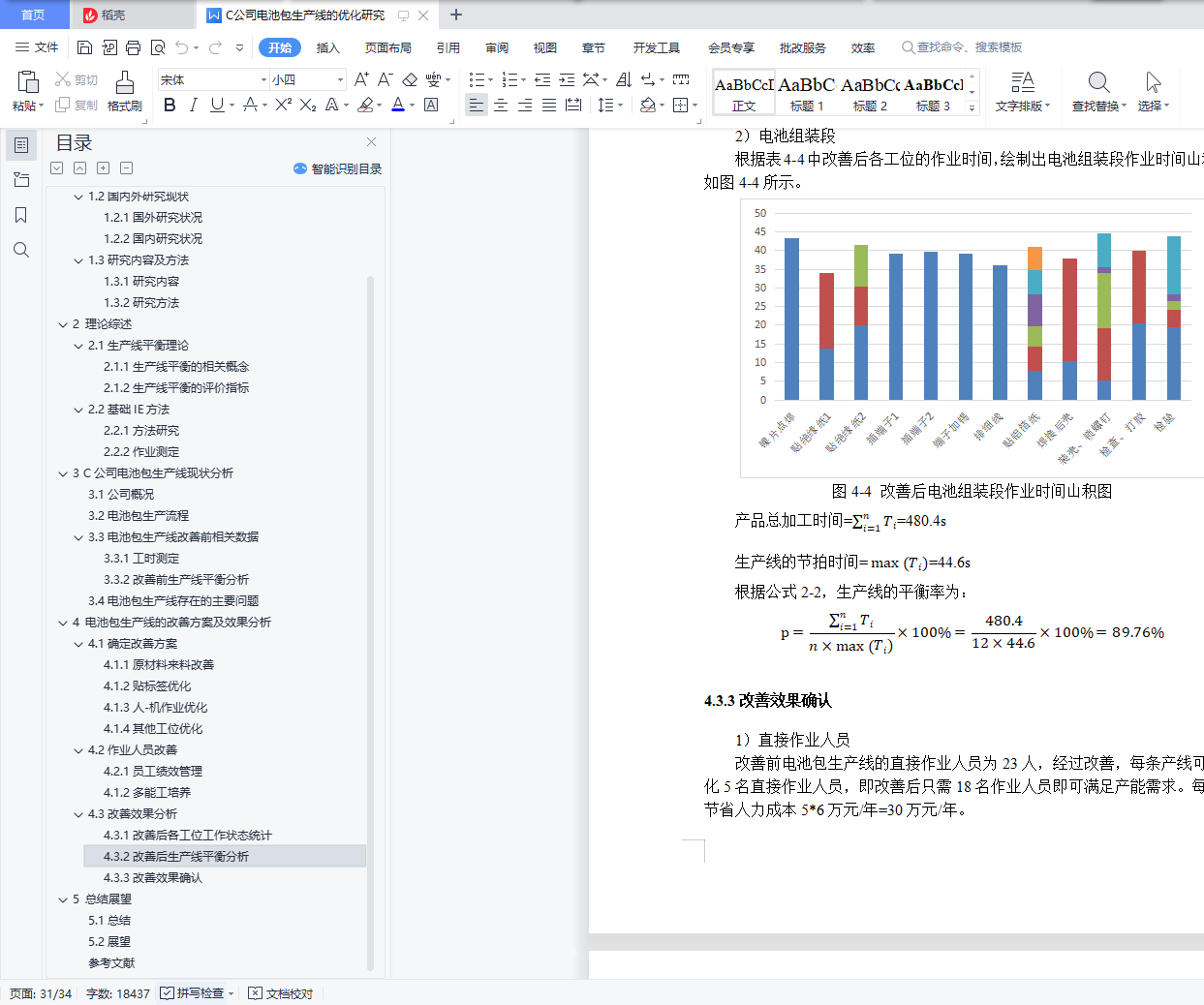
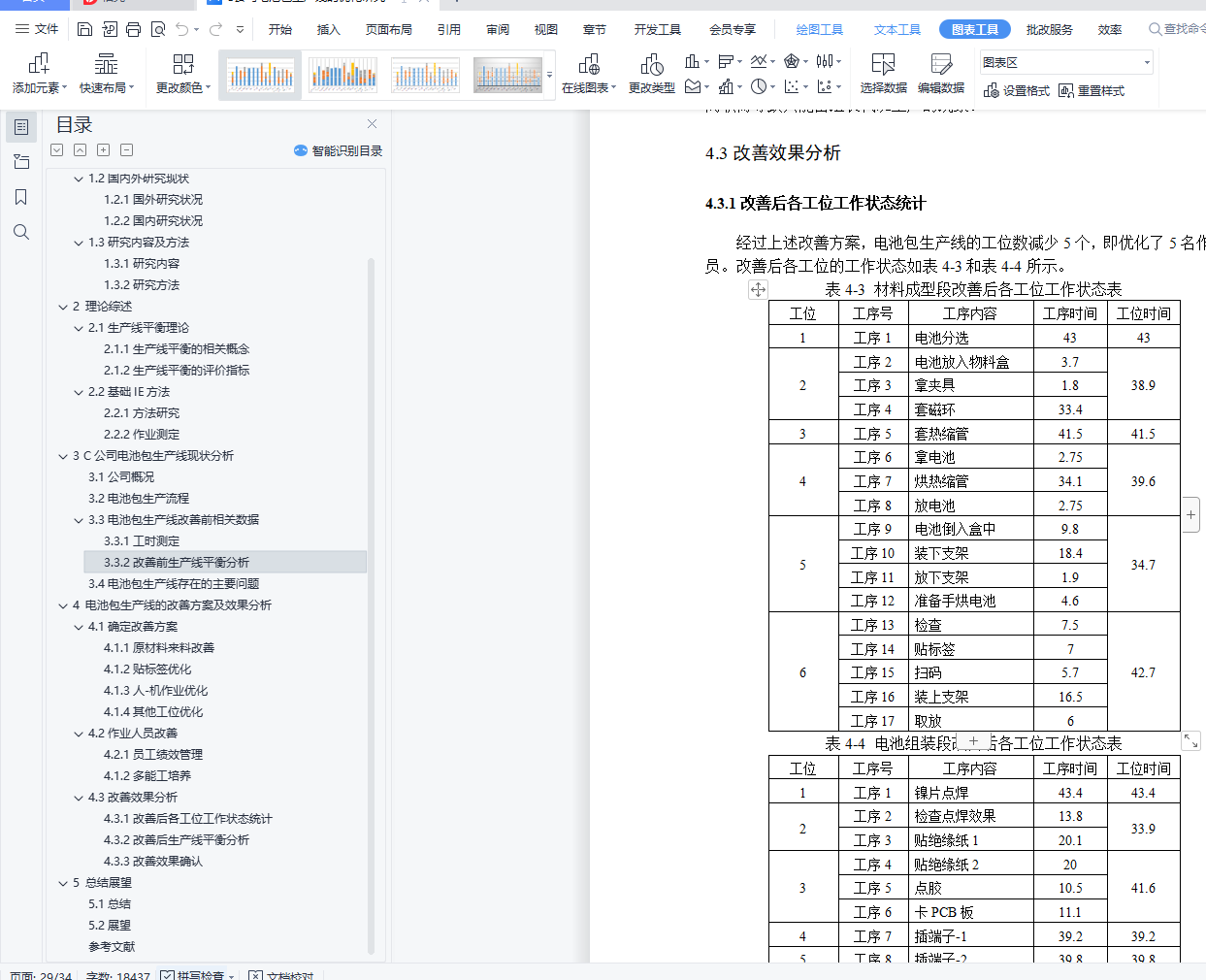
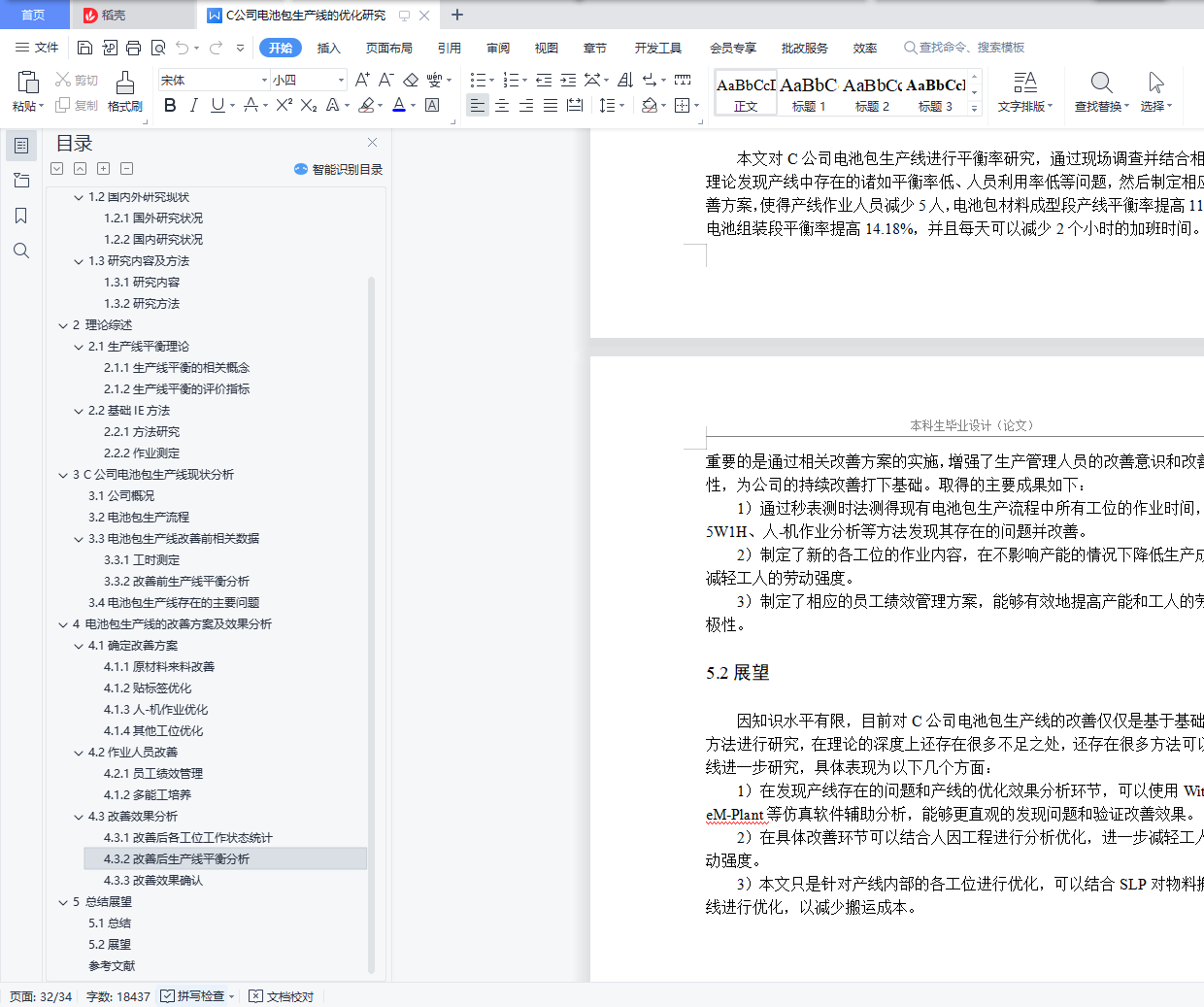
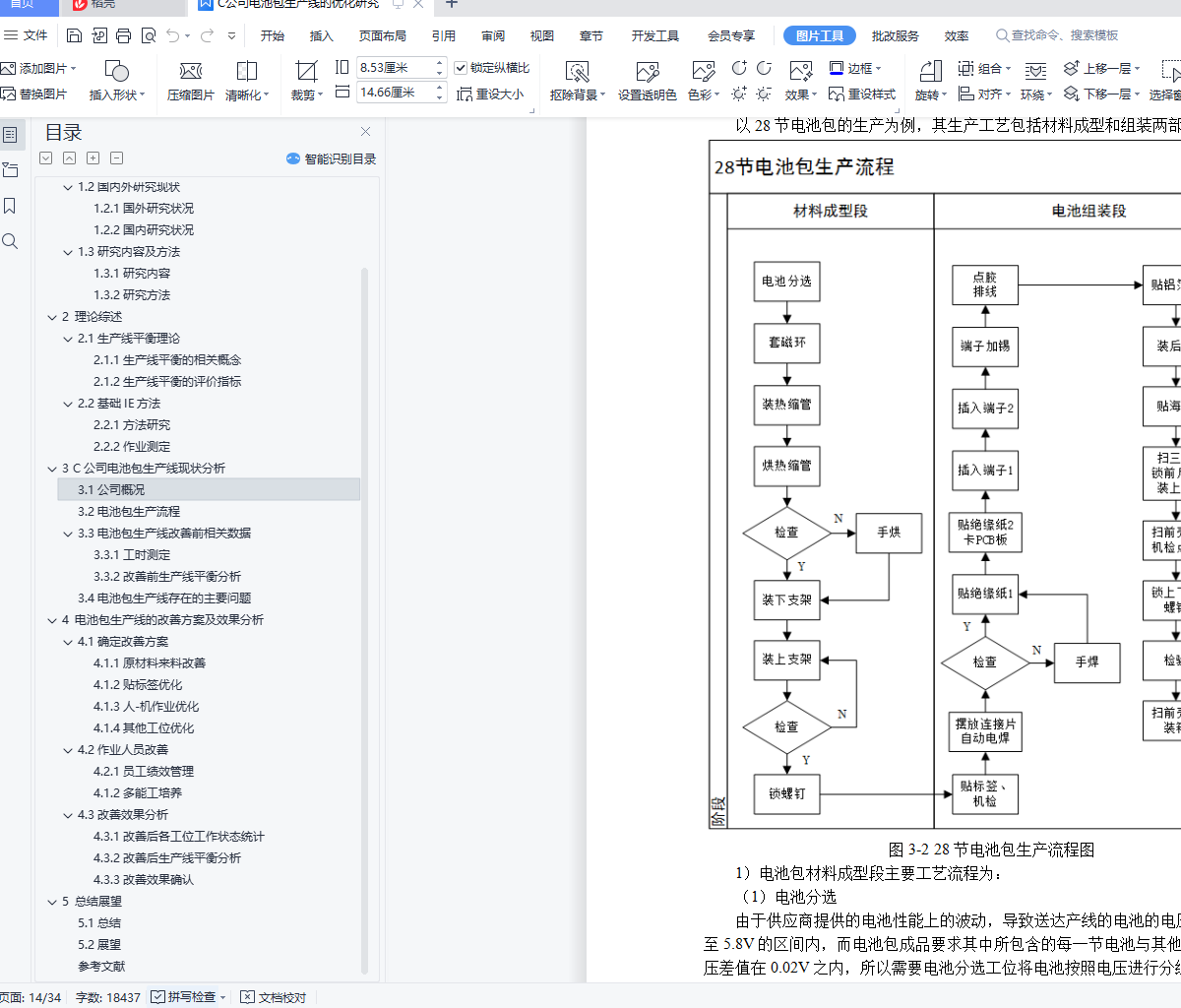
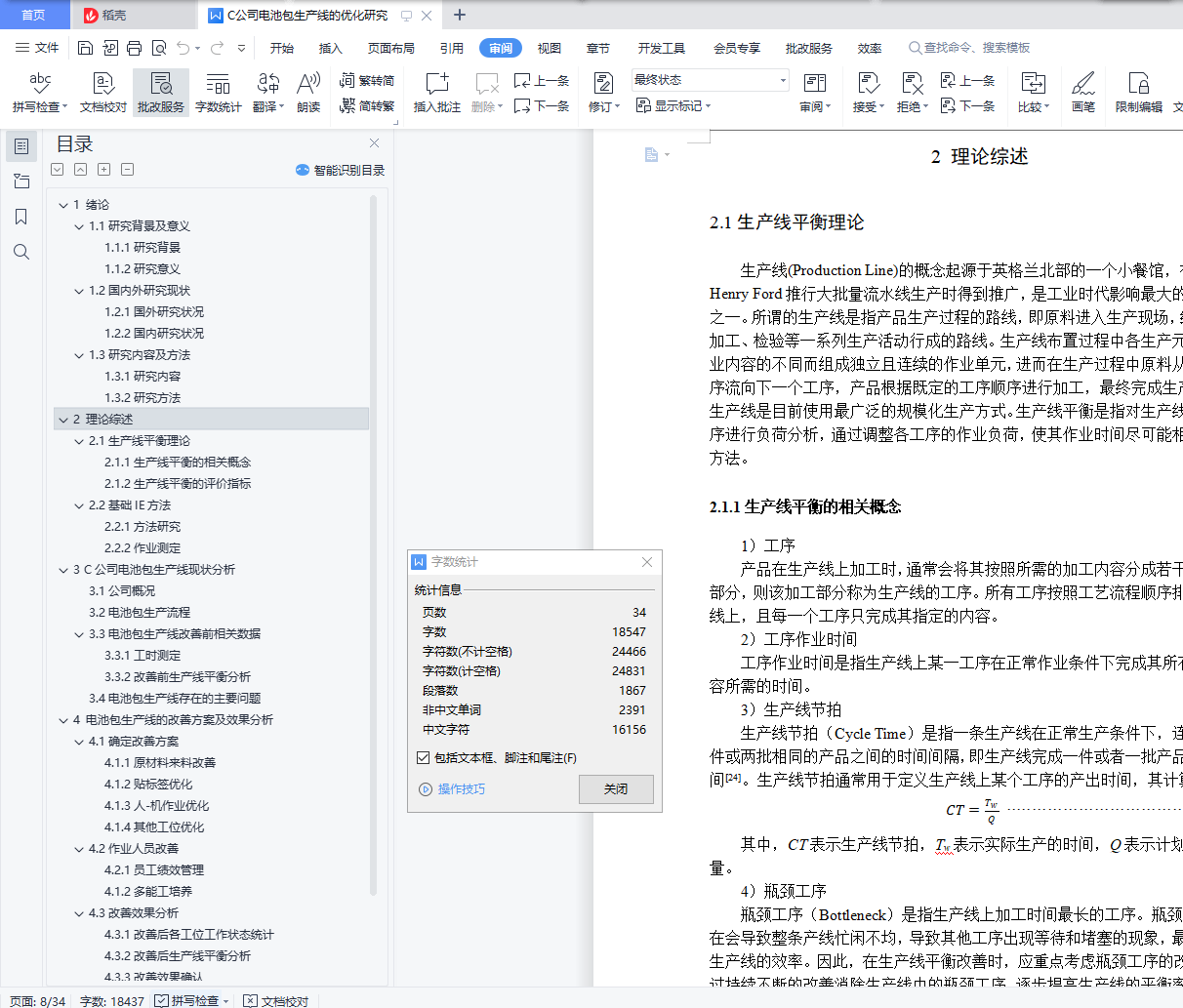
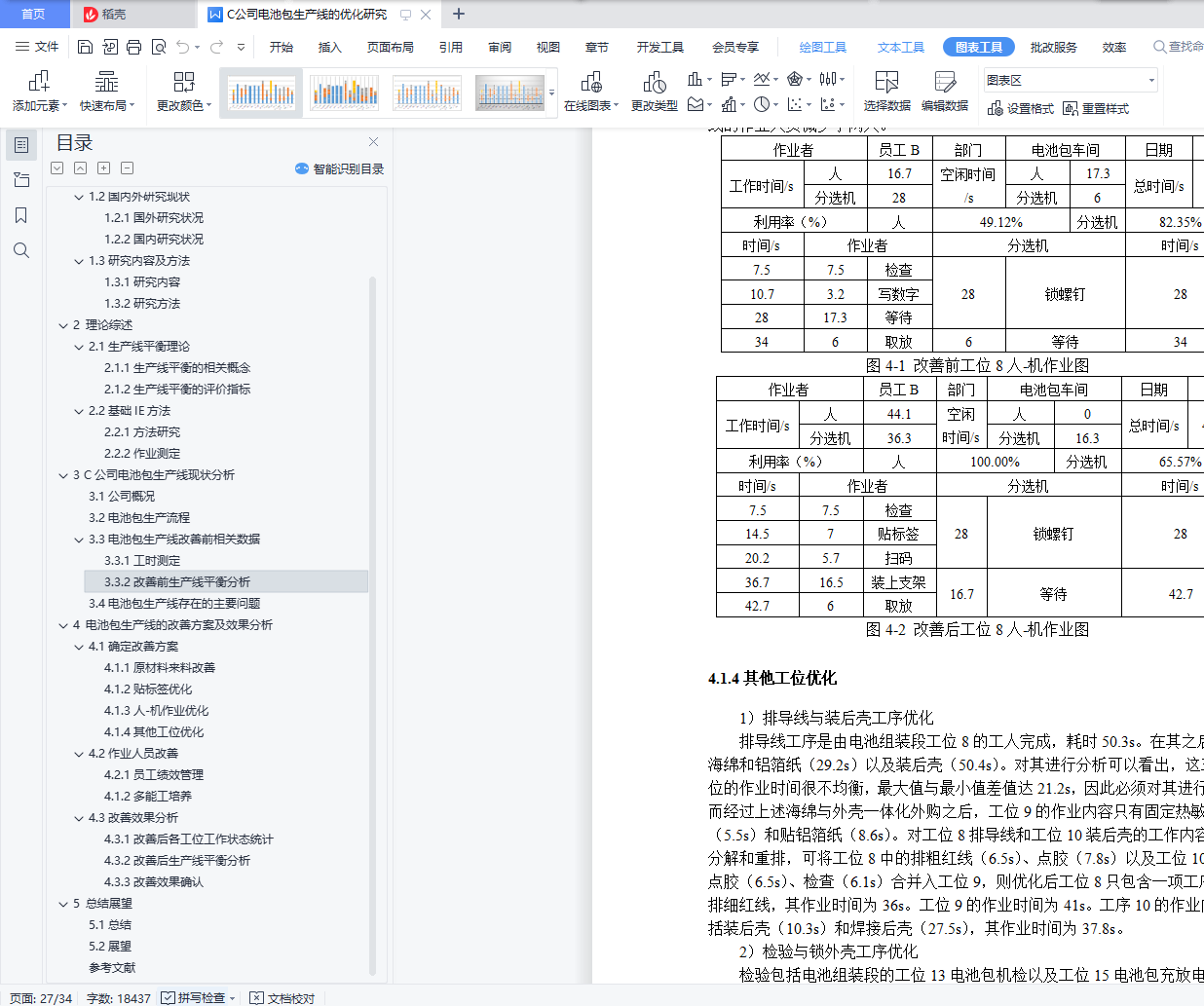
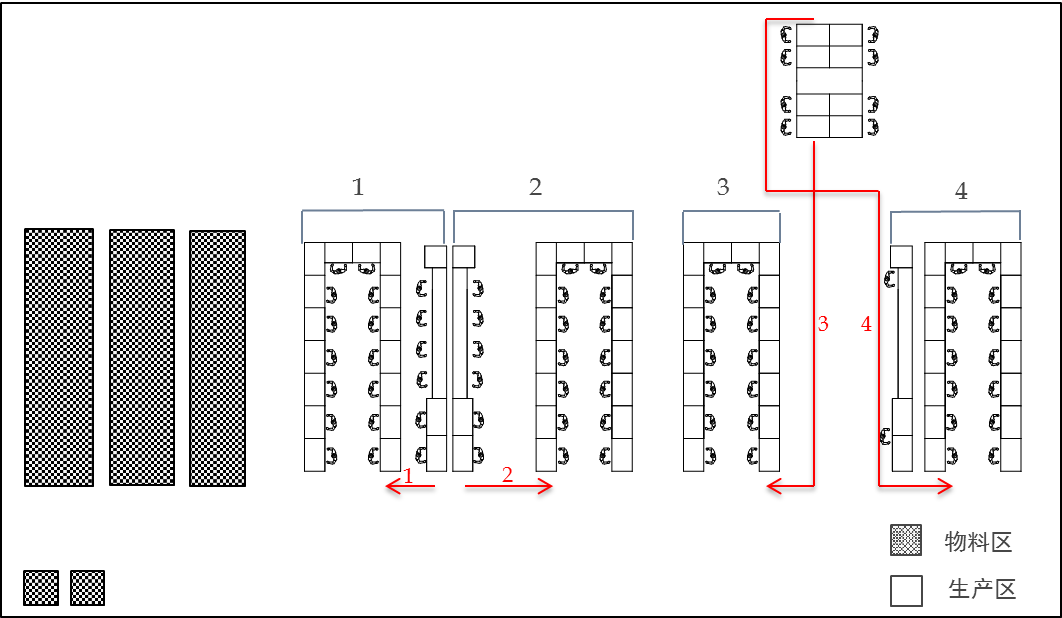
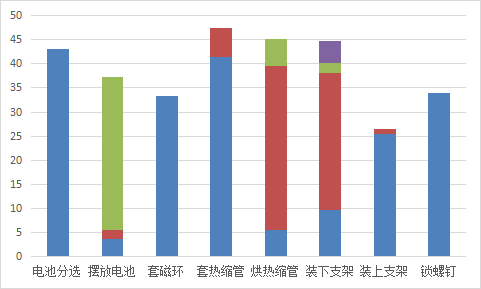
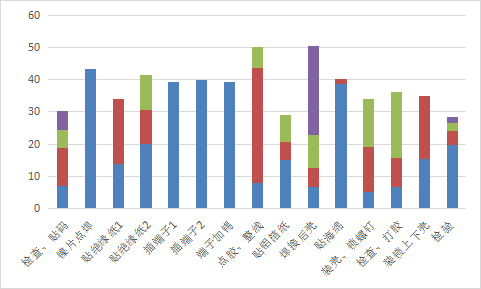