毕业论文(设计)开题报告
一、综述本课题国内外研究动态,说明选题的依据和意义
1.汽车模具发展现状及发展趋势
我国于1953年,长春第一汽车制造厂在中国首次建立了冲模车间,该厂于1958年开始制造汽车模具。我国于20世纪60年代开始生产精冲模具。目前,我国汽车模具制造企业约300家,形成了新的竞争格局:一是以天汽模、一汽模、东风汽模、成飞集成、比亚迪模具、巨轮模具、豪迈科技、延锋伟世通等为代表的行业重点骨干企业,不断进行产业结构升级,产品逐渐向中高档汽车模具转型。其中,天汽模、一汽模、东风汽模、成飞集成、比亚迪模具等综合实力最强,是行业内能够生产中高档轿车覆盖件模具的主要企业。二是河北兴林车身模具制造有限公司等原有的一些规模较小的模具企业迅速壮大,普什模具、上海屹丰模具等拥有较大投资规模的新兴企业不断涌现,并在市场上抢得一席之地。三是外来资本积极投入国内模具市场,如丰田一汽(天津)模具有限公司、烟台骏辉模具有限公司等。[6]
1.1我国拉延模应用
汽车模具中拉延工序是一个很重要的工序,我国的拉延模比以前有了大进步,以发动机罩内板举例,发动机罩内板是汽车零件重要结构件之一,具有成形面积大,变形复杂,模具设计要求高等特点。
发动机罩内板数学模型如图 1 所示,材料选为深冲压用镀锌钢,厚度为0.65mm,零件比较薄,质量约 4.8Kg,尺寸约 1450mm×1150mm×100mm,变形深度不大但成形面积较大,且变化曲率较为复杂,零件基本成对称性,成形力比较均衡。
图1 零件模型[7]
而设计方案为上模尺寸约 2350mm×2150mm×650mm,由模座、凹模型腔和标准件等组成。模座与凹模型腔为整体铸造并整体加工而成,材料为 MoCr 铸铁,为减轻重量设置若干减重孔为保证模具强度,在平衡块下方区域设置加强筋,平衡块用于调整上模与压边圈的压力平衡,导向装置采用四块导板保证上下模合模精度,上模与压力机上滑板用 T 型螺栓连接。
图2 上模[7]
压边圈尺寸约 2350mm×1700mm×320mm,由压边圈本体、顶杆和标准件等组成。本体材料为 MoCr 铸铁,整体铸造,为减轻重量设置若干减重方孔,平衡块与上模平衡块接触,控制压力平衡,导板与上模导板配合保证合模精度,压边圈底部由顶杆支撑,限位孔中安装限位螺钉,便于控制顶起高度。
图3 压边圈[7]
下模尺寸约 2350mm×1920mm×790m,下模由模座本体,凸模型芯和标准件等零件组成,模座本体材料是HT300,整体铸造,凸模型芯材料是 MoCr 铸铁,两者通过均匀分布的4处挡块安装,保证平稳,模座本体上设置垫块,保证与压边圈下侧接触平稳,安装 4 处限位螺钉,控制压边圈行程,顶杆通过顶杆孔与压机接触,模座本体与凸模型芯均设置多处减重结构,减轻模具质量节约成本。[7]
图4 下模[7]
1.2我国翻边整形模应用
汽车覆盖件的生产厂家一般都会有很多台生产设备,每个企业按照合理的生产方式把不同吨位的压力机在生产线上排布,一般一个零件的所有工序在同一条生产线上进行生产,这样可以减少工序件的运输流程,提高生产效率。
以汽车行李箱隔板为例,行李箱隔板在翻边整形时,压边力要足够大,成形过程中零件被稳稳地压制住不会发生窜动,这样零件翻边的质量高,零件上的孔位才不会发生偏移。成形零件为外观件,表面不允许有拉伤缺陷,因此外板压边力比内板压边力要略大。
图5 行李箱隔板[8]
行李箱隔板翻边整形模上、下模座导向只采用导板导向,采用HT300铸造。翻边整形模工作过程为:将修边后的板料放置在下模顶出器上并准确定位后,上模下行,压料块4 压住板料,初始阶段下模顶料力大于上模弹簧的压力,上模下行时完成零件B面向下翻边。上模继续下行,此时压力机冲压力作用到下模顶出器上,成形力远远大于顶出器的顶料力,上模整体与顶出器共同下行,实现C面向上翻边整形,当上模完全与限位块接触后,实现了零件的全部成形。[8]
图6 翻边整形模结构[8]
1.3国外现状
虽然我国汽车覆盖件模具行业进步很大,但与国外先进水平相比,存在明显差距。
国外的汽车封盖冲压仿真技术具有巨大的优势,大大提高了零件的表面质量,有效地降低了材料的利用率,缩短了零件的制造周期。冲压成形模拟包括网格密度、板材形状、拉珠设置、空架力等因素,以保证质量更好的冲压模拟结果,然后通过ETA后处理软件对车前进行数值模拟,可以更好地得到良好的仿真结果,广泛应用于工业设计制造,并提供参考方案。[9]
增量板材成形(ISF)是一种创新的工艺,通过计算机数控(CNC)移动的简单成形工具,以塑性变形符合预期形状的空白板材。该过程涉及使用单一光滑工具在CNC铣床上逐步进行局部钣金变形。该工具的控制运动使您能够进行三维轮廓。该工艺可以为直接从三维计算机辅助设计(CAD)模型制成成品的钣金零件,提供快速的原型设计优势。要获取复杂形状的工具路径,必须设计一个完整成形部件的CAD文件,然后导入到计算机辅助制造(CAM)软件中,并进行模拟。根据零件的复杂性,该过程可以包括一个基本的几何形状来支撑模具或根本没有模具。[10]
2.汽车模具的工艺
2.1拉延模工艺
2.1.1拉延方向的确定
拉延方向的确定是覆盖件拉延工艺设计的第一步,即确定零件在模具中的空间位置。拉延方向确定得合理与否,直接决定能否拉延出满意的覆盖件,同时影响到工艺补充部分的多与少以及后续的工序方案。
2.1.2工艺补充的设计
在汽车覆盖件零件成形过程中,为了给板料拉延提供一定的拉力以防止起皱,为了防止破裂等质量缺陷,或为了后续成形工序的需要等目的,通常将覆盖件的翻边展开,将覆盖件的窗口、孔洞填平,增加压料面、拉深筋等,而在零件本体外增加一部分材料,这部分增加的材料就是工艺补充。工艺补充是覆盖件拉延工艺设计中不可缺少的部分,它既是实现拉延的条件,又是增加变形程度和提高零件刚度的必要补充,还直接影响到拉延成形以后的修边、整形、翻边等工序。
确定工艺补充部分的原则通常是:
1.简化拉延件结构形状:形状越复杂,拉延越困难
2.保证良好的塑性变形条件:斜度较大的拉延件,为了保证拉延时材料能很好地贴紧凸模,可以利用工艺补充部分增加一部分直壁以保证良好的拉延条件。
3.对后续工序有利:尽量垂直修边,简化修边模具结构。
4.用料尽量少:因不是零件结构需要,为提高材料利用率,通常在修边时切除
2.1.3压料面的设计
压料面是压边圈上的环形封闭曲面,压料面是拉延模不可或缺的要素,与拉延筋配合,形成筋 - 槽系统,共同控制进料量,为拉深出合格零件提供条件。压料面要素包括管理面、筋槽 R 角、外压料面。以筋为界,筋的里侧定义为管理面,也叫内压料面,筋的外侧定义为外压料面。[8]压料面的设计会直接影响到拉延成型的进行。
2.1.4拉延筋(槛)的设计
拉延筋是拉延模的重要组成部分,根据筋的形式可分为半圆筋、方筋、坎筋等。一般来讲,走料型拉延模设计成半圆筋,胀型类拉延模设计成方筋或者坎筋。半圆筋又有单筋和双筋之分,需要较大进料阻力的通常设计成双筋。 拉延筋的要素包括筋高、筋宽、筋 R 角。其中筋高度和筋 R 角大小直接决定了筋的进料阻力,筋宽度一般按标准设计。[8]拉延筋设计的合理性,甚至会影响覆盖件的成形结果。
2.1.5工艺孔和工艺切口设计
当需要在零件的中间部位压出深度较大的局部突起或鼓包时,往往由于不能从毛坯的外部得到材料的补充或本身材料的延伸率不够而导致零件的局部破裂,此时可考虑在局部变形区的适当部位冲出工艺孔或工艺切口,使容易破裂的区域从变形区内部得到材料补充。
2.1.6拉延件图绘制
拉延件图是覆盖件拉延模的设计依据,因此拉延件图不同于产品图,而是在产品图的基上经过工艺补充后得到的适合冲压加工的工序图,绘制时必须符合下列要求:
1)按照拉延件的冲压位置绘制,不是像产品那样按照零件在产品上的装配位置绘制。
2)需要标注拉延件的轮廓尺寸,不同位置的深度,拉延件在汽车坐标系中的定位尺寸、拉延方向与坐标系的关系,后面工序示意线及尺寸,工艺补充部分的尺寸(修边线)等,有时还标注后面工序的冲压方向,但不标注拉延件的外轮廓尺.
2.2翻边工艺设计
2.2.1翻边方向的确定
根据翻边凸、四的运动方向不同,翻边有垂直方向边、水平方向边和倾斜边三种。
2.2.2翻边工艺参数的确定
由于翻边工序通常是覆盖件成形的最后一道工序,因此翻边工艺参数的合理与否直接影响到覆盖件的质量。翻边工艺参数主要包括回弹工艺参数的确定、翻边时变形区的受力状态分析以及压料力的确定。
3.汽车模具存在的主要问题
3.1拉延模存在的主要问题
3.1.1拉伤
3.1.2起皱
3.1.3拉伤
3.2翻边整形模存在的主要问题
3.2.1起皱
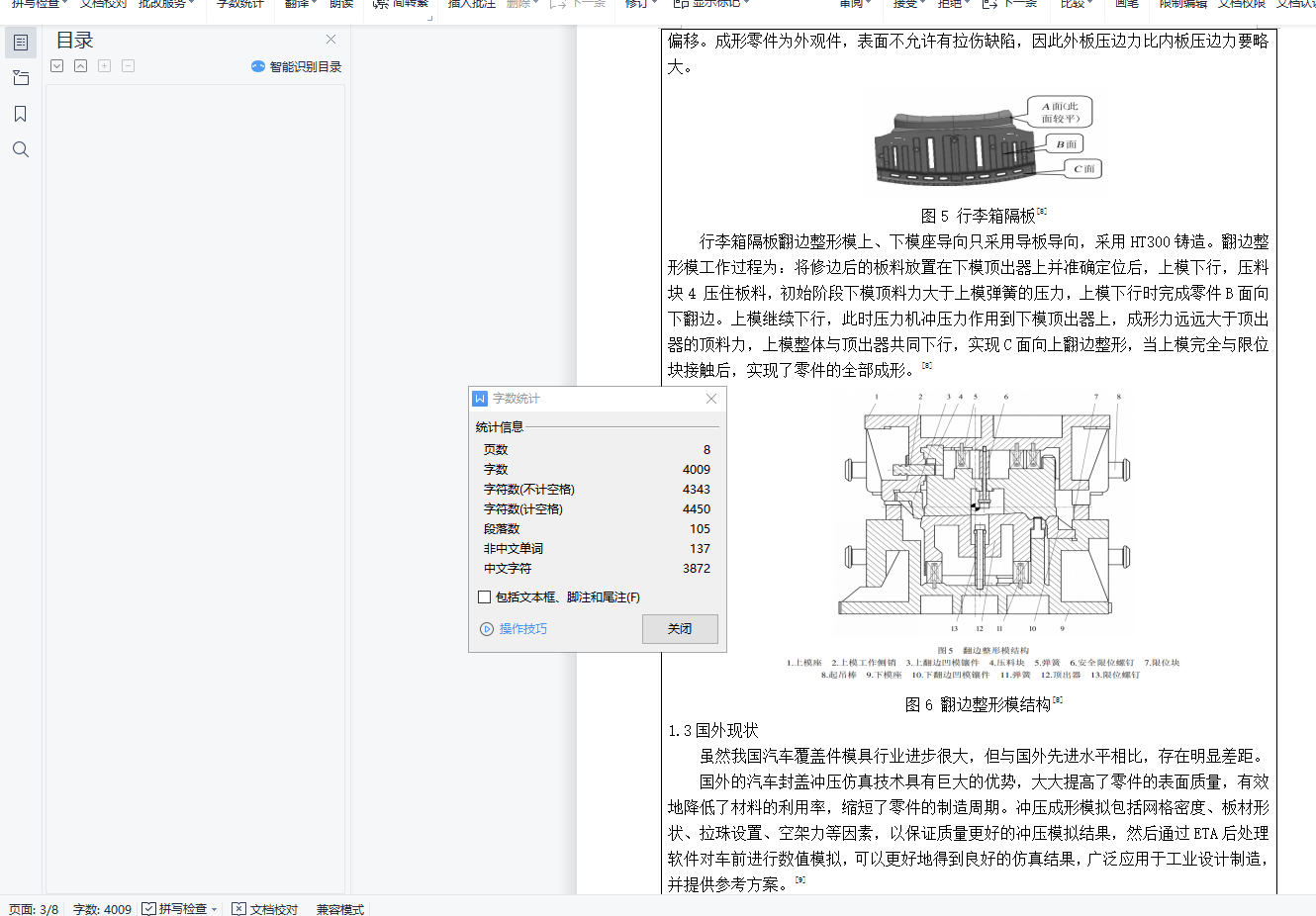
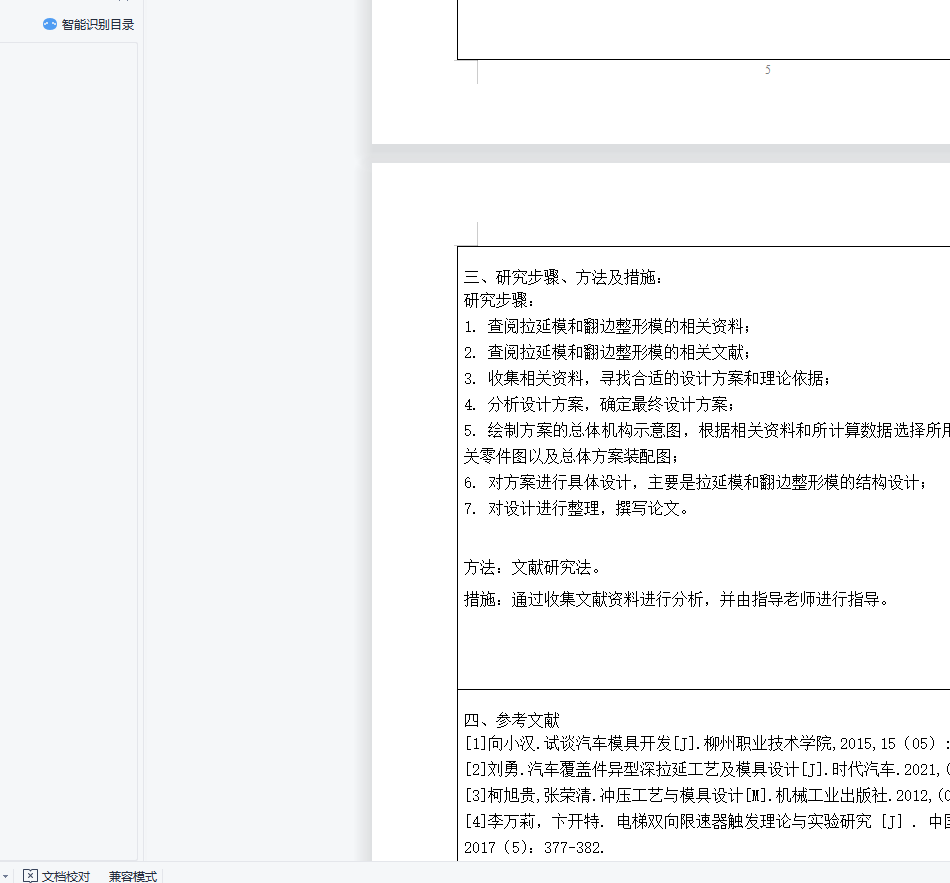