工艺规程制订与并行工程
。
工艺规程制订
工艺规程制订包括决定最适当的制造及装配步骤和顺序,在这些顺序和步骤中他们必须根据所提出的详细的设计说明书规范完成给定零件或产品制造。 能够被计划的工艺范围和多样性通常由于公司车间可用设备和技术能力而受到限制。在公司内部不能够制造的零件必须到外部市场购买,工艺规程制订所提及的工艺选择同样也受到详细设计资料的限制,我们稍后将会回到这一点。
工艺规程制订通常是由制造工程师完成的,工艺制订者必须熟悉工厂中详细可用的制造流程并且能够说明工程图。基于制订者的知识、技术和经验,用于制造每个零件的工艺步骤以最合乎逻辑的顺序被发展制订。下列各项是在工艺规程制订范围里的许多决定和详细资料:
.设计图的说明. 在工艺规程制订的开始,产品设计的这一部分( 材料、尺寸、公差、表面处理等等)必须进行分析。
.工艺和顺序. 工艺制订者必须选择哪一个工艺是必需的及必需工艺的序列。此外还必须准备好一个简短的工艺步骤描述。
.设备选择. 大体上,工艺制订者必须逐步展开利用工厂现有机器的计划。另外,组件必须被购买或在新设备上的投资必须被制定。
.工具、冲模、铸模、夹具、量具. 工艺必须决定每个工序需要什么工具,这些工具的实际设计和制造通常通过委派工具设计部门和工具库或者联系专攻那种工具制造的外面厂商来完成。
.方法分析. 车间规划,小工具,提升重物的提升间。甚至在一些人工操作情景中的肢体动作也被指定。
.操作步骤. 工作测量技术被用来为每个操作设定时间标准。
.切削工具和切削条件. 这些必须对加工操作通过推荐标准手册来进行详细说明。
零件工艺规程制订
对于单个零件,加工顺序通过一种被称为进路表的表格来进行文件证明备份。就如工程图被用于详细说明设计产品一样,进路表被用于详细说明工艺计划。他们是类似的,一个用于产品设计,另一个用于制造。
制造单个零件的典型加工顺序包括:(1) 一个基本工序 (2) 二级工序 (3) 提高物质特性工序和(4) 最后工序。一个基本工序决定了工件的起始造型。金属铸件、塑料成型、金属精炼是基本工序中的实例。起始造型常常必须通过改变起始造型操作(或者接近于最终造型)的二级工序来精制。二级工序习惯于和基本工序一起提供起始造型,当砂型铸造是基本工序,车加工通常是二级工序。当轧钢厂制造金属片是基本工序,冲压操作像冲裁和弯曲通常是二级工序。当塑料注入成型是基本工序时,二级工序通常是不必要的,因为他的大多数几何特征制造通过别的方式如成型制造来完成。塑料成型和其他操作的二级工序被称为净成型工序的并发二级工序,需要一些但并不多的二级工序的操作就是所提到的近似成型工序。许多有印象的摸锻件就是这一类,这类零件能够经常在锻造(初级工序)阶段被成型,因此减少了必要的加工(二级工序)。
一旦模型被建立,许多零件的下一步是改良它们的机械物理性能。提高特性工序并不改变零件模型,然而,它却能改变零件的物理特性。金属零件的热处理操作就是最普通的实例。类似的如玻璃通过热处理来制造钢化玻璃,对于大多数零件的制造来说,这些特性加强工序在加工工序中并不需要。
最后工序通常对零件(或装配体)的表面提供一个涂层。例如电镀、薄膜沉积技术、涂漆。表面处理的目的是改善外观,改变颜色或者表面保护防止腐蚀和磨损等等。在很多零件中最后工序是并不需要的。例如:塑料成型就很少需要最后程序。当必须需要最后程序,他通常是加工顺序的最后一步。
装配工艺规程制订
一个既定产品的典型装配方法由以下因素决定的:(1)预期产品数量(2)装配产品的复杂性。例如:不同组件的数量和(3)常用装配工艺。例如:机械定位焊接、对于小数量产品,通常在人工装配线上进行装配。对于大量制造的一打或这样组件的简单零件,要采用适当的自动化装配线。无论如何这里有一个工作必须被完成的优先顺序,这个优先需求经常用一个优先表来进行图表描绘。
装配工艺规程制订包括装配指令的发展,但是更详细地对于小批量生产。在一个岗位完成整个装配,对于一个装配线上的大批量生产,工艺规程制订由一种分配工作条件到装配线个别工位并被叫做人工投入线性平衡法的程序组成。这种装配线按照装配线平衡解决方案决定的顺序发送工作单元到个别工位,在个别组成,任意工具或夹具的工艺规程制订时,一条装配线的决定、设计和制造必须被完成,并且工作站的必须被列出来。
制造或购买决定
在工艺制定过程中出现的一个重大问题是一个特定零件应该在公司内部的工厂内生产还是从外部销售商处购买,并且这个问题的答案被认为是制造或购买决定。如果公司没有技术设备或制造零件所必须的详细制造工艺中的专门技术,那么答案就很明显了。因为没有其他选择零件必须购买。然而,在很多例子中零件既可以在利用现有设备在内部制造或者可以从外部拥有相似制造能力的生产销售商处购买。
在我们的关于制造或购买的决定的讨论中,他应该认识到在开始几乎所有的制造者从供应商那里购买原料。一个机械加工厂从一个金属经销商购买他的起动柄原料或从一个铸造厂购买他的砂型铸件。一个塑料成型厂从一个化工厂购买他的模塑料。一个冲压厂可以去经销商或直接从轧钢厂购买金属片。很少的公司能够在操作中从原料一直进行垂直整合,这看来至少购买一些也许在他的工厂可以另外制造的零件是合理的。也有可能为公司使用的每一个组成要求制造或购买决定。
这里有许多影响制造或购买决定的因素,一个人可能认为成本是决定是购买还是制造零件的最重要的因素。如果一个外部经销商比公司工厂更精通于制造零件的工艺,因而公司内部生产成本可能比经销商赚取成本后的价格还要高。可是,如果购买决定导致公司工厂设备和劳动的闲置,购买零件的表面优势就会丧失。考虑以下例子制造或购买决定。
为一个特定零件被引述的价格是100个单位的每单位$20.00。制造零件的成分如下所示:
单位原料成本=每单位$8.00
直接劳动成本=每单位$6.00
劳动加班150%=每单位$9.00
设备修理成本=每单位$5.00
___________________
总计=每单位$28.00
这个组成应该被购买还是在内部制造?
解决方案:尽管经销商的引证似乎支持购买决定,让我们来考虑如果引证被接受可能在生产操作中的冲突。$5.00设备维修成本是已经被制定的投资成本,如果设备设计因为购买零件的决定而变的没有利用价值,那么这个固定成本仍然继续尽管设备闲置着。同样,如果零件被购买由工厂空间,效用和劳动成本组成的$9.00的劳动间接成本仍然继续。通过这种推理,如果应该已用于生产零件的设备闲置的购买决定并不是一个好决定因为他可能花费公司将近$20.00+$5.0+$9.00=$34.0每单元。另一方面,如果正在讨论的设备可以被用于生产其他零件并且内部生产成本低于外部联系报价,那么一个购买决定就是一个好决定。
制造或购买决定并不像这个例子中的那样直接。这几年的一个趋势,尤其在汽车工业,公司和零件供应者建立紧密关系。由此我们将引出并行工程。
在计划操作方面制造公司有很大兴趣利用计算机辅助工艺(CAPP)系统来完成。那些熟悉加工详细资料和其他工艺的工厂培训的工人逐渐退休,并且这些人在将来工艺制订的过程中是非常有用的。一种可选择的用于完成这种功能的方式是必需的,CAPP 提供了这种选择。CAPP经常被看作是计算机辅助制造(CAM)的一部分。然而这种趋向意味着CAM是一系列系统。事实上,当CAD和计算机辅助设计协同作用创造了一个CAD/CAM系统。在这样一个系统中,CAPP成为设计和制造之间的直接联结。来自计算机辅助工艺的优点包括以下几点:
.工艺合理化和标准化. 自动工艺规程制订比完全用手工编制工艺产生的更合理化和一致化。标准设计趋向产生低成本和高生产质量。
.增强工艺制订者的生产力. 在数据文件中的系统方法和标准加工设计的实用性使工艺制订者可完成更多的工作。
.减少工艺规程的制订时间. 与手工准备相比,利用CAPP系统的工艺制订者可以在较短的时间内准备好进路表。
.改良异读性. 计算机准备的进路表比手工准备的进路表更容易简洁。
.结合其他应用软件. CAPP 系统可以在界面上与其它应用软件结合,象成本估计和工作标准。
计算机辅助工艺围绕着两个路径来设计,这两个路径被叫做:(1)CAPP检索系统和(2)CAPP生成系统。许多CAPP系统结合这两种路径而被称为生成检索CAPP系统。
制造业的并行工程和设计
并行工程引用一种常用于产品发展的路径,通过它使工程设计功能、工程制造功能和其他功能综合起来以减少一种新产品投放市场所需要的共用时间,也被称为并发工程,他可能被认为是CAD/CAM技术的类似组织版本,按照传统路径来使一件产品投放市场。如图(1)a所示,工程设计功能和工程制造功能这两种功能是分开并且连续的,产品设计部门开展一项新的设计有时很少考虑到公司的制造能力,也很少有机会能够让制造工程师来提供如何使设计更容易制造的一些建议。他好像消除了在设计和制造之间的一堵墙,当设计部门完成设计,他投掷工程图和说明书越过这面墙,并且那时工艺规程制订也开始了。
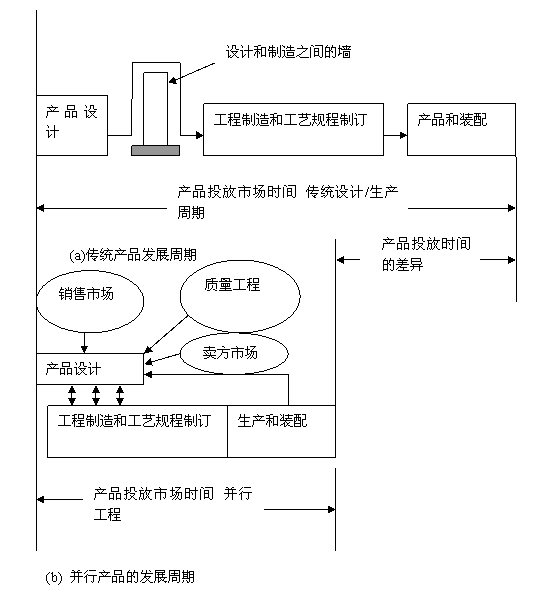
图(1) 比较 : (a) 传统产品发展周期和 (b) 并行产品的发展周期
通过比较,实行并行工程的公司,工程制造部门在早期就参与到产品发展周期。为如何使产品和他的组成能够被设计的更适于制造提供建议。他同样为产品提供制造计划继续进行的早期准备,这种并行工程的路径在图(1)b中被描绘出。除了工程制造以外其他功能同样被包括在产品发展周期中,如质量工程、制造部门、后勤服务、市场供应评定组成和一些情况下将使用这些产品的消费者。在产品发展阶段的所有这些功能不仅能改善新产品的功能和性能,同时也能改善他的可造性、自检性、易测性、服务能力和可维护性。通过早期功能改善,因为在最终产品设计之后的回顾太晚以至于不能对设计进行便利的修改的不利因素的消除,使产品发展周期的持续期大大减少。
并行设计包含以下因素:(1)一些制造和装配设计(2)质量设计(3)成本设计和(4)生命周期设计。另外,像快速成型、虚拟制造、和组织转变等辅助技术需要被用来促进公司的并行工程。
制造和装配设计
据估计一件产品的70%的生命周期成本是由在产品设计时所做的基本决定所决定的,这些设计决定包括每个零件的材料、零件模型、公差、表面处理、零件是如何被组织装配的和常用装配方法。一旦这些决定被指定,减少产品制造成本的能力就会被限制。例如,如果产品设计者决定用铝砂型铸造法制造一个分开零件,但是这个零件的工艺特性只能通过加工来完成(如螺纹孔和配合公差),制造工程师没有选择的余地,只能按照先砂型铸造在加工的方法来达到既定要求。在这个例子中,用一个在单独步骤所需要的塑料模制品也许是一个较好的决定。因此,当产品设计展开时给制造工程师一个忠告设计者的机会对产品的顺利可造性是非常重要的。
这种被用于尝试描述顺利改变一件新产品的可造性的条件是制造设计(DFM)和装配设计(DFA)。当然,DFM和DFA是紧密相连的,因此让我们用制造和装配设计(DFM/A)的形式来表达。制造和装配设计包括在一件新产品中的可造性和可装配性的综合考虑,这包括: (1)组织变化和(2)设计原理和指导方针。
.在DFM/A中的组织变化. DFM/A的有效执行包括公司组织机构的正式或非正式的变化,因此设计职工和制造职工之间有很好的交流和交互作用。这可以通过以下方法来完成:(1)通过成立由产品设计者制造工程师和其他员工(例如:质量工程师、材料专家)组成的攻关小组来进行产品开发;(2)通过要求设计工程师用一些事业时间在制造上,以能够掌握第一手可造性和可装配性是如何通过产品设计联系在一起的;(3)通过指派制造工程师到产品设计部门在一个临时的或专任的基础上做一个还原性顾问。
.设计说明和指导方针. DFM/A为了理解如何设计一个既定产品来使可造性和可装配性最大化也依赖于设计说明和指导方针的使用,这些通用设计指导方针中的一些几乎适用于任何产品设计。在其他方面,一些设计原理只适用于特定工序,例如:轴或锥度在阶梯中的使用和利用模制品来切除模内零件,在制造过程中我们只把这些具体过程指导方针放在书本上。
指导方针有时互相矛盾,一条指导方针是“简化零件模型,避免不必要的特征”。但是在同一表格里的另一指导方针为了装配安全而规定在设计产品时“特殊几何特征必须不时加上他的组成”。而且他也许值得来结合个别装配件的特征来减少产品中零件的数量。在这些示例中零件制造设计与装配设计相冲突,在这个矛盾冲突的两边,一个适当解决方法必须被发现。