毕业设计(论 文)开 题 报 告
1.结合毕业设计(论文)课题情况,根据所查阅的文献资料,每人撰写
2000 字左右的文献综述:
文 献 综 述
1.研究背景及意义
普通钻床改为多轴钻床的设计以简明的语言介绍了自动钻铣床的总体方案和工作台的设计过程,通过慧鱼教具的思路来进行多轴钻床的设计,钻床为孔加工机床,按其结构形式不同可以分为摇臂钻床、立式钻床、卧式钻床、深孔钻床等。主要用来进行钻孔、扩孔、 工科论文绞孔、攻丝等。本设计的重点是自动立式钻铣床的设计,包括了机械结构设计、机械传动系统的设计,并对工作台的元件进行了选择和设计:包括丝杠、同步齿形带、步进电动机和导轨的选型;最后部分则是电路设计方面的主要内容,以PLC为主体的控制单元可以快捷方便的完成进给任务,对PLC的工作原理和本设计所需要的程序进行了设计。
随着科学技术的不断发展,机械产品日趋精密、复杂,改型也日益频繁,对机床的性能、精度、自动化程度等提出了越来越高的要求。机械加工工艺过程自动化是实现上述要求的重要技术措施之一,不仅能提高产品质量和生产率,降低生产成本,还能改善工人的劳动条件。为此,许多企业采用自动机床、组合机床和专用机床组成自动或半自动生产线。但是,采用这种自动、高效的设备,需要很大的初期投资以及较长的生产准备周期,只有在大批量的生产条件(如汽车、拖拉机、家用电器等工业主要零件的生产)下电气电子、才会有显著的经济效益。
在机械制造工业中,单件、小批量生产的零件约占机械、加工的70%~80%。科学技术的进步和机械产品市场竞争的日益激烈,致使机械产品不改型、更新换代、批量相对减少,质量要求越来越高。采用专用的自动化机床加工这类零件就显得很不合理,而且调整或改装专用的“刚性”自动化生产线投资大、周期长,有时从技术上甚至是不可能实现的。采用各类仿型机床,虽然可以部分地解决小批量复杂的加工,但在更新零件时需制造靠模和调整机床,生产准备周期长,土建水利而且由于靠模误差的影响,加工零件的精度很难达到较高的要求。
据统计,一般在车间中普通机床的平均切削时间很少超过全部工作时间的15%。其余时间是看图、装卸工件、调换刀具、操作机床、测量 以及清除铁屑等等。使用数控机床虽然能提高85%,但购置费用大。某些情况下,即使生产率高,但加工相同的零件,其成本不一定比普通机床低。故必须更多地缩短加工时间。不同的加工方法有不同的特点,就钻削加工而言,多轴加工是一种通过少量投资来提高生产率的有效措施。
虽然不可调式多轴头在自动线中早有应用,但只局限于大批量生产。即使采用可调式多轴头扩大了使用范围,仍然远不能满足批量小、孔型复杂的要求。尤其随着工业的发展,大型复杂的多轴加工更是引人注目。例如原子能发电站中大型冷凝器水冷壁管板有15000个ψ20孔,若以摇臂钻床加工,单单钻孔与锪沉头孔就要842.5小时,另外还要划线工时151.1小时。但若以数控八轴落地钻床加工,钻锪孔只要171.6小时,划线也简单,只要1.9小时。因此,利用数控控制的二个坐标轴,使刀具正确地对准加工位置,结合多轴加工不但可以扩大加工范围,而且在提高精度的基础上还能大大地提高工效,迅速地制造出原来不易加工的零件。有人分析大型高速柴油机30种箱形与杆形零件的2000多个钻孔操作中,有40%可以在自动更换主轴箱机床中用二轴、三轴或四轴多轴头加工,平均可减少20%的加工时间。1975年法国巴黎机床展览会也反映了多轴加工的使用愈来愈多这一趋势。
2.1 国内外研究的现状
2.1 国内研究现状
20世纪70年代初,钻床在世界上还是采用普通继电器控制的。如70年代-80年代进入中国的美国的ELDORADO公司的MEGA50,德国TBT公司的T30-3-250,日本神崎高级精工制作所的DEG型等钻床都是采用继电器控制的。80年代后期由于数控技术的出现才逐渐开始在深孔钻床上得到应用,特别是90年以后这种先进技术才得到推广。如TBT公司90年代初上市的ML系列深孔钻床除进给系统由机械无级变速器改为采用交流伺服电机驱动滚珠丝杠副,进给用滑台导轨采用滚动直线导轨以外,钻杆箱传动为了保证高速旋转、精度平稳,由交换皮带轮及皮带,和双速电机驱动的有级传动变为无级调速的变频电机到电主轴驱动,为钻削小孔深孔钻床和提高深孔钻床的水平质量创造了有利条件。为了加工某些零件上的相互交叉或任意角度、或与加工零件中心线成一定角度的斜孔,垂直孔或平行孔等需要,各个国家而专门开发研制多种专用深孔钻床。
例如专门为了加工曲轴上的油孔,连杆上的斜油孔,平行孔和饲料机械上料模的多个径向出料孔等。特别适用于大中型卡车曲轴油孔的BW250-KW深孔钻床,它们均具有X、Y、Z、W四轴数控。为了客户需要,在一条生产线上可以加工多种不同品种的曲轴油孔,于2000年设计制造了第一台柔性曲轴加工中心,可以加工2~12缸不同曲轴上所有的油孔。MOLLART公司生产制造的专为加工颗粒挤出模具而开发的具有六等分六根主轴同时加工同一工件上六个孔的专用深孔钻床。该工件孔数量多达36000个。全都是数控系统控制的。图2-1为普通钻床的示意图。
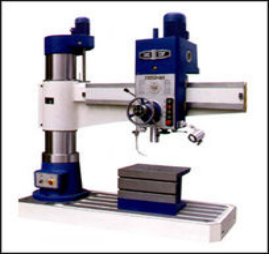
图2-1 普通钻床示意图
2.2国外研究现状
多轴钻床最早出现在日本地区,后经台湾传入大陆。距今已有二十年的历史。由于进入国内时间不长,所以很多企业都未曾耳闻。其实它是装在钻、攻机床上的夹刀头子,并且是两轴以上同时加工钻孔件或攻牙件,故称多轴钻床。一台普通的多轴钻床一次能把几个乃至十几二十个孔或螺纹加工出来。如配上气(液)压装置,可自动进行快进、工进(工退)、快退、停止。多轴钻床也称群钻床,可用来钻孔或攻牙,一般型号可同时钻2-16孔,提升效率,固定机种轴数不拘,钻轴形式,尺寸大小可依客户之需进行设计加一种运用于机械领域钻孔设备20世纪80年代日本人最早使用其设备,后经台湾传入大陆。距今已有二十几年的历史。
一台普通的多轴钻床一次能把几个乃至十几二十个孔或螺纹加工出来。如配上油压或数控装置,可自动进行快进、工进(工退)、快退、停止。多轴钻床也称群钻,可用来钻孔或攻牙,一般型号可同时钻2-16孔,提升效率,固定机种轴数不拘,钻轴形式,尺寸大小可依客户之需进行设计加工。多轴钻床广泛应用于机械行业多孔零部件的钻孔及攻丝加工。如汽车、摩托车多孔零部件:发动机箱体、铝铸件壳体、制动鼓、刹车盘、转向器、轮毂、差速壳、轴头、半轴、车桥等,泵类、阀类、液压元件、太阳能配件等等。多轴钻床可分为可调式和固定式两种规格,可调式多轴钻床在其加工范围内,其主轴的数量、主轴间的距离,相对可以任意调整,一次进给同时加工数孔。在其配合液压机床工作时,可自动进行快进、工进(工退)、快退、停止.同单轴钻(攻丝)比较,工件加工精度高、工效快,可有效的节约投资方的人力、物力、财力。尤其机床的自动化大大减轻操作者的劳动强度。固定式多轴钻床采用单件(加工件)专机的设计方案,根据其加工件加工频率高、量大之原因,专门量身定制一件一机的设备,在其工作中勿须担心尺寸跑偏而伤脑筋。除用到常规的产品外,还可根据客户的特殊要求进行专项设计。图2-2为多轴钻床的示意图。
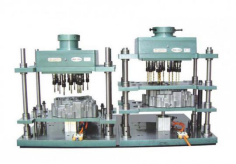
图2-2为多轴钻床示意图
3. 多轴钻床的加工现状和趋势
多轴加工是在一次进给中同时加工许多孔或同时在许多相同或不同工件上各加工一个孔。这不仅缩短切削时间,提高精度,减少装夹或定位时间,并且在数控机床中不必计算坐标,减少字块数而简化编程。它可以采用以下一些设备进行加工:立钻或摇臂钻上装多轴头、多轴钻床、多轴组合机床心及自动更换主轴箱机床。甚至可以通过二个能自动调节轴距的主轴或多轴箱,结合数控工作台纵横二个方向的运动,加工各种圆形或椭圆形孔组的一个或几个工序。
多轴钻床是伴随着经济的飞速发展和工业现代化的需要而产生的。其被应用与许多方面,像汽车零部件的加工,农业机械的零部件的加工以及其它大批量生产加工生产多孔零件的地方,多轴钻床在加工业中有着很大的优势。它的使用使加工速度提高。因为当一个工件在同一个方向上有数个孔时,用普通钻床加工时就要加工一个孔后又挪动工件加工另一个孔,这样就需要专人搬动工件,对于小型工件可以采用这种方法,但当工件很大时再采用这种方法就很落后,生产率很低,成本增加。所以,我们在批量生产多控工件时就需要一种专门的机床来加工,所以就产生由单臂钻床衍生而来的多轴钻床。
多轴钻床与普通钻床的不同是多轴钻床的主轴箱是像太阳系一样,绕中间轴均部排列的主轴被中间轴带动转动,主轴带动刀具转动,完成切削工作。这样多孔工件被一次加工成行,从而使劳动强度大大减小,加工时间大大缩短,提高了劳动效率,降低了测评成本。
3.1 多轴钻床的优势
1.加工速度快。使用多轴钻床加工轮辐,较之采用普通摇臂钻床,平均功效提高30%。
2.加工质量好。采用该钻床加工的孔组,孔的位置尺寸误差小,工件互换性好,从未出现过
3.多轴钻床造价低廉,维修方便,技术难度不高。
3.2 多轴钻床的种类和分类
多轴钻床的型式是多种多样的。根据多轴钻的结构可把多轴钻分为内啮合多轴钻和外啮合多钻头。内啮合多轴钻是指齿轮传动为内啮合式,外啮合多轴钻式指齿轮传动为外啮合式。根据钻头形式可分为卧式和立式两种。
4. 结论
总之,多轴钻床在我们的工业生产中有着重要的意义。它大大的提高了我们的劳动生产也推动了我国生产行业的迅速发展。我们应该加强对多轴钻床领域的开发。
参 考 文 献
[1]通用可调多轴钻床[J]. 杨庆荣. 机械与电子. 1985(05)
[2]多轴钻床改造及经济性分析[J]. 戴雄. 金属加工(冷加工). 2010(09)
[3]一种专用多轴钻床的设计与制造[J]. 侯志坚,王晓琴. 机床与液压. 2006(02)
[4]多轴钻床传动与液压系统的改造[J]. 周胜. 装备维修技术. 1998(03)
[5]微型计算机在自动多轴钻床中的应用[J]. 李文斌. 机械工业自动化. 1985(04)
[6]小轴距多轴钻床的设计和应用[J]. 李永贵. 机械制造. 1983(01)
[7]用普通车床改造成多轴钻床[J]. 黎阳. 装备制造技术. 2003(03)
[8]多轴钻床改造及经济性分析[J]. 刘磊. 科学技术创新. 2018(01)
[9]新型立式可调多轴钻床[J]. 汪泽民,浦海燕. 机械工程师. 2013(09)
[10]大型数控多轴钻床研制成功[J]. 机械设计与研究. 1994(04)
[11]大连组合机床研究所主编.组合机床设计(第一册)机械部分.北京:机械工业出版社,1978
[12]濮良贵,纪名刚编.机械设计(第七版).北京:高等教育出版社,2002
[13]刘鸿文主编.材料力学(第三版上册).北京:高等教育出版社,2001
[14]冯炳尧,韩泰荣,蒋文森编.模具设计与制造(第二版).上海: 上海科学技术出版社,2000
[15]郑堤,堂可洪编著.机电一体化设计基础.北京:机械工业出版社,1997
[16]濮良贵,纪名刚编著.机械设计(第七版).北京:高等教育出版社,2001
[17]杨长能.张兴毅.可编程序控制器(PC)基础及应用[M].重庆:重庆大学出版社
[18]ZJK7532A多功能数控钻铣床使用说明书.武汉:华中科技大学·材料学论文
[19] Swaffield JA, Boldy AP. Pressure surge in pipe and ducsystems.Aldershot: Avebury Technical, Aldershot: Ashgate Publishing Ltd,ISBN 0-291-39796-4, 1993.
[20] Wylie EB, Streeter VL. Fluid Transients. New York: McGraw-Hill,Inc.ISBN 0-07-072187-4, 1978.
毕 业 设 计(论 文)开 题 报 告
2.本课题要研究或解决的问题和拟采用的研究手段(途径):
1.本课题的研究内容以及需要解决的关键问题
1.1研究内容
在一批铸铁零件上分别加工4-
孔,在普通立式钻床上进行孔加工,通常是一个孔一个孔的钻削,生产效率低。用非标设备,即组合机床加工,生产效率高,但设备投资大。如果把普通话立式单轴钻床改造成立式多轴钻床,就可以同时完成多个孔的钻削,生产效率高,投资少,生产准备周期短,产品改型时设备损失小。
本设计的主要要求是:多轴箱拆装组合灵活、方便、快速、重量轻。
本设计的主要内容是:1、多轴箱齿轮传动方案设计;2、多轴箱内齿轮设计;3、多轴箱内轴结构设计;4、多轴箱导向装置设计;5、设计说明书;6、Pro/E实体。
本设计的原始参数是:1、工件尺寸为
;2、工件硬度
;3、4-
尺寸精度为
。
1)普通钻床改造成多轴钻床
(1)普通立式机床的选型
在一批铸铁连接件上有同一个面上有多个孔加工。在普通立式钻床上进行孔加工,通常是一个孔一个孔的钻削,生产效率低,用非标设备,即组合机床加工,生产效率高,但设备投资大。但把一批普通立式普通单轴钻床改造为立式多轴钻床,改造后的多轴钻床,可以同时完成多个孔的钻、扩、铰、等工序。
2)多轴齿轮结构箱与传动箱的研究
1.箱盖、箱体和中间板结构
(1)箱体选用240mmx200mm长方形箱体,箱盖与之匹配。箱体材料为HT20-40, 箱盖为HT15-33.
(2) 中间板的作用:
箱内部分是轴承的支承座,伸出箱外的部分是导向装置中的滑套支承座,为便于设计人员选用,已将中间板规范为23mm和28mm两种厚度的标准,现选用23mm厚的中间板,材料为HT15-33。
2.主动轴和惰轴的设计
(1)轴材料的选择
(2)轴径的确定
(3)轴结构设计
3) 构建实验模型
(1)建立等比例缩小的实物模型应用相同材质构建等比例缩小的实体模型,并建立相应的外部环境,测试整个系统在实际中的运行状况。
1.2 拟解决的关键问题
通过上述的理论基础以及查阅相关论文,目前在普通钻床改造为多轴钻床的研发工作中,拟解决的关键问题包括以下几个方面:
(1)生产任务
(2)普通立式钻床的选择类型
(3)如何设计多轴齿轮传动箱
(5)如何绘制多轴箱的结构设计与零部件
(6)导向装置的设计
2 本课题拟采取的研究方案
为了完成普通钻床改造为多轴钻床系统的设计,设计其硬件结构,也就是其机械部分是不可或缺的,通过“研究内容”部分的叙述,机械结构部分需要设计的内容包括多轴箱齿轮传动,多轴箱内齿轮设计,多轴箱内轴结构设计以及多轴箱导向装置设计等部分,考虑到系统大多属于中大规模以上布置,通常采取一维控制。
2.1 课题研究拟采用的手段和工作路线
(1)在学校图书馆查阅相关资料。
(2)在工厂的实践毕业实习。
(3)通过老师和工程师的指导。
(4)通过浏览因特网上的相关资料。
2.2 课题研究拟采用图纸内容及张数
(1)多轴箱传动系统结构装配图:1张。
(2)传动轴零件图:若干张。
(3)多轴箱箱体零件图:1张。
(4)齿轮零件图:1张。
(5)中间板零件图:1张。
2.3 课题研究拟采用工作路线
(1)设计准备
了解设计任务书,明确设计要求、工作条件、设计内容的步骤;通过查阅有关设计资
料,参观实物征询操作人员的建议等,了解设计对象的性能、结构及工艺性;准备好设计
需要资料、绘图工具;拟定设计计划等。
(2)草图设计
绘制装配草图;进行总体结构设计和部件设计。
(3)编写设计说明书
2.4 实物模型仿真研究
本课题拟用相同的材料构建等比例的实物模型,在实际条件下进行系统测试,得到相应的数据后对此前设计进行优化调整。