自动铆接机的机械结构设计
摘 要:当前,越来越多的企业关注工厂自动化改造提升。通过研究了解到,非标准装配自动化今后将满足更多产品种生产和自动化装配要求,尤其是能够满足个性化装配需求。机械工程各环节中,机械设计是机械生产的第一步,要在各种限定的条件下进行设计优化,综合考虑各项要求,包括最佳的工作性能、最少的制造成本、最低的能源消耗等等。本文以自动铆接机为例,进行机械结构设计。研究自动铆接机动力部分,采用气液增压缸来形成铆接压力。铆接模具的设计主要通过参数化、材料选用和铆压间隙来确定铆压部分的设计。送料部分采用振动盘结合分度盘进行。机械结构的建模和装配采用solidworks软件完成。所研究的设备可以确保紧固性要求、确保非装配位置的尺寸、确保装配件的稳定一致、提高生产效率、降低生产成本。
关键词:机械设计,建模,仿真,铆压,装配与调试,自动化
随着劳动力成本的不断提高,越来越多的企业关注工厂自动化这一领域,也给该行业带来了发展商机。机械自动化设备的开发包含为客户提供从方案、加工、组装到调试的一体化解决方案。即从产品的构思→方案→建模→出图→加工→组装→调试,提供给客户一整套的解决方案。
某企业专业生产和组装五金制品的企业,在生产过程中,一些零件的需求量非常大,以十万件计,零件紧固和密封要求度高,可置换性要求高。该企业生产产品“精密接头”零件图及装配体如图1-1所示,要求装配体中的上盖与底座进行铆接。
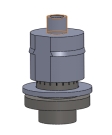
(a) 底座 (b) 垫片 (c) 上盖 (d) 装配体
图1 “精密接头”零件图及装配体
该零件是自动化生产线中的重要零件,装配工艺要求较高,其高要求主要体现在三个方面,一是紧固性要求高,二是零件变形控制要求高,三是可置换性要求高,否则无法通过检验。相对而言,手工操作的成本高、产品一致性和稳定性差、生产效率低;利用工业机器人进行装配,其自带的视觉传感系统可对零件进行识别,然后通过机械手进行装配,省去了一些周边设备,但成本高;本次计划设计制作出一台非标准自动化设备来完成装配和铆接动作,确保紧固性要求、确保非装配位置的尺寸、确保装配件的稳定一致、提高生产效率、降低生产成本,机械设计逻辑思路如图2,建模和仿真采用solidworks软件完成,通过装配检验设计的合理性。
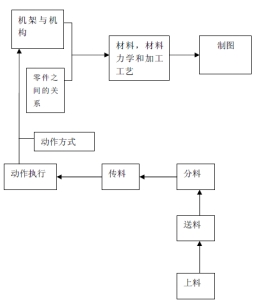
图2 机械设计逻辑思路
一、零件分析
本次装配的零件属于微小零件,底座和上盖零件大小不足10mm,两者之间采用过盈装配。零件材质为Q235,碳含量(WC%)在0.12%至0.22%之间,属于低碳钢,硬度为36~40HRC。装配截面如图3所示,干涉厚度约0.06mm,装配长度2.4 mm,考虑到装配动作不多,涉及零件只有3个,同时考虑合理利用空间及方便布局,本次选择回转式装配机。
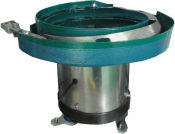
图3装配截面图 图4振动盘实物图
二、自动送料机构的选择
振动盘(Vibrator Bowl),是一种自动组装或自动加工机械的辅助送料设备,简称自动定向排序送料装置,能够对乱序的零件进行自动筛选和排序,实物如图4所示,其型号根据零件的尺寸来选择不同大小的顶盘,顶盘尺寸从Φ80mm到Φ1000mm都有。本次设计的零件都是微小零件,底座和上盖零件大小不足10mm,同时参考市场上振动盘的性价比,选择顶盘尺寸为Φ140mm的振动盘输送垫片,选择顶盘尺寸为Φ175mm的振动盘输送底座和上盖。
设计振动盘出料口与进料轨道位置如图5所示,振动盘出料口与进料轨道对齐,并通过高度调节螺栓调整振动送料器与进料轨道的高度(通常振动器的出口高度要比轨道的进料口高度高出0.3mm)。
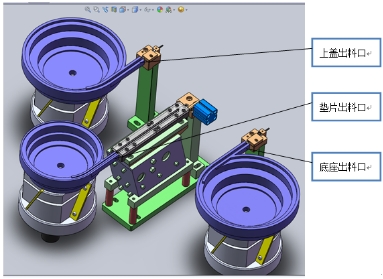
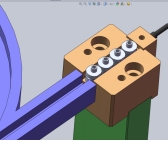
图5设计振动盘出料口及进料轨道
垫片是“精密接头”的装配零件之一,厚度只有0.6mm,外径只有8.5毫米,输送轨道设计如图6所示。直线轨道长度170mm,实践发现,仅仅依靠振动盘的力度,垫片会出现卡死现象,无法继续前进,增加直振器(如图7所示)解决垫片前进动力不足的问题。
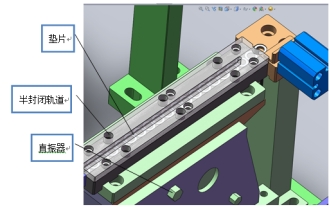
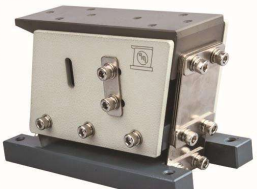
图6垫片(直振/钢带)进料轨道 图7直振器实物图
三、“精密接头”装配分度盘及回转机构的设计
考虑到“精密接头”的装配有三个进料位,加上铆接装配工位和卸料位,分度盘至少5个工位,考虑到制造及操作等更加方便,再扩展一个工位,因此设计分度盘为6个工位,且旋转方向为顺时针方向。
分度盘的间歇回转,需要选择合适的控制机构。步进电机回转机构、气动分度盘机构、棘轮棘爪机构、凸轮分割器是四种常见的回转间歇机构,经表1对比以及市场最新应用情况,采用凸轮分割器及传感器配合普通电机可实现间歇控制功能,如图8所示。
表1 常用回转间歇操作机构主要技术经济指标对比
序号
|
指标对比
|
步进电机回转机构
|
气动分度盘
|
棘轮棘爪机构
|
凸轮分割器
|
1
|
驱动力矩
|
小
|
大
|
大
|
大
|
2
|
定位精度
|
一般
|
高
|
低
|
一般
|
3
|
自动化水平
|
高
|
高
|
低
|
低
|
4
|
工作可靠性
|
一般
|
可靠
|
可靠
|
可靠
|
5
|
结构
|
复杂
|
简单
|
简单
|
简单
|
6
|
频率是否可调
|
能
|
能
|
否
|
否
|
7
|
噪音
|
小
|
一般
|
大
|
小
|
8
|
运行成本
|
高
|
一般
|
低
|
低
|
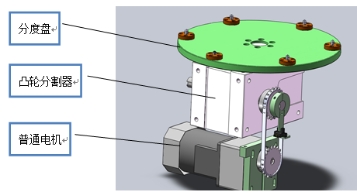
图8设计分度盘
四、气缸、气液增压缸的选择及铆合部分的设计
综合考虑,三个进料位和一个卸料位采用适当的气缸进行零件装卸,4个工位共用到8个气缸。前后运动采用标准型气缸,上下运动为了避免干涉采用薄型气缸,如图9所示。
为保证铆压效果,将装配工位设计为直压型气液增压缸,以纯气压源为动力,利用增压器的大小活塞面积比,将低压气压提高数十倍变为高压油压,达到高压输出的目的。一般来说,气液增压缸的行程较小,行程控制时要充分考虑和利用,避免出现限位无效的情况。形状控制方面确保铆合的质量而且不对装配件造成干涉与损害,按照经验,单边留出0.05mm作为零件放置的间隙,具体设计如图10所示。
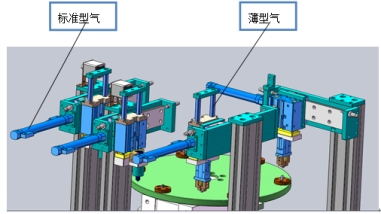
图9气缸的选择

图10 铆合部分的机械设计
五、自动铆接机机械构造的建模与装配
为了确保整个机械构造结构紧凑,逻辑关系便于梳理,维修操作方便,整体设计如图11所示。整个结构采用solidworks软件设计、装配和修改,以旋转工作台为中心,三条进料轨道平行放置,压铆工位设置在三条进料轨道对面,旋转工作台呈顺时针旋转,卸料工位位于压铆工位下一个位置。零件装配时,准确装配的关键是控制好自由度,包括线性尺寸、平行度、垂直度、同轴度及角度等等。当出现干涉时,首先考虑装配是否正确,排除装配问题后,就要对零件特征进行修改,直到合适为止。
以上对自动铆接机各个系统进行了总体布置及机械结构设计,包括底座送料机构、垫片送料机构、上盖送料机构、分度盘机构、压铆机构、卸料机构、箱体等,能够满足生产需要,结构简单紧凑、性能可靠、组装灵活、操作方便。
后续还要进行电气控制设计方面,PLC硬件控制电路设计和PLC控制程序设计,以及零配件的采购、装配与调试,不在此赘述,完成设备试制如图12所示。
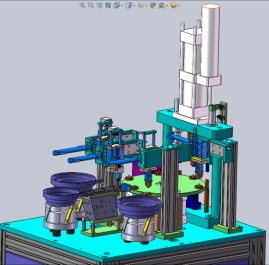
图11 整体设计
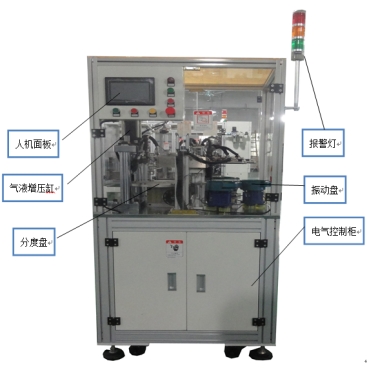
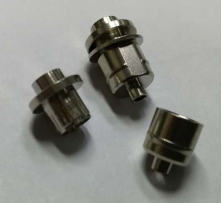
图12全自动“精密接头”装配一体机设备及装配成品
总之,本设备提高了“精密接头”的装配效率,把应用于机械装配控制系统相关的自动化技术融为一体,达到快速连续自动装配,避免了人工操作导致的部分铆压不到位,紧固性不好、装配零件变形、装配件稳定性不好等情况,减少了人工成本。装配自动化今后将在向模块化、柔性化、自动化等方面发展以满足多产品种生产和自动化装配要求。
参考文献
[1] 王志强.非标机械设计在工厂中的应用[J],中国机械,2014.
[2] 李文广.浅谈非标设备的设计与制造[J].化学工程与装备,2010 (10) :106-107
[3] 李洋.浅谈非标设计的标准化[J].中国机械, 2013 (7) :191-191
[4] 许菁.运用CAD技术进行非标设备模块化设计[J].网友世界·云教育 , 2013 (Z3) :46-47
[5] 曹仁涛.现代机械设计方法浅析[J].甘肃科技,2012 (23) :77-78
[6] 吴修文,郭红玉,何伟宁.生产装配线中气动分度盘的设计[J].农业装备与车辆工程,2009 (1) :42-44
[7] 张萍.《机械设计基础》[M],北京:高等教育出版社,2004:1-5
[8] 苏义.基于现代化的机械装配自动化应用及发展研究[J].电子测试,2015(10):36-37.
[9] 郑相周,唐国元.机械系统虚拟样机技术[M],北京:国防工业出版社,2007
[10] 秦勇坚.现代化机械装配自动化的应用与发展[J].科技信息,2013(05):137.