摘 要
随着我国经济的快速发展,市场需求在不断的变化,我国制造业面临着巨大的挑战。装配生产线广泛的存在于生产加工的制造业中,装配生产线的平衡,优化问题严重影响着装配线运行效率和整个装配线的产能,最终制约着企业的效益。传统的单一装配生产线已无法满足当今社会需求,许多企业已引入多支线装配线。相比传统的单线装配线,多支线装配线虽提高了装配效率、产线产能,但其优化问题仍制约着企业的发展,所以如何综合考虑对多支线装配生产线优化是一个值得深入研究的问题。
本文以S企业电暖气装配线为研究对象,对其装配线存在的问题进行分析总结。运用科学的技术方法和参考前人的研究成果对存在的问题进行分析改善,从而提高装配线的产能,降低生产成本。
首先,在S企业实习中,观察电暖器装配步骤,记录每个工序流程,收集相关资料,对其工艺流程和装配现状进行汇总。绘画出电暖器装配工艺流程图和各工序工时汇总表。通过对现场观察及数据分析,分析总结了电暖器装配线堆积过多、工人动作重复、换线时间长且次数多、工艺流程不合理等问题。
其次,运用工业工程5W1H提问方法、ECRS四大原则以及秒表测定方法对电暖器装配线的作业流程进行优化分析,改善工艺流程,对装配工序重新分配,装配动作标准化,提高装配效率。同时,运用精益生产中快速换线方法,分析装配线换线存在的问题。了解并记录车间换线操作流程,结合装配车间人员和物料的配置情况,按照快速换线的技术和工业工程的改善方法,重新设计换线流程,减少电暖器装配过长中换线时间;改善清尾物料统计方法,提高尾数物料欠缺的准确性,减少产线堆积现象和换线次数。提高转配效率,提升装配车间产能。
最后,制定出新的装配方案和换线方法。通过换线时间、返工次数和装配线平衡率三方面的改善前后的数据对比,分析总结改善效果。最后总结经验和全文不足。
关键词:工业工程;快速换线;装配线优化;工作研究;精益生产
Abstract
With the rapid development of China's economy and the constant changes in market demand, China's manufacturing industry is facing enormous challenges. The assembly line is widely existed in the manufacturing and manufacturing industries. The balance of the assembly line and the optimization problem seriously affect the operation efficiency of the assembly line and the production capacity of the entire assembly line, which ultimately limits the efficiency of the enterprise. Traditional single assembly lines have been unable to meet the needs of today's society, and many companies have introduced multi-branch assembly lines. Compared with the traditional single-line assembly line, the multi-branch assembly line improves the assembly efficiency and production line capacity, but its optimization problem still restricts the development of the enterprise. Therefore, how to comprehensively consider the optimization of the multi-branch assembly line is a problem worthy of further study.
This paper takes S enterprise electric heating assembly line as the research object, and analyzes and summarizes the problems existing in its assembly line. The use of scientific technical methods and reference to previous research results to improve existing problems, thereby increasing assembly line capacity and reducing production costs.
First, in the S company internship, observe the electric heater assembly steps, record each process flow, collect relevant data, and summarize the process flow and assembly status. Paint out the electric heater assembly process flow chart and the summary of each process man-hour. Through on-site observation and data analysis, the paper analyzes and summarizes the problems of excessive stacking of electric heater assembly lines, repeated worker actions, long time-changing lines and many times, and unreasonable process flow.
Secondly, using the industrial engineering 5W1H questioning method, the ECRS four principles and the stopwatch measurement method to optimize the operation flow of the electric heater assembly line, improve the process flow, redistribute the assembly process, standardize the assembly action, and improve the assembly efficiency. At the same time, using the quick change line method in lean production, analyze the problems existing in the assembly line change line. Understand and record the shop change line operation process, combine the assembly shop personnel and material configuration, redesign the line change process according to the quick change line technology and industrial engineering improvement method, and reduce the long line change time of the electric heater assembly; Improve the statistical method of material cleaning materials, improve the accuracy of the lack of mantissa materials, reduce the accumulation of production lines and the number of line changes. Improve transfer efficiency and increase assembly plant capacity.
Finally, develop a new assembly plan and method of changing lines. Through the data comparison before and after the improvement of the changeover time, the number of rework and the assembly line balance rate, the improvement effect is analyzed and summarized. Finally, the experience and the full text are insufficient. .
Keywords: Industrial engineering; Quick change line; Assembly line optimization; Work research;Lean production
目 录
摘 要 I
Abstract II
1 绪论 1
1.1 研究背景以及意义 1
1.2国内外装配线优化研究现状 2
1.3本文研究内容和框架 4
1.4本章小结 6
2. S企业生产现状分析 7
2.1S企业的介绍 7
2.2装配车间问题分析 7
2.3电暖器装配工艺流程分析 11
2.4本章小结 16
3.装配车间的优化研究 17
3.1电暖器装配工艺优化 17
3.2装配线的换线方案优化 27
3.3装配车间的物料控制 32
3.4本章小结 36
4.优化方案改善效果分析 37
4.1优化效果对比 37
4.2改善意见 38
4.3本章小结 39
5.总结与展望 40
5.1总结 40
5.2展望 41
参考文献 42
致谢 44
翻译部分 45

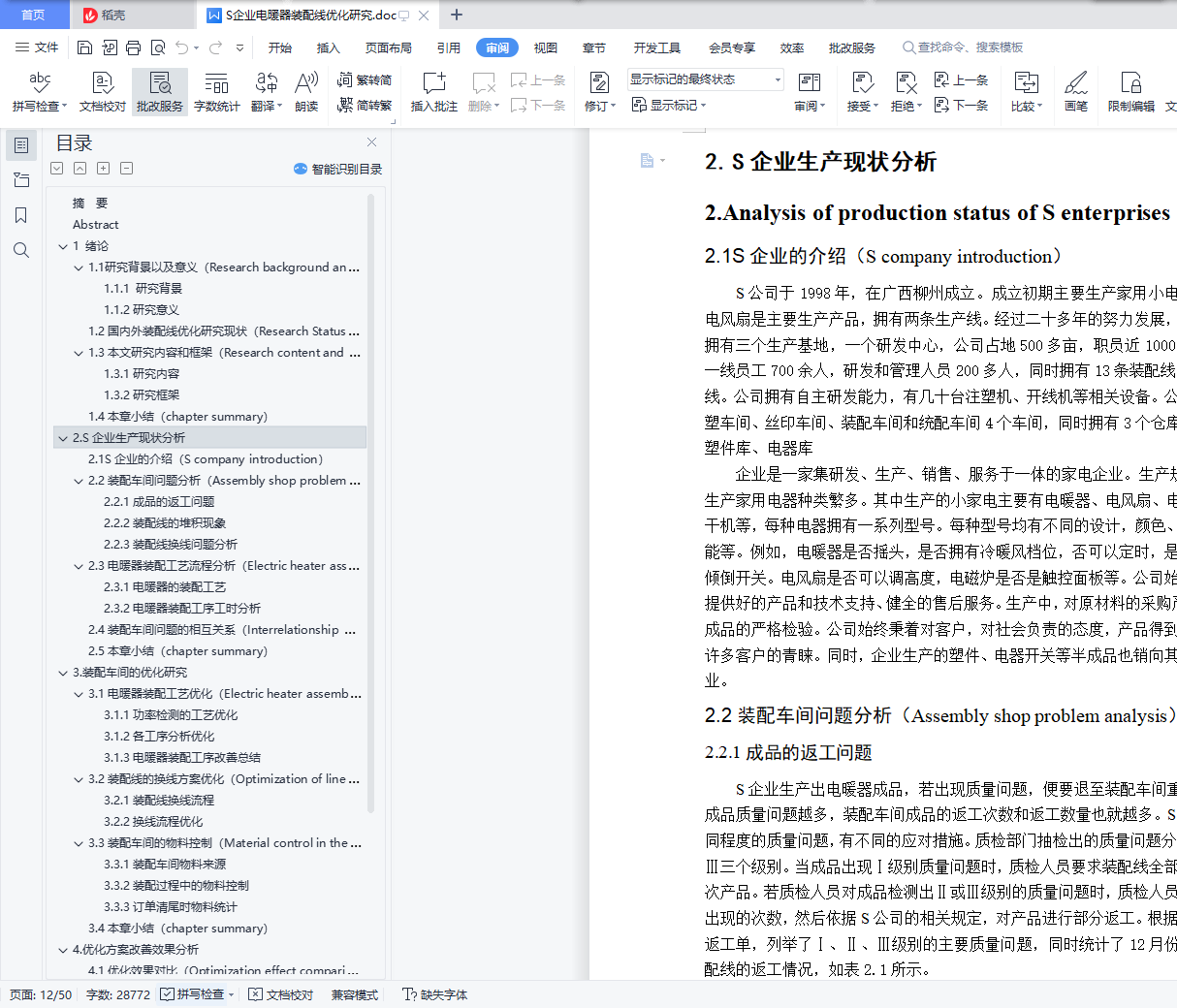
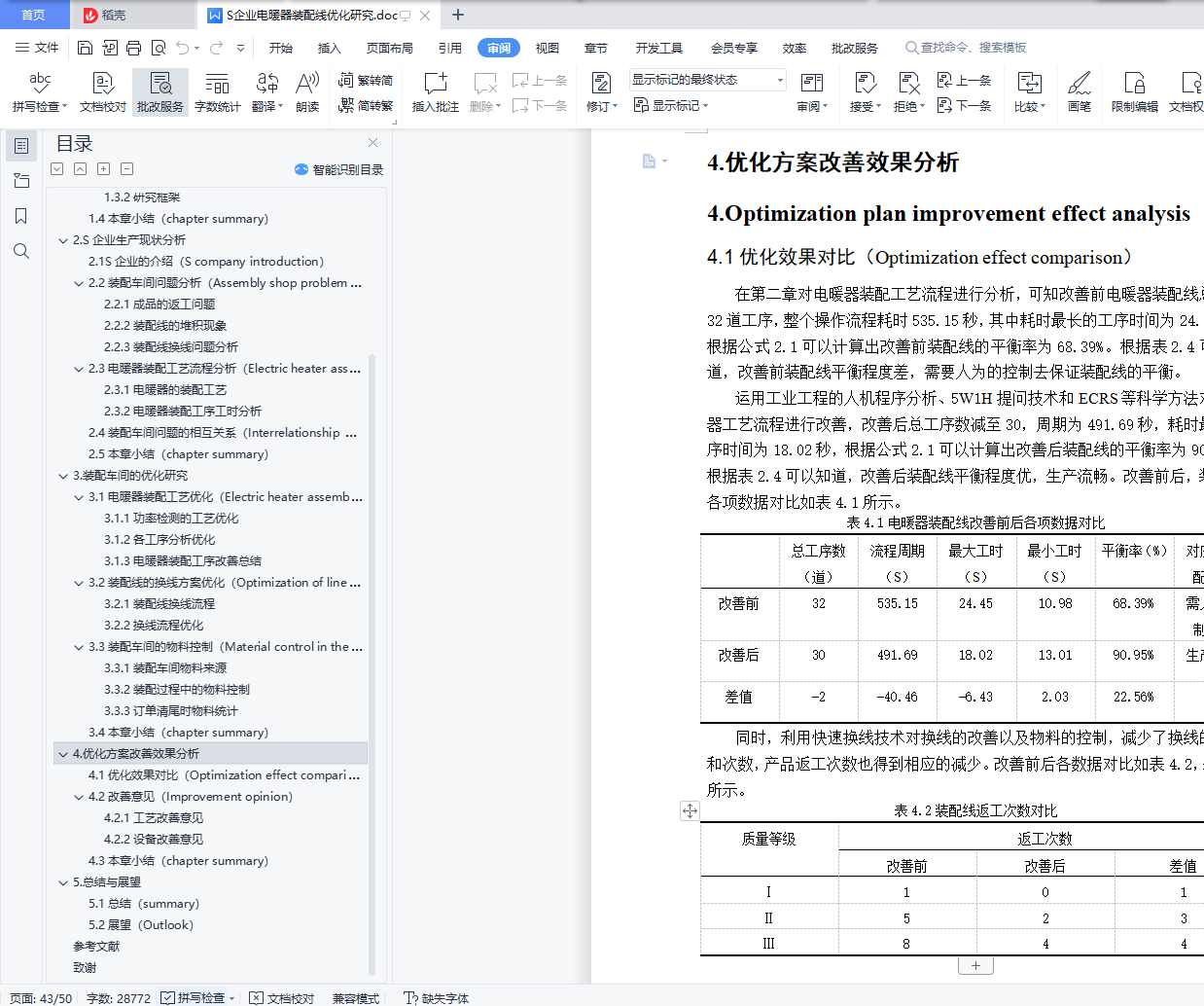
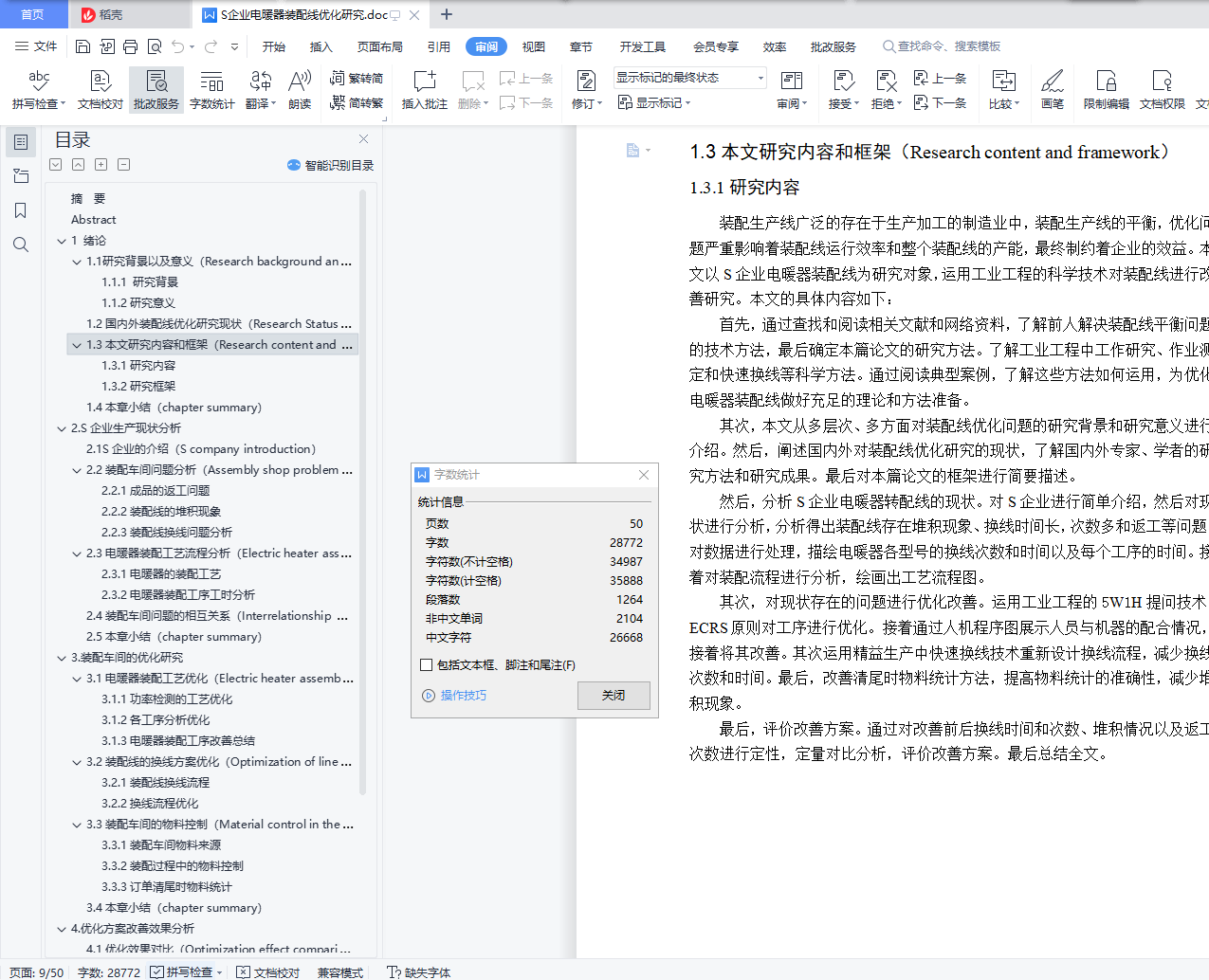
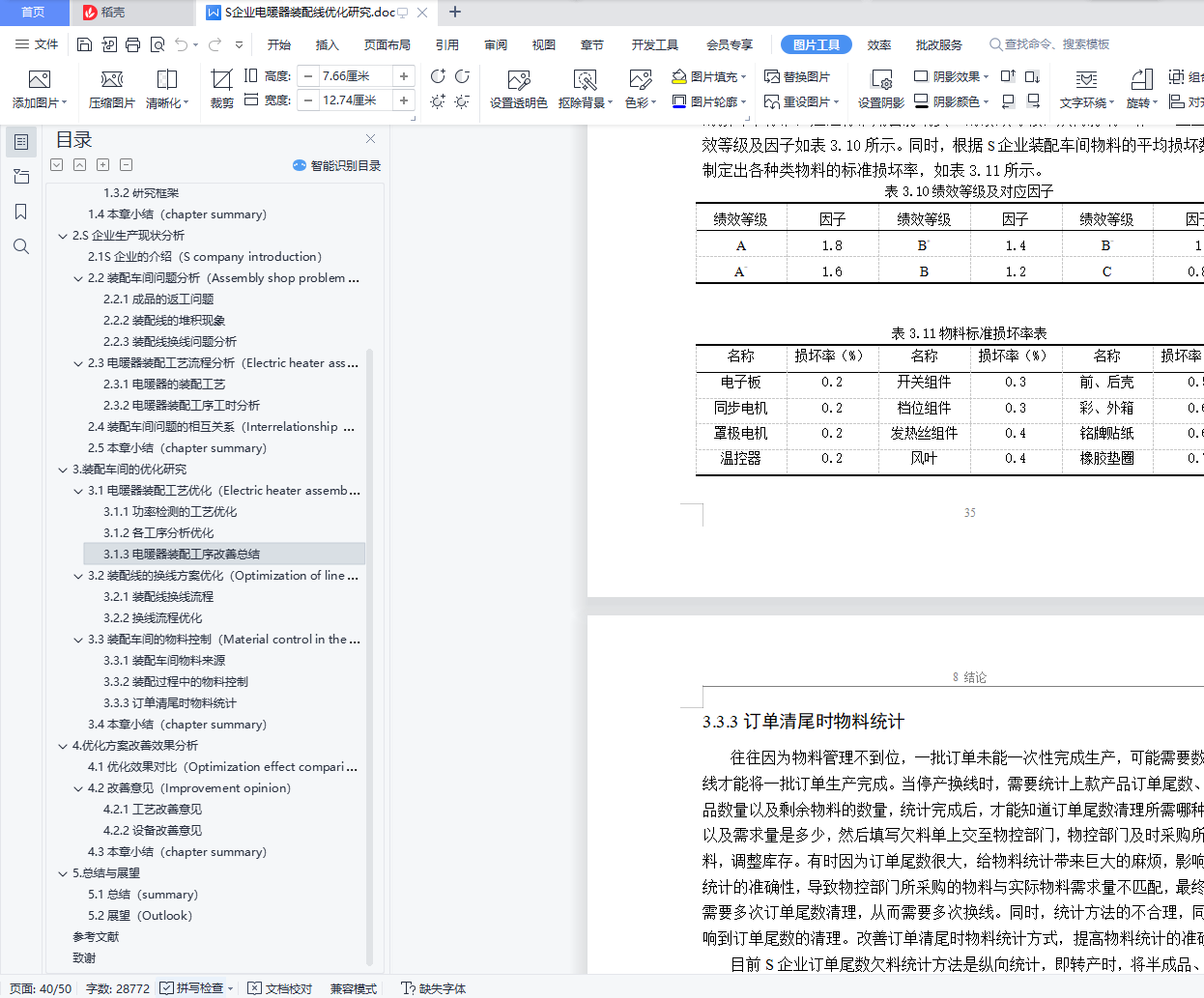
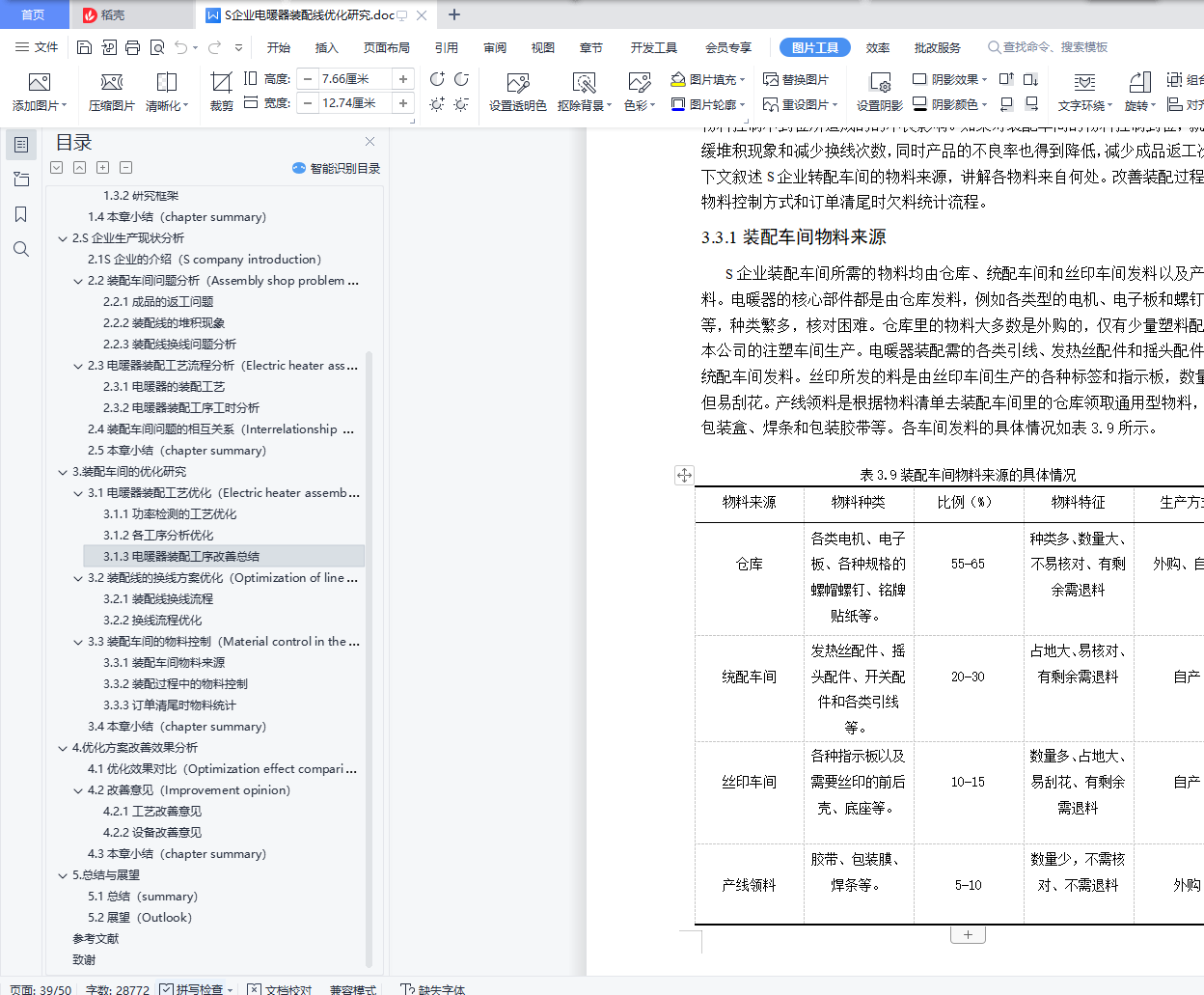
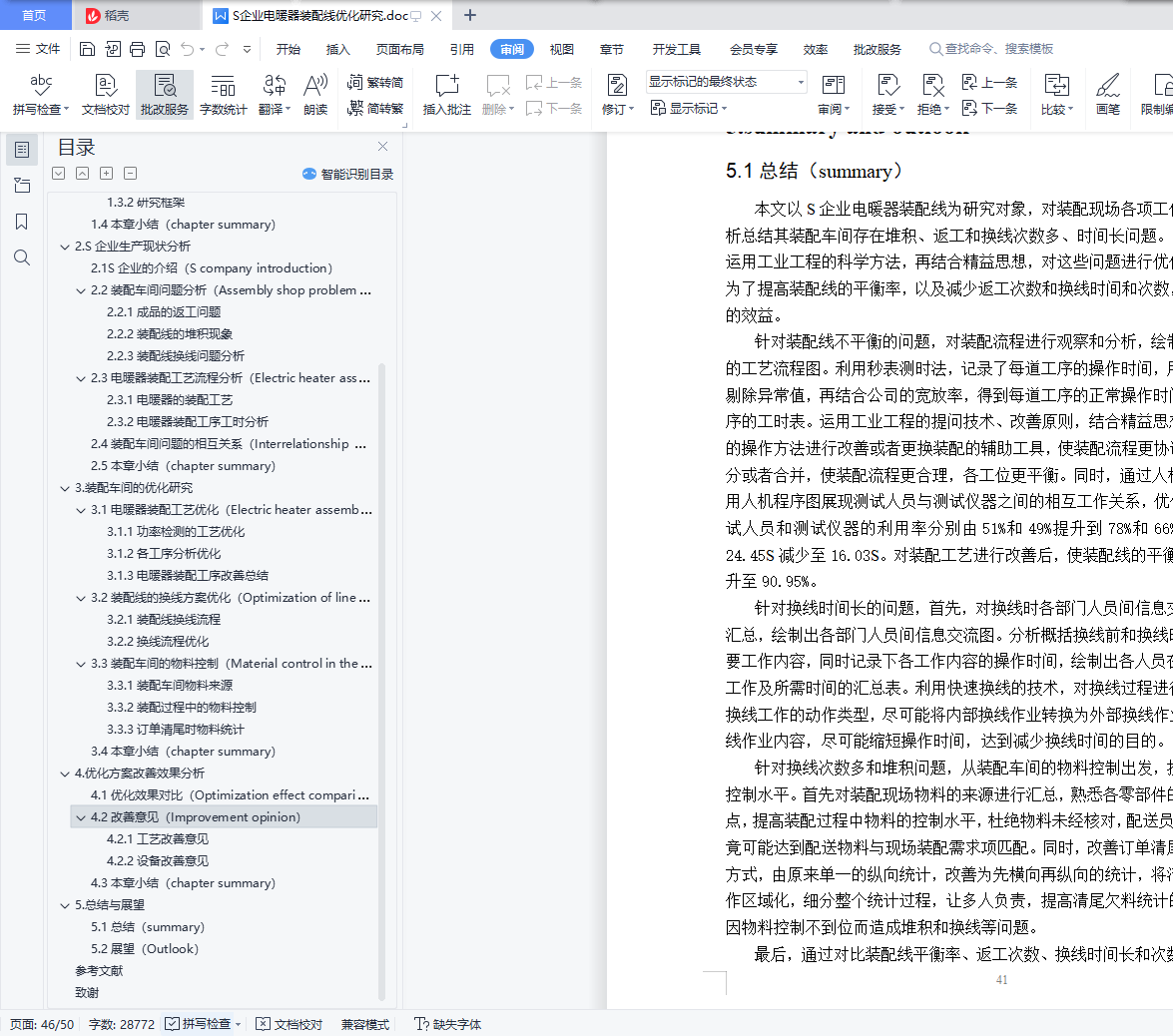
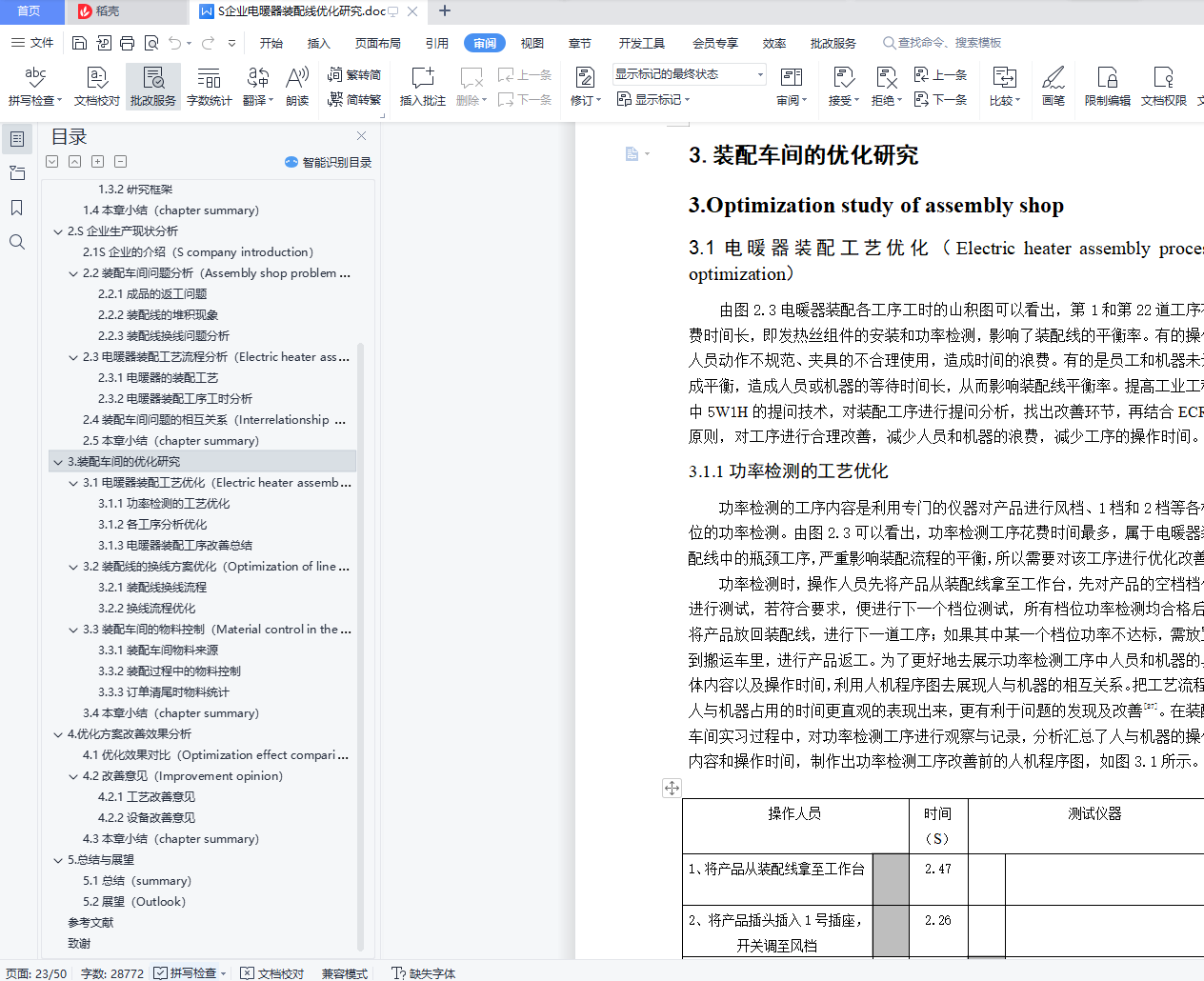
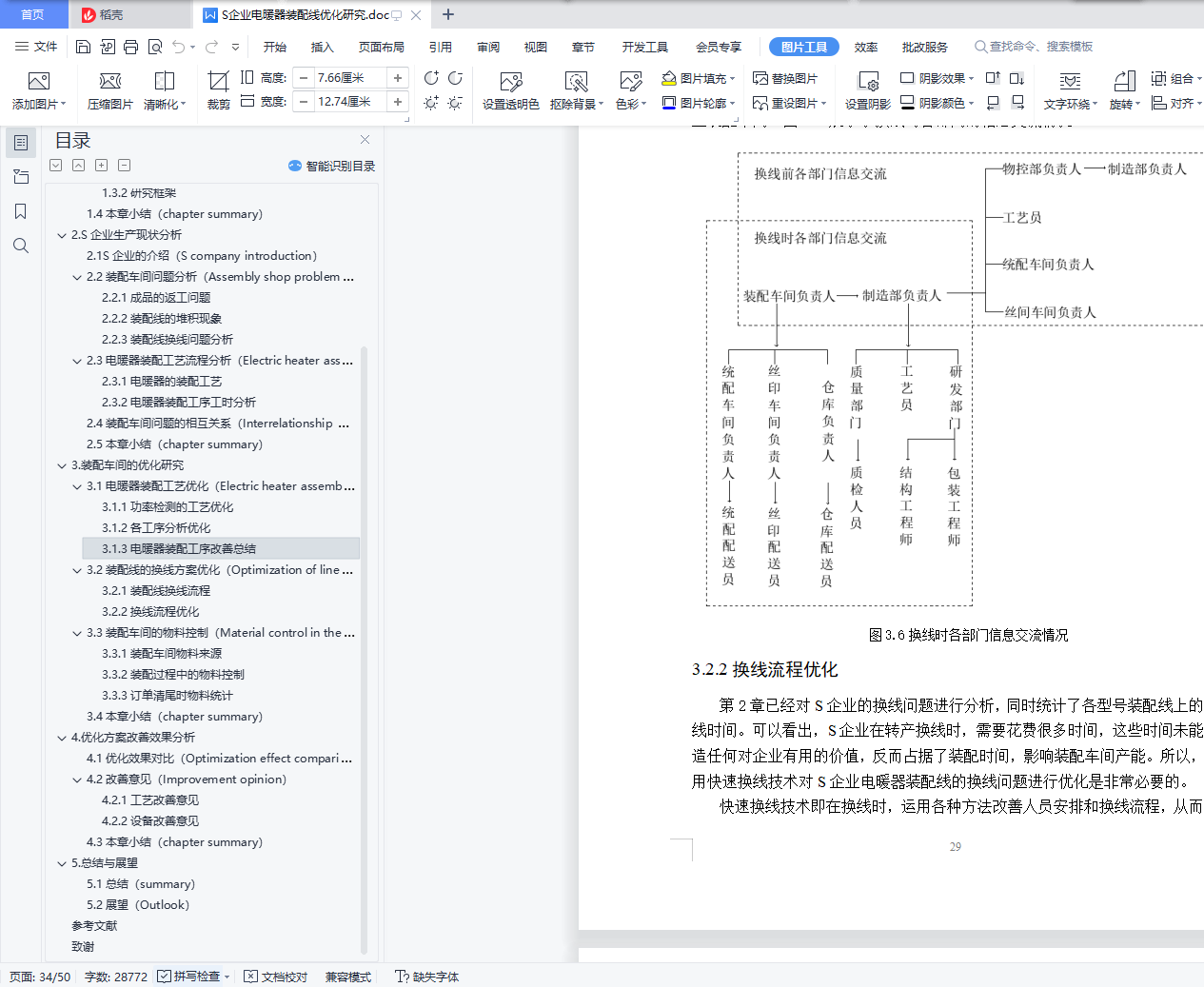
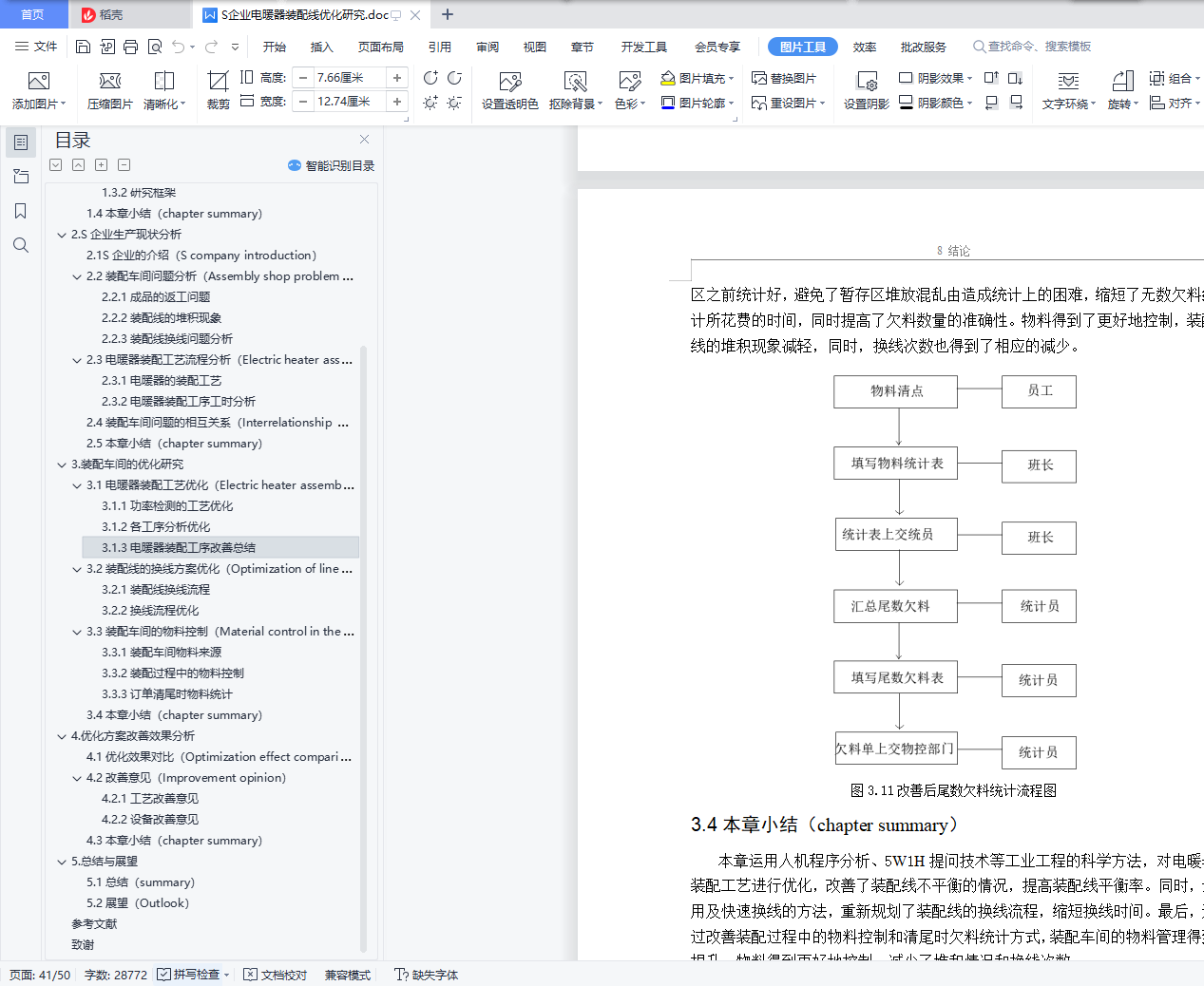
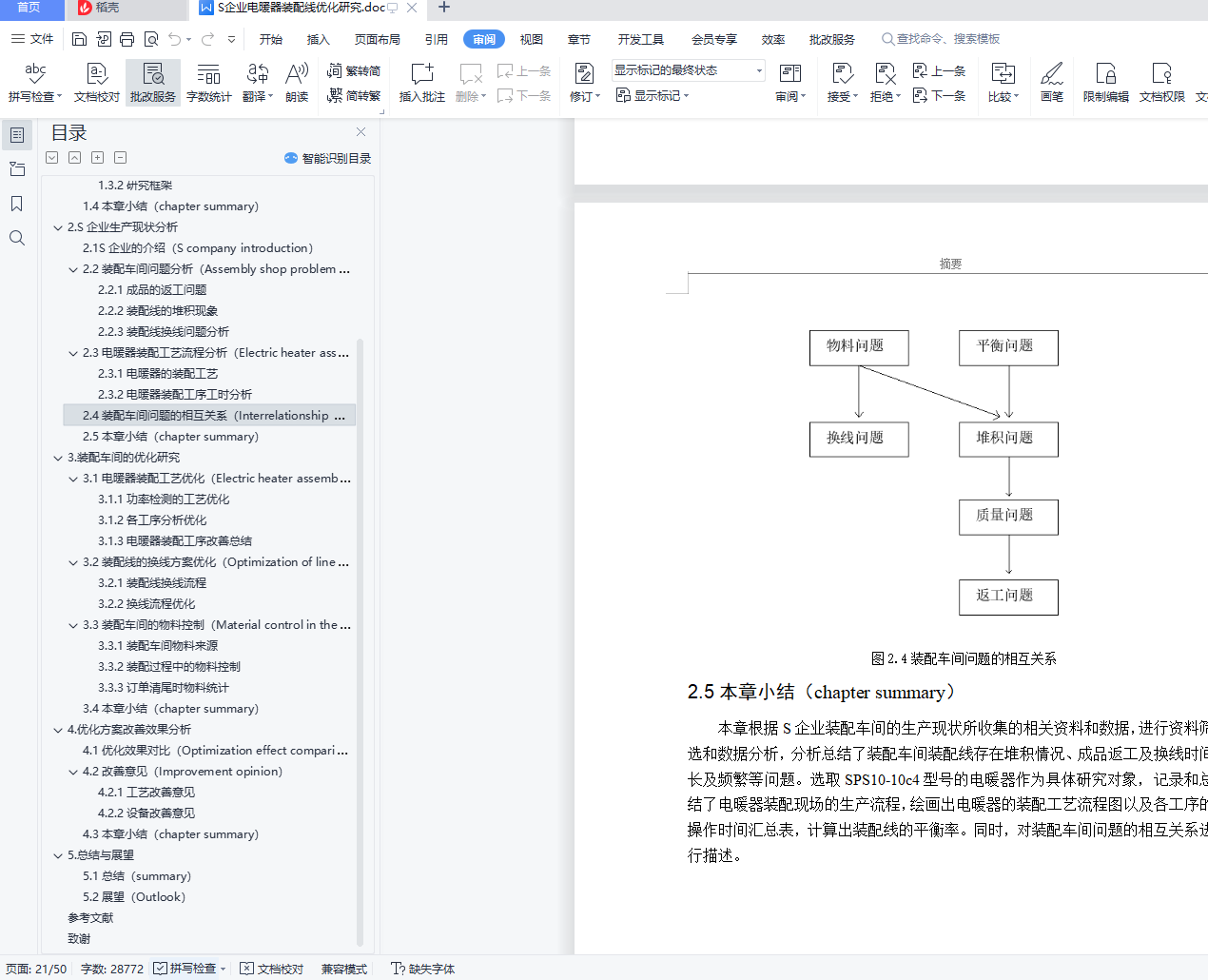
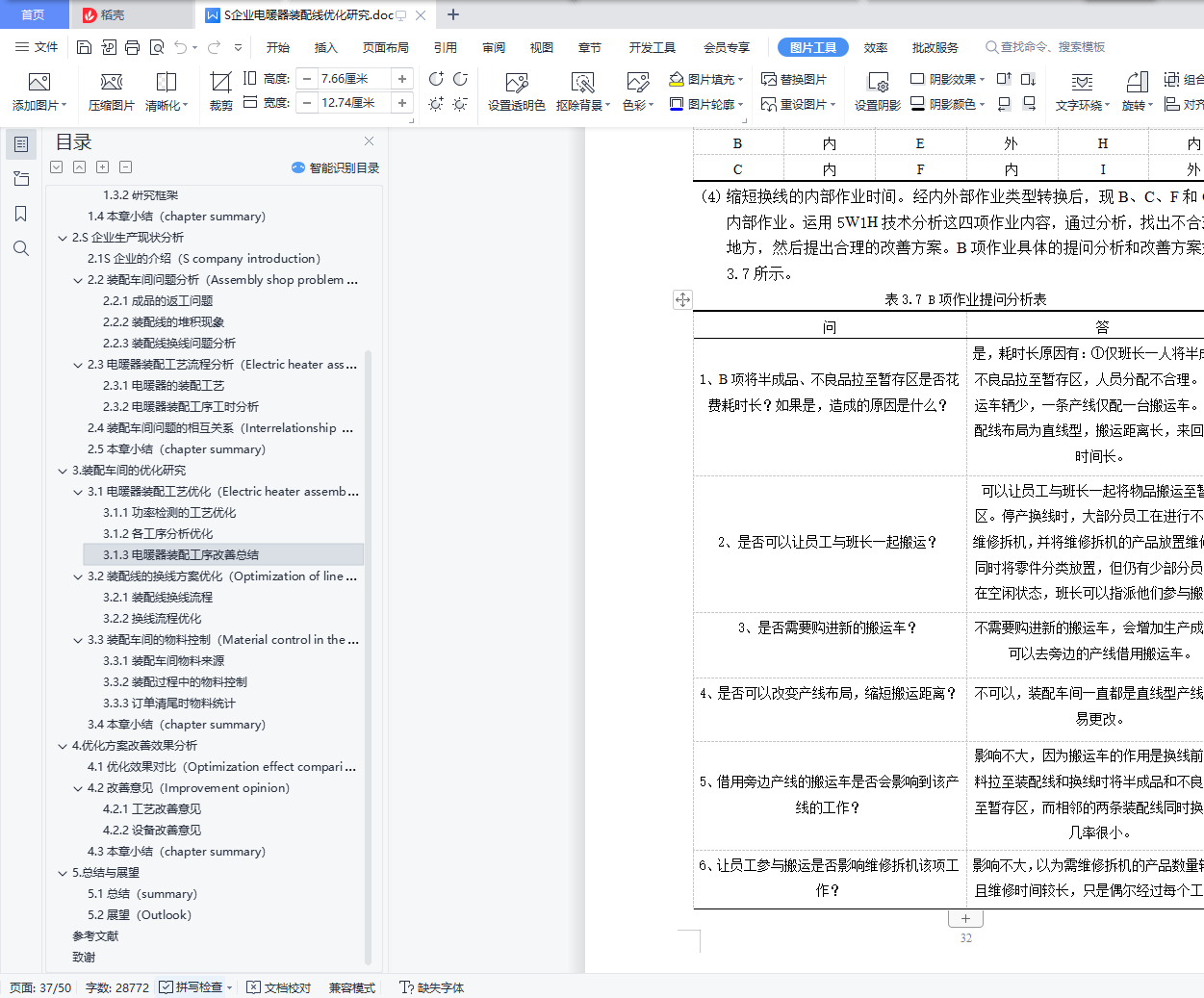
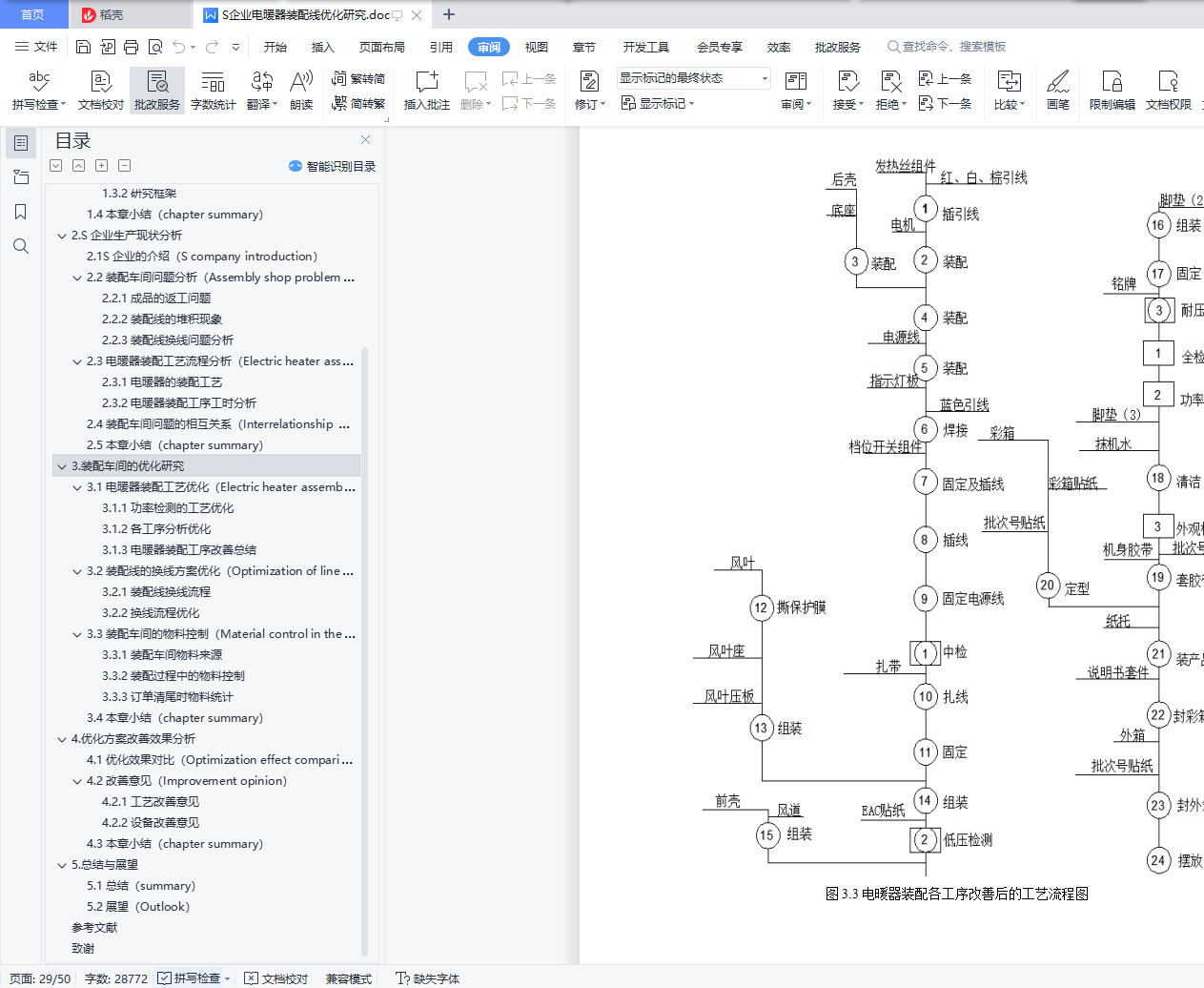
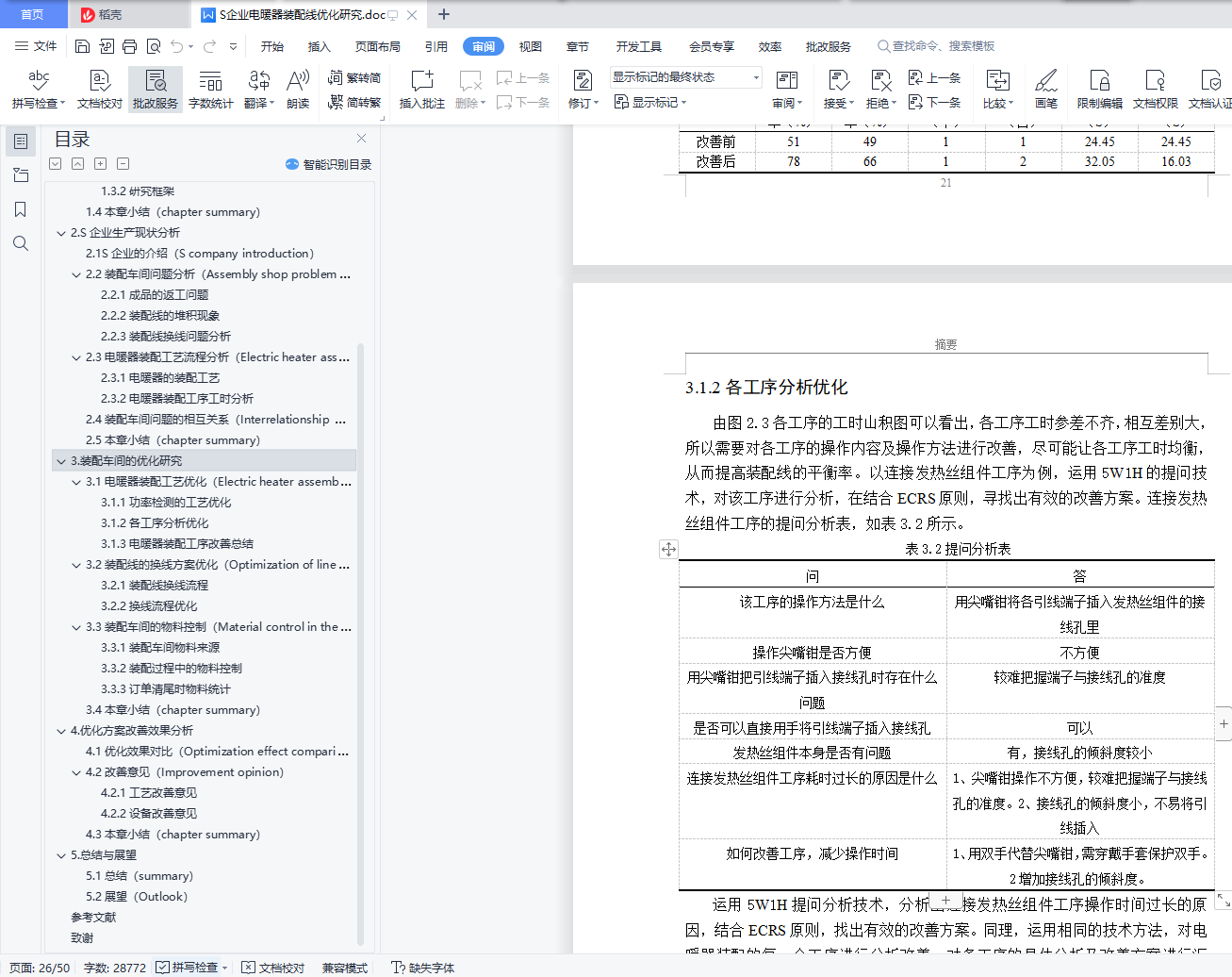
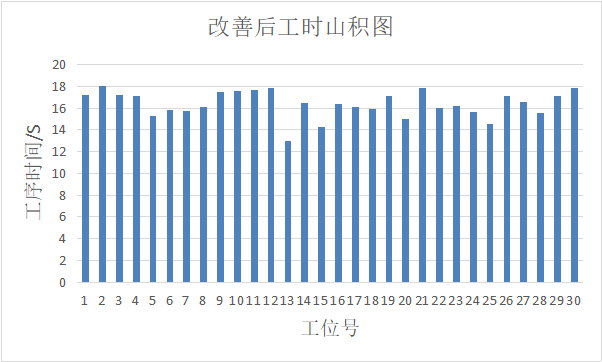