A Floor Cleaning Robot for Domestic Environments ∗
Arnab K. Bordoloi1 , Md. Faheemul Islam2 , Jiauz Zaman1 , Nabasmita Phukan3 and Nayan M Kakoty3 1 Department of Electrical Engineering
2 Department of Mechanical Engineering Jorhat Engineering College
Jorhat, INDIA
3 Embedded Systems and Robotics Lab School of Engineering
Tezpur University Tezpur, INDIA
nkakoty@tezu.ernet.in
ABSTRACT
Although a number of cleaning machines have made its way into the market, cleaning robot in the context of domestic floor environments with different types of dust and dynamic obstacles is still a challenge. This paper presents a mobile robot with sweeping, vacuum suction and wiping capacity for effective cleaning of a domestic floor. The robot can avoid collisions with dynamic obstacles through the fusion of in- formation from two sensors: a sharp infra red sensor and an ultrasonic sonar sensor. It can be used in both autonomous and manual mode of operations. In the autonomous mode, the robot moves in a zig-zag pattern following an edge de- tection algorithm. It can be controlled using an Android application in the manual mode of operation. In the exper- imental set-up, cleaning efficiencies of 85% and 92% have been obtained in the autonomous and manual modes re- spectively. It can clean the floor closer to the wall upto an average distance of ≈16 cm at a cleaning rate of ≈180 cm2
/sec.
Keywords
Cleaning robot, Domestic environment, Dynamic obstacles
∗
Permission to make digital or hard copies of all or part
of this work for personal or classroom use is granted with- out fee provided that copies are not made or distributed for profit or commercial advantage and that copies bear this no- tice and the full citation on the first page. Copyrights for components of this work owned by others than ACM must be honored. Abstracting with credit is permitted. To copy otherwise, or republish, to post on servers or to redistribute to lists, requires prior specific permission and/or a fee. Re- quest permissions from Permissions@acm.org.
AIR ’17, June 28-July 2, 2017, New Delhi, India Copyright 2017 Association for Computing Machinery. ACM ISBN 978-1-4503-5294-9/17/06...$15.00
https://doi.org/10.1145/3132446.3134883
1. INTRODUCTION
In spite of a number of automated cleaning systems avail- able in the market, cleaning robot for domestic floor envi- ronments with different types of dust and dynamic obstacles is still an open problem. This is because the available sys- tems are mainly designed for a hustle free smooth environ- ment such as polished floors and are equipped with vacuum suction only. The different climatic region across the globe introduces numerous types of dust particles (like cob webs, saw dusts, insect carcass etc.) which necessitates an efficient cleaning system with sweeping, vacuum suction and wiping capacity for domestic floor environment.
An endeavour has been made by many researchers in this area. Palacin et al. [9] have reported a cleaning robot hav- ing a sweeping section that consists of a roller brush, dust pan and a broom stick. It has ability to react to dynamic obstacles with the help of its eleven sensors. Gao et al. [4] reported a cleaning robot consisting of only a sweeping sec- tion with four brooms. It had the capability to be controlled in both autonomous and manual mode and can react to ob- stacles from a distance of 1.5 meters. The robot mentioned by Chaple et al. [2] consists of sweeping, vacuum cleaning and scrubbing mechanisms. It uses raster scanning for path planning algorithm. A topological based approach is used to control the path execution using eleven infra-red (IR) sen- sors to interact with the physical world. Kaur et al. [7] discussed about a robot having two cleaning section: swip- ing and moping. It works in both automatic and wireless (using radio-frequency (RF) module working at a frequency of 2.44 Hz and range of 50m) modes cleaning in a zig-zag pattern and detects obstacles at a distance of 1 ft. The robot discussed by Karthick et al. [6] has a vacuum cleaning sys- tem which works under the principle of centrifugal pump. It follows a random cleaning pattern with ultrasound sensors to detect obstacles. Thomas et al. [11] have designed a vac- uum cleaner robot that works in manual modes. Bluetooth module has been used to transmit and receive the signal to operate the robot through an Android application. The Bluetooth module has maximum 100m range and operat- ing frequency of 2.4 GHz. IR sensors are used for obstacle detection. Uman Khalid et al. [8] have developed a robot with electrical circuitry for controlling the motor in various sections i.e. sweeping and vacuum suction. Autonomous movement is controlled by IR sensor data using obstacle
avoidance technique and returns to the charging base af- ter cleaning. It also has a manual control mode remotely switched through a laptop with a graphical user interface. Paul et al. [10] reported a cleaning robot working in two modes as per the user’s convenience: automatic and man- ual; and ultrasonic sensors have been used to avoid hurdles. It performs vacuum suction, disinfection and mopping op- eration with minimal or zero human intervention and a ver- tical shaft is provided with cleaning brush for cleaning of walls. To make whole system wireless, CC2500 RF module has been used with communication range of 50m. Chavan et al. [3] have reported a cleaner robot that uses the posi- tion control of wheels. Seven ultrasonic sensors are used for obstacle detection.
Although a number of cleaning machines have been reported, very few of them are equipped with sweeping, vacuum suc- tion and wiping mechanisms [5]; which is essential for domes- tic floor cleaning in different climatic regions. Furthermore, the reported cleaning machines are not efficient in domes- tic floor environments with various types of dust and dy- namic obstacles. The work reported in this paper presents a cleaning robot using the Firebird V mobile robot research platform. The robot has three cleaning units: sweeping, vac- uum suction and wiping. It is provided with the flexibility to be controlled in two modes viz. autonomous mode and manual mode. The autonomous mode is programmed to follow a particular cleaning pattern using a hybrid combina- tion of ultrasonic and sharp infra red sensor. The robot has been wirelessly linked to an Android application. The robot can be controlled in manual mode using this application. The robot under consideration has been examined through various tests to determine the parameters viz. cleaning effi- ciency, cleaning rate, time required for cleaning in the pres- ence of dynamic obstacles and the distance closest to the wall that the robot can clean in the presence of heavy chalk dust.
2. ROBOT STRUCTURE
The structural units of the robot are built on a mobile robot platform: Fire Bird V. It consists of four structural units: sweeping unit, vacuum unit, wiping unit and the control unit. The sweeping unit consists of two brushes of flexible bristles. These brushes are attached to the shafts of two DC motors. The left motor rotates the left brush clockwise and the right motor rotates counter-clockwise pushing the dust particles towards the vacuum suction unit. The vac- uum suction unit is placed at the middle of the robot. It is comprised of a centrifugal fan driven by a DC motor. This is to create air pressure difference leading to vacuum suc- tion. A detachable dust cabin with an air filter collect and store the dust. A tube, having the opening on the floor to be cleaned, channel the dust to the cabin. The wiping unit is placed at the rear end of the robot and designed to wipe the floor along the path of the robot motion. It is comprised of detachable sponge strips and a pipe with uniform pores to spray the water from a water tank to the sponges.
The controller ATmega 2560 in the Fire Bird V is used to control the sweeping, vacuum suction and the wiping units. The combination of a sharp IR sensor and an ultrasonic sensor on the robot is used for obstacles avoidance and edge detection. A wireless module (Bluetooth HC-05) is used to
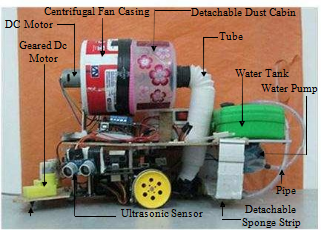
Figure 1: Floor cleaning robot indicating the com- ponents of the structural units
support the control from a mobile application. A pack of 9.6 V NiMH battery is used for electrical power supply. Figure 1 shows the robot indicating the components of the structural units. The specification of the robot are tabulated in Ta- ble 1.
Table 1: Speciftcation of the cleaning robot [1]
3. MOTION CONTROL OF THE ROBOT
The motion of the robot is controlled in two modes of op- eration: manual and autonomous. The mode of operation can be selected through an Android application. The robot is connected to the application through bluetooth at a fre- quency of 2 to 2.4 GHz and has a range of 10 meters.
3.1 Manual Mode of Operation
The home screen of the application is shown in Figure 2. The robot motion in forward, backward, left (axial left and left), right (axial right and right) and stop can be controlled through seven touch buttons on the mobile application. The
sweeping, vacuum and wiping units start functioning on the activation of any of the touch buttons. The robot operation can be transferred to the autonomous mode through the application. The manual mode of operation allows the user to use the robot to clean the region of interest on the floor.
Figure 2: Android application to Control the robot
3.2 Autonomous Mode of Operation
In this mode of operation, the robot starts from any ran- domly placed position on the floor and moves forward after finding a continuous edge (i. e. the wall) of the room and traverse along it keeping a distance of 16 cm using the ul- trasonic and sharp IR sensors. On traversing two successive ends of the edge of the wall, the robot confirms itself to be located in one of the corners in the room. Following this, the robot moves in a zig-zag pattern to traverse the maximum area on the floor. On detection of any dynamic obstacles by the robot using the sharp IR sensor, it produces a buzzer sig- nal as alarm and regains its original path once the obstacle moves away.
3.3 Cleaning Principle
In the autonomous mode, the robot first finds one of the wall edges of room and starts an edge following algorithm. Once the robot reached two consecutive corners following the edges of the wall, it starts a zig-zag pattern motion to traverse the complete floor area. During the process, the brushes in the sweeping unit collects the dust from the sur- rounding along the motion of the robot and pushes towards the vacuum unit. The vacuum unit draws in the dust and deposit to the dust cabin. Following this, the dustless area of the floor is wiped down by the sponge in the wiping unit of the robot. Figure 3 shows the flow of dust from the floor to the dust cabin and flow of water in the wiping unit for cleaning the floor.
In the manual mode, the cleaning units of the robot work as in the autonomous mode following the path of motion as controlled by the user through the mobile application.
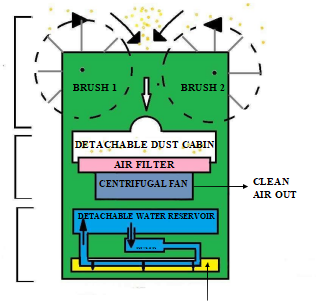
DETACHABLE SPONGE
Figure 3: Cleaning principle of the robot
4. EXPERIMENTAL SET-UP
A 140×150 cm2 floor area is considered for the experiment. Figure 4 shows the experimental floor along with the ideal lines for the robot to follow in autonomous mode of opera- tion. The floor is filled with chalk dust and sponge pieces (≈1 cm3) distributed unevenly for the experiment and is shown in Figure 5. The distance closest to the wall that can be cleaned by the robot, number of sponge pieces collected by the robot vis-a-vis the total number of sponge pieces on the floor (i.e. the efficiency), cleaning rate and the time to complete the cleaning process with different numbers of dynamic obstacles have been considered during the experi- ment.
Figure 4: Experimental Floor (140×150 square cm) with the ideal path to be traversed by the robot
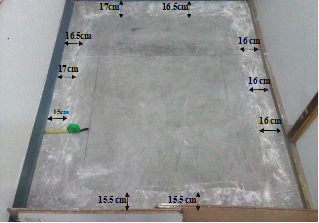
Figure 5: Experimental floor with unevenly dis-
tributed chalk dust and sponge pieces
5. EXPERIMENTAL RESULTS
Figure 6 shows the path of the robot in autonomous mode of operation. It can be observed that the robot follows the edge of the wall in the experimental set-up from a random position on the floor and on reaching the second corner, it starts moving in a zig-zag path. It is in line with the mo- tion planning algorithm although there are small deviations in following the ideal zig-zag pattern. Figure 7 shows the floor after the robot had traversed on it implementing the sweeping, vacuum suction and wiping operations.
Figure 6: Path traversed by the robot in the au- tonomous mode of operation
A total of 650 sponge pieces were unevenly distributed on the floor. The number of sponge pieces collected in the dust cabin in one trial was used to calculate the cleaning efficiency (η) of the robot using the following formula:
Number of sponge pieces collected
Figure 7: The experimental set-up after the robot cleans the floor showing the distance closest to the wall that can be cleaned by the robot in autonomous mode
tonomous and manual mode of operation calculated over 10 trials. Because of the freedom to run the robot successively in the same area under the manual mode of operation, the cleaning efficiency is higher compared to the autonomous mode of operation.
Table 2: Efficiency of the robot in the autonomous and manual mode of operation

The distance to which the robot can approach closest to the wall is one of the parameters to determine its capacity. Fig- ure 7 shows the minimum distance between the wall and the cleaning line of the robot at ten points under autonomous mode of operation. It has been found that the robot can clean the floor closer to the wall upto an average distance of
≈16 cm. Figure 8 shows the variation in the cleaning time required by the robot in the presence of dynamic obstacles. This is reported from 10 trials of cleaning by the robot with a number of dynamic obstacles varying from one to 10.
Areas of different sizes in the experimental set-up were con- sidered to be cleaned by the robot for evaluating its clean- ing rate. Table 3 shows the cleaning rate of the robot over the different areas. The experimental results show that the robot has a cleaning rate of ≈ 180 cm2/sec.
6. CONCLUSIONS
In this paper, we presented a floor cleaning robot for do- mestic environments through sweeping, vacuum suction and wiping mechanism. The robot could clean the floor in the
η = Total number of sponge pieces on the floor
× 100%
experimental set-up with cleaning efficiencies of 85% and 92% in the autonomous and manual mode of operation re- spectively. The robot can clean the floor closest to the wall
Table 2 shows the average efficiency of the robot in the au-
upto an average distance of ≈16 cm. It can clean the floor at
150
100
0 1 2 3 4 5 6 7 8 9 10 11 12
Number of Dynamic Obstacles
Figure 8: Time required for cleaning vis-a-vis the number of dynamic obstacles on the floor
Table 3: Cleaning rate of the robot
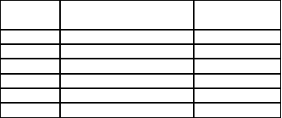
a rate of ≈180 cm2/sec avoiding the collisions with dynamic obstacles.
The presented robot is promising compared to the ones re- ported in the literature in terms of the three cleaning mech- anisms: sweeping, vacuum suction and wiping and its capac- ity to clean the domestic floors with heavy layers of chalk dust at a comparable cleaning rate. The future research focuses in the direction to improve the results, design of the robot and experiments in common house-hold environ- ments, which holds promise in improving the life style of the mankind. The robot has been developed using indigenous technology and if it succeeds in the consumer testing, it will lead to an enterprising device.
Acknowledgement
The financial assistance by the Ministry of HRD, Govt. of India’s Centre of Excellence Project in Machine Learning and Big Data is gratefully acknowledged.
7. REFERENCES
[1] e-yantra. http://www.e-yantra.org/. Accessed: 2017-05-29.
[2] Chaple, A., Bhaskarwar, S., Bhaskarwar, A., and Chidarwar, S. Autonomous cleaning robot. In International Journal of Computer Applications (India, 2012), pp. 1–4.
[3] Chavan, S. P., Dhanvijay, M. R., and Jaybhaye,
M. D. A low cost aurdino controlled floor mopping robot. International Journal of Engineering Research 5, 2 (2016), 319–321.
[4] Gao, X., Li, K., Men, Y. W. Y., and KiKuchi,
D. K. A floor cleaning robot using swedish wheels. In
IEEE International Conference on Robotics and Biometric (Sanya, China, 2007), pp. 2069–2073.
[5] Hess, J., Beinhofer, M., Kuhner, D., Ruchti, P., and Burgard, W. Poisson driven dirt maps for efficient robot cleaning. In IEEE Intl. Conf. on Robotics and Automation (Germany, 2013), pp. 1–6.
[6] Karthick, T., Ravikumar, A., Selvakumar, L., Viknesh, T., and Parthiban, B. Simple autonomous cleaner robot. International Journal of Science, Engineering and Technology Research 4, 5 (2015), 1231–1236.
[7] Kaur, M., and Abrol, P. Design and development of cleaner robot automatic and manual. International Journal of Computer Application 97, 19 (2014), 32–38.
[8] Khalid, U., Baloch, M. F., Haider, H., Sardar,
M. U., Khan, M. F., Zia1, A. B., and Qasuria, T.
A. K. Smart floor cleaning robot (clear). In IEEE Standard University Student Application Papers (2016), pp. 1–7.
[9] Palacin, J., Salse, J. A., and Clua, I. V. X. Buliding a mobile robot for a floor cleaning operation in domestic environment. IEEE transaction on Instrumentation and Measurement 53, 4 (2004), 1418–1424.
[10] Paul, T. R., Kumar, L. A., Mahamunkar, M., Jose, R. M., and Khan, S. Automated operating room cleaning robot. International Journal of Advanced Research in Electrical, Electronics and Instrumentation Engineering 5, 4 (2016), 3058–3061.
[11] Thomas, V. J., Xaviour, B., and K.George, J. Cleaner robot. International Journal of Emerging Technology and Advanced Engineering 5, 12 (2015), 285–288.