摘 要
本论文针对一款采用ABS塑料制造的薄壁塑件进行了详细的滑塞注射模具设计。首先,对塑件进行了深入分析,明确了其设计要求,包括尺寸精度等级、塑料材质以及壁厚特征。通过计算得出塑件体积为1.01cm³,质量为1.08g,同时详细阐述了ABS塑料的优异综合性能,如良好的成型工艺、韧性、化学稳定性、耐热性以及吸湿性等。
在型腔总体布置与分型面选择方面,考虑到塑件侧壁具有通孔和台阶结构,设计采用了包含侧向分型抽芯机构的一模四腔方案,以简化模具结构。型腔采用交叉排列形式,旨在实现浇注系统的平衡、模具尺寸紧凑、对称布局及防止偏载导致的溢料问题。分型面设计遵循便于塑件与浇注系统凝料取出的原则。
针对注射机的选用,结合制件与浇注系统的质量和模具结构特点,选择了适宜的注射设备。浇注系统设计中,详细规划了主流道、浇口套、冷料穴、分流道、进料口等组件,确保熔融塑料的有效填充与压力传递。此外,还对成型零部件的结构设计、工作尺寸计算、型腔壁厚与底板厚度计算进行了详尽探讨。
论文进一步阐述了排气结构设计、冷却系统设计以及侧向分型与抽芯机构的设计,包括斜销侧向分型与抽芯机构和弹簧侧向分型抽芯机构的具体参数确定与设计要点。注射模的导向及脱模机构设计亦得到了充分关注,涵盖了导向机构(导柱、导向孔数量与布置)与脱模机构(分类、设计原则、脱模力计算及推出零件尺寸确定)的设计细节。
最后,论文讨论了注射机与注射模具之间的关系,对注射量、锁模力、模具安装尺寸(高度、长度与宽度)、开模行程及顶出装置进行了校核,确保模具与设备的匹配性与生产过程的顺利进行。
关键词:滑塞注射模具、ABS塑料、塑件分析、型腔布置、注射机
ABSTRACT
This paper designs the sliding plug injection mold for a thin-wall plastic piece made of ABS plastic. First of all, the plastic parts are analyzed in depth, and the design requirements are clarified, including the size precision grade, plastic material and wall thickness characteristics. Through calculation, the volume of the plastic parts is 1.01cm³ and the mass is 1.08g. Meanwhile, the excellent comprehensive performance of ABS plastic is elaborated, such as good forming process, toughness, chemical stability, heat resistance and moisture absorption, etc.
In terms of the general layout of the type cavity and the selection of the classification surface, considering that the side wall of the plastic parts has the through-hole and step structure, the one-mode and four-cavity scheme including the lateral type core extraction mechanism is adopted to simplify the mold structure. The cavity is arranged to realize the balance of the pouring system, compact mold size, symmetrical layout and prevent the overflow problem caused by partial load. The design of classification surface follows the principle of facilitating the removal of plastic parts and pouring system.
According to the selection of injection machine, combined with the quality of the parts and casting system and the characteristics of the mold structure, the appropriate injection equipment is selected. In the design of the pouring system, the main channel, pouring gate sleeve, cold material hole, shunt channel, feed inlet and other components are planned in detail to ensure the effective filling and pressure transfer of molten plastic. In addition, the structure design, working size calculation, cavity wall thickness and floor thickness calculation of the forming components are discussed in detail.
The paper further expounds the design of exhaust structure, cooling system and the design of lateral type and core pumping mechanism, including the specific parameter determination and design points of inclined pin and spring lateral type core pumping mechanism. The design of the guide and release mechanism of the injection mold has also received full attention, covering the design details of the guide mechanism (guide columns, number and layout of the guide holes) and the release mechanism (classification, design principles, calculation of the release force and the size determination of the introduced parts).
Finally, the paper discusses the relationship between the injection machine and the injection mold, and checks the injection volume, mold locking force, mold installation size (height, length and width), mold opening stroke and jacking device to ensure the matching between the mold and the equipment and the smooth production process.
Key words: sliding plug injection mold, ABS plastic, plastic parts analysis, type cavity arrangement, injector
目 录
1 塑件分析……………………………………………………………1
1.1 明确塑件的设计要求………………………………………………1
1.2 计算塑件的体积和质量……………………………………………1
1.3 明确塑料的特性……………………………………………………1
2 型腔总体布置与分型面的选择……………………………………1
2.1 型腔数目的确定……………………………………………………1
2.2 多型腔的排列………………………………………………………2
2.3 分型面的设计………………………………………………………2
3 注射机的选用………………………………………………………3
4 浇注系统的设计……………………………………………………3
4.1主流道的设计……………………………………………………4
4.1.1主流道尺寸………………………………………………………4
4.1.2浇口套的固定……………………………………………………5
4.1.3冷料穴的设计……………………………………………………5
4.2分流道的设计………………………………………………………5
4.2.1分流道的截面形状………………………………………………6
4.2.2 分流道的尺寸……………………………………………………6
4.3 进料口的设计…………… …………………………………………7
5 成型零部件的设计………………………………………………8
5.1成型零部件的结构设计………………………………………8
5.1.1 凹模(下型腔板)………………………………………………8
5.1.2 凸模(上型腔板)………………………………………………9
5.2 成型零部件的工作尺寸计算………… ……………………………9
5.2.1 塑件尺寸精度的影响因素………………………………………9
5.2.2 成型零部件的工作尺寸计算…………………………………10
5.3 成型型腔壁厚和底板厚度的计算………………………………13
5.3.1 成型型腔壁厚的计算…………………………………………13
5.3.2 型腔底板厚度计算……………………………………………14
6 排气结构设计………………………………………………………14
7 冷却系统的设计……………………………………………………14
7.1 冷却系统的设计原则……………………………………………15
7.2 模具温度对塑件的质量影响 ……………………………………15
7.3 温度调节对生产效率的影响 ……………………………………15
7.4 冷却管道的工艺计算 ……………………………………………15
8 侧向分型与抽芯机构的设计 ……………………………………16
8.1 斜销侧向分型与抽芯机构的设计 ………………………………16
8.1.1 斜销侧向分型与抽芯机构主要参数的确定 …………………17
8.1.2 斜销侧向分型与抽芯机构的设计要点 ………………………18
8.2 弹簧侧向分型抽芯机构…………………………………………19
9 注射模的导向及脱模机构设计 …………………………………19
9.1 导向机构设计……………………………………………………19
9.1.1 导柱……………………………………………………………19
9.1.2 导向孔…………………………………………………………20
9.1.3 导柱的数量和布置 ……………………………………………20
9.2 脱模机构设计……………………………………………………20
9.2.1 脱模机构的分类及设计原则…………………………………20
9.2.2 脱模力的计算及推出零件尺寸确定…………………………20
10 注射机与注射模具的关系………………………………………23
10.1 注射量的校核……………………………………………………23
10.2 锁模力的校核……………………………………………………23
10.3 模具安装部分的尺寸校核………………………………………24
10.3.1 模具高度………………………………………………………24
10.3.2 模具的长度与宽度……………………………………………24
10.4 开模行程的校核…………………………………………………24
10.5 顶出装置的校核…………………………………………………25
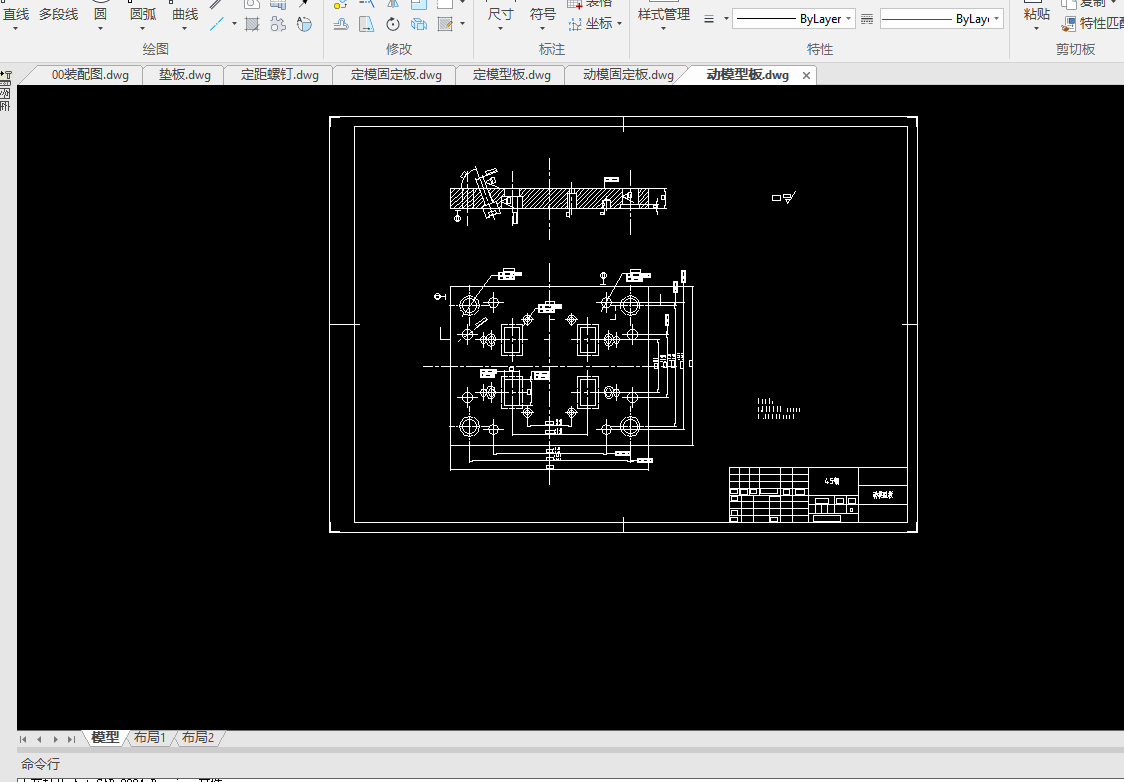
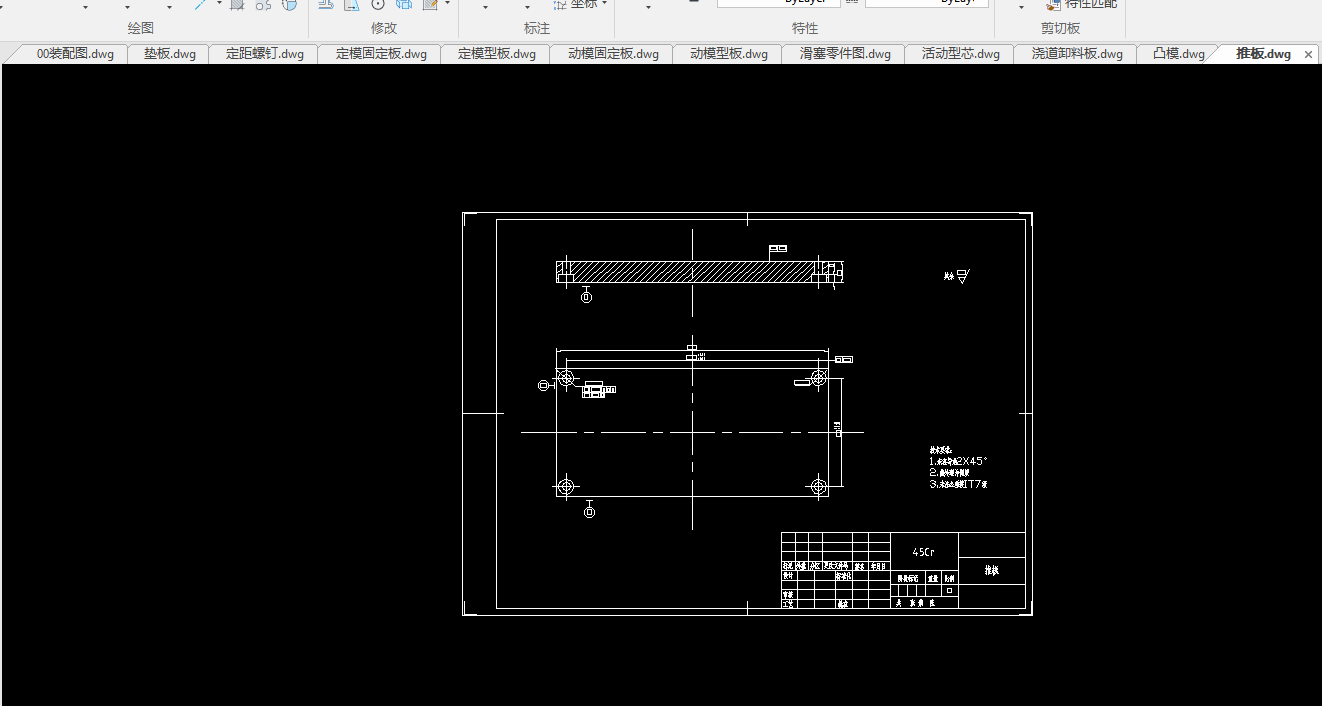
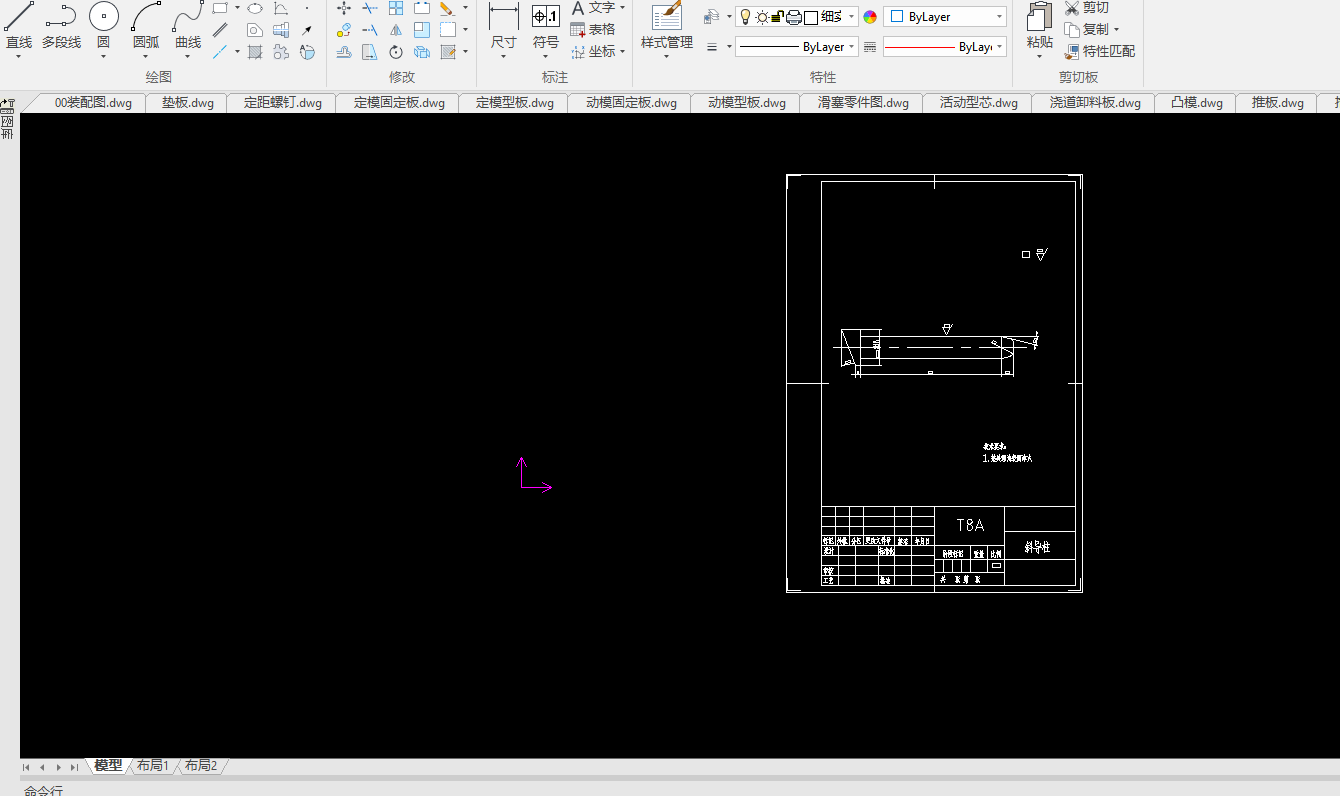
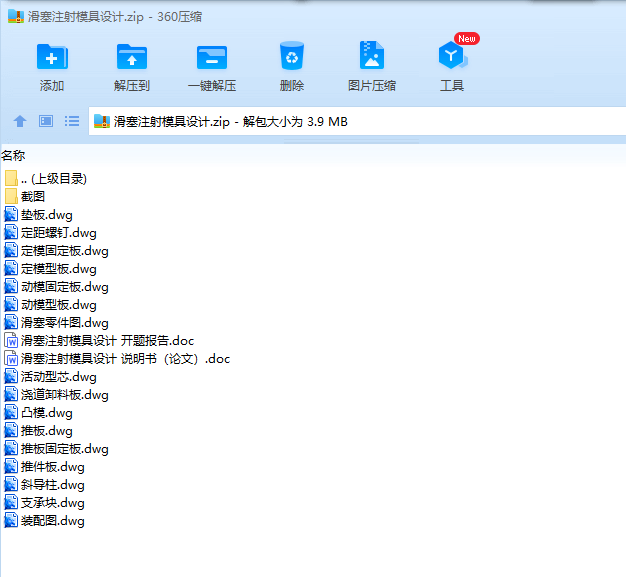
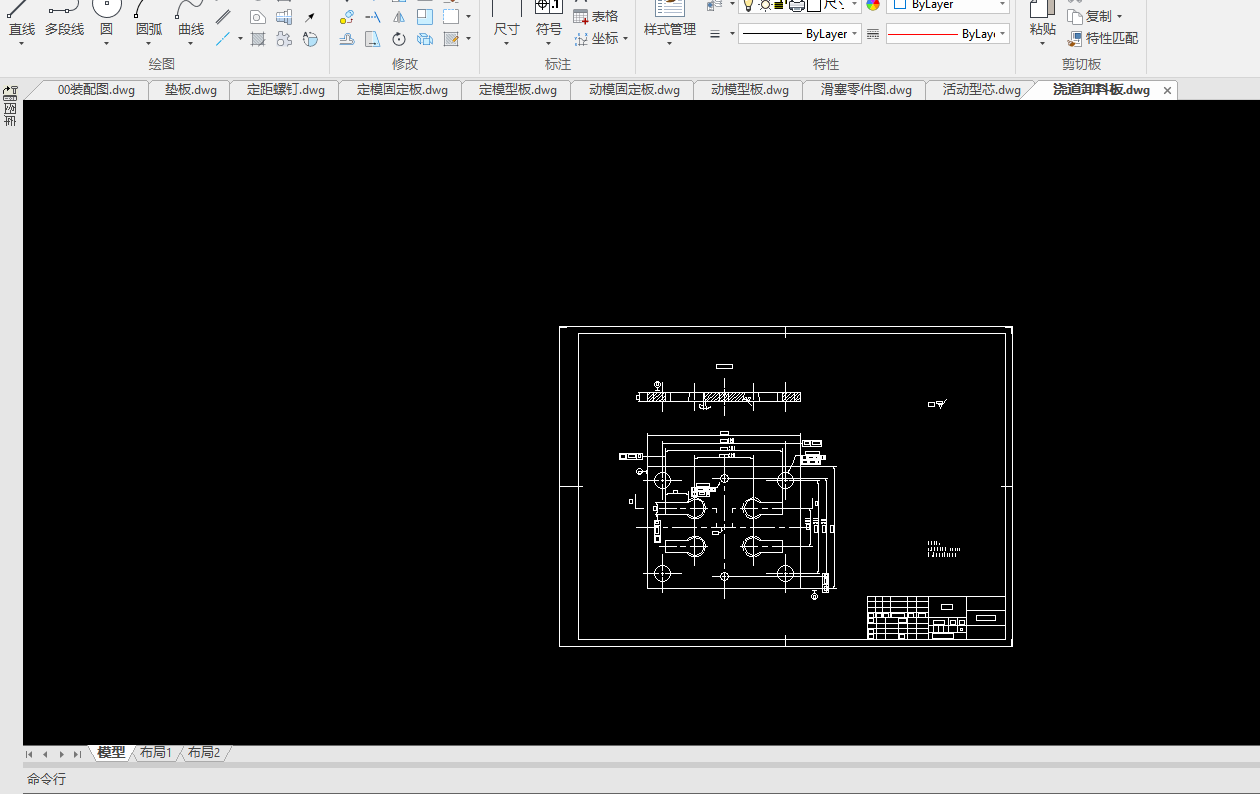
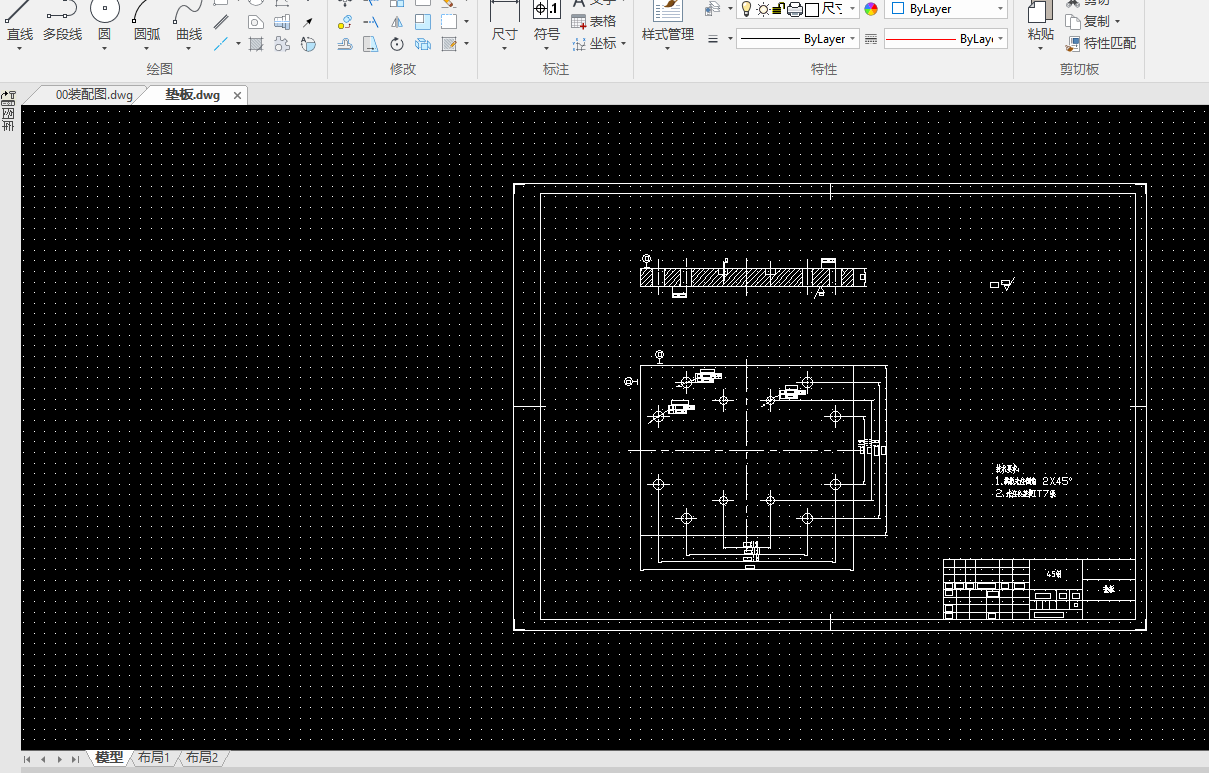
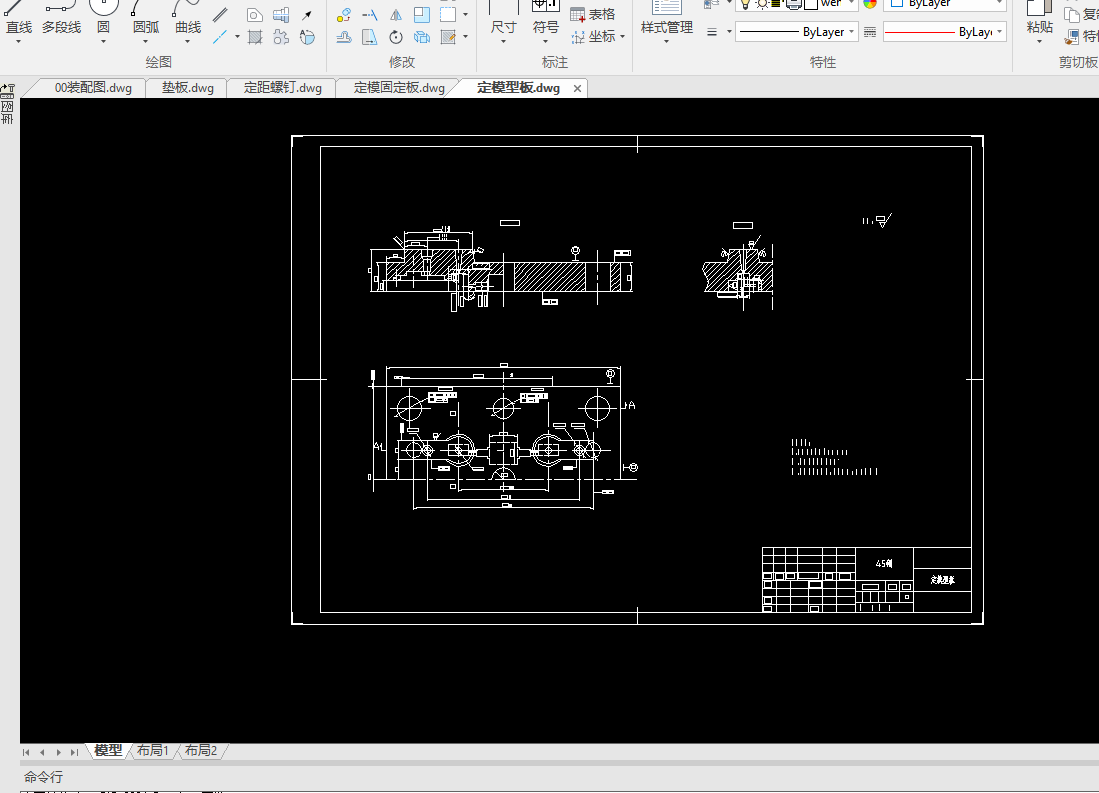
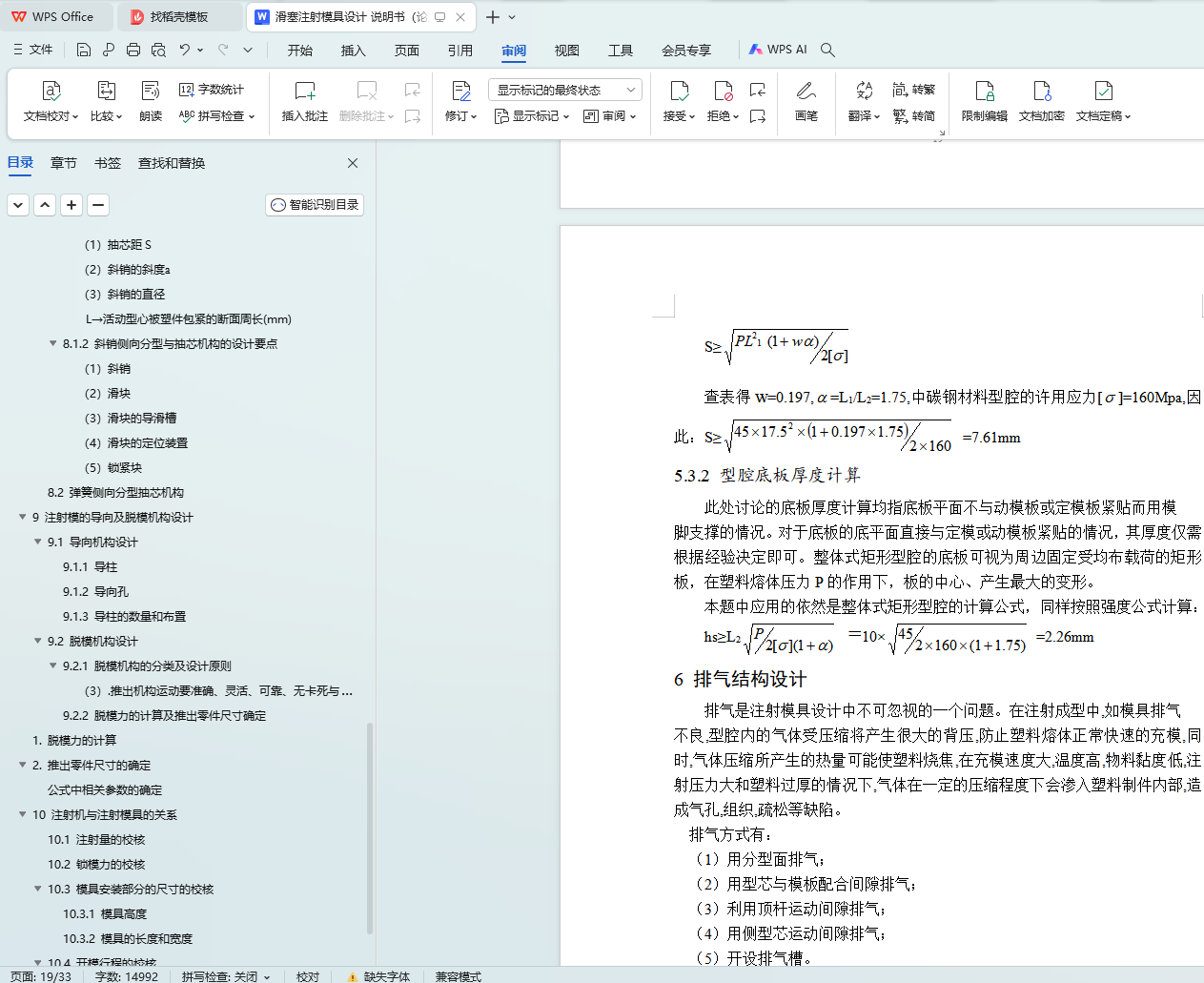
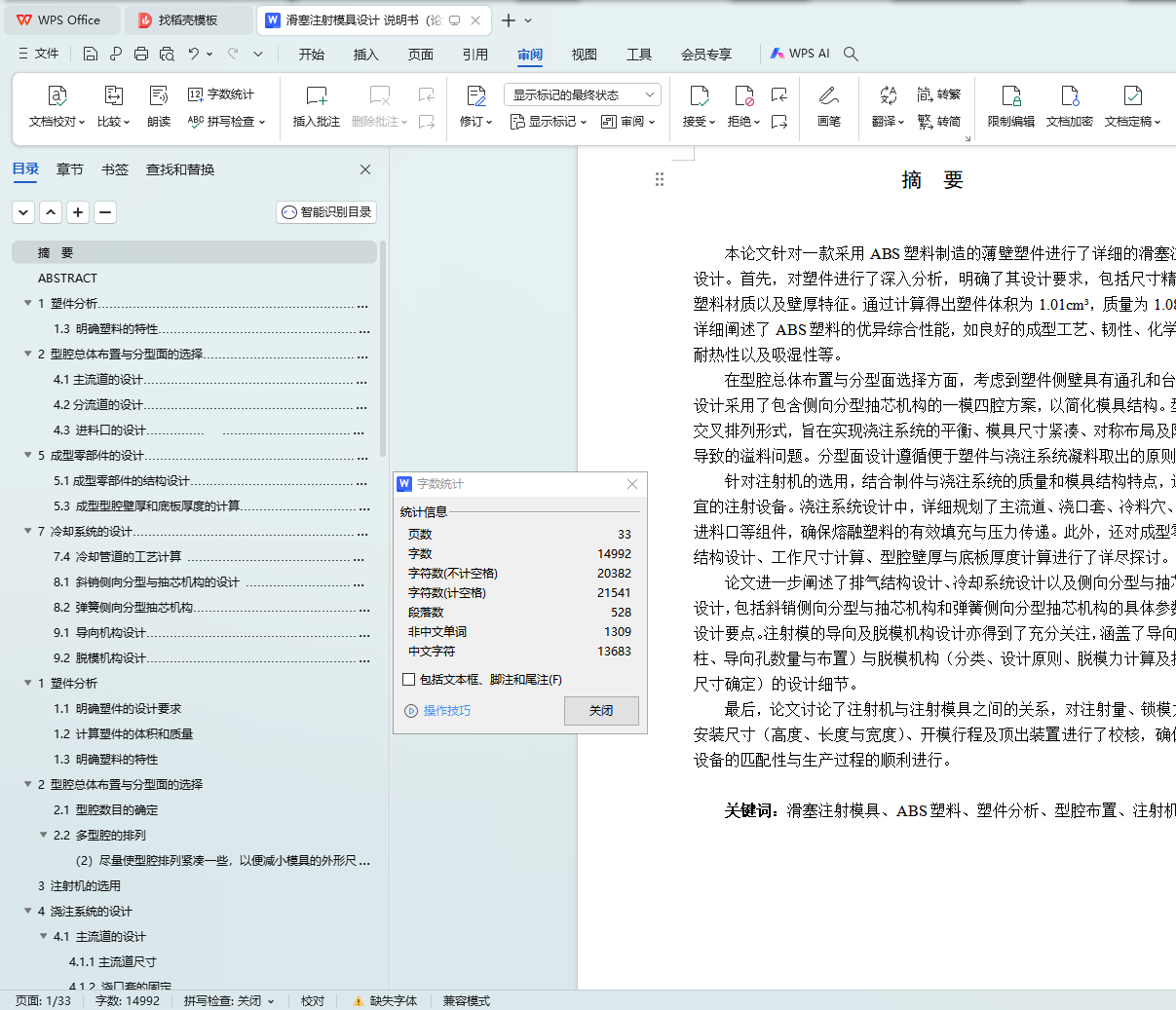
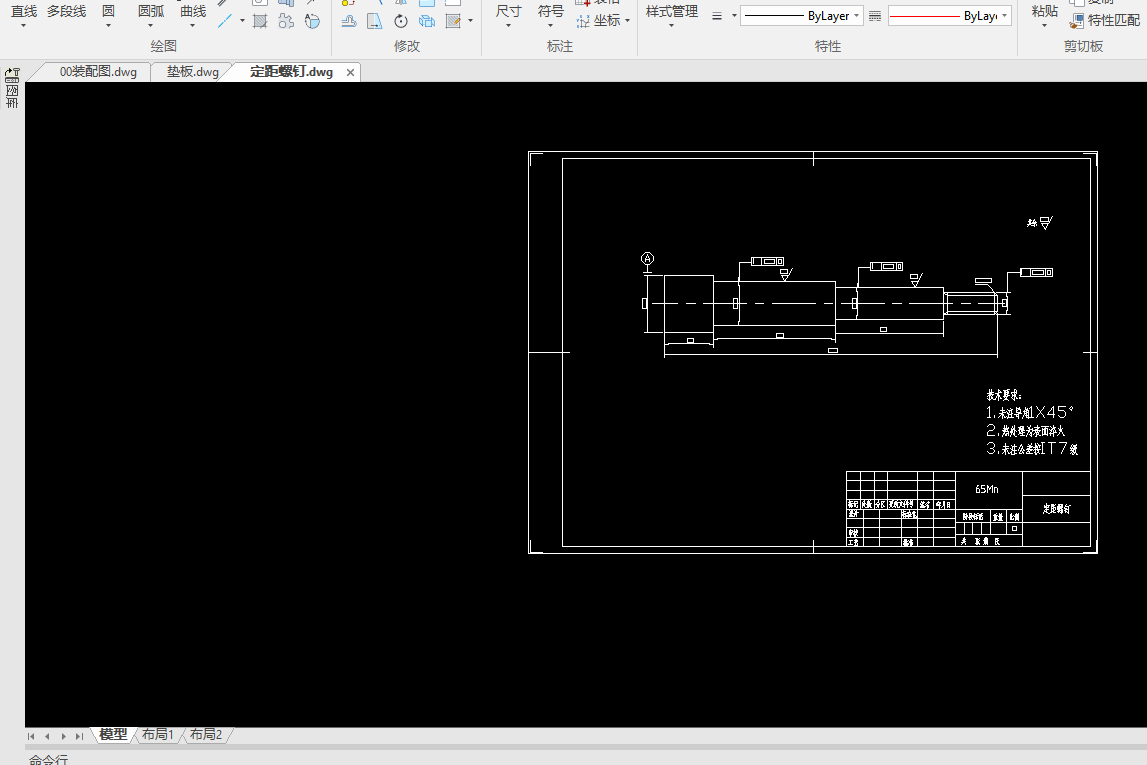

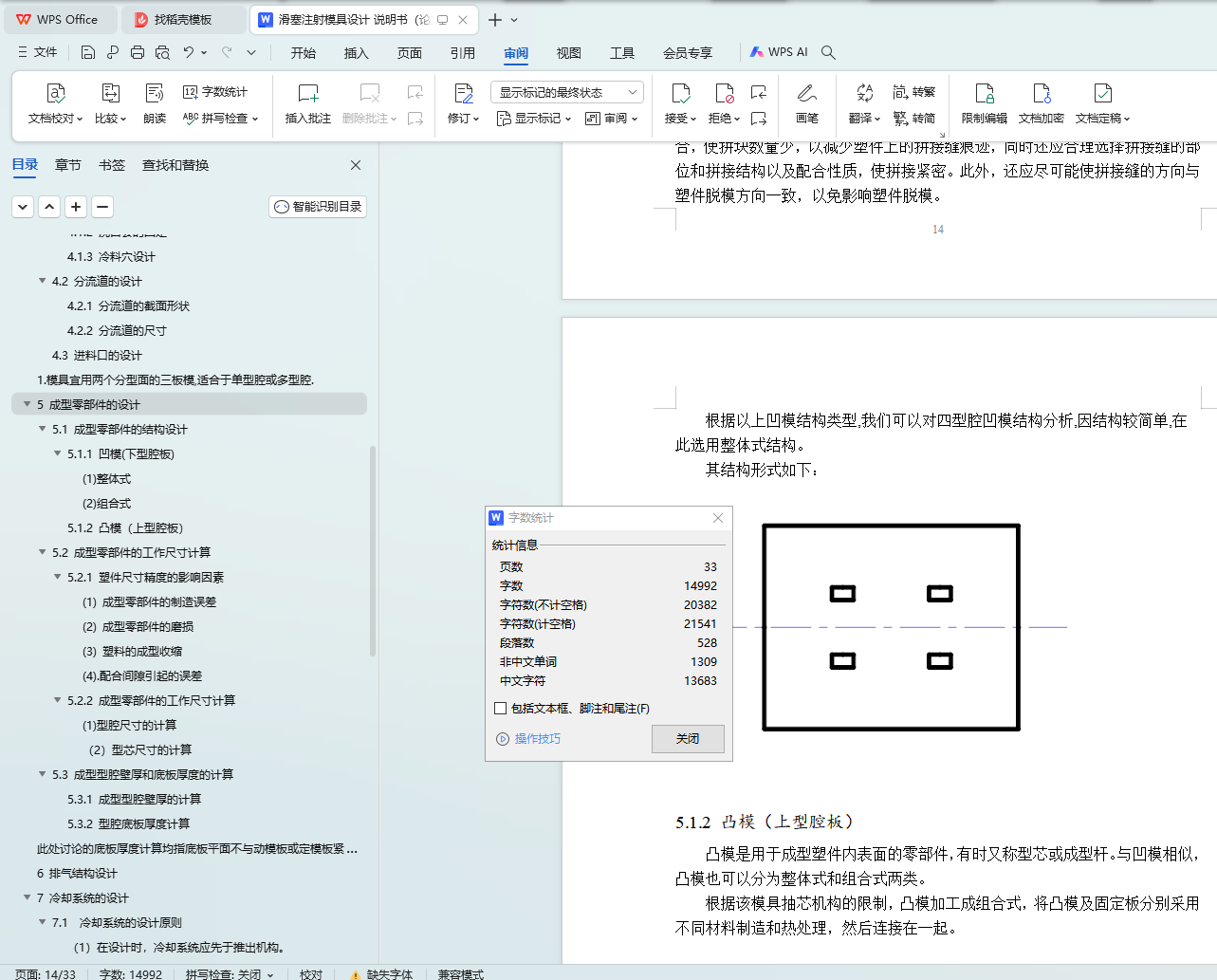
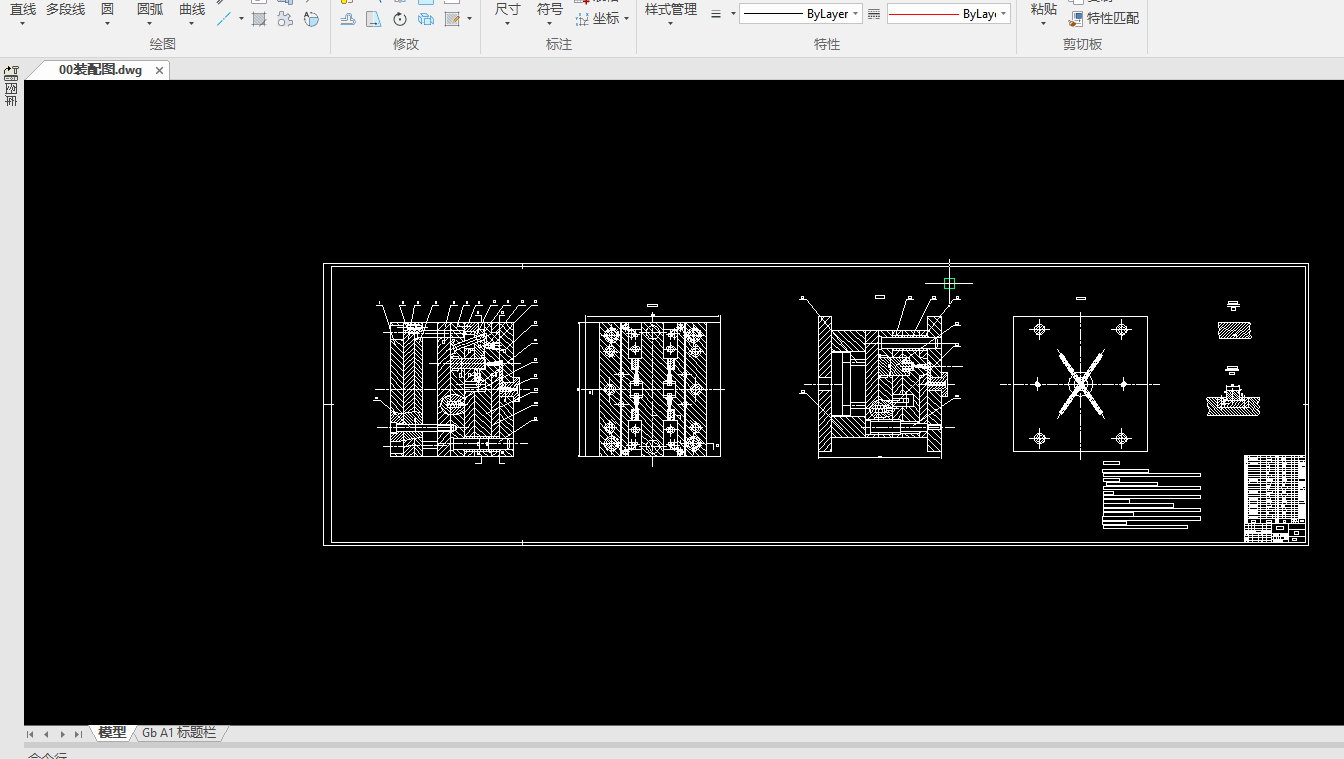
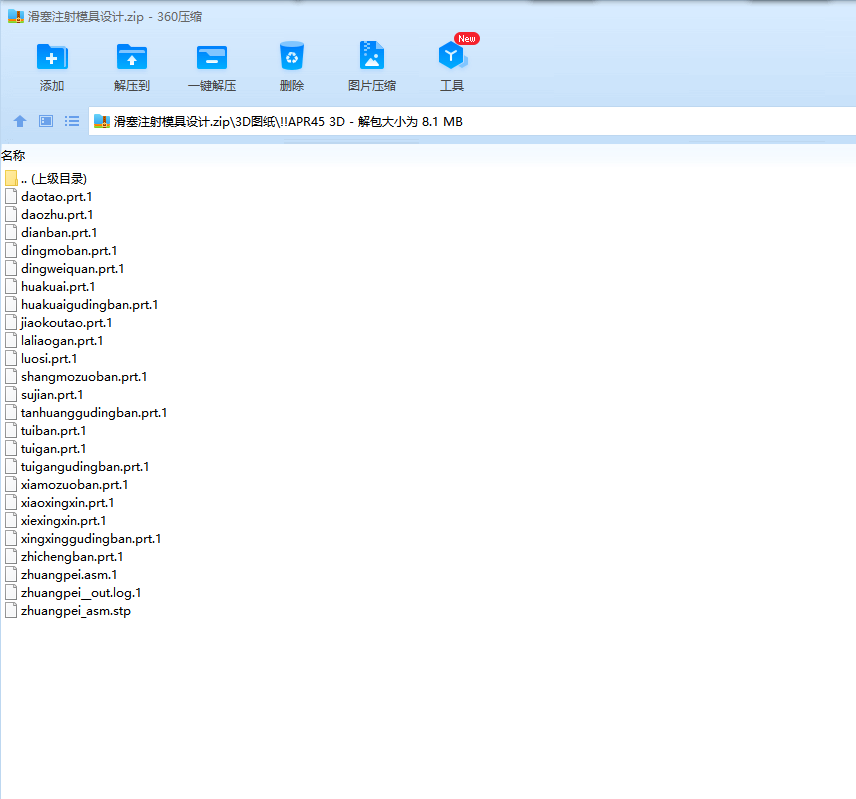
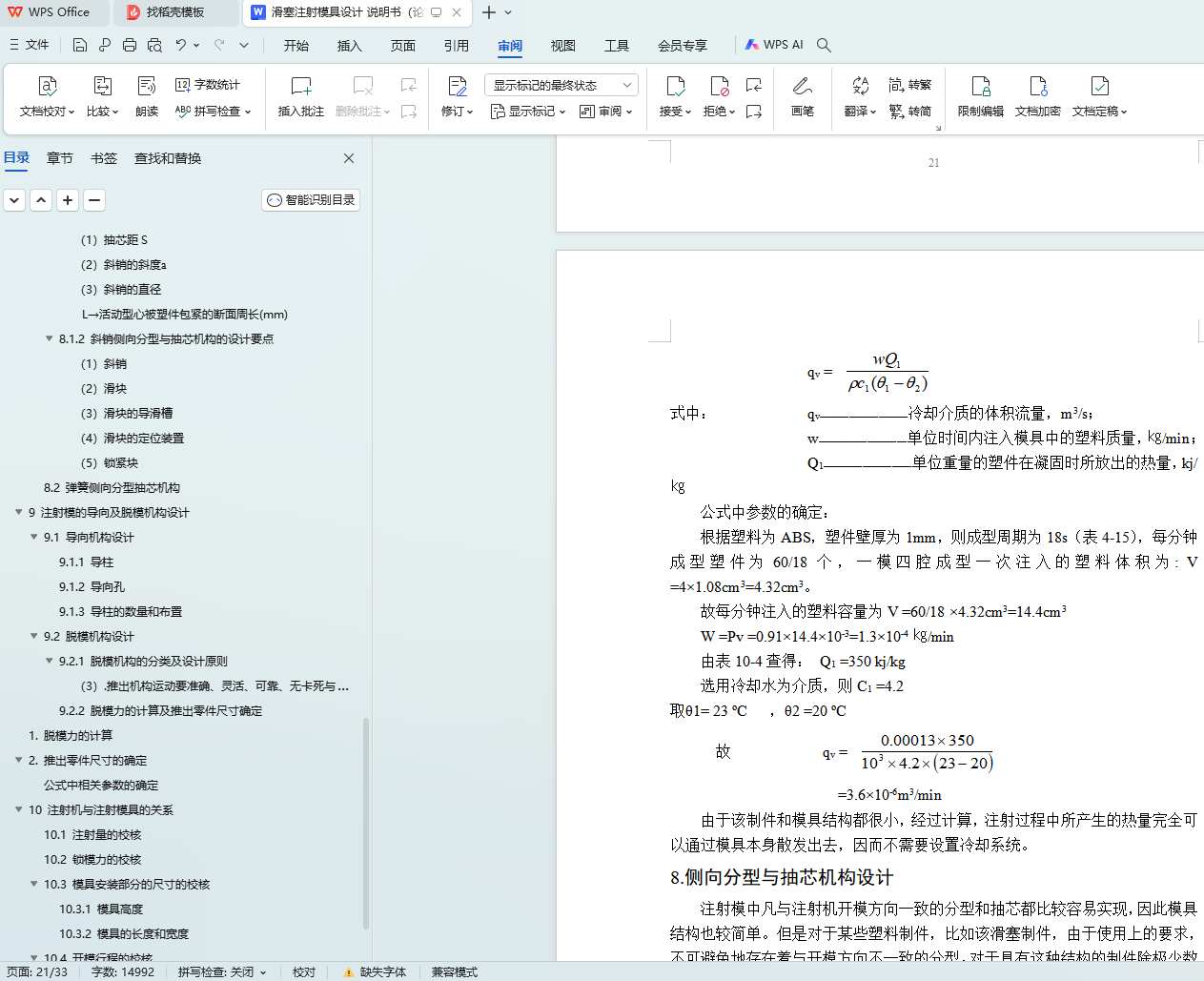
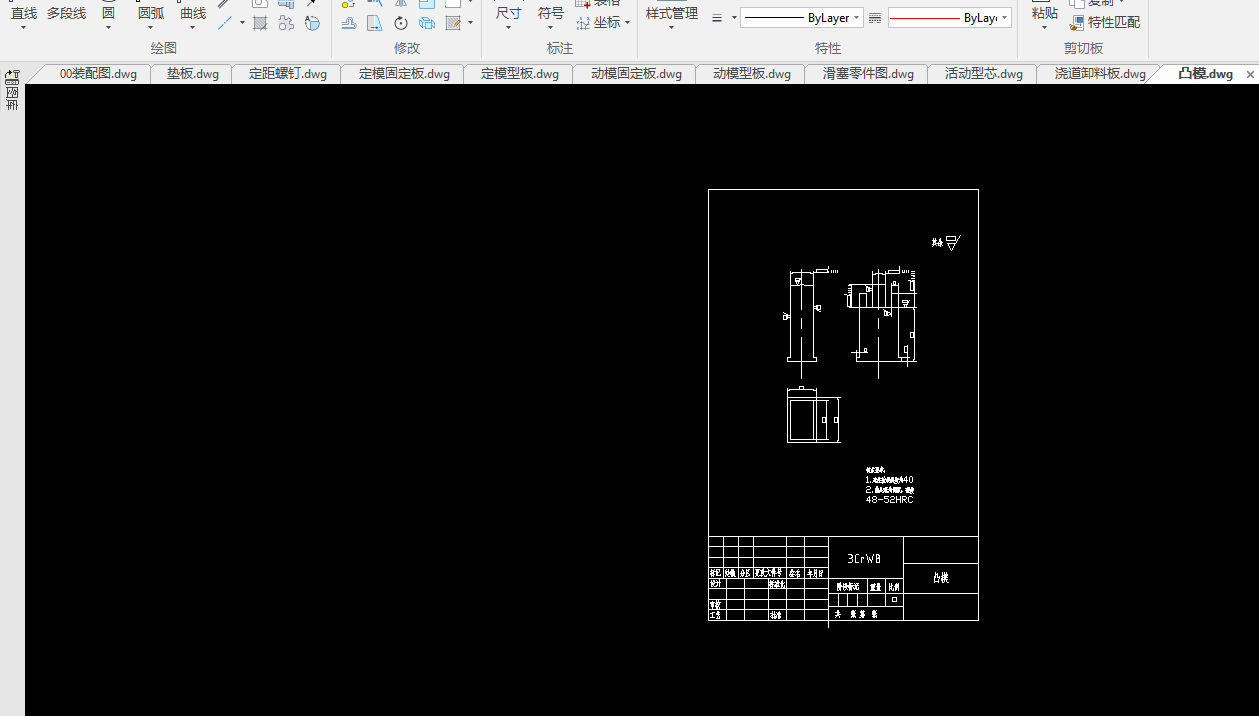
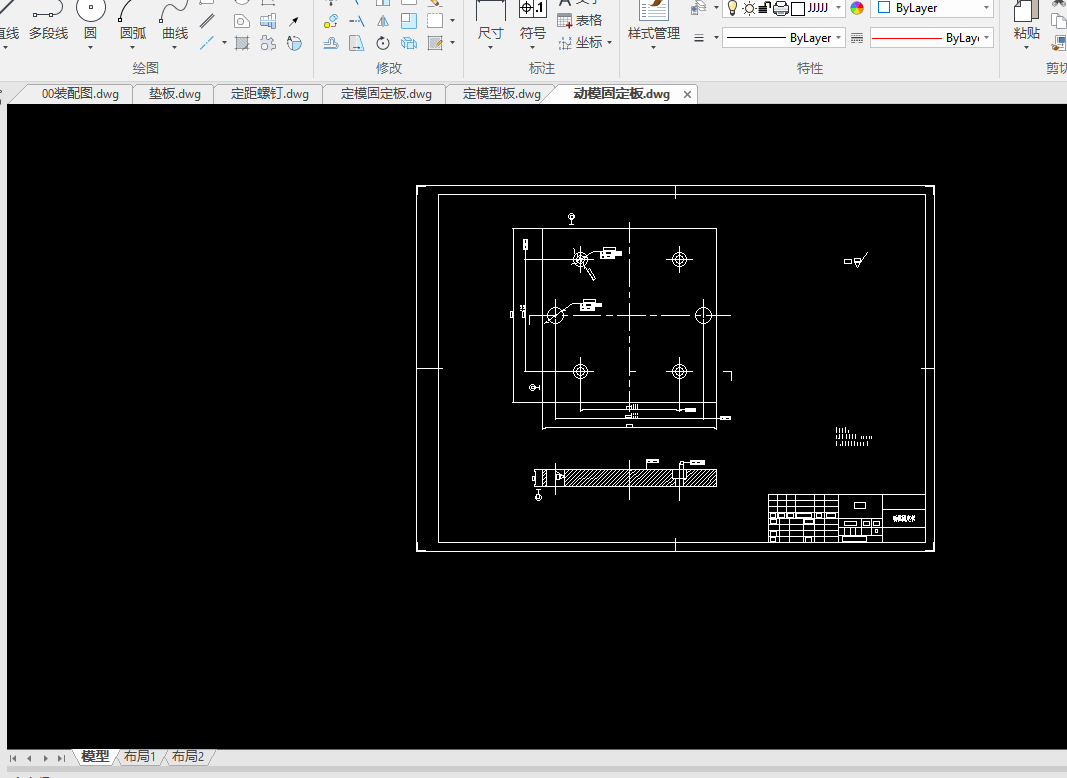
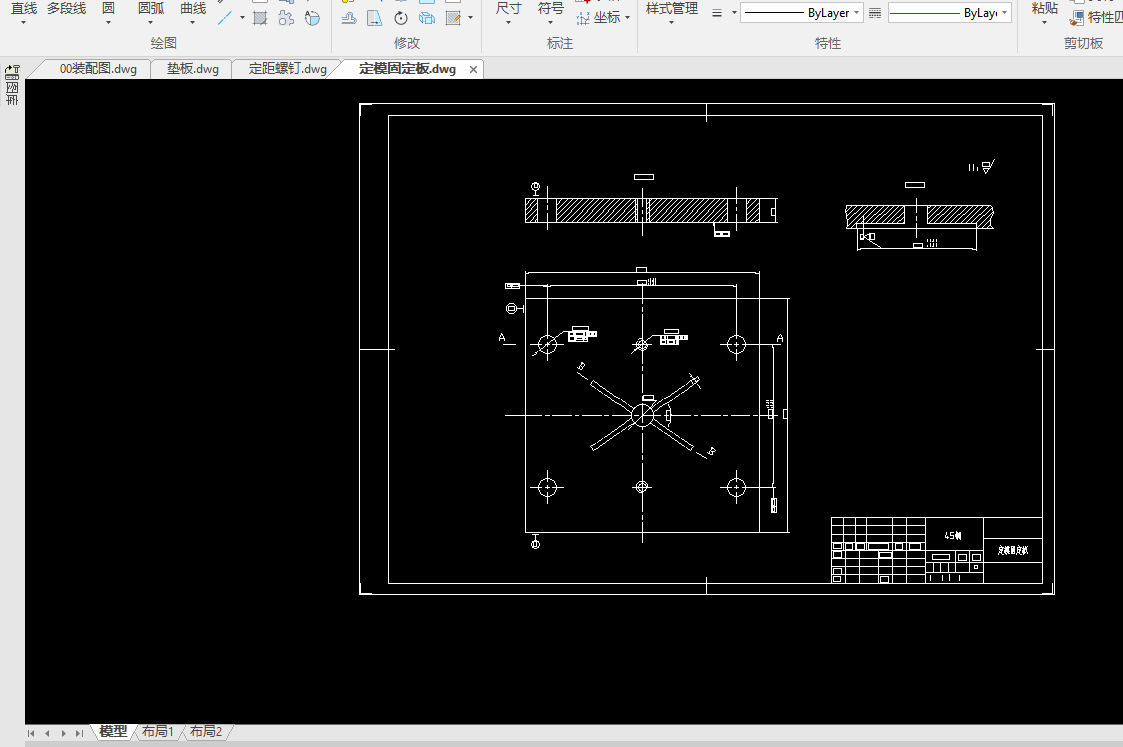
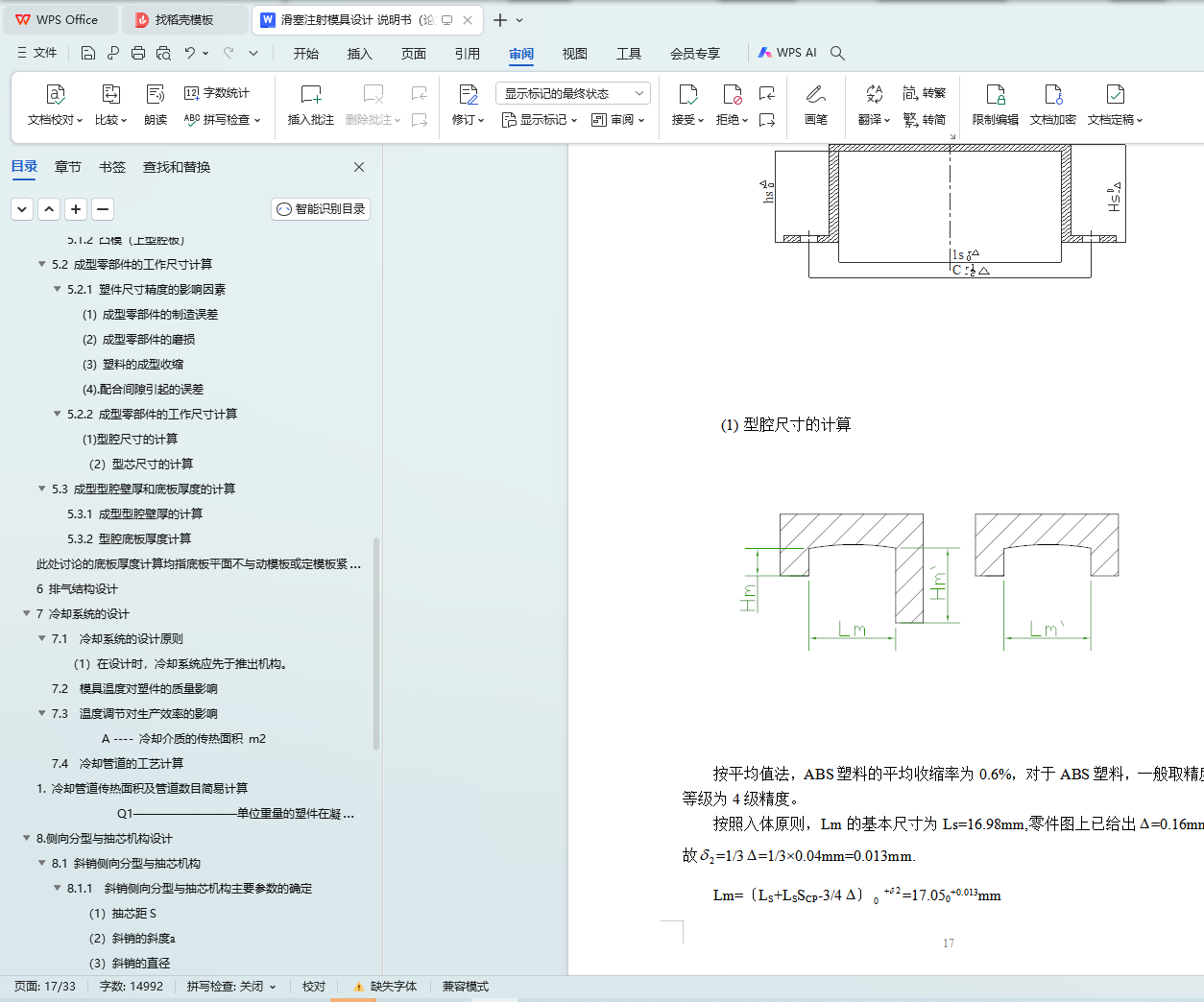
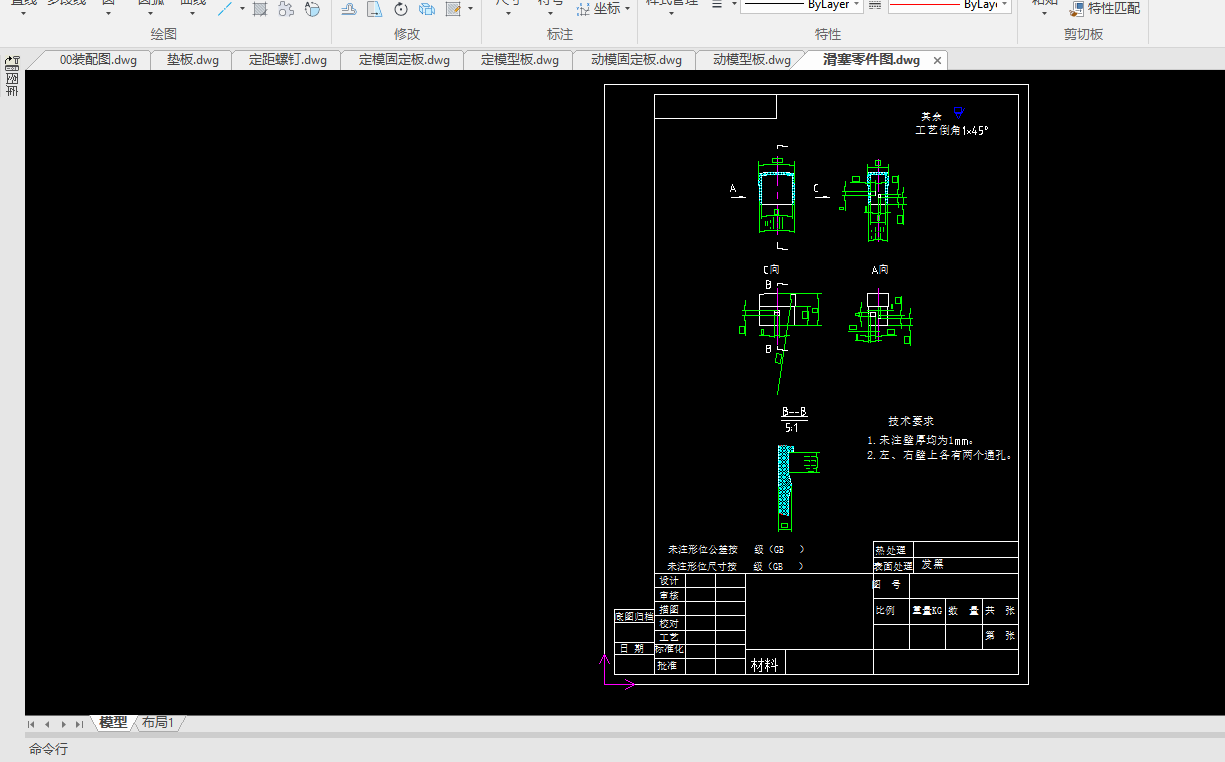
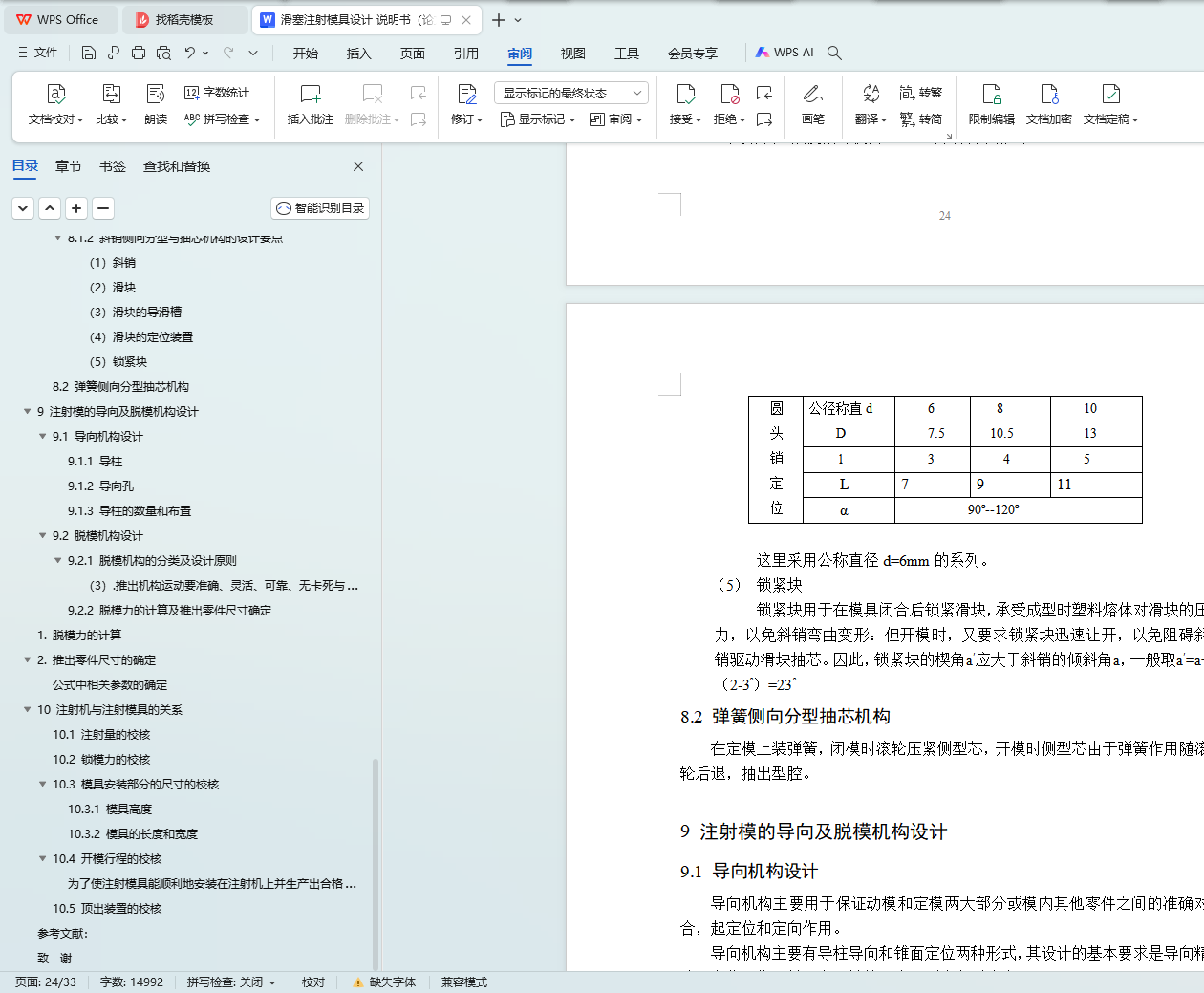
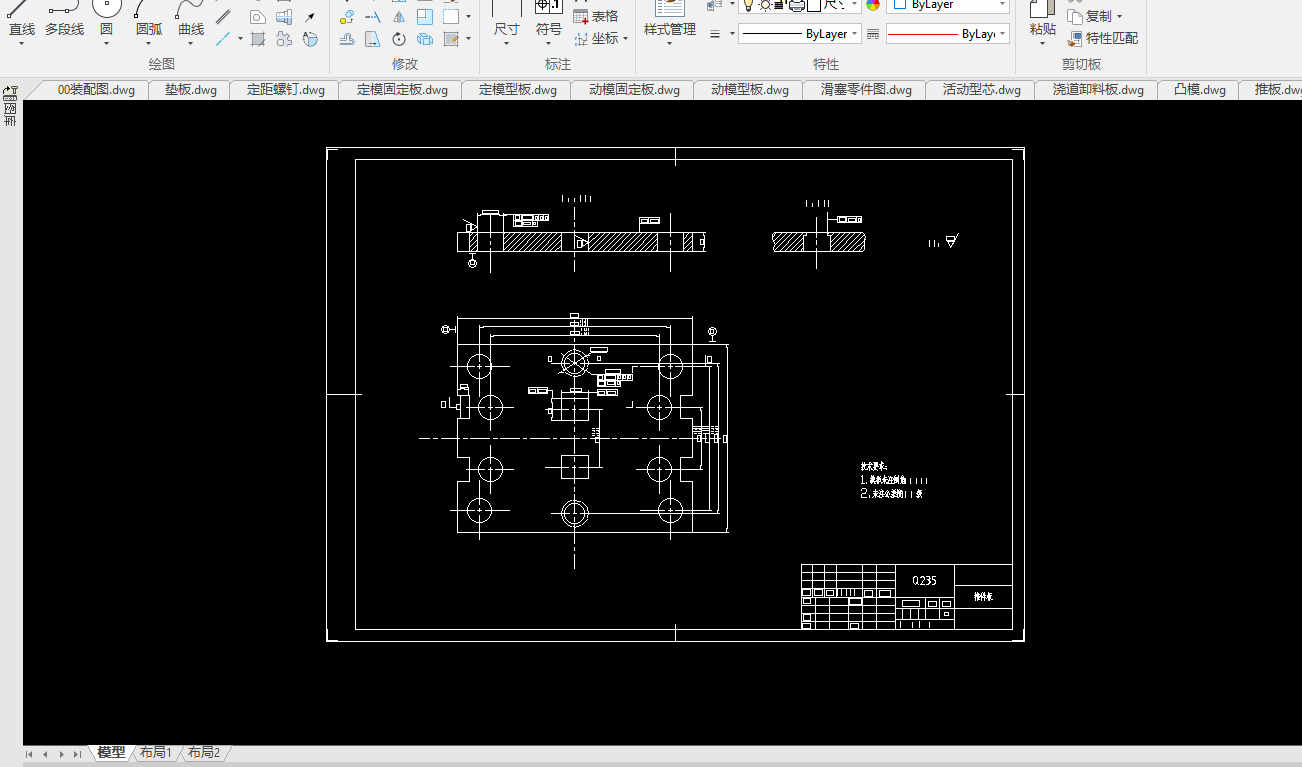
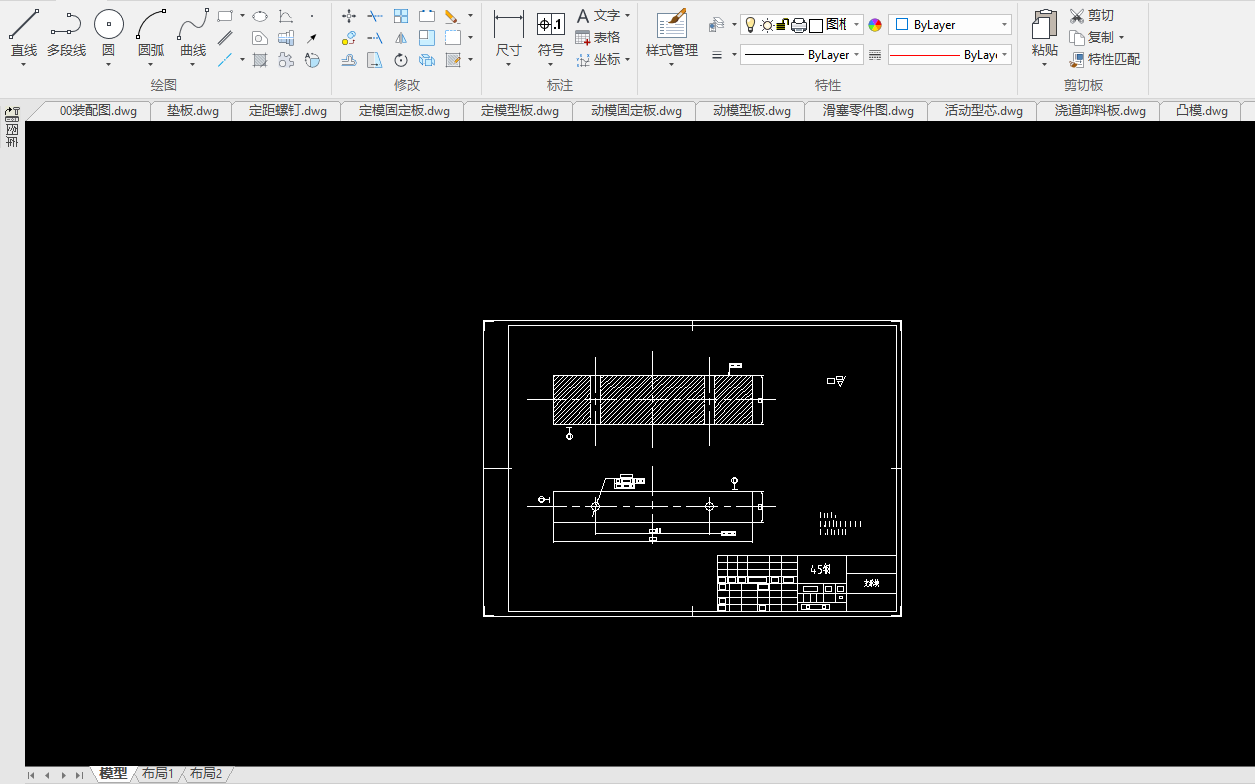
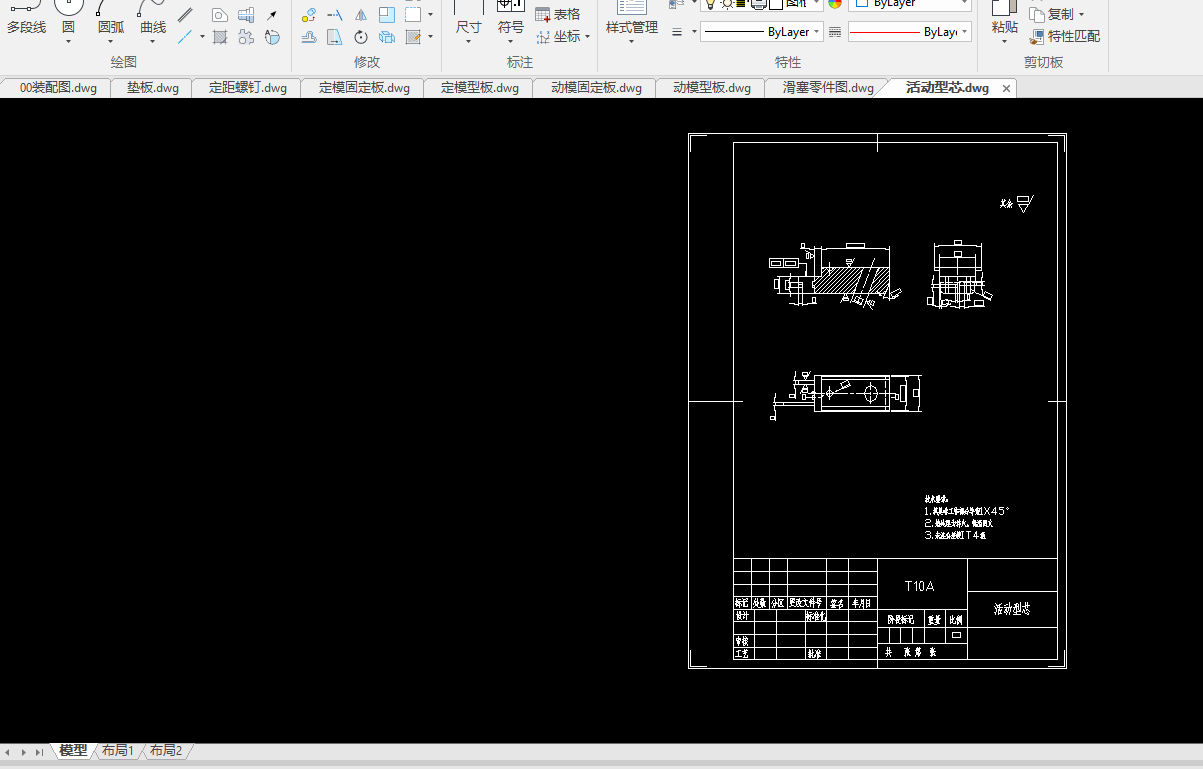