摘要:从磨损失效分析入手,对破碎粉磨系统中易损件的结构形状、相互匹配关系、耐磨材料生产工艺、质量控制与使用性能等进行评述,并列举了国内外典型耐磨材质的化学成分覆机械性能,同时阐述了破碎粉磨材料的发展。
1、引言
冶金矿山、建材、火电、化工、煤炭等工业部门,需要各种破碎粉磨设备。这些设备的易损件受研磨体、衬扳、物料的磨损,每年消耗大量金属。以水泥工业为饲,1994年水泥全国产量4.05亿吨。球磨机衬板类、破碎机类损耗金属约为300~ 350g/t水泥;研磨介质(球、段)为500g/t水泥,这样1994年仅水泥工业就消耗衬板类金属12万t,研磨体2o多万t。据有关资料统计,黑色、有色矿山消耗金属更多,全国消耗破碎机、球磨机衬扳金属约5o万t,研磨介质金属约130万t,总价值达80亿元。材料的消耗必然反映到能源消耗上,因此降低金属材料消耗也是节约能源的一个重要方面,具有明显的经济效益和社会效益。同时因更换易损件而被迫停车的时间在水泥行业约占总停车时间的50 ~55 ,占因磨损而增加设备维修工作量的6o ~65 ,因此随着破碎粉磨设备工艺技术的飞速发展,随着设备日趋大型化研制和使用,新型耐磨材料越来越为人们所重视。
2、破碎粉磨设备的磨损
破碎粉磨设备的磨损可分为内部因素和外部因素。内部因素包括材料的冶金质量、化学成分、金相组织和机械性能I外部因素包括物料的硬度和韧性,粒度和棱角锐度等等。易损件是否耐用取决于材料的抗冲击磨损能力,抗疲劳磨损能力,抗显微切削和犁削的能力。下面对几种破碎粉磨设备主要易损件的磨损进行简要分析。
2.1 颚式破碎机齿板
颚式破碎机齿板的磨损属于凿削式磨损。以江苏常熟采石场使用PZ250~500型颚式破碎机齿扳为例,齿扳材质是经水韧处理的标准高锰钢。在扫描电镜下观察齿扳磨面可以看出,齿扳表面被挤压成凹凸部分材料,随后又被磨料推挤形成压舌磨面,在磨面上可以看到很多磨料尖角短程滑动造成的磨痕,并可看到齿板表面有微裂纹,见图1。
经过分析,齿扳磨损的主要原因是磨料相对齿板短程滑动、切削金属造成磨屑和磨料反复挤压引起齿扳材料多次变形,导致金属材料疲劳脱落,磨损失教过程是:(1)物料多次反复挤压凿削齿扳,在齿扳区表层,或在挤压金属的突出部分根部形成微裂纹,此微裂纹不断扩展到相连,造成表面金属材料脱落,形成磨屑。(2)物科反复挤压,造成齿扳金属材料被局部压裂或翻起,其碎裂或翻起部分又随着挤压撞击的物料一起脱落形成磨屑 (3)物料相对齿板短程滑动,切削齿板形成磨屑。
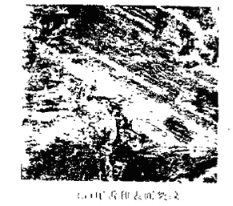
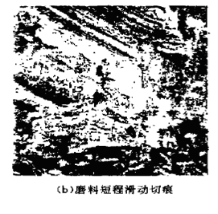
因此从耐磨材料上控制齿板磨损主要是硬度和韧性。材料硬,物料挤压深度浅,材料变形小,物料对材料短程滑动的切削量也小 材料韧性好,抵抗断裂能力强,可消除挤压撞击过程中脆性断裂,提高抗疲劳变形开裂能力。
颚式破碎机的大小规格不同,进料粒度、锐度不同,对齿板的挤压、撞击力不同,大中型挤压力大,除考虑材料的抗挤压力和抗滑动切削外,还应考虑受撞击时的冲击力及弯曲应力 因此大型齿板选材应选用韧性高、综合性能好的材质
从上述磨损失效分析可知,对于齿板材料应选择硬度高的材质以抵抗挤压、显微切削失效,选择足够韧性柏材质以抵抗凿削撞击疲劳失效。同时从齿板结构上进行改进,以减少物料与齿板的相对滑动,这不仅对提高生产率有益,而且对提高材料的使用寿命也有益。
2.2 锤式破碎机锤头
不同规格的锤式破碎机,锤头形状大小也各不相同,一般认为90~125kg的锤头为大型,25kg以下为小型,其余为中型。大中水泥厂一般使用25~50kg锤头。由于锤头大小不同,使用工况条件不同,它的磨损失效也各不相同。
锤头的磨损方式,以冲击凿削为主,伴随有冲刷显微切削磨损。其磨损形貌为冲击坑和切削犁沟。由于锤头的主要磨损方式为冲击,所以人们习惯于选择高锰钢做锤头材质。
(1)12kg以下锤头
由于其冲韧小,不能充分发挥高锰钢的加工硬化作用,因此耐磨性很不理想,如破碎长石、劣质煤和高炉矿渣等物料,锤头有的用几天甚至几个班即失效。有人把玻璃厂用5.8kg锤头和水泥厂用11.5kg锤头进行磨损后残体失效分析,结果表明两类锤头加工硬化效果都很差,表面硬化曲线如图2所示。
小锤头的磨损过程是一方面物料小能量冲击锤头,金属表面产生塑性变形和徽裂纹。在反复多次塑变情况下裂纹扩展,金属受挤压形成碎片脱落,导致冲击磨损;另一方面物料刺入材料表面,在一定法向力与切向力作用下,对材料表层金属产生显微切削、冲刷,使金属表面磨损,但由于冲击力 大,高锰钢不足以被加工硬化。所以应选择有一定韧性,以硬度高为主导的材料才能大幅度提高使用寿命。
(2)50kg级锤头
由于其冲击力大,采用高韧性的高锰钢材质,其加工硬化性能得到一定发挥,锤头以磨损、冲击、凿削为主,伴随冲刷显微切削磨损,磨损的微观形貌表现为冲击坑和切削犁沟。但是如果物料工况条件不同,同样是高锰钢锤头使用情况也相差很大。如同样是陕西延河水泥机械厂生产的12P 50kg级高锰钢锤头,在永登水泥厂仅应用2~3个月即失效;在耀县水泥厂可用8~11个月。
电镜观察永登水泥厂锤头在磨损面上主要是切削犁沟,有冲击坑存在,说明其磨损失效是以切削机理为主,向时伴随有撞击磨损。分析原因是该厂石灰石物料中含泥量大,粒度小,使冲击负荷减小,高锰钢加工硬度不明显,同时物料中常带有高硬度的硅石板岩,对高锰钢奥氏体像硬质合金刀一榉切 ,留下许多切削沟槽,所以磨损快。
耀县水泥厂锤头磨损面上主要是冲击坑,并有少量的切削沟槽,说明它是以撞击磨损为主,伴随切削磨损,这是因为耀县厂的石灰石块度大,且均匀、冲击力大。石灰石与锤头磨损面撞击时形成许多撞击坑,坑周围有明显的翻边。由于高锰钢有良好塑性,在磨料正向撞击下较易塑性变形而形成冲击坑;另一方面由于较大冲击力使高锰钢得以被加工硬化,增大了变形抗力,因而表现出较高的抗磨损能力。
从上述分析可以看出:在以切削为主的情况下,诗件的硬度对耐磨性起主导作用 为解决这一问题,我们与湖北水泥机械厂在研制一种超强高锰钢高韧性的前提下,丈幅度提高其屈服强度(达 450N/ram。),提高初始硬度到HB260~300,同时提高其加工硬化速率,使寿
命大幅度提高。
(3)大型破碎机90kg和125kg锤头
以90kg锤头为倒其工作参数如表1

由表1可知该破碎机进料粒度大,破碎比大,转速高,所以锤头受撞击力大,是以撞击为主的磨损机制。选材应以冲击韧性为主导兼顾硬度、强度等综合性能。冀东水泥厂t983年3月使用从德国O8Ⅸ 公司引进的MB70/90型锤式破碎机,90kg锤头原来是双金属铸造,头部用高铬铸铁,锤柄用低合金钢,使用中锤头削落,结合处断裂较多,影响正常生产,威胁整机的安全,1 986年7月进口O&K 公司单金属90kg锤头,平均使用10个月破碎180万t石灰石。唐山水泥机械厂在解剖分析簿国锤头基础上研制超高锰钢锤头,1 991年通过部级鉴定。含锰钢高达17 ~18 ,主要是使锤头厚大,中心部也为全奥氏体,保持其优良的韧性,使用可靠,增加Cr Mo等元素,提高屈服强度和初始硬度等综合性能满足生产需要。以上说明以冲击磨损为主的易损件必须选择高韧性材料并辅以其它综合性能。
2.3 球管磨机衬板的磨损
球(管)磨机的衬板承受磨球和物料的冲击、凿削、挤压和显微切削多方面作用,磨损特征是表面出现凹坑、裂纹和犁沟。磨损程度与物料特性、粒度、锐度和易磨性有关,也与磨机直径大小规格、衬板所处部位有关。
以Φ2.2m×6.5m水泥磨机为倒,一仓、二仓高锰钢衬板磨损表面电镜照片如图3和图4所示。
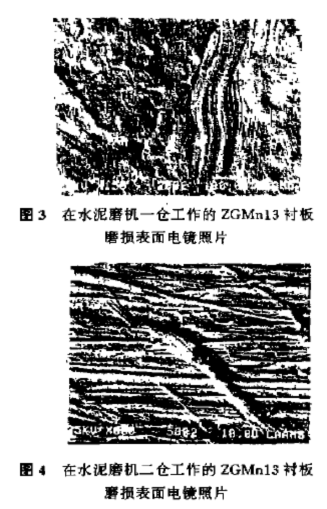
从图片中可见一仓衬板有许多犁沟和剥落坑,这是因为一仓平均球径为 70~80mm,最大球为 9O~100mm,物料平均粒度25ram,最大可达40mm,且棱角尖锐;二仓球径为 30~50mm或~35mm×30mm 以下钢段。物料从一仓被破碎后经厢仓板到二仓,粒度已变成5ram左右,棱角锐度已大大减小,所以二仓衬板主要是显微切削、挤压堆积和冲局4磨损。进料端磨头衬板由于受较大研磨体和物料粒度大、棱角尖锐的侧冲击、滑动切削,因此比出料端篦板磨损严重得多。隔仓板既受一、二仓球的侧冲击,又要使物料通过啼缝受冲刷显微切削,因此磨损也比较严重 若要求隔仓板既有抗冲击磨损能力不断裂,又要有较高的屈服强度和硬度,抗弯曲,抗物料冲刷,保持篦缝宽度,满足工艺要求,就应选择韧性好硬度高的材料。
即使是同一块磨机衬板,不丽部位磨损也不同,比如端衬板、中部衬板受物料和磨球的冲击严重,尤其是迎料面更甚,而靠近筒体尾部则轻些。筒体衬板不论是阶梯、凸棱、压条等衬板迎料球面受切削、冲击严重,因此在衬板生产工艺中应考虑不同部位的抗冲击磨损的耐磨性问题,或从结构设计中加以改进,如磨头端衬板迎料面加棱;一仓村板做成双阶梯;隔仓板磨损部位加厚等等。
综上所述衬板磨损是一个系统工程,要针对不同的工况条件研制相应的耐磨材料。
2.4 磨球的磨损失效
磨球在球摩机工作中消耗金属是最多的。我们对不同材质、使用在不同工况条件下的磨球进行分析,可知磨球的磨损失效有以下几种机理:
(1)凿削和切削磨损。磨球在磨内上升阶段与物料相对滑动,被物料中硬而尖锐的部分在表面切削出较深沟槽,被敬而钝的物料切出较浅的沟槽,物料大小不同,软硬尖锐不同,造成球表面沟槽探浅、宽窄不同,纵横交错。磨球弛落时以一定角度撞击物料,产生局部凿削磨损形成凿削坑。
(2)变形磨损。磨球与物料相对滑动或冲击时除直接切削、凿削外,还有犁沟变形发生,金属被推挤至沟槽和凹坑外侧,在物料反复作用下金属变形,由应变疲劳产生裂纹,裂纹扩展、连接,形成犁屑薄片,表面脱落。
(3)脆性剥落。磨球受冲击过程中,材料脆性相(如碳化物)开裂、破碎自表面卓i落造成磨屑。
(4)疲劳磨损。磨球在磨机内周而复始的上升、抛落、反复滑动、滚动和冲击等变化,在冲击接触压应力、切应力作用下产生疲劳,在亚表层形成相互平行的疲劳裂纹,并向表面延伸形成疲劳剥落层。疲劳裂纹可在亚表层下夹杂物和脆性相下生核,也可在表面硬化层和动态软化层问生核。当在远表层的铸造缺陷和夹杂上生核,扩展时将导致宏观疲劳剥落,产生大块碎片造成球开裂或失圆。近表层生核则导致微观疲劳剥落,形成显微薄层和剥落坑。