Typical failure analysis and processing of belt conveyor
Abstract:The paper analyzes two typical failure forms of roller and conveyor at the belt conveyor, and describes the maintenance methods of prevention and elimination failures to ensure the normal operation of belt conveyor.
Keywords: belt-conveyor, fault, deviation, service.
1. Introduction:
Belt conveyor is a commonly used equipment of continuous transport, it has a high efficiency and large conveying capacity, simpler construction, small amount of maintenance. Can be achieved at different distances, different materials transportation. It iss widely used in mining, coal handling system in thermal power plant and other projects. Belt conveyor will often occur some typical problems in the course, this paper Based on research common typical failure of belt conveyor during use, analysis the cause of failure, proposed some effective methods to solve the problem.
2. Typical faults of conveyor belt:
2.1. Conveyor belt deviation
In the belt conveyor, as the conveyor belt is traction components, transmit power and motion, also is carrying components, support material load. Working more complex, so at work often happen belt deviation. Deviation is the conveyor belt during operation, the center line of belt deviation the center line of conveyor. As the conveyor belt deviation may cause between the belt edge and rack wear, cause belt edge premature damage, Ranging impact the life of conveyors, affect the throughput of materials, Weight is caused by withdrawal material, even happen stop occurrence, direct impact on production. As the conveyor belt is more important, the most expensive parts. Its price about 25%~50% to the conveyor. So analysis the reasons of belt deviation, reduce and eliminate belt deviation, It is an important part of ensure belt to work, extend equipment life. Cause the belt occurs deviation because of the following factors.
2.1.1. In the device itself
a. Rack rigid is poor, large deformation under load, causing the belt deviation.
b. The larger error of roller outer cylindrical, caused deviation when the conveyor belt running.
c. The supporting roller rotation is not flexible, causes the conveyor belt both sides stress to be uneven, causes the conveyor belt deviation.
d. The parallelism error cylindrical axis and roller axis is too big, causes the conveyor belt deviation.
e. Conveyor belt itself is questionable quality, thin and thick uneven, caused a shock lead running conveyor belt deviation.
f. Conveyor belt manufacturing quality have defects, the length of belt both sides edge is inconsistent, cause running conveyor belt deviation.
g. Not parallel with belt connector, connection error is too big, cause belt deviation.
2.1.2. Installation adjustment
a. Drive, change roller axis and conveyor centerline vertical error is too big, make conveyor and horizontal line have a bigr inclination, cause belt deviation.
b. Roller axis and conveyor centerline vertical error is big, will cause belt deviation also.
c. The connection strength between rack and ground is not enough, the rack unstable, causing belt deviation.
d. The feeding plate of discharge trough and improperly located, both sides of the conveyor belt uneven force cause belt deviation.
2.1.3. With maintenance
a. The cleaning performance of sweeper is poor, make the roller cylindrical diameter local increases.
b. Feeding mouth location is wrong, so that the material partial load on the conveyor belt, cause belt deviation.
c. Poor maintenance and improper adjustment, resulting in the conveyor belt deviation.
d. For the steel cord belt, as the manufacture of steel cord is uneven force, so that a deviation occurs in the operation, or a strong difference of belt, large elongation under load, causing the vibration, the belt will deviation.
e. Also, the vibration of running conveyor belt system can cause the deviation.
f. In addition, when conveying some viscous material, make the roller, etc. bonding materials, make the cylindrical diameter of roller part increases, causing belt deviation.
2.2. Measures to prevent the belt deviation
2.2.1. Due to equipment in the manufacture of conveyor belt causes the deviation, primarily through improved design, manufacture precision to prevent and reduce the occurrence of conveyor belt deviation.
2.2.2. For installation adjust improper and daily use causes deviation, mainly the following aspects should be considered:
Conveyor belt in drive roller or on rear rollers deviation, usually by adjusting the position of the roller bearing ways to eliminate, usually by adjusting the position of the roller bearing ways to eliminate.
A. The longitudinal centerline of the roller rotation axis and conveyor is not perpendicular, resulting in the conveyor belt one side loose and the other tight, belt move from the tight side to the loose side, Occurs deviation phenomenon. Should be adjusted bearing position of the tighten deviation side. Make horizontal pull of belt equal, eliminate deviation. When tail roller is spiral tensioning, the reasons of tail deviation may be due to the top tight power of tensioning device both sides screw rod are not equal, resulting in caused by imbalance.
B. Cylinder axis is not horizontal, at both ends bearing of the height difference is cause another reason of head or tail deviation. At this point, at both ends roller bearing should add and subtract shims way to leveling roller axis ,to eliminate conveyor belt deviation.
C. Roller surface adhesion material, equivalent to increasing the roller local rdiameter, will cause the conveyor belt deviation, should strengthen empty segment cleaning of conveyor belt to reduce the adhesive material or dust accumulation on the conveyor belt. In addition, the conveyor belt between the nose and tail parts deviation, called central or local deviation. Such deviation reasons is more complex, it is with the conveyor belt along device exposure to a relationship. Need a detailed analysis for specific issues. Using the following methods can resolve these issues.
a. Load or no-load branch roller axis with the conveyor belt running centerline is not perpendicular, causing tape at the roller deviation. Deviation ends should adjustment to the conveyor belt running direction. At this time often need to adjust the adjacent groups of rollers in order to achieve the purpose of eliminating deviation, adjusting deviation angle should not be too big.
b. Conveyor belt joint with the tape centerline (trumpet) is not perpendicular, to cause the deviation, Should improved installation connection accuracy to eliminate deviation.
c. If material loaded on the conveyor belt is straight; make the material block and weight distribution along bandwidth direction distribution serious inequality, cause deviation, through adjustment blanking tube and skirt plate location method to be eliminated.
D. Recently, it was suggested that the method of application film for transfer partial conveyor belt, because of high manufacturing costs and some technical problems not well solved, makes this method very difficult to promote the use.
3. The typical failure of roller:
3.1. Operation is not flexible
Each belt conveyor have lot number rollers, installation shown in Picture 1, their work status directly affects the conveyor is working. According to the actual work of conveyor, roller in the conveyor system can be classified four kinds according their efect, trough roller, parallel roller, buffer roller and self-aligning roller; according to the loads case can be divided two kinds, no-load roller and bearing roller. Trough roller use bearing branches of materials, play a supporting role and increased throughput role.
Parallel roller is a long-shaped roller, for no-load branch of conveyor, to play a supporting role of no-load branch tape; buffer roller is trough roller too. Flexible support trough roller be installed on conveyor load branch, Installed in the material office. Reduce the impact of material for conveyor belt, protect the tape and support bearing. Generally based on the elastic support were divided into rubber ring and spring plate; the role of self-aligning roller is a certain degree of automatic adjustment of conveyor belt deviation, To avoid excessive wear of belt and materials scattered. In the load and no-load branch are equipped with a number of self-aligning roller. The self-aligning principle shown in Fig. 2.
Manufacture installation quality of roller directly affect the life and running resistance of conveyor belt. roller repair and replacement costs are also an important part of conveyor belt operating expenses. The roller operation quality for conveyor of the running resistance, power consumption, roller and belt life, maintenance workload and cost of transportation has a significant impact. Therefore, analysis method to extend the service life of rollers, also an important contents to ensure stable operation of belt conveyor, practical significance in engineering. Trough roller of belt conveyor systems used on material bearing branch, play supporting role and increased throughput role. Parallel roller is a long-shaped roller, for no-load branch of conveyor, to play a supporting role of no-load branch tape; buffer roller is trough roller too. Flexible support trough roller be installed on conveyor load branch, Installed in the material office. Reduce the impact of material for conveyor belt, protect the tape and support bearing. The role of self-aligning roller is a certain degree of automatic adjustment of conveyor belt deviation, To avoid excessive wear of belt and materials scattered. In the load and no-load branch are equipped with a number of self-aligning roller. If roller appear rotating not flexible or not turning phenomenon.The drag coefficient of roller operation by rolling into a slide,
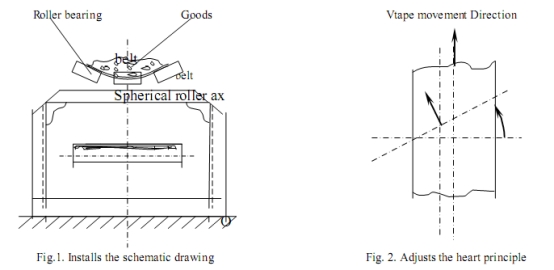
value was ten times to increase. The results will result in increased running resistance of belt conveyors, electric power consumption increases. As the roller rotation is not flexible, the friction between roller and conveyor belt by rolling friction into sliding friction, make the friction increase between the two, shorten the equipment life . Therefore, we must often replace a large number of idlers, conveyor belt, resulting in increased equipment maintenance, operating costs increased.
Many factors for affect the flexibility of running rollers and life span, summarized in the following areas:
a. Manufacturing quality of roller
Roller manufacturing problems mainly in the bearing stiffness is not enough, it is difficult to ensure
precision of roller assembly, thereby constraining the flexibility of running roller.
b. Sealed lubrication and the use of maintenance
Main factors of affect roller rotation not flexible include sealing and bearing lubrication problem. As the work environment of belt is more severe. Generally speaking, the dust are great on used site. The seal form of bearing have a great influence on the running flexibility for rollers. If sealed not well, Dirt is easy into bearing to cause the roller rotation is not flexible, In addition, bearing grease if using the general calcium base grease is easy to change color to dry, can not play a very good lubricant role.
3.2. Solutions
a. In the roller manufacturing processes guarantee the accuracy requirements, For example, pressing bearing bore to achieve three precision, tube at both ends of dimensional tolerances, concentricity and ovality must meet national standards. The products have strict quality inspection to ensure that all
products qualified.
b. Sealed lubrication, in addition to manufacturing quality assurance, go with good lubricating materials, such as use of lithium-based grease, can improve the lubrication of bearings which extend the life of the roller is necessary.
c. Bearing used to ball bearings support, plastic sealing ring labyrinth seal structure, this can ensure roller worked reasonable force, While ensuring dust effect good, resistance small, easy assembly and disassembly, easy to maintain, reduce conveyor operating costs.
4. Conclusion:
Wide range applications of belt conveyors, and the work environment is generally more difficult, to keep equipment running in good working condition, extend equipment life, improve the quality of operation, reduce operating costs has been the goal of engineering and technical personnel. Analyze and resolve the impact normal operation of the main problems, to ensure the good functioning of device, it is an important work of equipment maintenance. This paper analyzes the proposed method. Helpful improve site maintenance staff levels to solve practical problems, for practical project has important significance.