机械装备寿命的可靠构建与优化设计
摘要:维护设计对于机电产品或系统的寿命周期来讲,是一种重要的设计方法。基于机构作用可能会出现失败的几率,机械系统的可靠性建模被发展了起来。基于部件可能会出现失败的情况,机械系统的可靠性建模就被发展了起来而系统最小的可靠性和最稳定的可靠性系数被定义为机械系统在寿命周期内大致的可靠性。其次,提出维护的一个基于可靠性的设计最优化模型,总生活周期消耗被考虑作为设计目标和系统可靠性。最终,维护的基于可靠性的设计最优化方法通过组分设计示范被说明。
关键词:维护; 可靠性; 模拟; 优化设计
1. 介绍
在一个机械产品期间的生命周期,维护是非常重要的,可以保持产品可利用时间和延长它的寿命。关于维护的研究机械产品的大致被分类为以下三种:(1)如何拟定维护政策或(和)如何优选考虑系统可靠性和维修费用的维护期间[1−4]。(2)发展维护方法和工具保证系统维护到低成本和短的修理时间,例如发展特别的维护工具[5−9]。(3)在设计程序期间,为维护设计,系统可维护性地被评估和被改进[10−12]。维护在设计之初就开始了。明显地,维护的设计方法论,是其中一个在产品的生命周期的最佳的有效的维护手段,吸引许多研究者的兴趣。然而,维护设计的研究主要在于两个领域。一个是在产品设计选择的可维护性评估; 另一个是为方便维护设计的特殊结构的零件。在本文中,根据时间对失败零件的密度函数,要调查接受维护的一个机械系统的零件的服务寿命。然后机械系统的可靠性模型被重建并且被仿真。最终,维护的新颖的设计最优化方法通过一个链式设计被发展并说明。
2. 可靠性塑造维护的机械系统
2.1模型假定
在一个机械系统运行一段时间之后,由于失败的被替换分开,主要可靠模型是不适用于改变系统,因而应重建可靠性模型。在本文谈论的机械系统有以下特征:①一个系统包括很多同样的零件,零件的数量在系统期间的一生周期是恒定的。②所有零件的时间对失败密度分布函数是相同的,并且替换件也和原始的零件一样有失败分布函数。③每个部分的失败是一个任意的独立事件,也就是说一部分的失败不影响其他部分在系统的中的失败。
2.2为维护的可靠性建模
一个机械系统的可靠性取决于它的零件,可靠性和失败的可能性取决于他们的工作寿命。在这里,根据时间的密度分布函数对零件的失效,应计算好部件在机械系统中工作寿命,然后开发机械系统的可靠性模型。在一个机械系统的服务期间,发生故障的有些零件要求及时替换,因此机械系统的部分的寿命分布被改变了。推测在机械系统运行一段时间后tn = nτ,其中τ是维护活动之间的时间,即维护间隔时间之后, τ单位可以是几小时、几天、几个月或者几年。 如果pi (pt)代表零件的年龄比例在n用年龄iτ,因而部分的年龄分布在时间上表示为矩阵{p0 (tn), p1 (tn), L、pi (tn), L, pn (tn)}。零件的失败密度函数和部分的寿命分布在系统的确定寿命分布在下次或者在下一段时间区内留下来的部分目录。寿命分布取决于每一段时间内每一部分部件在下一段时间区内失效的几率。要发现零件的失效可能性失败密度函数是从零开始的。存留下来的数量在下一个时间段得到提升,失效的部分被新的部件替换被重新返回第一个盒子里。
最初的,所有零件是新的病在第一个盒子里。 即在t0=0,在第一个箱子的部分是
P0(t0)=1 (1)
在t1=τ,第一个箱子的年龄分数和第二个箱子代表:
P1(t1)=p0(t0)[1-∫f(x)dx]
P0(t1)=p0(t0) ∫f(x)dx (2)
两种寿命盒子内的部分,生存并且到下个寿命箱子,而不合格部件的部分被新的零件替换,从这两个箱子到第一个箱子。
在T2 = 2τ,计算前三个箱子的比例
P2(t2)=p1(t1)[1-∫f(x)dx]
P1(t2)=p0(t1)[1-∫f(x)dx]
P0(t2)= p1(t1) ∫f(x)dx+ p0(t1) ∫f(x)dx (3)
……
因此,通过使用以下等式,在tn = nτ时,在每个箱内的部分部件将被进行如下计算:
当P0(tn)是寿命在tn的部件总量的一小部分时,代表了部件刚刚被投入使用。这就意味着P0(tn)是这部分的失效率,或者说是小部件的代替。换种说法就是说,这些在第一个盒子里的一小部分部件在t0,t1,L,tn是用来取代失效部件的新部件。
一系列的系统包含了N个有相同失效概率分布的部件,每一个部分只是一系列的单元,每个单元是相对独立的。在同一系列系统里任何一个单元的失效表现为一个系统的失效,按照可能增长的原则,一系列系统的可靠性就是:
由于组成系统的部件数量是恒定的,在此,机械系统维护的系统稳定性被定义为:
3. 维护可靠性的模拟仿真
模拟仿真的结果显示了系统的稳定性在工作期间是不断变化着的。一个系统的可靠性经历了几次波动,有时是最大值而有时是最小值,最终达到一个稳定的值。系统稳定性的震动会周期性的衰减,这段时间是部件μ的预期寿命(根据韦伯分布,参数β近似于大α的预期寿命)。对于机械系统的设计和维护,系统稳定性的最小值跟稳定值是最重要的。系统的最低稳定性出现在初始阶段,但系统可靠性的稳定值出现在运行一段很长时间后。在此,为了后面方便讨论,系统维护的最低可靠性和稳定可靠性被定义为基于如图6所示的系统稳定性的仿真结果中。
由于它发生在初始阶段,系统最小可靠性会在从t=0到t=2μ的仿真结果的不相关联的可靠性值中找到。最小可靠性被定义为:
假设仿真时间是T0和Rmax、Rmin分别代替了在t∈[T ,T + 2μ]的最大值和最小值。一旦当最大可靠性值和最小可靠性值的比值Rmin/Rmax>ε满足,系统可靠性被认为在T0时达到一个稳定的值。因此,系统稳定性或者说稳定可靠性被定义为:
ε ≤ 1是稳定的要求,通常是98%。如果T0不存在,系统稳定性是不稳定的。
4. 可靠性的优化设计模型库
对于维护的一个基于可靠性优化设计模型被用来跟耗费维护的系统可靠性和寿命周期消费来代替,上述模型对于计算系统的部件替换率,最小可靠性和系统可靠性有帮助。在这个模型里,寿命周期的消耗被认为是一个设计目标,而系统的可靠性被认为是设计约束条件。我们的工作目标就是要去找到一个最小消耗的设计方法并同时满足这个系统规定参数。
4.1 模型的寿命周期损耗
机械系统的寿命周期损耗包含着产品成本和维护成本。系统维护成本是来源于以下所列的项目:(1)替代部件的成本;(2)操作损耗包括替换部件时的资源损耗(比如: 劳动、装备);(3)替换部件时的生产间隔造成的间接成本;(4)替换部件的准备工作成本。在前面的三个项目参与了每次维护时替代部件的数量。替换越多的部件就会耗费越多的资源,占用越多的生产时间,因而带来巨大的损失并增长了维护成本。最后一项没有参与替换部件的数量上但参与了每次维护跟替换上。结果,机械系统的维护成本被保密为替换部件数量上的成本考虑和维护次数上的成本考虑。在这种方法下,对于一个包含固定数量N部件的机械系统,在它运行了一段时间M,它的寿命周期损耗模型包含了生产成本和维护成本,表示为:
在式子9,C是系统内每一部分部件总的寿命周期损耗。c0, c1, c2分别表示部件生产系数,更换成本系数和准备成本系数,这些数据是统计分析领域的数据。m = M /τ,M代表着系统寿命。式子10等号右边的首项代表系统的生产成本,式子9右边的第二项表示系统的维护成本。在式子9里,由于部件的替换成本包含着不仅仅是替换失效部件的部件生产成本,而且有用于资源的成本和用于替换的间接成本。显然,式子10里表示的不是绝对成本,而是相对成本。式子9也可以表示为:
4.2 基于可靠性的设计与优化
假设系统的一类部件有n种设计方案。X= (x1,x2,L,xn), 它们的失效密度函数被表示为每一种方案,X= (x1,x2,L,xn) 它们的失效密度函数被表示为F=(f1(t),f2(t),L,fn(t)) 作为每一个方案。
对于一个维护的固定间隔τ0,它的基于可靠性优化设计的模型I的维护被表示为:
显然的,最小寿命周期损耗和可靠性取自上述模型的一段特定的时间段。对于任何一个的n种设计方案,它的成本和可靠性取决于维护间隔τ。最小的成品成本可以取自于最优化的维护间隔。所谓的最佳的维护间隔,顾名思义地,就是将维护间隔优化到最小的寿命周期成本,因此基于可靠性设计和优化的模型Ⅱ的维护克表示为:
在式子11和式子12里,C是取自式子9或式子10,Rm、Rs分别表示系统的最小可靠性和稳定的可靠性。Rm0、Rs0是系统允许的可靠性值。通常来讲,Rm0= (0.75~0.95)Rs0,这也就意味着系统稳定性在整个寿命周期内允许在某一定的程度上变化,但变化范围不会超过稳定可靠性值的5%~25%。
4.3 根据系统可靠性模仿的设计最优化
显然,系统平稳的可靠性、极小的可靠性和部分在设计模型的替换率可以从可靠性模仿而获得。所以,维护的设计最优化是基于模拟的设计方法。在设计模型,可靠性模仿的输入的情况是时间对失败密度系统部分F,系统服务生活M的分布函数,并且生活周期消耗系数是c0,c1,c2。
为固定的间隔时间维护,输入的情况在固定的维护间隔时间τ 0增加。维护的时间与M/τ 0明显地是相等的在一生周期期间。 至于维护间隔时间需要被优选的情况,维护的时间是获得的被环绕的M/τ在另外维护间隔时间。另外,系统的设计选择必须满足系统可靠性的要求,因而Rm, Rs得出来了。 终于,一个优选设计选择和它极小的信度、平稳的可靠性和生活周期费用被得出了。 设计最优化流程图维护的显示作为式子二,设计最优化二个模型维护的是联合。最可能,一个模型的解答通常是与另一个模型不同。
5. 设计示范
有链式传送机链接圆环的三个设计选择,产品使用期限M等于100个月。时间的密度分布函数对圆环的失败的是Weibull的作用,并且他们的发行参量和费用系数生命周期在表1被列出如下。
假设极小的可靠性和平稳的可靠性的要求是R0 = 0.85, R0 = 0.75。 考虑系统维护间隔时间从一系列的等效区别价值被挑选,离散最优化方法被采取。两个设计模型的模仿结果维护在表2.图8到图11被列出说明系统可靠性和总生活周期费用随系统的工作次数变化。
注: τ 0是间隔时间固定周期维护的设计模型Eq (11),和最宜的间隔时间优选周期维护的设计模型Eq(12).
当系统维护间隔固定,最宜的设计选择如显示从模仿结果在表2列出了,Eq(11)是选择τ 0 = 1 2 x。其中1x不满足系统可靠性压抑,并且共计选择2 x的寿命消耗低于选择3 x。 从这个例子,了解到不可能有将遇见系统可靠性为不适当的固定的维护间隔时间压抑的设计选择。当系统维护间隔时间被优选时,最宜的设计选择被获得了。Eq(12)是选择3 x。 在这个例子中,所有设计选择符合系统可靠性的要求,并且共计选择3 x的寿命消耗是最低的,相应地系统维护间隔时间τ *1.8选择了3 x。 显示易变的维护周期警察导致设计选择另外选择,并且共计生活费用可以是通过优选维护间隔时间减少。
几个有趣的结果能从图3到图6中被找到。.
(1)当固定的间隔时间(τ0 = 1)是坚定的,选择的系统可靠性τ0 = x2不仅满足所有设计要求,而且接近对要求价值。选择x1的可靠性满足平稳的可靠性的要求,但是不满足极小的可靠性的要求竟管它最便宜。 虽然选择3 x满足系统可靠性的要求,平稳的可靠性或极小值可靠性,它有最高的总寿命周期消耗。
图3.设计选择的可靠性模仿固定的维护间隔时间
图4. 设计选择的生活周期费用模仿固定的维护间隔时间
(2)当维护间隔时间被优选时,最宜的间隔时间的选择根据系统可靠性的令人满意要求前提。 至于选择1 x,为了符合系统可靠性的要求,维护间隔时间减退,但是它的总生活费用增加有些。 为选择τ * = 0.8x2,维护间隔时间在优化以后保留常数,也,因此意味着间隔时间τ =1是这个选择的最宜的间隔时间。 为选择3 x,由于优化、维护间隔时间增量、τ =1.8和在系统可靠性和设计要求之间的区别减少,因而它有更低的总生活周期费用。 其外,三个设计选择被优选,系统可靠性和总生活周期费用他们的曲线趋向对集中化和坚固性,并且费用区别在三个选择之中的减少。
图5.设计选择的可靠性模仿最宜的维护间隔时间
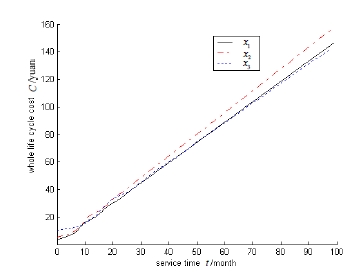
图6.设计选择的生活周期费用模仿最宜的维护间隔时间的
(3) 当系统要求高的可靠性时,相应地,维护间隔时间将减少,并且维修费用将上升。 相反,当系统要求低可靠性,相应地,维护间隔时间将延迟,因此维修费用将减少,系统维护费用减退受系统可靠性要求支配。系统可靠性平稳的价值和最小值随着维护间隔时间的增加单调减少总生活周期费用随着维护间隔时间的增加而减少。结果,稳定的极小的间隔时间系统可靠性价值和最小值满足设计要求将得到设计选择的极小的总生活周期费用。必须指出设计选择的系统可靠性比要求价值不是相等与,而是少许更多由于离散最优化的采用。
(4) 当系统的设计选择决定时,设计选择最宜的选择取决于不仅维护系统可靠性和系统服务生活的间隔时间而且还有要求。 例如,当间隔时间被固定时(τ 0 = 1),并且需要的系统可靠性减少从对,从Eq.(11)获得的最宜的设计选择是选择0.75 m R = 0.70 m R = x1而不是选择2 x。当系统服务生活转换从M = 100到50时,最宜的设计选择被获得了。 Eq(12)是替换3 x而选择1 x显示作为图6。这就意味着,因为高质量材料做的零件有长的产品使用期限,设计选择得到更低的总寿命周期成本,竟管他们会有更高的生产成本。
6. 结论
在产品期间的生命周期维护是其中一项重要任务。零件的替换将导致系统可靠性和生活周期费用的变动。基于零件的时间失效密度函数,平稳的可靠性、极小的可靠性和生活周期费用可以通过可靠性模型的系统可靠性的重建和模仿得到。本文开发维护的基于可靠性的设计最优化方法学,总生活周期费用被看待,当作为设计的设计对象和系统可靠性压抑。它提供一种新的方法做在机械系统之间的可靠性和总生活周期费用的一种交易在设计最优化的维护。
鸣谢
这项工作得到了湖南科学技术大学的刘博士的大力支持。 笔者相当感激能得到其参考资料的注释,极大地改进了目前这项工作。
参考文献
[1] B.Y. Liu, Y.T. Fang, J.X. Wei, et al. “Reliability and check replacement policy of mechanical equipment under predictive maintenance”. Chinese Journal of Mechanical Engineering. 2006.Wuhan, vol.42,pp.30- 35,February .
[2] H. Zhang , J. Wang, F.S Wen, et al. “Optimal scheduling of condition based maintenance for electric equipment considering reliability and economy”. Electric Power Science and Engineering. Beijing, 2006. vol..21, pp.8-13.
[3] Q. He, “Mathematical model of preventive maintenance period”. Transactions of the Chinese Society of Agricultural Machinery.Beijing, 2005, Vol..36, pp.153-154.
[4] H. Wang , H. Pham, “Some maintenance models and availability with imperfect maintenance in production systems”. Annals of Operations Research. Springer US,1999, Vol..91, pp. 305-318.
[5] Y.H. Yang, Y.C. Feng , “Complex repairable system reliability and maintainability simulation”. Acta Simulata Systematica Sinica. Beijing, 2002, Vol.14, pp.978-982.
[6] W.S. Yin, W.G. Zhu and S.Q Li, “Virtual system of training and maintaining oriented to the life cycle of mechanical and electronical products,” China Mechanical Engineering, Wuhan,2004, Vol.15, pp.1530-1532.
[7] Y.L. Li, S.X. Pan , “Remote dynamic assembling disassembling process simulation system for mechanical product maintenance”, Journal of Computer Aided Design & Computer Graphics, 2005, Vol.17, pp.2744- 2750.
[8] J. Liu, D.J. Yu, R. Li, et al, “Research on general stochastic Petri net based maintenance system simulation and optimization”, Chinese Journal of Mechanical Engineering, 2005, Vol.41, pp.164-169.
[9] D. Chaudhuri, O. Mohammed, “Optimal inspection and replacement models for systems with increasing minimal repair cost,” International Journal of Reliability, Quality and Safety Engineering, 1999, Vol.6, pp.155-171.
[10] M.Z. Gan, “Maintainability design and validation” , Beijing:Defence Industry Publishing House,1995.
[11] E.G. Welp, U. Lindemann, X.S. Lv, “Support instructions for a recyclable and maintainable design,” Engineering Design, 2002, Vol.9, pp.77-88.
[12] H. Zhou, M.Z. Gan, A.Q. Liu, et al. “Maintainability design of product based on concurrent engineering,” Journal of Machine Design, 2003 ,Vol..20, pp.3-5.
[13] Y. Liu, H.Z. Huang, “Comment on ‘‘A framework to practical predictive maintenance modeling for multi-state systems’’ by Tan C.M. and Raghavan N. [Reliab Eng Syst Saf 2008; 93(8): 1138–50],” Reliability Engineering and System Safety, 2009, Vol.94, No.3, pp.776-780.
[14] H.Z. Huang, X. Zhang, “Design optimization with discrete and continuous variables of aleatory and epistemic uncertainties,” ASME Journal of Mechanical Design, 2009, Vol.131, pp.031006-1-031006-8.