。在非常早期的10–20s,足够高的液柱尚未形成,这个阶段应该完全忽略。在第一阶段,而金属是完全液体,具有完善的接触与寒冷的表面,传热系数达到其最大值约19 的铜和6.5千 为钢冷。我们计算的感应加热技术值非常相似的文献中的凝固铝合金铜和钢模具[10,26,30,31]。没有皮肤形成固体金属在寒冷的表面会出现由于动荡在熔融金属浇注相模。浇注时停止,动荡消失。一个稳定的皮肤金属凝固形成的寒意,因为冷提取热量熔化的金属。该接口是压对冷却的静水压力的液体金属。然后,该感应加热技术的铜冷却急剧下降的时间很短。第一阶段只持续了30s因为高导热的铜冷却。然而,它持续了120s为钢冷低热量的传导,在这段时间的感应加热技术逐渐下降时间。静水压力作用的减少与增加皮肤厚度的固体。在第一阶段,一些参数,如润湿性液体在冷表面,其熔体量超热,表面粗糙度,模具温度,熔体浇注动量,导热性寒,静水压力和动荡,影响传热系数。
4.1.2二级阶段
后形成的足够的固体金属在冷表面,完美的接触寒冷和凝固铸造不再存在,因为收缩铸件凝固。此外,液体的热导率远远高于固体。然而,减少了感应加热技术在铜冷却不断进行由于剩余的亲密接触,其高电导率直到凝固在135s内完成,图9显示感应加热技术在钢冷在二期往往保持在恒定值,约6 在铸件的凝固,直到310s因为热量提取率的钢冷不一样高的铜冷却和温度之间的差异固体金属和冷却表面(热电偶商标)下降时间。可以看出,在图4和5的钢和铜发冷。凝固取向,在这一阶段的传热系数导热系数和冷却表面粗糙度是最重要的参数。
4.1.3.第三阶段
在金属凝固在模具的铜冷却完成,继续的感应加热技术减少到较低的值由于高导电铜。另一方面感应加热技术在钢冷却保持在恒定值。铸件凝固收缩的影响
可能是冷却的平衡的热膨胀,可能产生恒定的接触压力之间的铸造和冷表面。
5.结论
我们的计算结果表明,应用模型,测定金属铸造–冷感应加热技术在一维热流是取得成功,并以下结论可以概括如下:
1.用有限差分法评价的感应加热技术在铝硅共晶–金属铸造的铜和钢冷接口实现了一维热流。
2.数值计算和实验温度值相协调,因此,感应加热技术可靠性高。
3.该感应加热技术在垂直向上定向凝固共晶铝–硅铸造之间约19–9.5 和6.5–5 铜钢发冷。这些值已经表现出了良好的协调性。
4.结果表明,后退的铸造的铜和钢冷表面不发生凝固。
5.该感应加热技术主要是由接触的位置和面积之间的铸造和冷却的表面粗糙度所影响。今后的调查应考虑这些影响。 , 测定金属铸造–冷却接口的非稳态凝固的单向传热系数
摘要
在这项研究中,测量共晶铝硅垂直向上的界面换热系数(感应加热技术)是通过凝固过程中铸造水冷铜和水冷钢定向凝固完成的。有限差分方法(频分复用)是用于解决逆热传导问题(IH CP)。六计算机引导热电偶连接的冷却和铸造,和时间–温度数据的自动记录。热电偶被放置在位于对称5毫米,37.5毫米和75毫米的接口。如侧表面有很好的隔热,垂直向上的接口表面单向凝固过程的开始。测量的时间–温度数据文件所使用的有限差分法用一个明确的技术。热流量计算机程序已经写入估计过渡金属–冷感应加热技术在热传导反问题。实验和计算温度表现出极好的协调。该感应加热技术在垂直向上定向凝固铸造铝硅铜和钢–发冷有之间约19–9.5千瓦/平方米和6.5–5千瓦/平方米的变化。
命名
q 热通量, W/m2
热生成率每单位体积, W/m3
h 小时界面换热系数, W/m2 K
TC 铸件表面温度, K
TM 模具温度(冷)表面, K
T 温度, K
t 时间, s
x 距离, m
k 钾导热, W/m K
C 比热容量, J/kg K
M 编号
l 潜热, J/kg
L 长度, m,
希腊符号
q 材料密度, kg/m3
△t 驱动时间间隔
△x 距离间隔
下标
m 节点
上标
p 时间表示
1.简介
金属冷界面传热,金属铸件凝固速度有其重要的影响力,研究了一些以往的试验研究。一些研究人员已经研究了传热机理铸件,找到影响因素的感应加热技术以及宏观传热值。在这些以往的研究中,该感应加热技术是依赖于许多因素的,包括存在和厚度的表面涂料,铸件表面的方向和大小铸件,冷或模具材料,应用压力,合金类型和组成,合金液的表面张力,模具和冷预热,合金过热度和冷表面粗糙度[1-11]。影响重力的方向有关的接口已审查通过调查与冷藏放置在底部,顶部或侧面模具[ 1]。为准确模拟凝固过程,它需要正确的边界条件应建立 [12–14]。
估计的传热系数在金属铸造–寒意接口通常是计算时间的–温度测量数据在凝固的单向冷冻实验铸造。铸造合金及冷材料用于实验铸造,一般,把一些材料和合金上准确地了解他们的物理行为是众所周知的,如铝,铜,铁和 [ 15 , 16]。传热系数不同,取决于不同的实验条件和铸造合金[ 4]。
回顾文献,可以发现,主要感应加热技术[ 17 , 18 ] 有2种测定方法。一是衡量大小的差距之间形成金属铸造,冷和关联这一差距的大小与传热系数[19-21]。另一种方法是进行温度测量中的铸造和在寒冷的几个指定的地点和使用逆方法得出的感应加热技术[1,5,14]。
一些研究人员已经研究了过渡金属–冷感应加热技术在定向凝固测量问题。这些研究表明,传热系数成为一个初始阶段凝固的高值,然后由于铸件的表面寒冷下降到一个低稳态值,形成一个界面差距[1,12,17,22,23]。由此发现,热传系数更高值时,凝固是垂直向上垂直向下或水平[ 1]。
热损失,当金属首先接触到模具的调节不仅是蓄热能力的模具材料也由换热条件的金属本身,特别是在金属–冷却接口。山度士所确定的实体只有在接触孤立点,与实际接触面积只有一小部分的名义面积[ 12]。
各种工艺参数及其影响的感应加热技术已审查了一些研究人员。在文献中,一些研究人员已经研究了确定感应加热技术在金属凝固冷却接口–铝合金铜,钢或铸铁模具和提供了一些广泛的不同价值观。这些值已报告高达20千瓦/平方米,小于1千瓦/平方米[35]–1,10,24钾。
我们工作的目标是确定金属–冷感应加热技术在定向凝固垂直向上的一个圆柱形铝硅合金铸造–水冷铜的表面与钢冷和比较的感应加热技术的铜和钢发冷。在工作过程中,热流量计算机程序已经写入估计过渡金属–冷感应加热技术在热传导反问题。
2.实验程序
示意图的实验装置连接到数据记录器分析系统,铸造装置和位置的热电偶在定向凝固实验,如图1所示。在土耳其安卡拉的加齐大学,进行了2组实验来评价的感应加热技术进行液体合金(铝–硅)水冷钢和铜发冷技术。液体中铸造金属陶瓷模具由硅酸铝耐火管长度290毫米,内直径28毫米,壁厚10毫米。耐火管嵌入陶瓷棉20毫米厚度的横向热隔离的改进。圆柱冷(铜或钢)长度90毫米插入一个圆柱形模具如图1所示。热电偶是集中在共同的圆柱轴的寒冷和铸造在径向方向(见图1)。他们被置于对称和位于5毫米,37.5毫米和75毫米从铸造–冷却接口。所有热电偶是由电缆连接到一个数据记录仪与计算机接口。
热物理性质的铸造和冷却材料选定为我们的实验总结于表1[36 , 37]。本实验用的–铝合金,共晶组成,有一个很窄的凝固范围。基准的目的,铜与低碳钢金属用于冷却体材料由于其众所周知的物理行为。
垂直凝固装置的目的是提取只有通过水冷底板的允许热量。横向表面的很好的隔热,使单向凝固过程的开始垂直向上的接口表面。
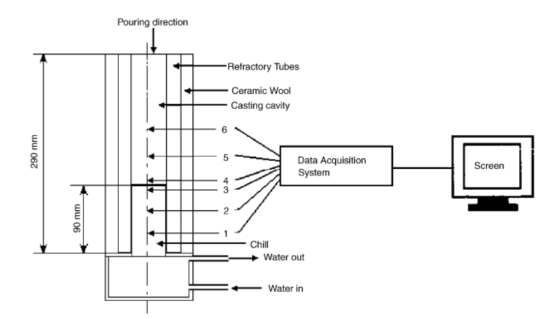
表1
使用数据输入到计算机程序的感应加热技术热的物理性能[36 , 37]
材料 C, J/kg K q , kg/m3 k, W/m K
冷钢H13 435.37+0.2·T 7866.86-0.3174·T 25
冷铜 351+0.11069·T 9095.11-0.46292·T 416.51-0.05874·T
Al–%13Si (solid ) 1180 2682.54-0.2969·T 149.2+0.019667·T
Al–%13Si (liquid ) 1200 2613.27-0.2414·T 0.865·T-648.75
该合金熔化电阻炉熔化的金属合金,直到达到预定温度(980金),高于其熔点温度为849度,然后冷却到室温的模具。用于校准热电偶。
六计算机引导热电偶连接的寒冷和铸造,和时间–温度数据自动记录。数据来自热电偶,在寒冷和铸造是用来绘制时间依赖性实验温度分布。测量的时间–温度数据文件被用来找到正确的边界条件以及相关的温度产生的频分复用使用一个明确的技术,这是纳入热流量计算机程序估计的过渡金属–冷感应加热技术,如在3章。流程图见图2概述了该解决方案的程序。
3.传热系数的确定
在我们的研究中,该感应加热技术在凝固过程的计算方法是解决热传导反问题用有限差分法。进行实验,以确定未知的温度和热通量之间的界面上的铸造和寒冷。时间–温度数据复制被用来评价边界条件。热通量的金属–寒意接口可以说是由一个宏观平均–冷金属感应加热技术(小时)。一个可以写作
分母是平均热流在金属–冷界面瓦/平方米,与商标的计算界面温度的铸造金属表面和冷表面,分别。热通量为铸造冷却界面的计算从温度梯度 的表面和次表面节点如下:
是一个热传导材料冷铸造,W/m K,宏观平均感应加热技术(小时)计算公式(1)。
3.1.传热系数的数学公式
1.冷却的热流量
有足够的绝缘的冷硬铸造室,热流量通过铸造可以合理近似为一一维传热问题。非稳态(瞬态)传导传热的一一维体可以被描述为

T是温度,t是时间、x是笛卡尔坐标。 是热扩散的导电材料,是一个热传导, 是密度c是比热容量。 是导电材料的热扩散率, k是热传导, 是密度和c是比热容量。
3.1.2概述铸造热运动
铸件的热流量,控制方程类似于公式(3),但 包含在左边(3)式。我们可以写传热方程凝固金属如下:
;
在左边,方程(5)是一个热源项,这是纳入考虑为凝固潜热,由 ;l是融合潜热, 是固体部分的铸造。 确定如下,(7)式:
; 在式(6)可以与温度表示如下:
;
式(8)代到(6)给出了方程 ,替代式(9)到(5)给出了方程 ,这个方程可以重新作为:
;一个可以定义 在凝固中作为一个明显的比热。然后,式(11)可以写为:
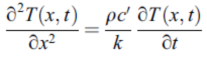

图2.确定在金属铸造–冷却接口感应加热技术流程图。
3.1.3概述有限差分法
使用分析方法,在某些情况下,评估数学模型精确解稳定,一或二维导热问题。然而,这些解决方案是要由简单的几何形状和边界条件产生,他们是有案可循的。另一方面,解析解的瞬态问题局限于简单的几何形状和边界条件。在这方面,在许多情况下,几何和边界条件排除使用的分析技术和资源必须以有限差分法。一些研究人员开发了一个数学模型为基础的有限差分法模拟凝固[38-40]。在目前的工作,这个问题已经在同一个三维几何用有限尺寸如图3所示如下:
该区 分成相等大小的网格 ;
m是用来指定某位置的x离散点在图3。除了正在离散空间,问题也必须是离散的时间。为了这个目的作p介绍:
有限差分逼近的导数公式(3)和同一类型(12)表示为:
p是用来表示时间T,和时间导数表达方面的差异,温度与新的(p+1)和以前(p)的时间步骤。
图(3)和(12)解决使用显式差分的冷却和铸造:
它可以重新作为: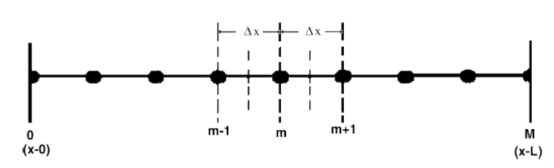
f是一个有限差分形式的傅里叶数, 式(17)明确因为未知节点温度的新时间确定完全由已知节点温度在过去的时间。因此,计算的未知的温度是简单的。因为温度的每个内部节点是众所周知的在 从规定的初始条件,计算开始于 ,在式(17)适用于每个内部节点确定其温度。与温度被称为 ,适当的有限差分方程,然后应用在每个节点发现温度 。在这方面,瞬态温度分布通过出时间,使用间隔的 。
精度的有限差分方法可以改善降低值 和 。当然,一些内部节点必须考虑增加较小的网格间距宽 ,数量和时间间隔需要在规定的最后时间的增加而减少,时间间隔 。因此,计算时间随 和 的变化。
式(17)必须写为铸造和冷却因素。计算的收敛,因素的大小和时间的步骤是选择考虑 的。
在式(18), 和 指的是计算中使用的空间和时间增量。在这项工作中,不同元素选定 ,因此,铸造和冷却 。
3.2.边界条件和求解
在目前的工作中,初始温度和边界条件选择如下:
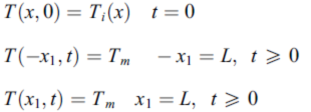 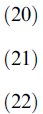
在使用温度的边界条件, 和 ,期间获得实验,测定在对称位于热电偶在冷却寒冷和铸造金属–寒意接口 处。
第一所记录的温度的热电偶置于,对称,75mm的金属铸造–冷却接口被用作初始温度,式(20)t=0,在铸造和冷却。从这些热电偶的温度也被用来作为边界条件在稍后时间在有限差分计算。(21)和(22),分别为。本边界条件的界面,通过假设的表面温度均匀在铸件表面和冷却。温度的热电偶每0.5s读一次,定义为时间的测量。
计算出的温度,5mm的接口在铸造和冷却,分别,进行了比较与实测温度在同一点。为此,该实际位置的热电偶两国之间的相邻节点的决心,和温度,他们之间是线性插值。所谓的表面温度在铸造与寒冷的界面进行了修改,和有限差分计算的前0.5s间隔重复。精度的数值模拟已准备同意通过±0.1K与测量温度的点对称距离5mm该接口在铸造和冷却。
这样,一个可靠的温度场已确定了表面温度在铸造和冷却的接口在选定的准确性±0.1K。
4.结果与讨论
温度测量实验在六个地点:在冷却和铸造,对称在5毫米,37.5毫米和75毫米从铸造–冷却接口,分别为。他们被显示在图4中与计算温度以下的数值模拟研究冷(商标)和铸造(热电偶)接口的Al-Si铸造和水冷钢冷。图5显示了相同的数据对Al-Si铸造–和水冷铜冷却。本变化的过程的温度场的实验可以遵循的钢和铜冷却。图4和5,体现了热物性定律。
为了检验精度达到了有限差分法,计算温度在铸造在点37.5毫米从铸造–冷界面进行了比较与温度测量在这一点0.5s的上一段。
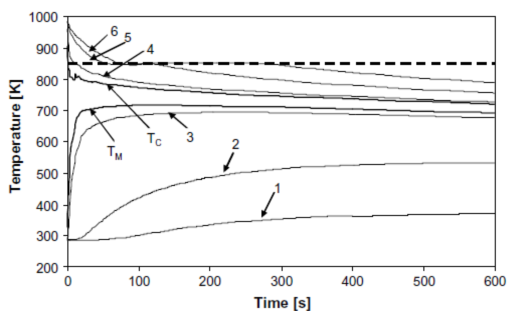
图4.实验和计算的温度响应在Al-Si铸造–水冷却钢冷的六个点。
图5。实验和计算的温度在Al-Si铸造–水冷铜板冷却的六个点。
测量和计算温度点(37.5毫米)的接口冷却和铸造的监测控制的可靠性之间的相关性测量与数值计算。在寒冷的中点,只有热传导,该协议的测量和计算是可行的,不到1–2K的差异,考虑限制热电偶的准确性。
另一方面,不同在铸造复杂的事件计算温度。在文献中,温差<±20K之间的测量和数值计算在铸造接受[ 3]。在本研究中,测量和数值计算间的协调已达到。在图6和7显示计算和测量在共晶铝硅铸造的温度。分别进行水冷钢和铜发冷。这些数字表明正确的坐标温度之间的差异计算和测量。在铸造中心,计算和测量温度,重叠在固相线,并在液相线,温差不超过16度和14度的钢铜发冷。在图6和7明确表明在冷却和铸造领域我们计算确定的时间变化的温度的可靠性和准确性较高。
4.1.冷却曲线和热传递系数
在确定的温度场,热转移之间的铸造和寒冷已计算的帮助下,方程(2),如图8所示为铜和钢发冷。然后,该感应加热技术已评估的帮助下,方程(1)。时间依赖性变化的感应加热技术在图9中显示,从最初的时刻,直到准静态的铸造工艺情况是达到了,可区别主要在三个阶段。
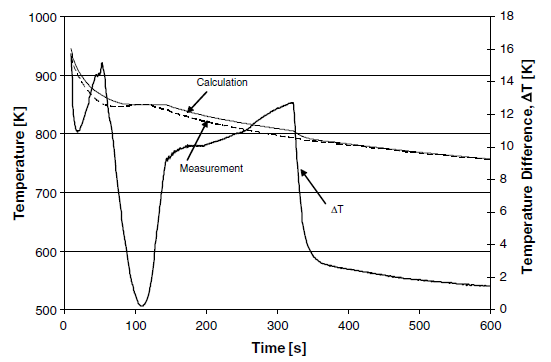
图6。在共晶铝硅铸造–在水冷钢冷却时计算和测量温度。(右纵坐标表示温度之间的差异计算和测量。)
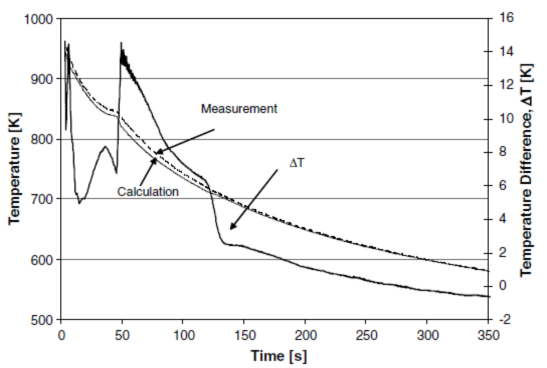
图7。在共晶铝硅铸造–在水冷铜冷却时计算和测量温度。(右纵坐标表示温度之间的差异计算和测量。)
4.1第一阶段
液体倒入模具
全套毕业设计论文现成成品资料请咨询微信号:biyezuopinvvp QQ:1015083682
返回首页
如转载请注明来源于www.biyezuopin.vip
|