摘要
随着游戏产业的蓬勃发展,游戏手柄作为游戏玩家与游戏设备交互的关键工具,其设计和制造的重要性日益凸显。本文基于SolidWorks三维建模软件,对游戏手柄双按键模具设计进行了深入研究。首先,对塑件材料进行了详细分析,包括其基本特性、成型性能和成型条件。其次,对塑件进行了工艺分析,涉及结构设计、尺寸精度、表面粗糙度以及体积和质量等方面。在此基础上,制定了注射成型工艺方案,并对模具结构进行了分析和确定,包括浇口种类的选择、型腔数目的确定以及注射机的选择和校核等。最后,详细设计了注射模具结构,包括分型面的设计、型腔的布局等关键部分。通过SolidWorks的仿真和模拟功能,本文成功提升了设计的准确性和效率,优化了用户体验,并为模具设计的智能化提供了可能。本研究成果对于推动游戏手柄设计的现代化和促进游戏产业的发展具有重要意义。
关键词:SolidWorks;游戏手柄;双按键;模具设计;注塑成型;塑件材料分析
Abstract
As the gaming industry flourished, the design and manufacture of gamepads became increasingly important as a key tool for game players to interact with gaming devices. Based on the SolidWorks, the design of the-key is is is studied. First, the plastic parts materials are analyzed in detail, including its basic characteristics, molding properties and molding conditions. Secondly, the process analysis of plastic parts, involving structural design, dimensional accuracy, surface roughness and volume and quality. On this basis, the injection molding process scheme is formulated, and the mold structure was analyzed and determined, including the selection of gate types, the determination of the number of cavities and the selection and checking of injectors. Finally, the structure of the injection mold is designed in detail, including the key parts of the design of the classification surface and the layout of the type cavity. Through the simulation and simulation functions of SolidWorks, this paper successfully improves the accuracy and efficiency of the design, optimizes the user experience, and provides the possibility of intelligent mold design. The results of this study are of great significance for promoting the modernization of the game controller design and promoting the development of the game industry.
Key words: SolidWorks; game controller; double keys; mold design; injection molding; plastic parts material analysis
目 录
1 引言
1.1 塑料简介
1.2 注塑成型及注塑模
2 塑件材料分析
2.1 塑件材料的基本特性
2.2 塑件材料成型性能
2.3 塑件材料成型条件
3 塑件的工艺分析
3.1 塑件的结构设计
3.2 塑件尺寸及精度
3.3 塑件表面粗糙度
3.4 塑件的体积和质量
4 注射成型工艺方案及模具结构的分析和确定
4.1、注射成型工艺过程分析[5]
4.2 浇口种类的确定
4.3 型腔数目的确定
4.4 注射机的选择和校核
4.4.1 注射量的校核
4.4.2 塑件在分型面上的投影面积与锁模力的校核
4.4.3、模具与注射机安装模具部分相关尺寸校核
5 注射模具结构设计
5.1 分型面的设计
5.2 型腔的布局
5.3 浇注系统的设计
5.3.1 浇注系统组成
5.3.2 确定浇注系统的原则
5.3.3 主流道的设计
5.3.4 分流道的设计
5.3.5 浇口的设计
5.3.6 冷料穴的设计
5.4 注射模成型零部件的设计[7]
5.4.1 成型零部件结构设计
5.4.2 成型零部件工作尺寸的计算
5.5 排气结构设计
5.6 脱模机构的设计
5.6.1 脱模机构的选用原则
5.6.2 脱模机构类型的选择
5.6.3 推杆机构具体设计
5.6.4 脱模动作原理
5.7 注射模温度调节系统
5.7.1 温度调节对塑件质量的影响
5.7.2 冷却系统之设计规则
5.8 模架及标准件的选用
5.8.1 模架的选用
5.8.2 标准件的选用
6 模具材料的选用
6.1 成型零件材料选用
6.2 注射模用钢种
7 注射成型工艺过程模拟分析
总 结
致谢
参考文献
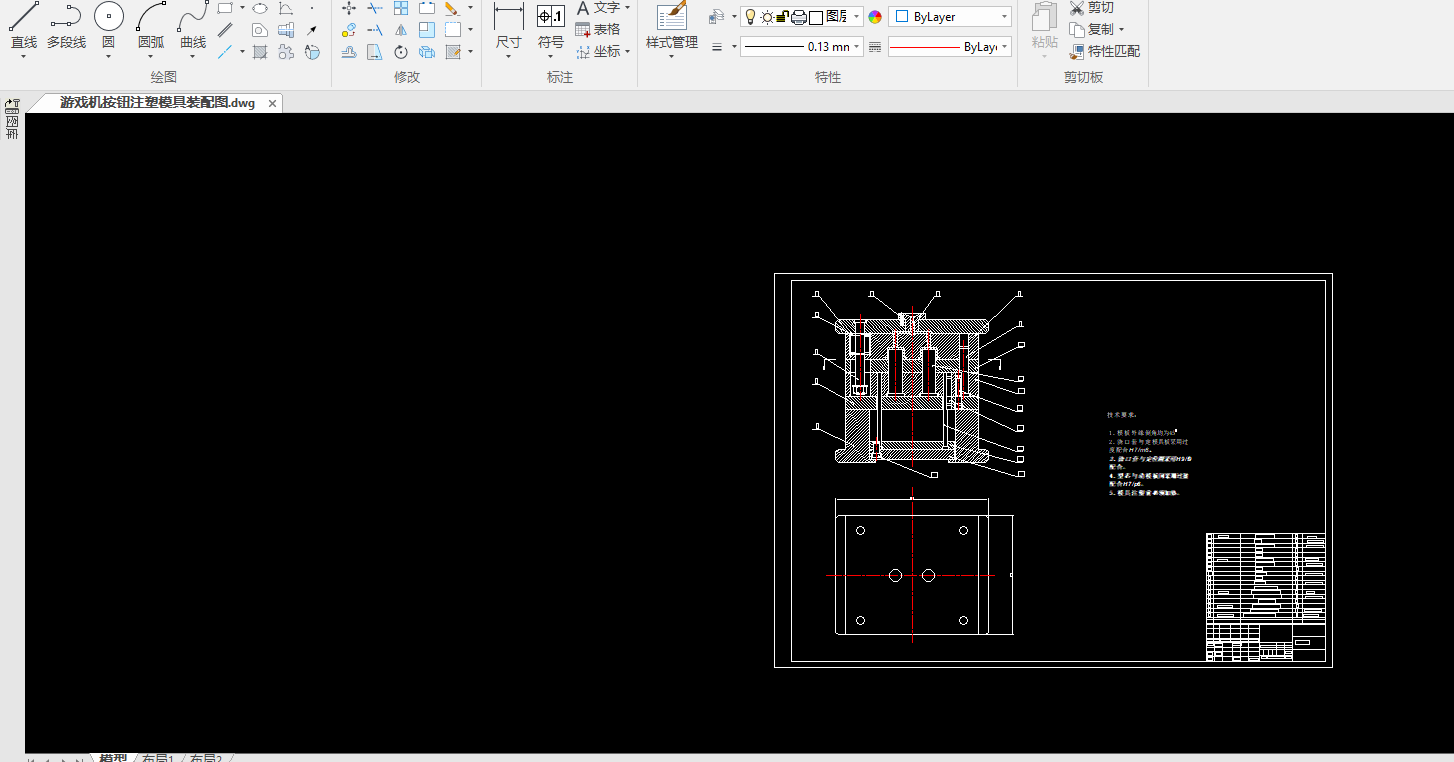
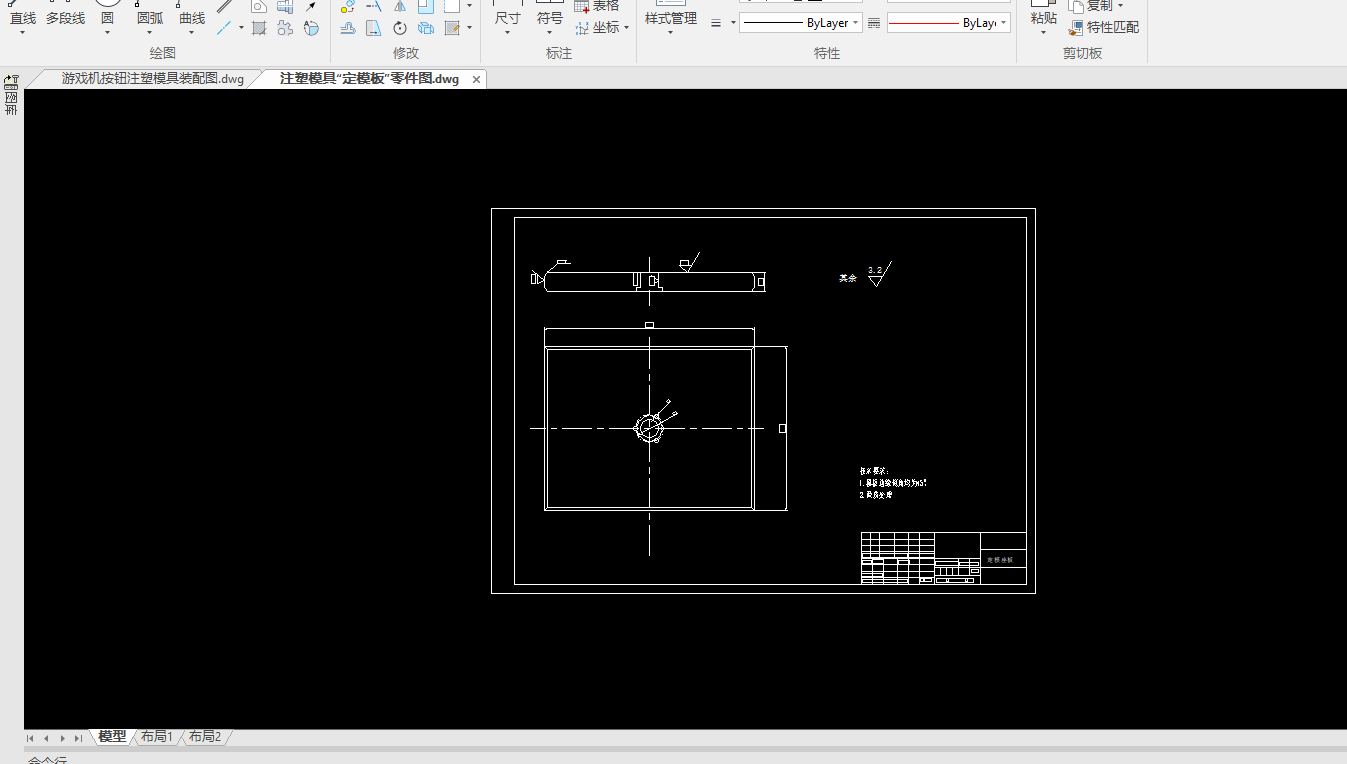
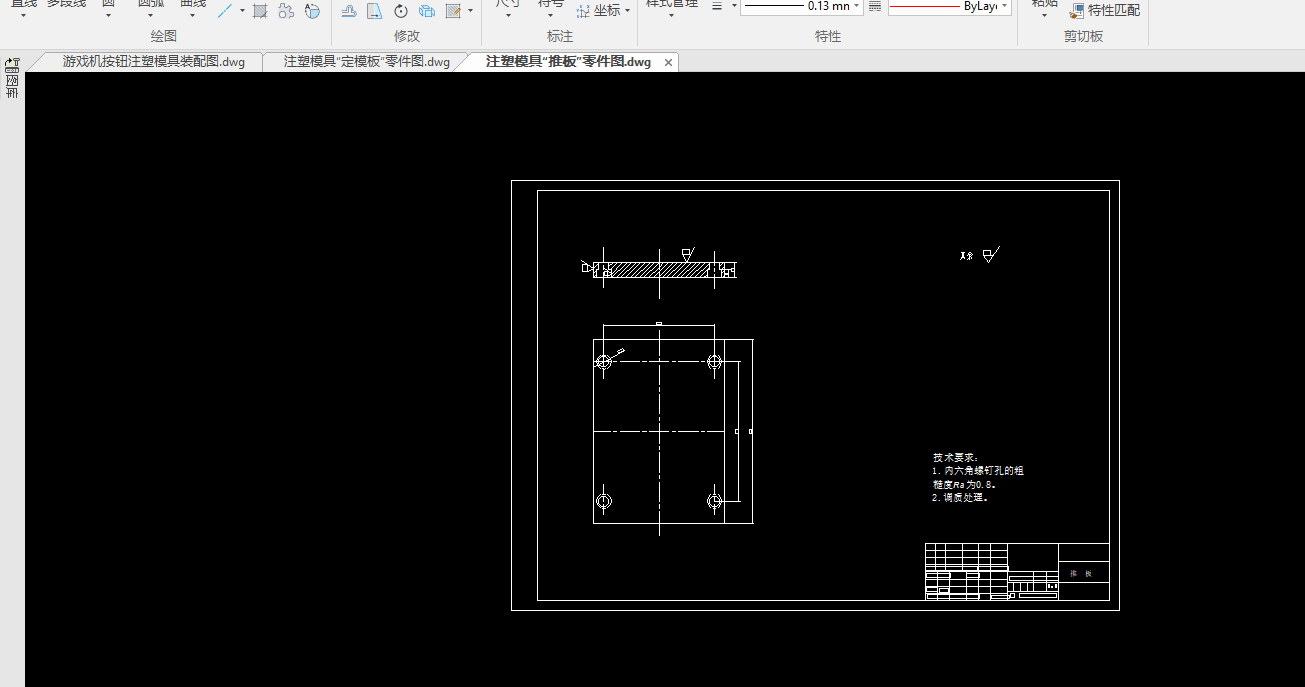
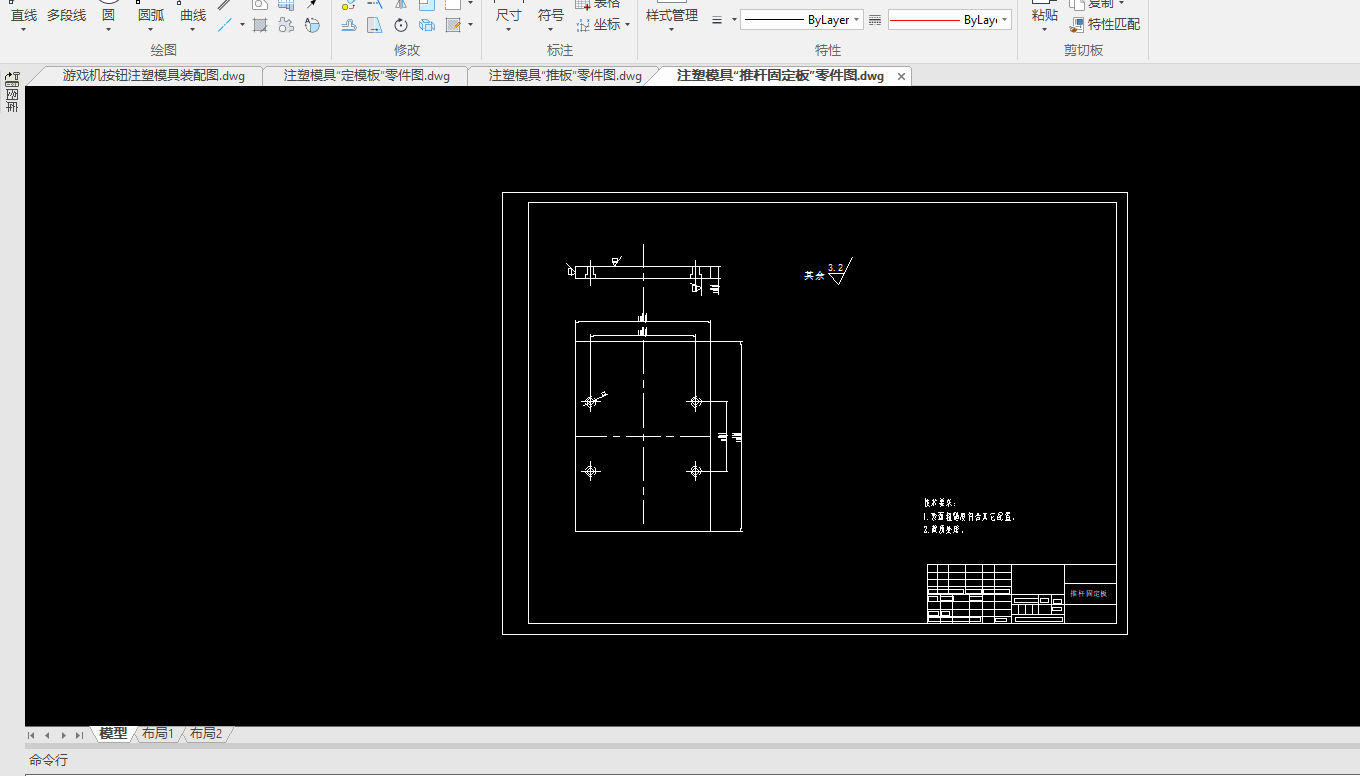
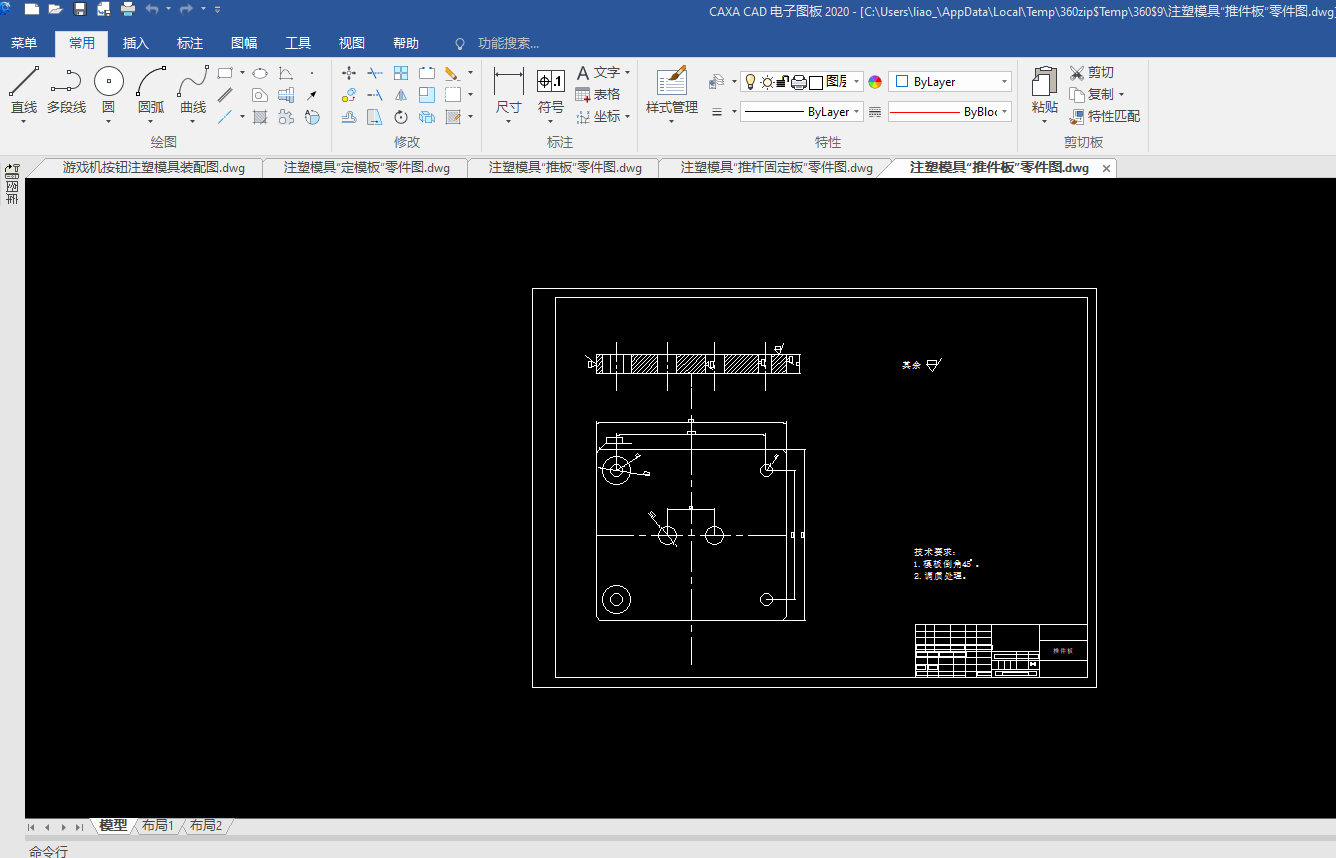
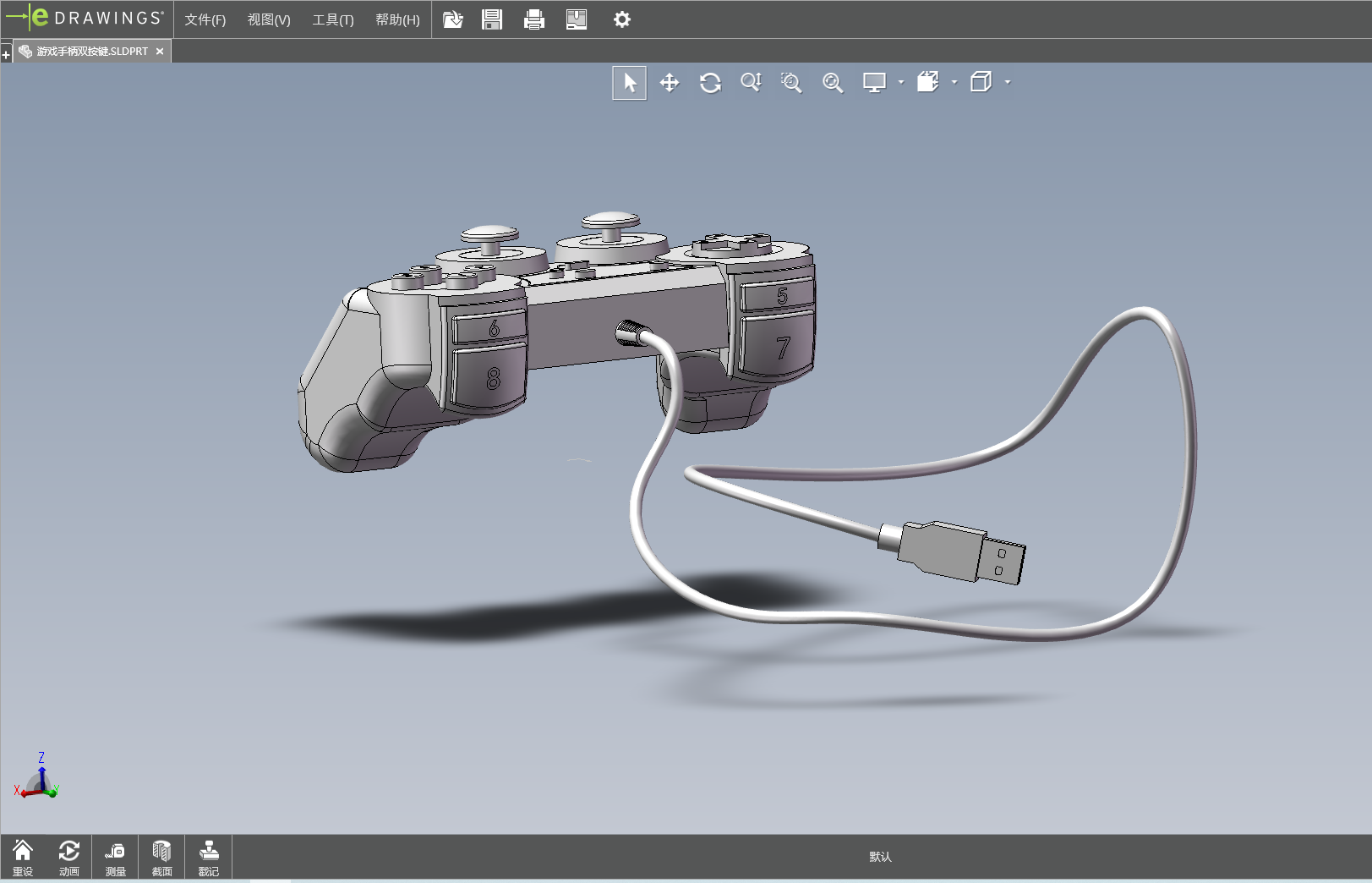
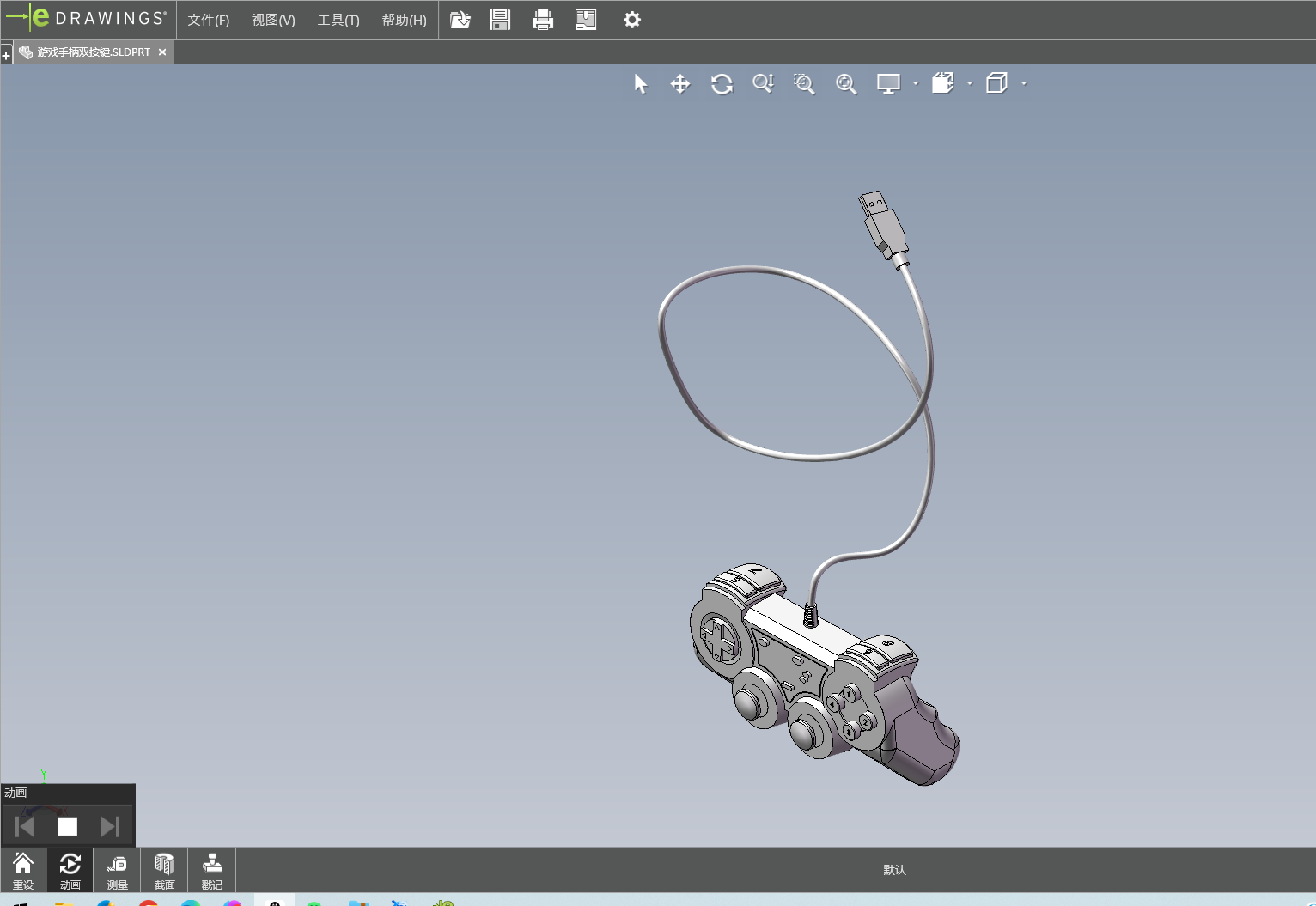
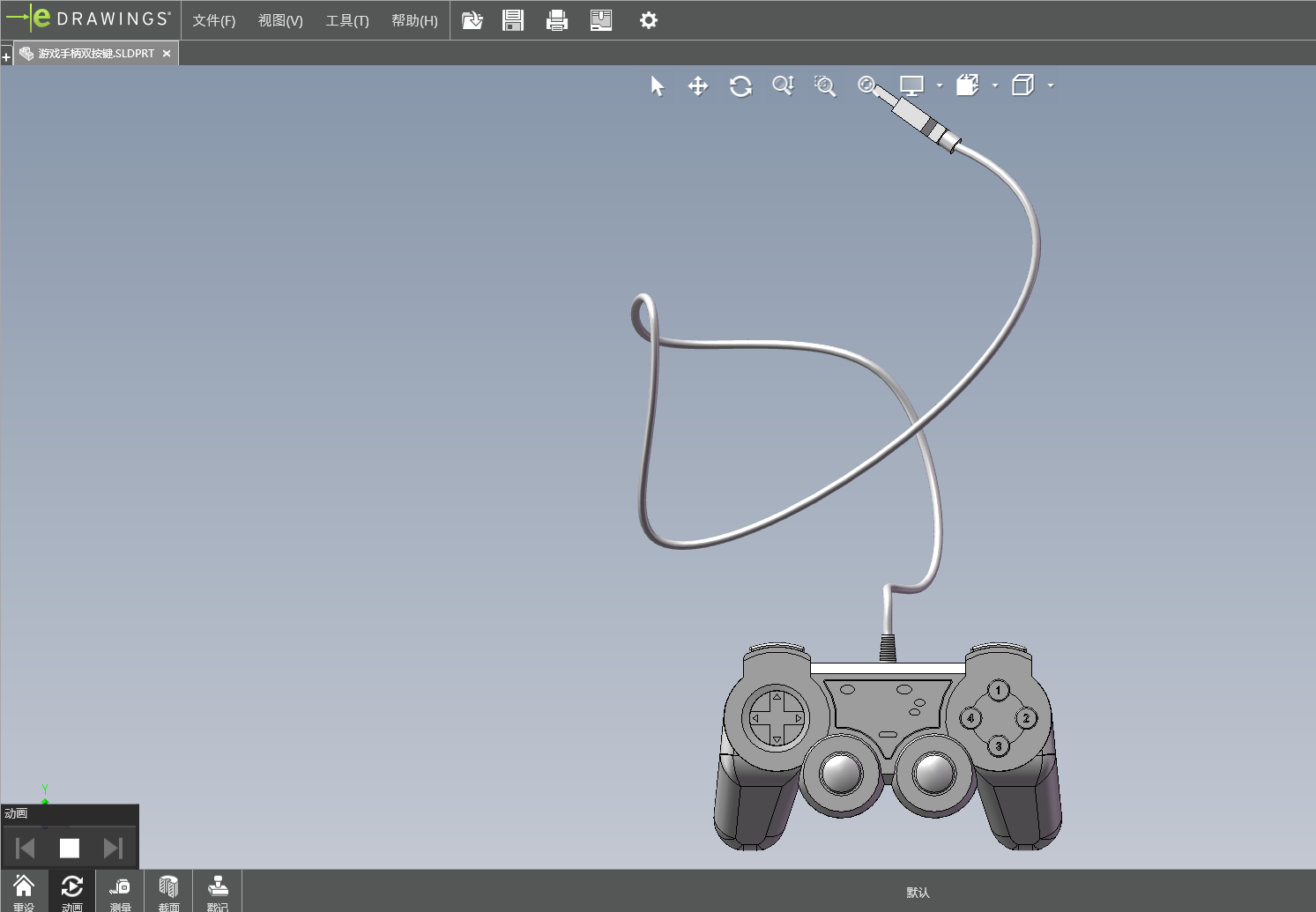

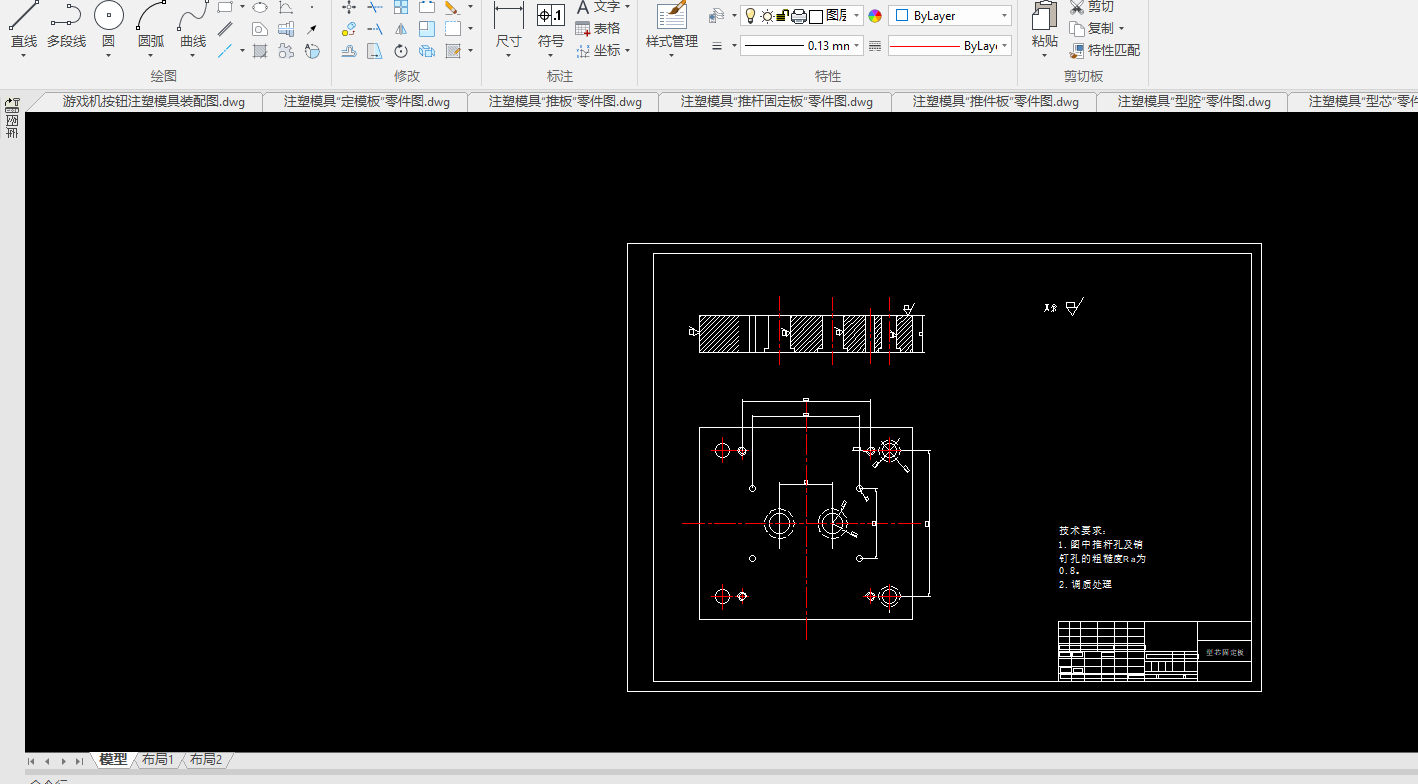
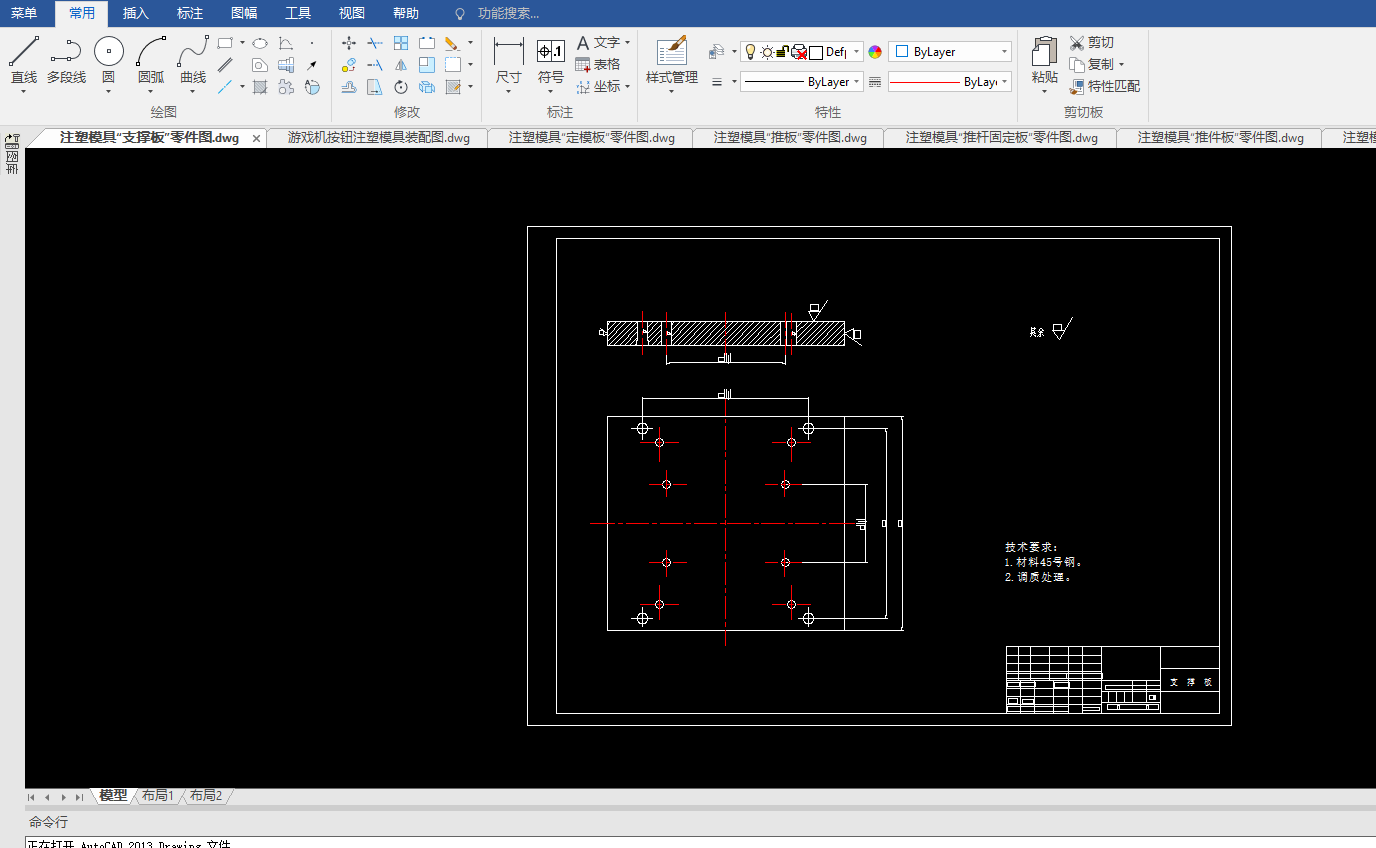
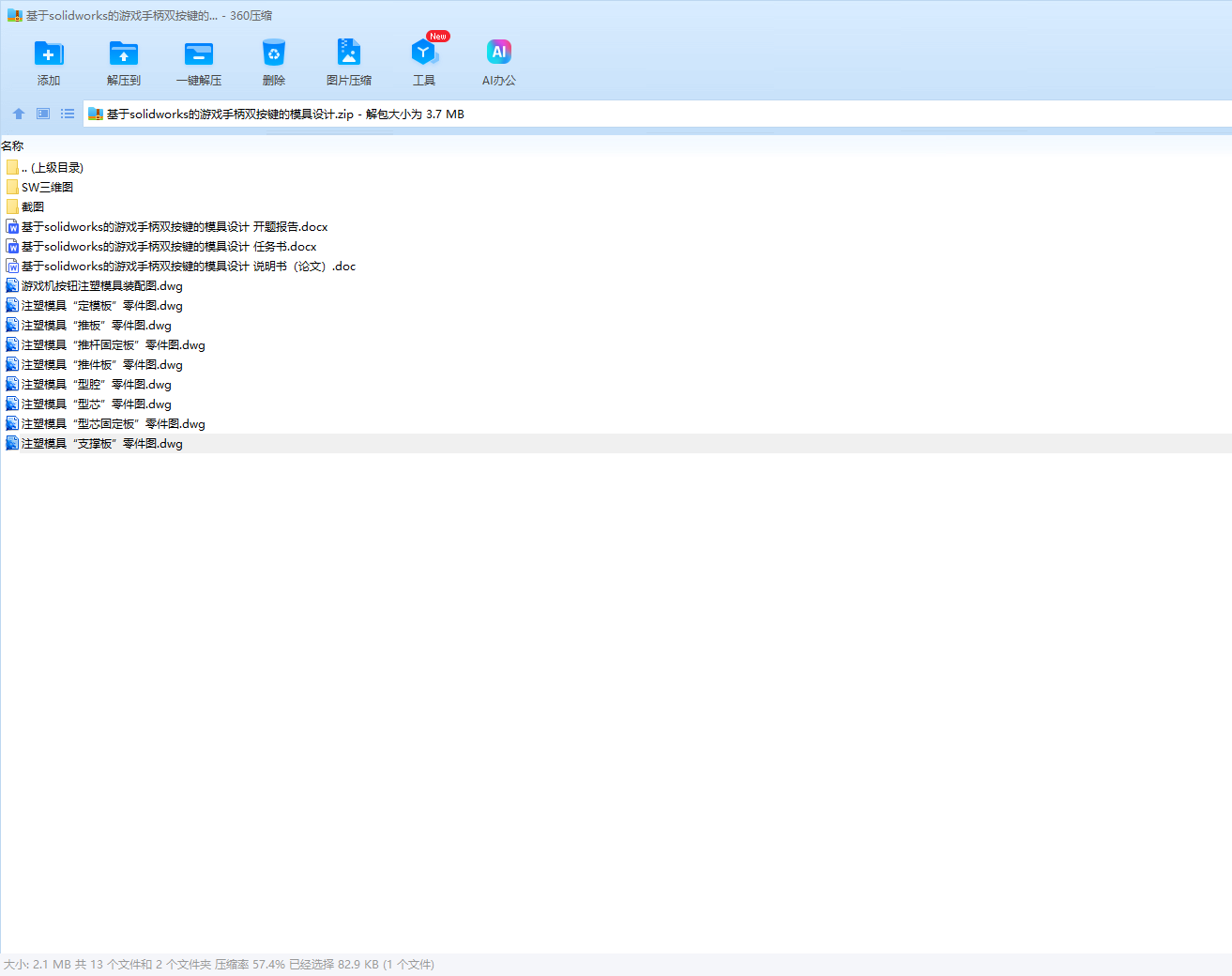
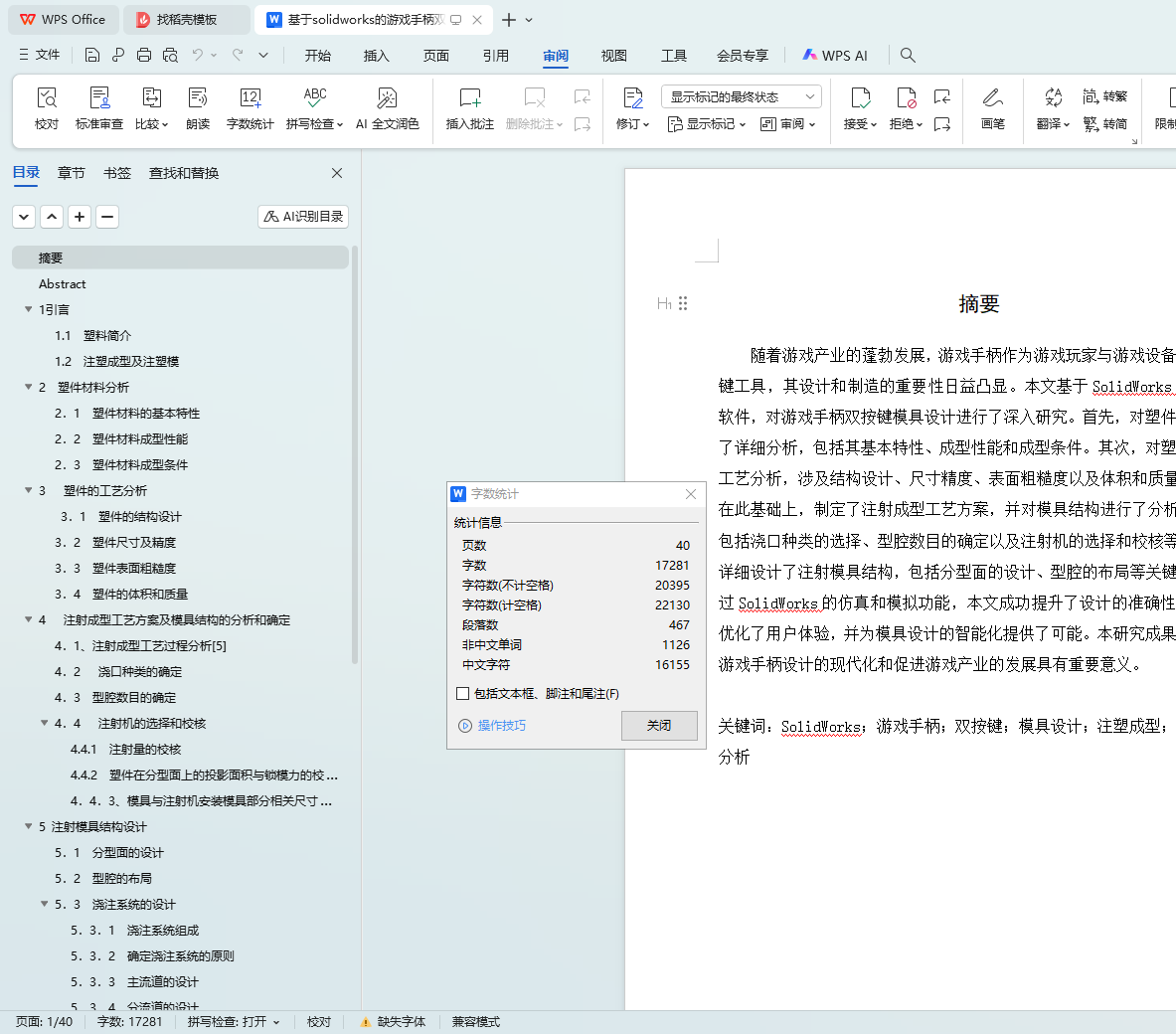
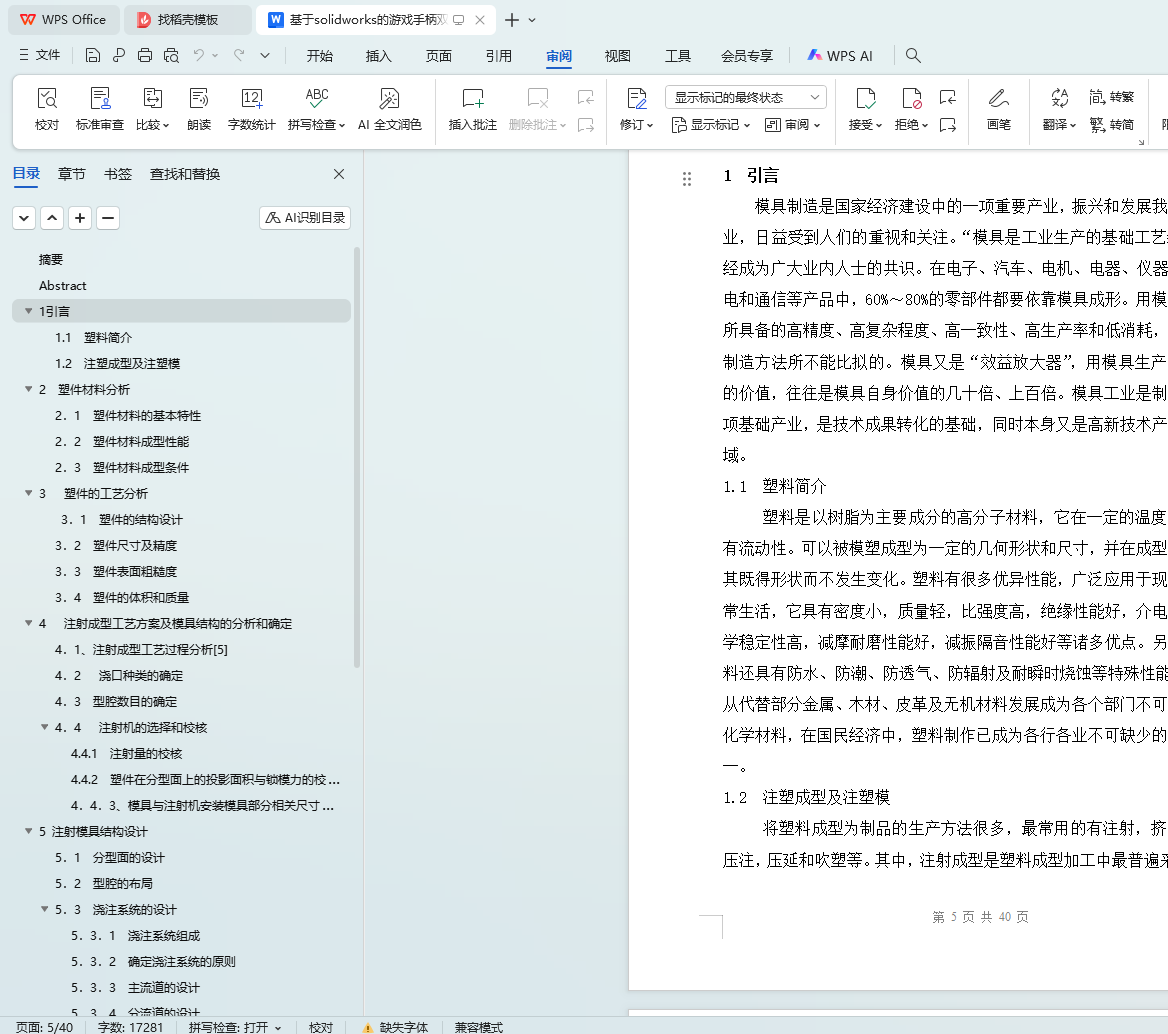
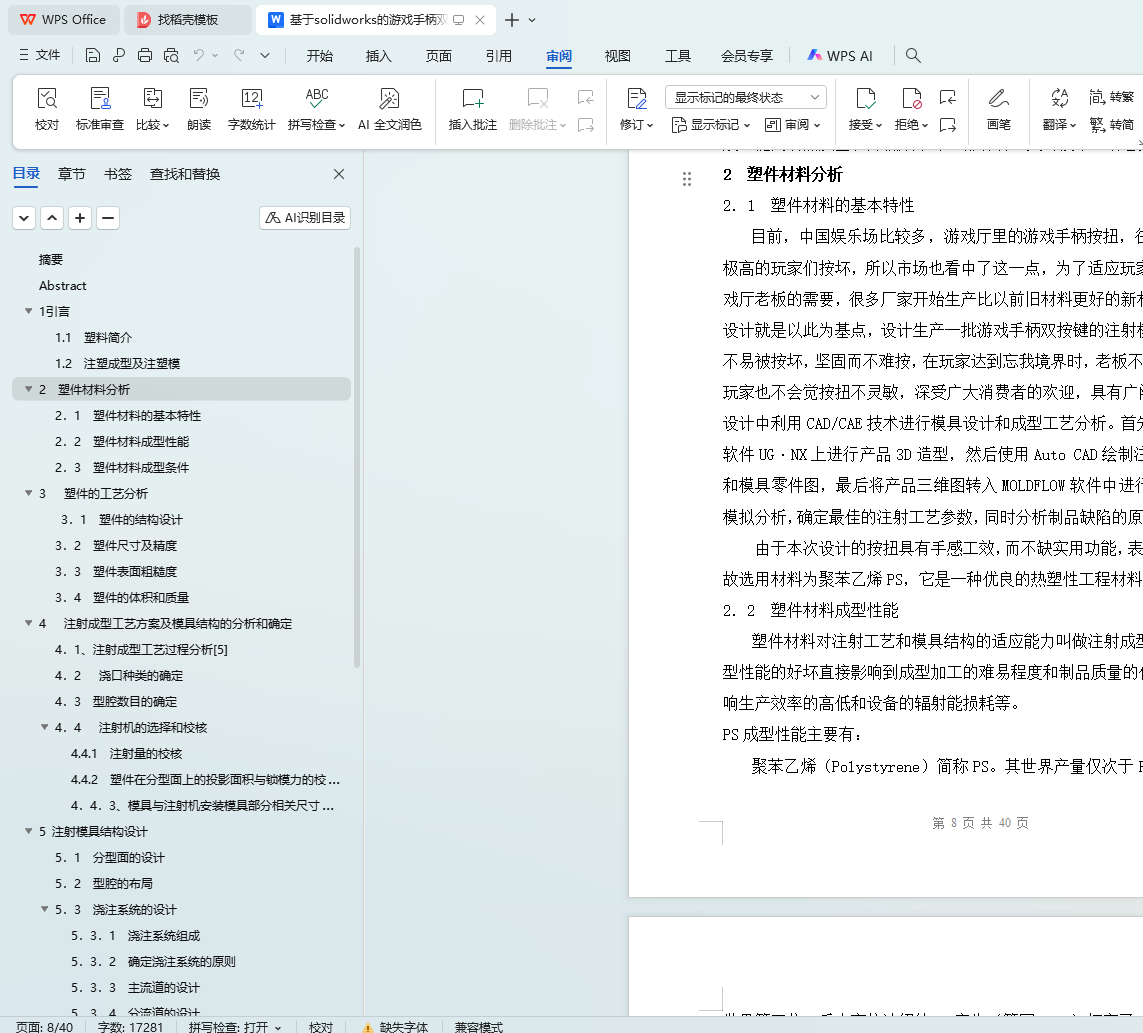
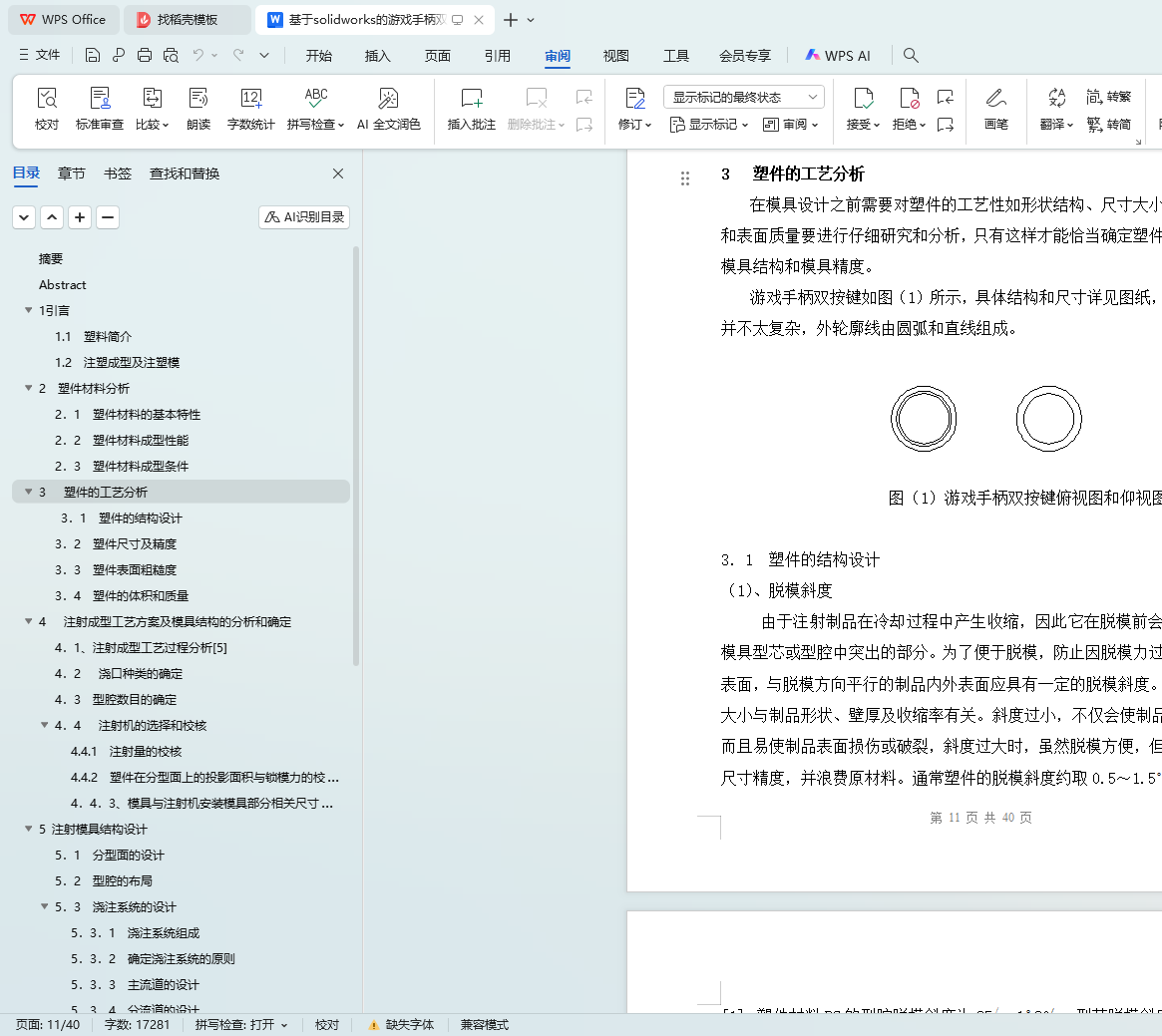
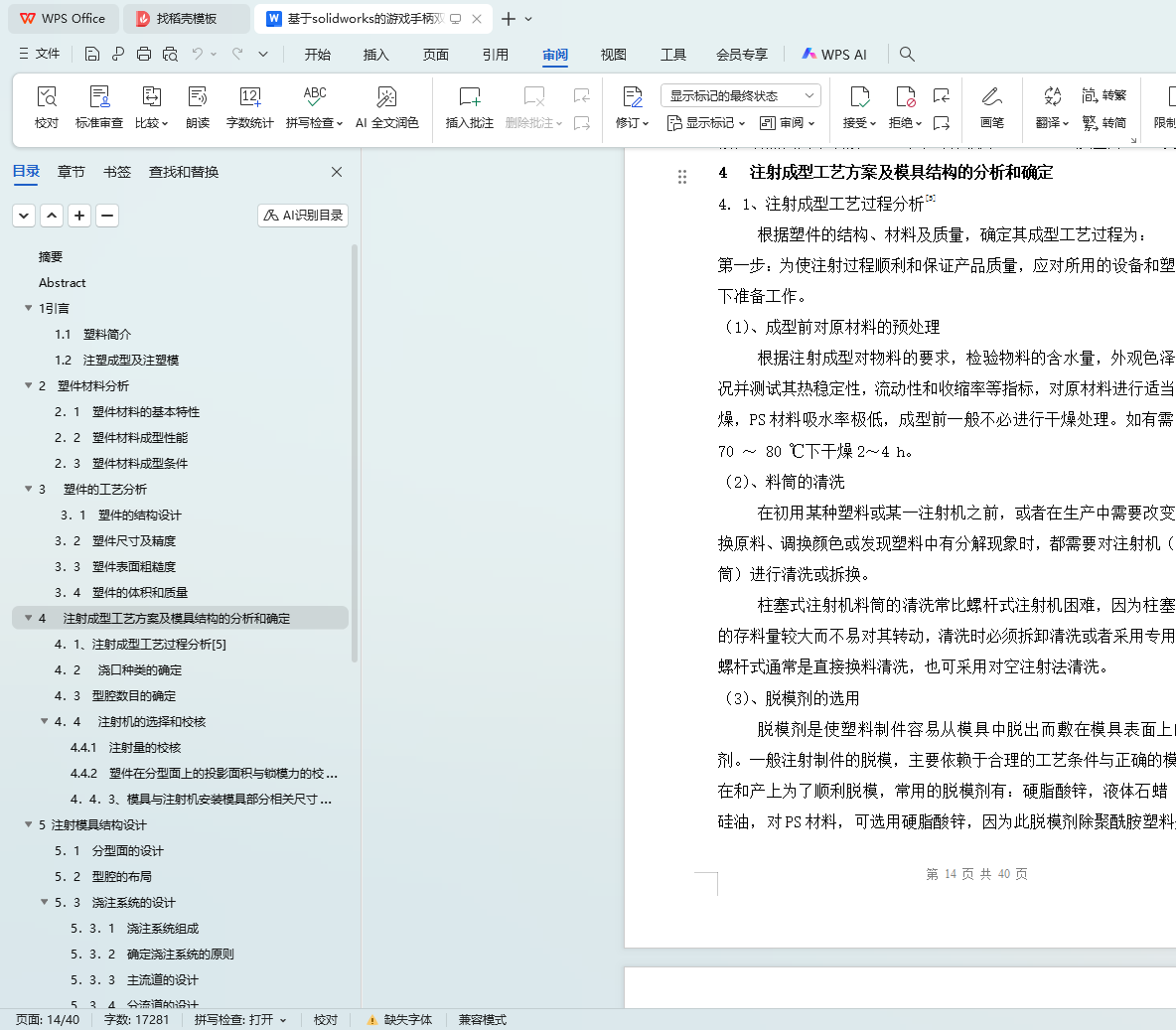
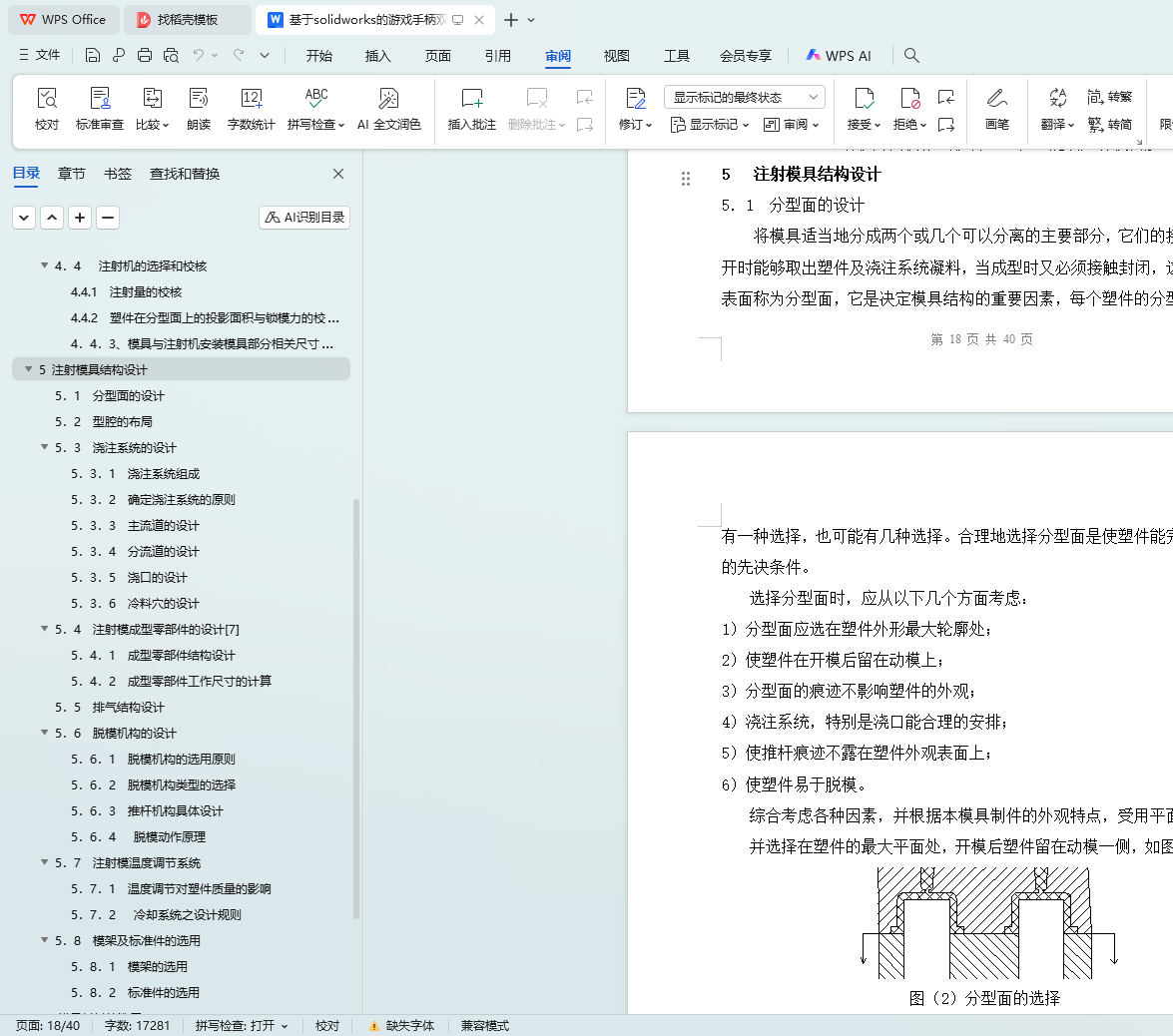
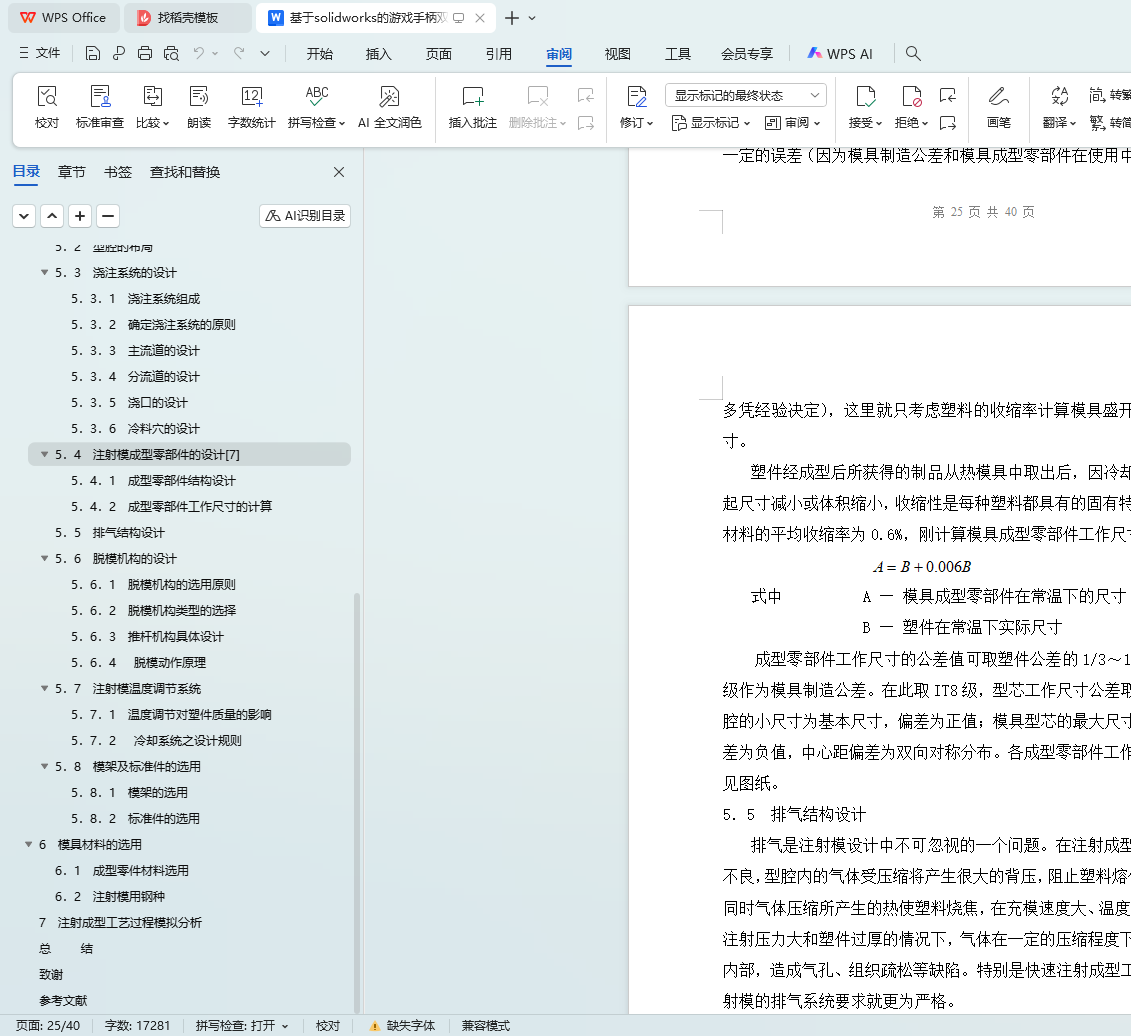
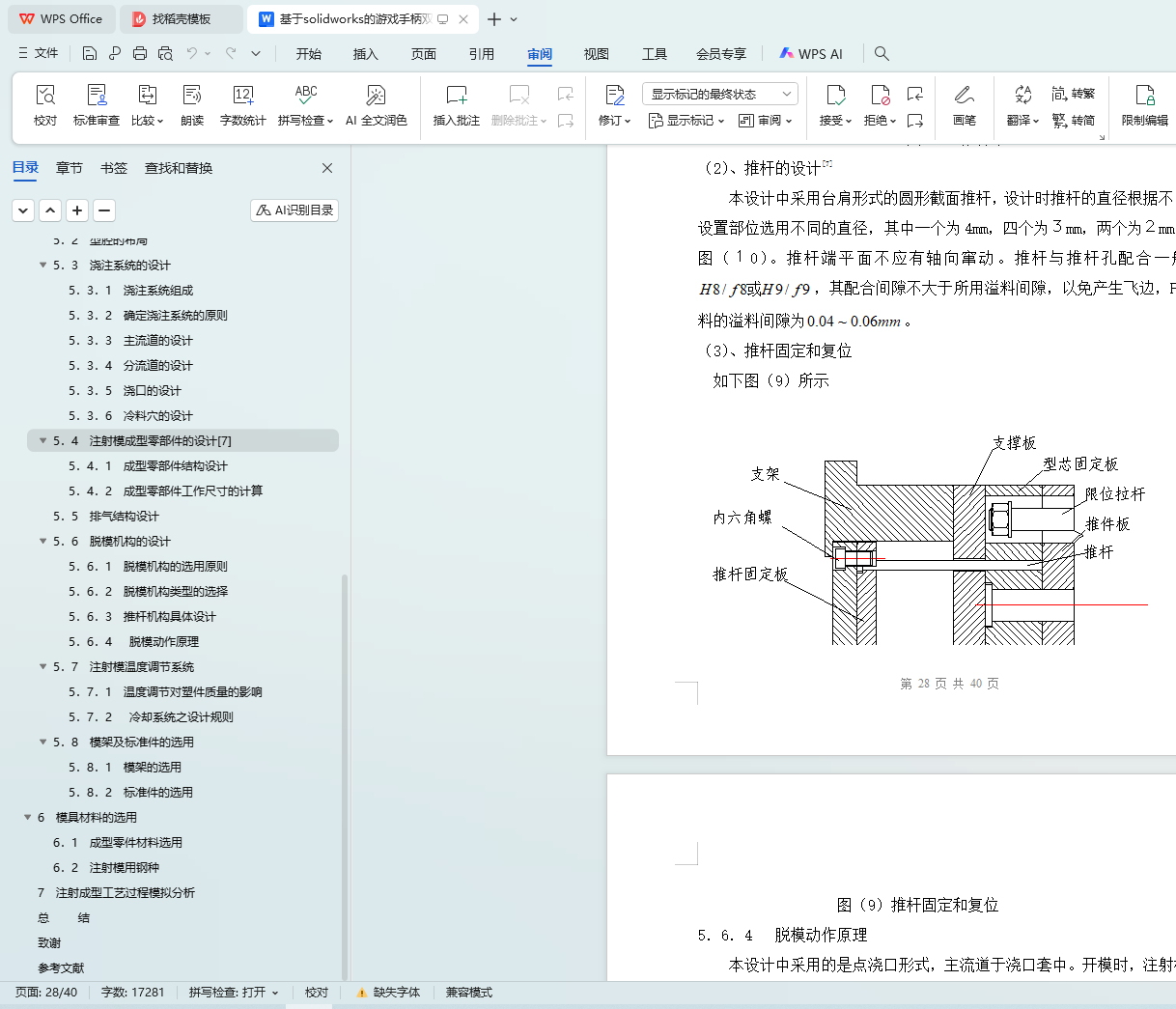
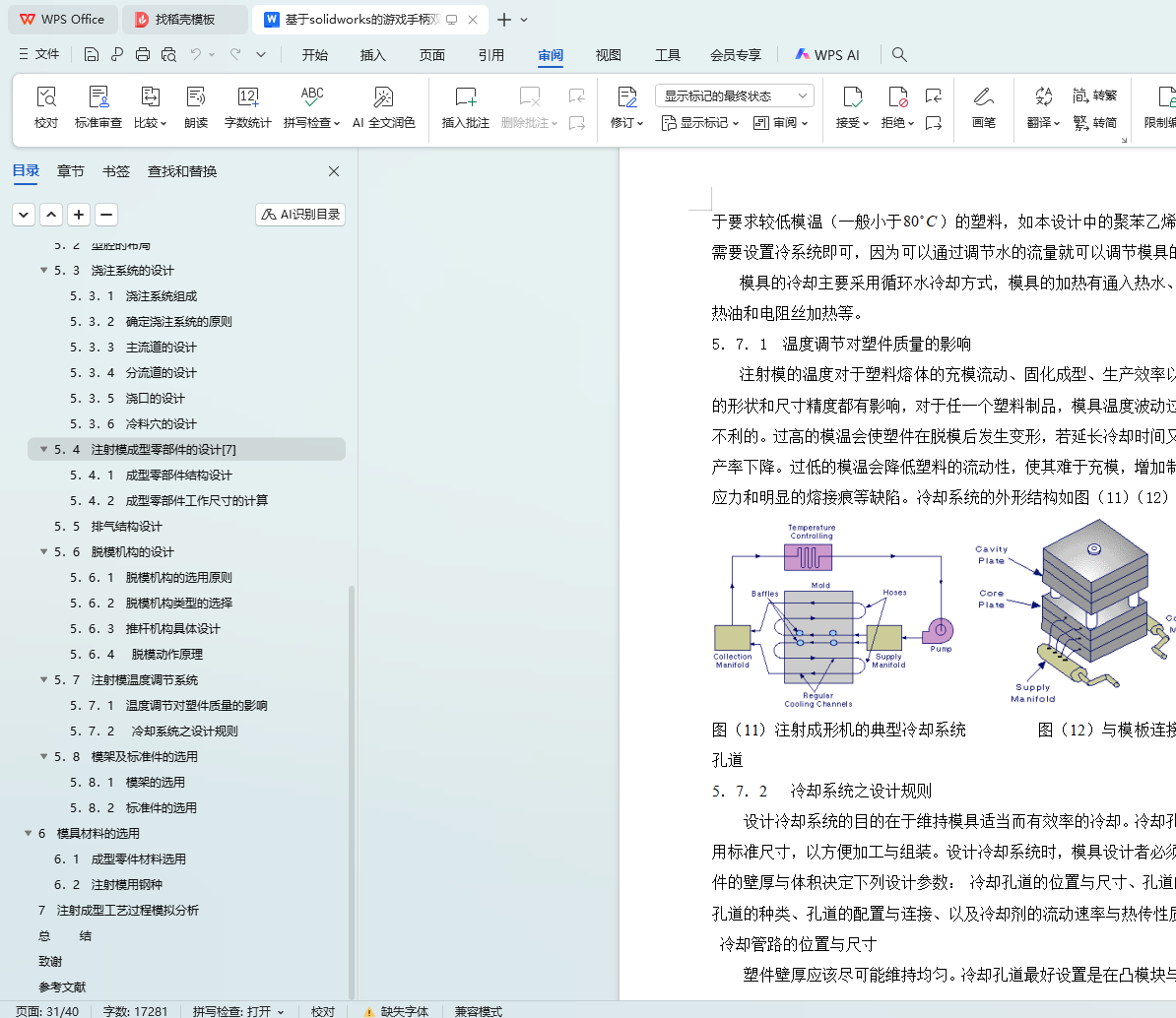
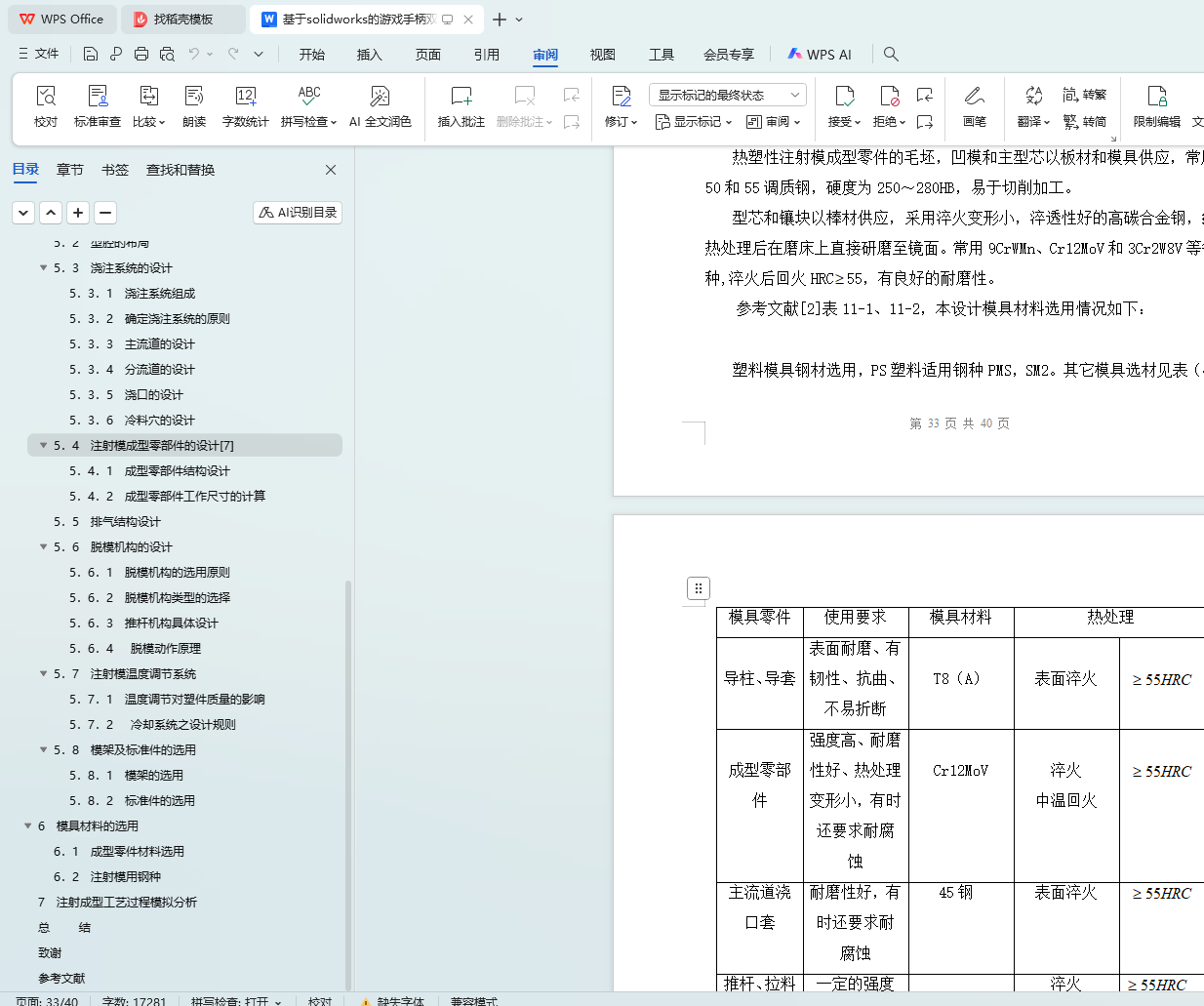
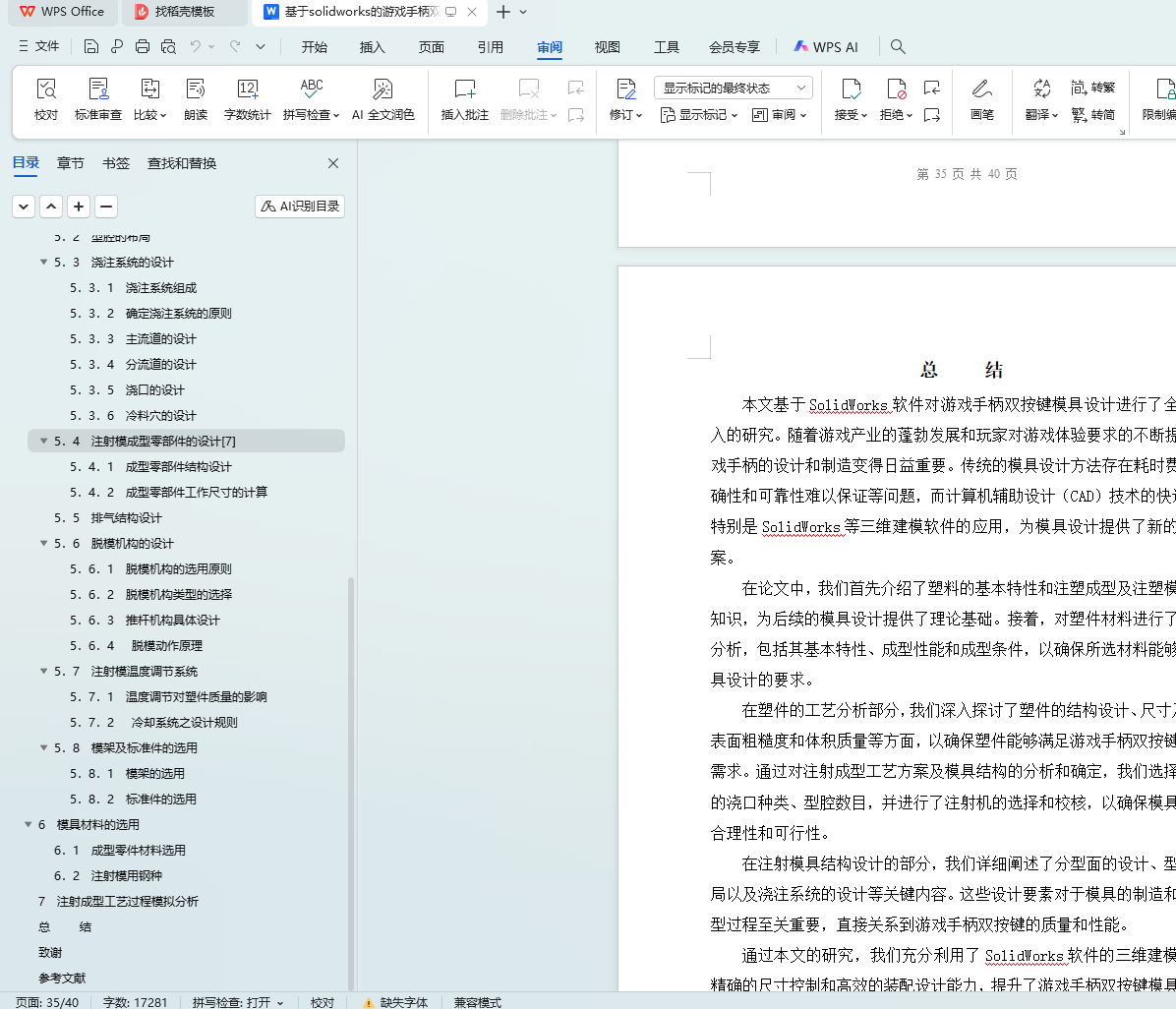