TECHNICAL NOTE
SOME FACTORS WHICH AFFECT THE GENERATION OF FLAKY PARTICLES BY A CONE CRUSHER
A.C.APLING and N.B.BARRETTT
§Department of Mining and Mineral Engineering,University of Leeds,Leeds LS2 9JT,UK
Lindley Plant,Heage,Derbyshire,UK
(Received 6 October 1995,"accepted 15 March 1996)
ABSTRACT
The products from a series of pilot scale tests have been analysed for size and flakiness to evaluate some of the factors affecting the generation of flaky material in a cone crusher.Two different feed sources characterised in terms of resistance to crushing and tensile failure were used to evaluate the influence of crusher set.feed rate and of material type on the resultant product character.
Keywords
Industrial minerals;crushing;particle morphology;comminution
INTRODUCTION
Aggregate producers must meet both size and shape specifications.The BS
Flakiness Index
F.I.= Mass flaky material in range×100 / Total mass material in range (1)
avoids a rigorous definition of particle shape by simply assigning particles according to their ability to pass a special slotted gauge.
The shape of crushed product depends on the material characteristics and the comminution method.Early work concluded that impact machines give the least and cone crushers the most flaky product and low reduction ratios favour the production of non—flaky product【2】.Cone crushers have much lower running costs particularly for harder abrasive materials and are in widespread use in the aggregate industry.
THE PROGRAMME OF WORK
Work has been undertaken with the Objective of evaluating the effects of feed rate and crusher setting on the generation of flaky material by a cone crusher from two different natural materials.Two feed rates and five crusher sets covering the range of the machine were used.The lower feed rate ensured free crushing,with particles crushed independently and loaded directly by the crusher faces.A higher level allowed material build up in the crusher feed cavity giving choked conditions where loading is achieved through a particle bed.
THE MATERIALS
The two feed materials were of similar size.The first contained two major rock types;carboniferous limestone 77%,and millstone grit(gritstone),23%(Redland Aggregates,Masham,North Yorkshire),the second also contained two major rocks;a metamorphic type known locally as ‘granite’,88%and ‘shale’,12%(Tarmac,Cliff Hill Quarry,Leicestershire).
Particle characterisation
Flakiness Index【1】determination was undertaken for all materials larger than 4.0 mm.For smaller sizes,a microscope was used to distinguish flaky particles and the index determined from the weights of the two categories.A conversion factor was established between the methods.Size analysis of all materials was determined by standard sieve analysis.
Crushability
The simpler Rock Impact Hardness Number (RIHN)【3】was used rather than the recommended aggregate strength tests【4】which require extensive laboratory apparatus.Its linear relationship with tensile strength 【5】,suggests a good correlation with generation of particles by cleavage,an important mechanism in the generation of flaky particles 【6】.The Crushability Work Index(CWI)【7】was determined for comparison.Both Cliff Hill species were substantially harder than those from Masham.
THE PILOT SCALE TESTS
Tests were conducted using a Standard Symons 2-foot Cone Crusher fitted with a fine bowl having a feed opening of 57.2 thin.and recommended minimum discharge setting of 6.4 mm,【8】.Products and feed for each of twenty tests were analysed for size and shape.
DISCUSSION OF RESULTS
Full analytical results,presented elsewhere【9】,allow the characterisation of the products in terms of
1) the mass fraction in each size fraction
2) the flakiness index of each fraction
3) the flakiness index of the total product
4) the distribution of flaky and non—flaky material by size
and permitted the identification of conditions favourable for the generation of non—flaky material.
Factors affecting size distribution of product
The Masham product was generally finer than that from the harder Cliff Hill material due,in part,to its crushing behaviour.Only the Masham material showed any difference between feed rates,generating more fines during choke feeding.The granular structure of this material would tend to encourage this.A tendency for the crushing faces to be forced apart by the harder Cliff Hill feed under crowded conditions would reduce its production of fines.
Factors affecting Flakiness Index of different sizes
The pattern illustrated in Figure 1 was observed in all cases.Product flakiness of 100% at the largest size,falls as size decreases,passing through a minimum,before then increasing.All larger particles tend to be flaky but at decreasing set particles of similar size have to be increasingly flaky (thin) to enable passage through the crusher cavity.
For the Masham feed the flakiness of coarser sizes is slightly lower for choke feeding,more especially at finer sets.suggesting that under these conditions flaky material is more likely to be broken as a consequence of the restricted opportunities for favourable orientation within the crushing chamber.
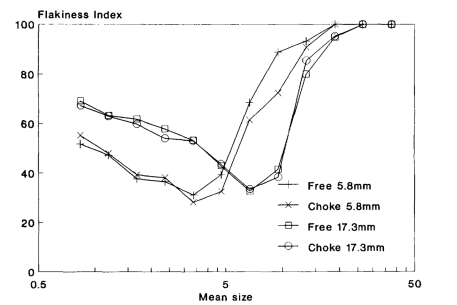
Fig.1 Flakiness Index versus size--Masham Products for different feed rates and crusher sets
In all cases the size at which flakiness index is a minimum is broadly related crusher set,increasing as the crusher set increases.Overall product flakiness,calculated as the weighted mean of the index for individual size fractions is generally less under choke feeding,and reduces as set decreases.
Factors affecting sizes for peak production
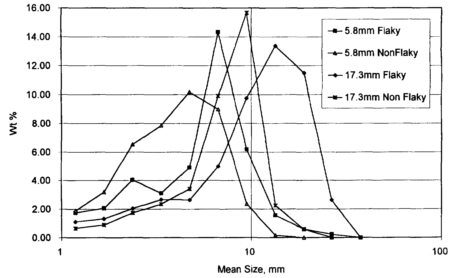
Fig.2 Product distribution by shape and size--Masham choke feeding ac stated stated sets
An alternative measure of product character given by the distribution of flaky (F) and non—flaky(N) material by size,illustrated in Figure 2,also reveals differences in behaviour.
Examination of the data revealed,despite the scatter of the results,that for both materials
(1)peak production(both shapes)is related to set and in all cases tends to increase and occur in larger sizes as set increases.
(2)peak flake production occurs in a size larger than that for non—flake
Peak flake and non-flake production is similar under different feed conditions with the Cliff Hill material but increases and occurs at higher sizes as set increases.whilst for the Masham feed maximum production occurs at increasing size but flake production decreases whilst non-flake increases.Choke feeding conditions,especially at finer sets,tends to result in more non—flake and 1ess flake production although the effect on the Cliff Hill material is noticeable only at the finest set.Large sizes consist almost entirely of flaky material which escapes breakage due to favourable orientation.
General Discussion
If the form of the product size distribution is similar then a smaller crusher set should reduce overall flakiness since any increase in flakiness of the coarser sizes will be counter balanced by an increased proportion of non—flaky finer sizes.For the Masham feed this tends to be the case.The results for Cliff Hill are 1ess clear.Earlier work [2]suggested that flakiness decreases at high feed rates and also at larger crusher sets.These results appear to contradict the latter finding.However overall flakiness masks the effects on individual size fractions,some of which may not be required as product.Larger sized ftaky particles generated by crushing at large sets could presumably be removed by screening leaving the finer non—flake as product.
The increased peak non—flake production for larger crusher sets with the weaker Masham material suggests that these conditions favour the generation of a product,following rejection of coarse sizes by screening,of low flakiness.
Contrary to earlier work [2] the minimum flakiness size is always less than the size at which total production is a maximum and does not correspond to the size of maximum non—flake production.Equivalence of these two sizes would clearly generate the maximum quantity of non.flaky product,normally the objective.The ratio of maximum production sizes to minimum flakiness size allows examination of the effect of crushing conditions on non.flake production,shown in Figure 3,revealing a broad trend for these sizes to approach each other as crusher set decreases.This suggests that the most favourable conditions occur for smaller sets,that iS high reduction ratios.Although peak non—flake production increases as set increases it is accompanied by greater flake product in the same size.
The dilemma then is whether the requirement is maximum production of non—flake and that generation of flaky material in the same size is not a problem.in which case a low reduction ratio seems to be required.or whether the minimum flakiness index iS required.that is the generation of flaky material iS to be minimised in a particular size.If this is the case then a much smaller set seems to produce the required result.The choice then is between maximum production of non—flake or minimum flakiness index.In reality a compromise between the two requirements will often generate the maximum product of the required specification and close control on the set of the crushing machines will be required to ensure optimum conditions are met at all times.
The large variation in the data leads to a degree of uncertainty in relation to its interpretation and reflects the difficulty of obtaining data in relation to large sized material,nevertheless it is believed that some important trends have been identified which are of relevance to the performance of cone crushers.The work here highlights the importance of gathering further information in order properly to quantify these effects.
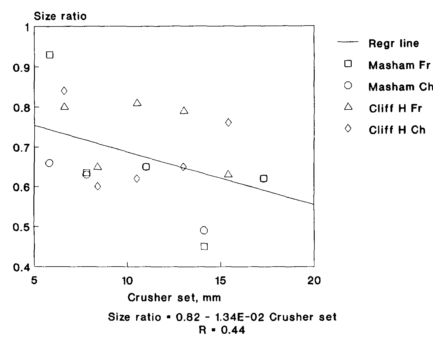
Fig.3 Size ratio versus crusher set
CONCLUSIONS
The broad conclusions reached from the current work can be summarised as follows;
1.Maximum flakiness occures at the maximum product size and reaches a minimum at a smaller size,related to crusher set,before increasing in the finer size ranges.
2.Flakiness of a specific size fraction increases as crusher set decreases in the coarser size range but decreases for the finer size ranges.
3.Choke feeding results in lower flakiness only for small crusher sets in the coarser sizes.This effect is reduced for the harder material.
4.The size where maximum material is generated increases as set increases.The minimum flakiness size is always less than the size for maximum production of non—flake which in turn is less than the size for maximum flake production.
5.As crusher set decreases there is a tendency for the size at which maximum production of non—flake occurs more closely to approach the size for minimum flakiness.
ACKNOWLEDGEMENTS
Thanks are due to Warren Spring Laboratories (DTI) for the support of this work.
REFERENCES
1.BS 812.Testing Aggregates.Pnn 1.Methods for determining particle size and shape.British
Standards Institute,London(1975).
2.Shergold,H.E.,A study ol the granulators used in the production of roadmaking aggregates.
Dept.Scientific and Industrial Research,Road Research Laboratory,Technical Paper 44,HMSO
(1959).
3.Brook。N.,Fines measurement of the impact testing of rocks,/nf.J.Rock Mech.Min.Scf.&
Geomech.Abstr.,23(4),333(1986).
4. BS 812.Testing Aggregates.Part 2 Methodsfor determining physical properties.British Standards Institute,London(1 975).
5. Townhill.Rewston,P.&Hamis,A.,The relationship between Rock Impact Hardness Number
fRIHN)and tensile strength.Leeds University Mining Association Journal,l 19(1988).
6. Kelly,E.G.&Spottiswood,DIJ.,The breakage function;what is it reaUy?Minerals Eng.,3(5),405(1990).
7. Bond,F.C.,Crushing and grinding calculations--part 1.Brit.Chem.Eng.,6(6),378(1990).
8. Nordberg Symons Cone Crusher Process Manual,Bulletin No 1 10,Nordberg Manufacturing
Company,Milwaukee.
9. Barrett,N.B.,The computer simulation of cone crusher circuits for the aggregate industry.PhD Thesis,University of Leeds,Sept.1992.