INTRODUCTION
In jacketed heating applications where processes require operating temperatures up to 350°F, steam and hot water serve as typical forms of heat transfer.
Currently, an increasing number of process engineers are switching from steam to hot water for heating jacketed reactors or vessels. There are several basic reasons for this trend:
· The temperature in the jacket can be controlled much more accurately with hot water than with steam. This higher degree of control protects against damage to or loss of product through overheating.
· Hot water ensures a better quality end product. This is particularly important in processes requiring very precise product temperature control.
· Hot water distributes heat more evenly than steam. This eliminates hot spots which often cause product to bake onto the walls of the vessel, and at worst, ruin the entire batch.
· In critical processes utilizing glass-lined reactors, steam can shock and damage the lining. Hot water allows smooth transitions from heating to cooling with no thermal shock.
In addition, many are switching to direct steam injection (DSI) systems to create the hot water for several basic reasons:
· With an advanced-design steam injection hot water set, the temperature of the process can be adjusted at any predetermined rate on any desired time cycle.
· A steam injection hot water system can be programmed to heat, then cool a process by stopping the heating cycle, then introducing cooling or tempered water into the jacket at any desired rate and temperature.
· In this system the condensate leaves the loop through a back pressure relief valve at the lowest temperature after all the possible heat has been extracted. In a steam system, on the other hand, condensate at a much higher temperature is returned to the boiler in a condensate return line with its inherent heat losses.
In this article, we will take an in-depth look at the advantages and disadvantages of steam and hot water for jacketed heating, and compare indirect and direct steam injection systems for making hot water.
Then, we will review several specific applications now utilizing direct steam injection systems for jacketed heating.
夹套加热传热介质采用热水相对于蒸汽的优势
1998年6月4日菲利普J.萨特在休斯敦化学工程博览会
简介
在夹套加热的应用过程中要求的操作温度高达350°F,蒸汽和热水充当典型的高温传递形式。
当前,在夹套加热反应器或容器的传热介质采用中越来越多的过程工程师们从蒸汽转换到热水。有这一趋势的几个基本原因:
. 在夹套中的温度用热水比蒸汽更能加精确的控制。这更大程度的控制,能保护防备损毁或过热损失产品。
. 热水保证最终产品的质量更好。这个过程要求特别重要的是非常严格的产品的温度控制。
. 热水热量分配比蒸汽更均匀。这消除了经常导致产品回容器壁上,在最坏的情况下甚至毁坏整批的潜在危险。
. 在决定性的过程中利用供应搪玻璃反应釜。蒸汽产生冲击并损毁衬套,但热水可以从加热到冷却没有热量的冲击,平稳的过渡。
此外,许多转换到直接用蒸汽喷射装置系统产生热水的几个基本的原因:
. 具有先进的设计,蒸汽射入热水的装置在任何预定的速度、在所需的任何时间周期上调整该过程的温度。
. 蒸汽注射热水系统可在任何所需的速度和温度下用程序控制加热然后冷却的过程,停止加热的一个周期,然后引入冷却或回水进入夹套。
. 在这个系统中,冷凝回路通过后面的泄压阀在可能加热的最低温度引出。在蒸汽系统中,另一方面凝析物在更高温度时返回到锅炉,在冷凝物返回线中有固有的热量损失。
在本文中,我们将深入研究在带夹套加热中采用蒸汽与采用热水的优点和缺点,比较间接和直接产生热水的蒸汽喷射装置系统。然后,我们将回顾一些具体的应用。现在直接利用蒸汽喷射系统来夹套加热。
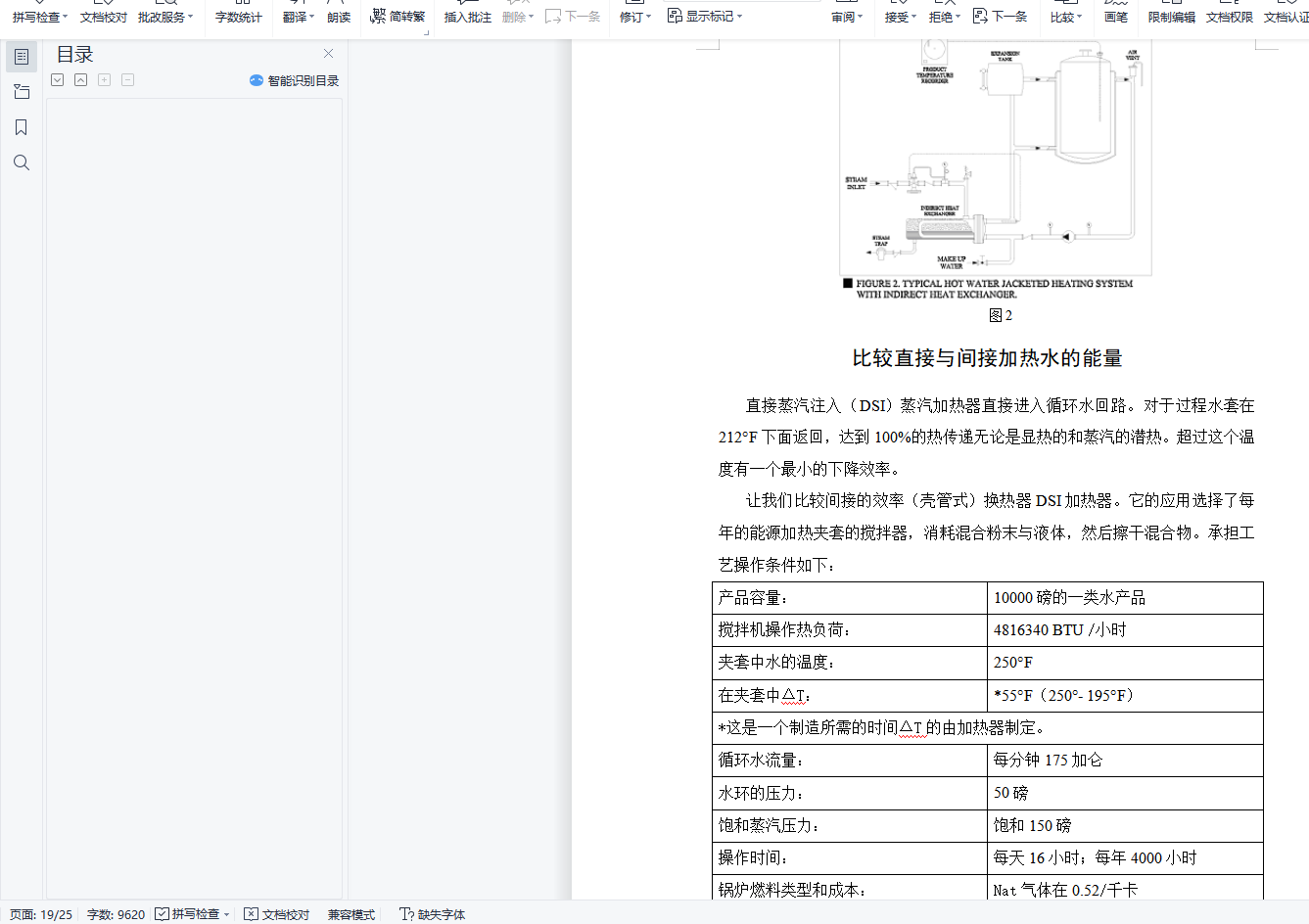
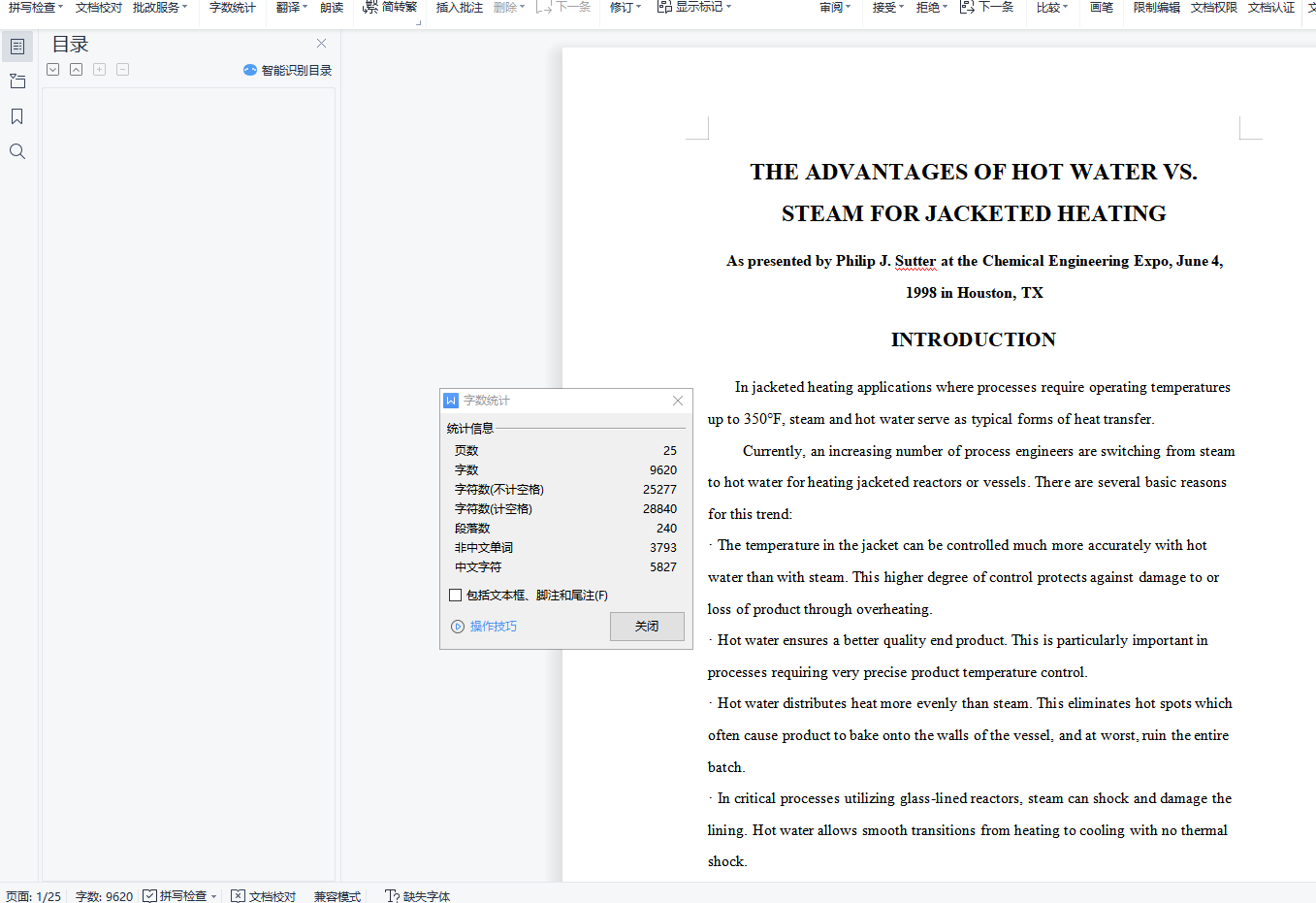
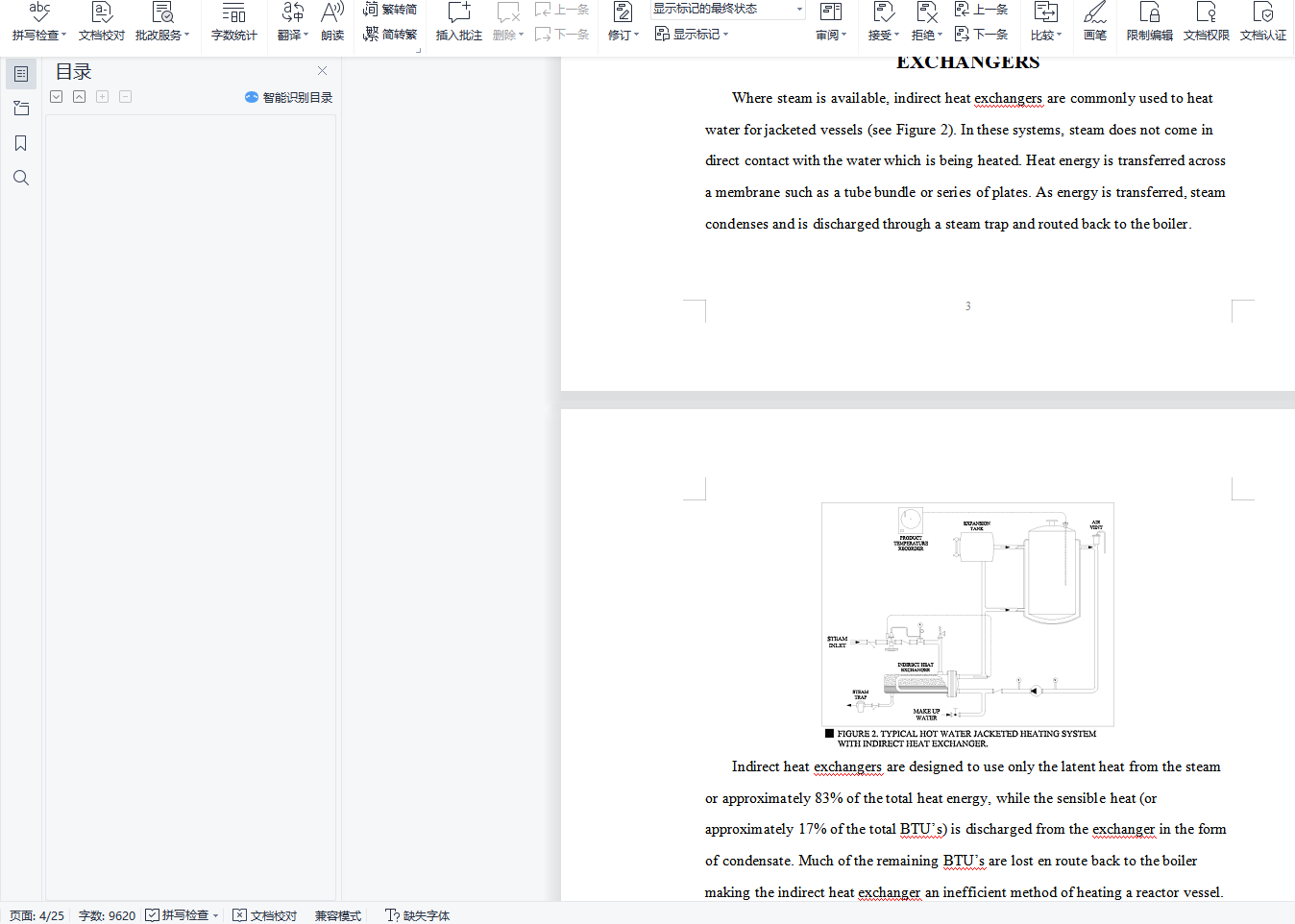