板材的的等径角挤压
摘要
本文介绍的是不同宽厚比(W/T)的长矩形坯料的等径角挤压的问题。并对内部塑性变形区和进出口通道进行了应力分析,他们是有接触擦力和板材的几何形状确定的。同时,对及加工进行优化设计,制定了设计工具的工艺方案。可以看出,当板材的W/T>>1时,这为大规模冶金中处理庞大的平板状批料和技术商业化提供了重要的技术优点。
关键词:等径角挤压;优化处理;板材;大规模商品化
1、导言
材料结构在剧烈塑性变形(SPD)的影响下带来重要的科学和实际利益。这个方案的一个重要优点是可以用一个高效益的方法使大量的不同金属或合金坯料的晶粒结构细化到亚微米级。这种超细晶粒结构,通常在从几微米至0.2微米,同时具有高的强度和良好的延展性,因此广泛应用于结构材料。随着(SPD)商业化的应用,相关的成行技术也得到实质性进展,关键因素是变形方案和加工特点的优化。不论加工目的,材料性质,温度—应变速率条件如何,SPD具有大而统一的应变,简单剪切变形和低应力变形。在SPD的几个较著名已知的方法,等径角挤压(ECAE) ,是目前被认为最应用最多的。然而,等径角挤压的发展并不完善。尽管在这一领域应用广泛,但绝大多数的
以细长坯料的应用为主,如文献[1]。这些棒状坯料会限制材料,特点和等径角挤压的特点和进一步的加工。他们和少应用于半成品。目前也没有商业化的报道。相比之下,板材的等径角挤压出现在轧制后,第一次出现在文献[ 2 ] 。
再加上其他的技术优点,等径角挤压工艺有很大现实意义。目前细长坯料的等径角挤压已经有了很好的研究和开发,板材的等径角挤压的特点还不清楚,在仅有的几个相关出版物[ 3-5 ]也没有论述 。本文板材的等径角挤压为例,讲述一下板材的等径角挤压的一些重要细节。
2 、机加工我们可以认为矩形坯的等径角挤压就是(图一)厚度T,宽度W和长度L的坯料通过角度为90度的通道。在图一中,坯料的初末位置(1,2)分别用点画线和实线表示。由于坯料宽度不变,坯料作为一个刚体移动时,图[ 6 ]表明,应力应变状态和塑变区的范围取决于进口通道1和出口通道2所施加的边界条件。因此,应对相应的条件加以分析。
2.1 进气通道
等径角挤压开始时,将坯料润滑并放置在模具入口。实际摩擦力取决于工件和刀具之间的接触面积和正压力。假设管道内的应力类似于线形塑性压缩,正压力 σn ∼ (p − Y )其中,P是轴向压力,Y是材料的流动应力,如果p ∼ Y,正压力σn ∼ 0 ,对于 L/T >>1的长坯料来说,塑性接触主要由有横向屈曲形成。这种不规则的原始接触仅提供很小的摩擦力。如果p > 2Y,正压力σn > Y ,塑性区接触面积大约等于坯料和管道的接触面积。在这种情况下,沿管道轴向相同润滑下将会产生一个大的摩擦力和一个明显的压力差△P。因此原始压力pe = p1 + △ p是通道入口的轴向压力。实验表明,△P这一增量总是与管道长度成正比。假设有效的变形摩擦力均匀分布,△P可有此公式计算
(1)
F是坯料和管道的接触面积。在某一特定条件下,
已知,图2矩形通道的四个摩擦面上的原始压力的最大增量为:
(2)
参数n=L/T , m=W/T,限定了坯料的长度和宽度。特殊情况下,m=1对应于正常情况下的长棒状坯料,m>>1指的是板状坯料,m<<1 指的是条状坯料。公式(1)(2)表明,原始压力
由于m、n决定 即使在校摩擦力状态,原始压应力可能比材料的流动应力明显大。
降低摩擦力,增加刀具使用寿命和冲压稳定性的有效方法是通过移动管道面(图7)一种可能的方法(图2b,详见图7)是用固定模具和随坯料1运动的矩形槽滑杆2 形成进口管道。这样,就消除了三个管道面上的摩擦,原始压力的最大增量为
(3)
另一种情况(图2)进口通道有两个滑杆2,3组成。因此模具的前后面固定。相应增量为
(4)
对比公式(2)-(4)可得出结论:在所有情况下,原始压力都随长厚比的增加而增大。为了有效加工,长厚比应足够大。但实际长厚比一般取为4~8。图2c的
p/Y几乎是图2的两倍对于固定通道(图2a)原始压力也取决于宽厚比m。但是这个比率不影响原始压力在滑动渠道这两种情况下的大小。图3示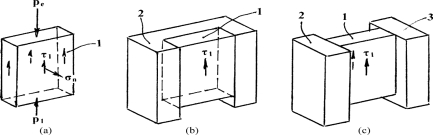

以m为变量,n=6 时,计算结果三种状态已给出:1.长坯料 2 .板形 3 .条形. 很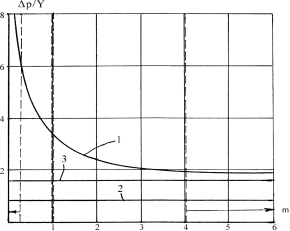
显然,长形坯料特别是条形坯料在固定通道下会增大
p/Y。在这些情况中,只有在大压力下的移动渠道模具才能对大坯料和硬质合金坯料进行等径角挤压。然而,对于板材来说,两滑动面对原始压力的减小作用甚小。因此,大多数大板材可以在固定进口渠道和常压下使用简单模具。
2-2出道口
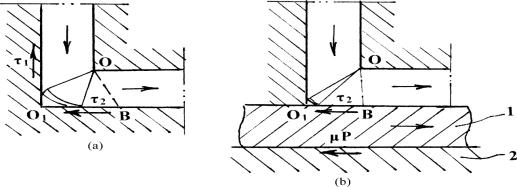

与进口渠道相反,出口渠道的润滑是个难题。由于方向改变巨大,即使是用最好的润滑剂,也会出现底部压力过大,产生沿底部接触面
出现滑移,还会出现摩擦 。这话导致挤压力太大,坯料表面质量差,模具磨损加剧。在底部渠道里用一个滑杆就可以解决这个问题(图4b)。
这样材料和模具间的弹性摩擦被滑杆 和导轨之间的摩擦所代替。在挤压过程中,滑杆 处于自由状态,为克服滑杆和导轨之间的摩擦力,须沿坯料接触表面
产生一剪切力
。
f
=
指的是接触面
的面积,
是摩擦因数。通常情况下,滑杆速度接近挤压速度。由于摩擦并不稳定,可以观擦到滑杆运动中的一些偏差。如果
大于滑杆与毛坯的弹性摩擦力,则流动类似于固定模具。在出口渠道的相应的边界条件不能提供高效加工所需要的塑性区和简单的剪切变形。因此,
应该非常小。
2-3塑性变形区
内外渠道为塑性区限定了摩擦的边界条件
和
(图5为
>
时滑移情况) 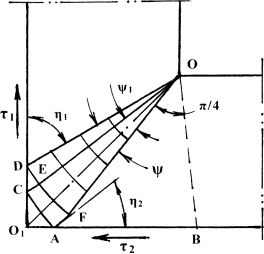

假设材料处于理想塑性状态。滑移线PEDO中心区,混合边界CDE和不变区
CA,阴影区的中心角: 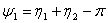
可由此公式算出.
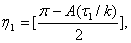
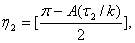
是指材料的流动剪切应力。图6考虑了
、
在特殊情况下的解决方法。
现在我们做一下总结,概括一下等径角挤压工艺的优化方案。首先,注意到固定的出口渠道总是出现的润滑问题。在
的极限条件下,经滑移线分析,进口处全部压力
.这将会使坯料和渠道全部接触,在
的狭长渠道和有限摩擦力
>0的实际情况下会产生大的挤压力
。实际上,一、已出版的资料显示:挤压了可高达7 (图9)
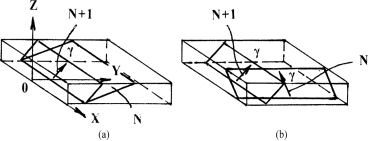
由于大多数材料处于低加工温度下都不允许如此大的压力。因此,尽管简便出口固定渠道在工业应用中也不实用。
出口渠道底面有一适当滑移面,摩擦力
和摩擦系数
都较小。在这种情况下图5的滑移区域可被看作当
=
=
=
=0和塑性区是单滑移线
时,“零方案”的小变动。然后用滑移线波动省略中间结果 ,精确到第二位 ,可得到公式
~
Y,
~
在进口 内部 总压力为
~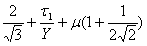
与Ep一致.如果挤压里增量
变化不明显。在摩擦力下,坯料和进口渠道
和
能足以形成接触面的.出口渠道移动,进口渠道可以是固定的(图2a),也可以是有两个滑移面(2c)如前所述,简单固定渠道对于长厚比
的板材比较有效,然而对于长坯料和带状坯料,则适合用滑动轨道。因此仅有第一种情况要进一步考虑多段加工。
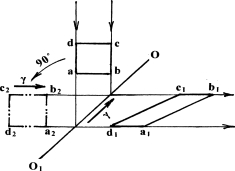

3-1基本路线
为了集聚大的剪切应变,控制变形,需要要在每段之后绕坯料的x、y、z对称轴反复旋转进行等径角挤压。对于板材来说,旋转的基本系统或路线可为:A-无旋转 B-坯料绕Z轴旋转
C-坯料绕Z轴旋转 D-坯料旋转
与轴旋转 中,长宽相等的方坯料最受欢迎,因为不论怎样旋转它们都可在一相同模具中加工。无数可能的旋转组合产生不同结构,组织。尽管这个基本路线最简便,但其它路线可能在一些特例中更有利。其中一些方法在后面将被提到。
3-2材料的变形
由于两渠道中接触摩擦力较小,塑性区的中心角
小。在这种情况下,通过塑性区的材料拉力重要包括边界DO和AFO的两个简单剪切力。这种集中剪切大致与
的沿
时相对应的“0方案”的滑移线
单面剪切相平衡。图6显示了在剪切力
作用下,正方形abcd。沿
转变成平行四边形
可以看出,随着剪切力变成流动方向,通过把进口渠道原始位置abcd旋转
到出口到内部
位置。就可达到相同的变形。这种流动方法有益于计算多段等倾角变形。因为对于板材来说,所有变形都发生在坯料的平面上。通过保留出口道内部材料的位置和在不同路线段应用连续剪切力。可以简化这个过程。因为短暂作用不影响元素变形,可以认为
由于
作用在坯料平行面上,底部被修整,顶部
逐渐过渡。最后的位移是所有先前剪切作用的总和。图7、8显示了基本路线中的四段的相应位移和相对于原坐标x、y、z整个材料的变形。在长坯料中,A,C平板流动和变形相同。类似地,C和D分别在每2和4到次程序后提供材料恢复所需的循环载荷。路线A可观察到随长度增加Y向倾角增大,最大变形量的变化情况。路线B的变形量比的小
倍,在无数Ⅰ段后它们都位于偏离Y
方向。
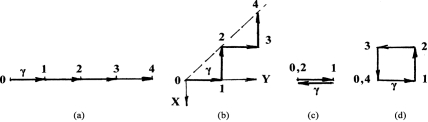
图 7. 组织的移动路线A (a), B (b), C (c), 和D (d).
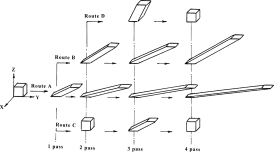
图. 8. 在四途径经由路线A, B, C 和 D. 之后,工件的变形。
3-3剪切带
机加工考虑的因素是简单剪切变形模式和每段中剪切带角度。剪切带在多端等倾角变形中起重要作用。在第一段,使用小角度,晶核强烈组织了沿
方向长度变形。在以下的工序中。剪切带内部的微观流动取代了连续的塑性流动,它们朝同一剪切方向
。尽管SPD晶粒细化机制还不是很清楚,仍有无数试验可以断定了对于不同材料和加工条件(温度、应变率)在等径角挤压过程中,剪切带占据新角度晶界的最大部分。是晶粒细化到亚微米和纳米尺寸的其他方法包括剪切带的交汇以及剪切带与晶界所组成的材料的旋转。因此重新细化的强度和细化为结构形态取决于加工剪切带的进展。和材料的大晶界角。在每个工序中,微观剪切带随相应的宏观 增加。在随后的工序中,剪切带依然是稳定形状,他虽材料一块流动,随坐标改变方向。任何工序中剪切带位置由下一个工序的变形决定。例如板材为旋转的第N和N+1个工序,剪切带的变形由第N+1剪切引起但是板材旋转
时,N+1不影响N的剪切带,因而,在板材的多段加工中,有两个与x、y向变形相对应的两个独立系统。
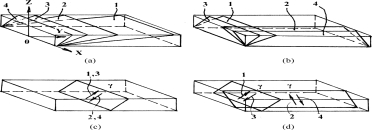
图10显示经过四个路线后,剪切带的位置1、2、3、4分别与剪切带的一、二、三、四段对应。