温度控制和PID控制器简介
过程控制系统
自动过程控制系统是指把温度、压力、流量、成份等相关的过程变量保持在要求的运行值的一类系统。过程实际上是动态的。变化总是时时在发生的,此时如果不采取相应的措施,那些与安全、产品质量和生产率有关的工艺参数就不能满足设计要求。
为了理清思路,让我们来看一下热交换器,流体在这个过程中被过冷凝蒸汽加热,过程如图1所示。
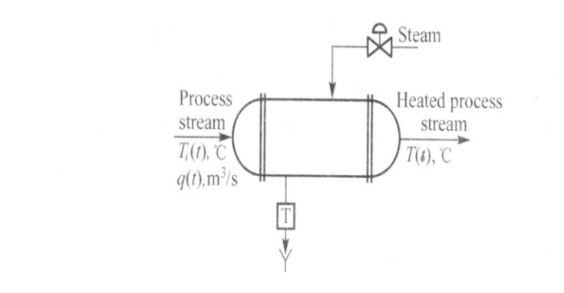
图1热交换器
这一装置的目的是将流体由入口温度Ti(t)加热到某一期望的出口温度T(t)。如前所述,加热介质是冷凝蒸汽。
只要周围没有热损耗,即热交换器和管道间的隔热性都很好,过程流体获得的热量就等于蒸汽释放的热量。
在这个过程中很多变量会发生变化,导致出口温度偏离期望值。如果出现这种情况,就应该采取一些措施来校正温度偏差,目的是控制出口温度至期望值。
实现该目的的一种方法是首先设定初始温度T(0),然后与期望值相比较,由比较结果决定如何校正偏差。蒸汽的流量可用于偏差的校正。就是说,如果温度高于期望值,就关小蒸汽阀来减小进入热交换器的蒸汽流量;若温度低于期望值,就开大蒸汽阀来增加进入换热器的蒸汽流量。所有这些操作都可由操作员手动完成,操作很简单,不会出现什么问题。但是,由于多数过程对象都有很多变量需要保持为某一期望值,这个校正过程就需要许多的操作员来进行。因此,我们想自动完成这种控制。就是说,我们需要一种无需操作人员介入就可以控制变量的设备。这就是所谓的自动过程控制。
为了实现上述目标,就需要设计一个可行的控制系统。图2为一个可行的控制系统及其基本构件。
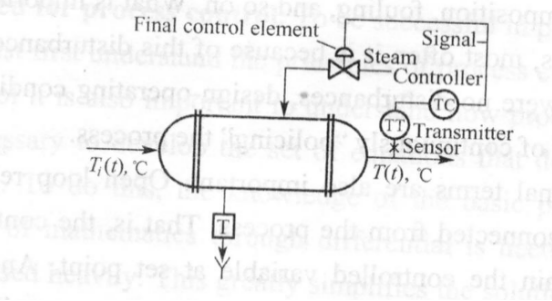
图2热交换器的控制回路
首先要做的是测量过程流体的出口温度,这一任务由传感器(热电偶、热电阻等)完成。传感器连接到发射器上,发射器将传感器的输出信号转换为足够大的信号传送给控制器。控制器接收与温度相关的信号并与期望值进行比较。根据比较的结果,控制器决定如何保持温度为期望值。基于这一结果,控制器再发一信号给执行机构来轮流控制蒸汽流量。
以上的叙述表明整个控制系统有四个基本组成部分,分别是:
(1)传感器,也称为一次元件。
(2)发射器,也称二次元件。
(3)控制器,控制系统的“大脑”。
(4)执行机构,通常是一个控制阀,但并不全是。其他常用的执行机构有变速泵、传送装置和电动机。
这些元件的重要性在于它们执行每个控制系统中都必不可少的3个基本操作,即:
(1)测量:被控量的测量通常由传感器和发射器共同完成。
(2)决策:根据测量结果,控制器必须决定如何进行操作维持输出为期望值。
(3)操作:根据控器的处理,系统必须执行某种操作,这通常由执行机构来完成。
如上所述,每个控制系统都必须有M,D和A这三种操作。
PID控制器可以是独立控制器(也可以叫做单回路控制器),可编程控制器(PLCS)中的控制器,嵌入式控制器是用VB或C#编写的计算机程序软件。
PID控制器是过程控制器,它具有如下特征:
(1)连续过程控制;
(2)模拟输入(也被称为“测量量”或“过程变量”或“PV”);
(3)模拟输出(简称为“输出”);
(4)基准点(SP);
(5)比例、积分以及微分常数;
“连续过程控制”的例子有温度、压力、流量及液位控制。例如:控制一个容器的热量。对于简单的控制,你需要两个具有温度限定功能的传感器(一个温度下限,一个温度上限)。当低温限定传感器接通时就会打开加热器,当温度升高到高温限定传感器时就会关闭加热器。这类似于大多数家庭使用的空调及供暖设备的温度自动调节器。
反过来,PID控制器能够接受像实际温度这样的输入,来控制阀门,这个阀门能够控制进入加热器的气体流量。PID控制器自动地找到加热器中气体的合适流量,这样就保持了温度在基准点稳定。温度稳定了,就不会在高低两点间上下跳动了。如果基准点降低,PID控制器就会自动降低加热器中气体的流量。如果基准点升高,PID控制器就会自动的增加加热器中气体的流量。同样地,对于高温,晴朗的天气(当外界温度高于加热器时)及阴冷,多云的天气,PID控制器都会自动调节。
模拟输入(测量量)叫做“过程变量”或“PV”。你希望PV能够达到你所控制过程参数的高精确度。例如,如果我们想要保持温度为+1度或—1度,我们至少要努力使其精度保持在0.1度。如果是一个12位的模拟输入,传感器的温度范围是从0度到400度,我们计算的理论精确度就是400除以44096 ,即0.097656度。我们之所以说这是理论上的因为我们假设温度传感器,电线及模拟转换器上没有噪音和误差。还有其他的假定,如线性等等。即使是有大量的噪音和其他问题,按理论精确度的1/10计算,1度精确度的数值应该很容易得到的。
模拟输出经常被简称为“输出”。经常在0%到100%之间给出。在这个热量的例子中阀门完全关闭(0%),完全打开(100%)。
基准点(SP)很简单,即你想要什么样的过程量。在这个例子中你想要该过程处于怎样的温度。
PID控制器的任务是维持输出在某一个程度上,这样在过程变量(PV)和基准点(SP)上就没有偏差(误差)。
在图3中,阀门用来控制进入加热器的气体,冷却器的制冷,水管的压力,水管的流量,容器的水位或其他的过程控制系统。PID控制器所观察的是PV和SP之间的偏差(或误差)。它观察绝对偏差和偏差变换率。绝对偏差就是'PV和SP之间偏差是大还是小。偏差变换率就是——PV和SP之间的偏差随着时间的变化是越来越小还是越来越大。
SETPOINT P,I,&D

CONSTANTS

Difference error PID control

algorithm
process output
variable
图3 PID控制器
如果存在过程扰动,即过程变量或基准点迅速变化时,PID控制器就要迅速改变输出,使过程变量快速返回到基准点。如果你有一个PID控制的可进入的冷冻装置,某个人打开门进入,温度(过程变量)将会迅速升高。因此,PID控制器不得不提高冷却(输出)来补偿这个温度的升高。
一旦过程变量等同于基准点,一个好的PID控制器就不会改变输出。你所要的输出是非常稳定的(不会改变)。如果阀门(发动机或其他控制器件)不断改变,而不是维持恒量,这将造成控制元件更多的磨损。
这样就有了两个矛盾的目标。当有“过程扰动”时能够快速反应(快速改变输出)。当PV接近基准点时就缓慢反应(平稳输出)。
我们注意到输出量经常超过稳定状态输出使过程变量回到基准点。比如,一个制冷器通常打开它的制冷阀门的34%,就可以维持在零度(在制冷器关闭和温度降低后)。如果某人打开制冷器,走进去,四处走,找东西,然后再走出来,再关上制冷器的门,PID控制器会非常活跃,因为温度可能将上升20度。这样制冷阀门就可能打开50%,75%甚至100%,目的是赶快降低制冷器的温度,然后慢慢关闭制冷阀门回到它的34%。
让我们来考虑一下如何设计一个PID控制器。
我们主要集中在过程变量(PV)和基准点(SP)之间的偏差(误差)上。有三种定义误差的方式。
绝对偏差
他说明的是PV和SP之间的偏差有多大。如果PV和SP之间偏差小,那我们就在输出时作一个小的改变。如果PV和SP之间偏差大——那我们就在输出时作一个大的改变。绝对偏差就是PID控制器的比例环节。
累积误差
给我们点时间,我们将会明白为什么仅仅简单地观察绝对偏差(比例环节)是一个问题。累积误差是很重要的,我们把它称为是PID控制器的积分环节。每次我们运行PID算法时,我们总会把最近的误差添加到误差总和中。换句话说,累积误差,误差1+误差2+误差3+误差4+……
滞后时间
滞后时间指的是PV引起的变化由发现到改变之间的延时。典型的例子就是调整你的烤炉在合适的温度。当你刚刚开始加热,烤炉热起来需要一定时间,这就是滞后时间。如果你设置一个初始温度,等待烤炉达到这个初始温度,然后你认为你设定了错误的温度,烤炉达到这个新的温度基准点还需要一段时间。这也被认为是PID控制器的微分环节。这就抑制了某些将来的变化因为输出值已经发生了改变,但并不是受过程变量的影响。
本文摘译自:http://ieeexplore.ieee.org/