Machining fixture locating and clamping position optimization using genetic algorithms
Necmettin Kaya*
Department of Mechanical Engineering, Uludag University, Go¨ru¨kle, Bursa 16059, Turkey Received 8 July 2004; accepted 26 May 2005
Available online 6 September 2005
Abstract:In order to ensure the machining accuracy and fix the workpiece in the process of mechanical machining, the process equipment which can be used for machining or testing is referred to as fixture for short. Jigs first appeared in the late 18 th century. With the development of science and technology, fixture has developed from an auxiliary tool to a complete range of process equipment. Jig is a kind of device used for clamping workpiece on machine tool. Its function is to make the workpiece have a correct position relative to the machine tool or cutting tool and keep this position unchanged in the process of machining. The role of jigs and fixtures in machining can be summed up in these aspects: to ensure machining accuracy; to improve Production efficiency, reduce costs; expand the scope of machine tools; reduce the labor intensity of workers. Its composition includes positioning element, clamping device, connecting element between fixture and machine tool, cutter or guide element, other device or component, clamping detail. According to the scope of use of the fixture can be divided into: general fixture, special fixture, general adjustable fixture and group fixture, combination fixture, accompanying fixture. Here we focus on fixture design automation, standardization, generalization and high efficiency, and pay attention to green design to make the operation comfortable, agile, accurate. This is beneficial to shorten the production cycle and reduce the cost, so as to obtain good economic benefits.
Keywords: Fixture design; Genetic algorithms; Optimization
1. Introduction
China's domestic jigs began in the 1960s, when the Tianjin jig factory for machinery industry and Baoding Xiangyang machinery factory for aviation industry were established, and several factories for producing modular fixture components were set up. At that time, the annual production level of 8 million modular fixture components was reached in the whole country. After the 1980s, the two factories independently developed the hole series modular fixture system suitable for NC machine tools and machining centers, which not only met the domestic demand of our country. Also exported to the United States and other countries. At present, our country still needs to import many NC machine tools and machining centers every year. Very expensive, now most of the domestic support, saving a lot of foreign exchange.
Internationally, Russia, Germany and the United States are major producers of modular fixtures. At present, the international fixture enterprises are small and medium-sized enterprises, special fixture, adjustable fixture mainly accept the local and domestic orders, and the versatile modular fixture has gradually matured into a variety in international trade. The output value and trade volume of jigs and modular jigs are still lack of statistical data, but a set of central tools used in machining centers in Europe and the United States is usually 1110 to 1115 of the price of machine tools, and the large base parts of modular jigs are especially expensive. Because our country has the historical accumulation in the combination fixture technology and the performance price ratio superiority, along with me China's entry into wTO and the trend of global integration of manufacturing industry, especially the development of electronic commerce, contain great business opportunities and have a good prospect of further expanding export.
The statistics of the International production Research Association show that, at present, about 85% of the total number of workpieces are produced in small lots and many varieties. Modern production requires that the products manufactured by enterprises are often updated to meet the needs and competition of the market. However, the general enterprises are still used to a large number of traditional special fixture, generally in the factory with medium production capacity, there are about thousands or even nearly ten thousand sets of special fixture; On the other hand, in many kinds of production enterprises, 50% or 80% special fixture should be renewed every 3 ~ 4 years, and the actual wear quantity of fixture is only about 10 ~ 20%. Especially in recent years New machining technologies, such as NC machine tools, machining centers, group technology, flexible manufacturing system (FMS), etc.
New requirements for fixture are put forward as follows:
The main contents are as follows: 1) it can quickly and conveniently equip the new product to put into production, so as to shorten the production preparation period and reduce the production cost;
2) capable of holding a set of similar workpieces;
3) the fixture of high precision machine tool which can be used in precision machining;
4) A new type of machine tool fixture which can be used in various modern manufacturing technologies;
5) adopt high-efficiency clamping device with hydraulic station as power source to further reduce labor intensity and improve labor productivity;
6) improve the standardization of machine tool fixture.
The direction of modern machine tool jigs mainly shows four aspects: standardization, precision, high efficiency and flexibility.
The main contents are as follows: (1) Standardization and generalization of machine tool fixture are two interrelated aspects. At present, there are national standards of fixture parts and components in China: GB/T2148~T2259-91, all kinds of general fixture, modular fixture standard and so on. The standardization of machine tools and fixtures is beneficial to the commercialization of jigs, the shortening of production preparation period and the reduction of total production cost.
(2) with the increasing precision of mechanical products, the precision of fixture will be improved accordingly. There are many structural types of precision jig, such as multi-tooth disk for precision indexing, its indexing accuracy can be up to ±0.1 ", and high precision three-claw self-centering chuck for precision turning, with a centering accuracy of 5 μ m.
(3) the high efficiency fixture is mainly used to reduce the basic time and auxiliary time of workpiece processing, in order to improve the labor productivity and reduce the labor intensity of workers. Common high-efficiency jigs are automatic jigs, high-speed jigs and clamps with clamping force. For example, using electric vice to clip workpiece on milling machine, the efficiency can be increased about 5 times; Using a high speed three-claw self-centering chuck on a lathe can ensure that the claw can firmly clamp the workpiece even when the test speed is 9000r/min, thus greatly increasing the cutting speed. At present, in addition to the production line, automatic line configuration corresponding efficiency, In addition to the automatic fixture, various kinds of automatic clamping fixture of workpiece and the device of replacing the fixture automatically appear in the NC machine tool, especially in the machining center, which makes full use of the efficiency of the NC machine tool.
(4) the flexibility of the flexible fixture is similar to the flexibility of the machine tool. It refers to the ability of adjusting and combining the fixture to adapt to the variable factors of the process. Process variables are: process characteristics, batch production, workpiece shape and size, etc. New types of jigs with flexible features include: modular fixture, general adjustable fixture, group fixture, modular fixture, numerical control fixture and so on. In order to meet the needs of modern mechanical industry in many kinds and medium and small batch production, expand the flexibility of fixture, change the non-detachable structure of special fixture into detachable structure, and develop adjustable fixture structure, it will be the current situation. The main direction of fixture development.
With the rapid development of science and technology, advanced manufacturing technology has been continuously developed. The fixture occupies a very important position in the process of mechanical machining. It can guarantee the machining precision of the workpiece reliably, improve the machining efficiency and lighten the intensity of labor. Driven by the development of machine tool technology in the direction of high speed, high efficiency, precision, conformity, intelligence and environmental protection, fixture technology is developing towards the direction of high precision, high efficiency, module, combination, general use and economy.
According to the requirement of machining technology of base level milling die fixture, the features of this subject are high precision, strong pertinence, compact structure, simple operation and high productivity. In addition, the type and structure of the jig must be suitable to the batch size of the parts, and the structure and parts of the fixture should have sufficient rigidity and strength to ensure the operation of the fixture is convenient, the clamping is reliable, and the operation is safe. And there is reasonable loading and unloading space.
Fixtures are used to locate and constrain a workpiece during a machining operation, minimizing workpiece and fixture tooling deflections due to clamping and cutting forces are critical to ensuring accuracy of the machining operation. Traditionally, machining fixtures are designed and manufactured through trial-and-error, which prove to be both expensive and time-consuming to the manufacturing process. To ensure a workpiece is manufactured according to specified dimensions and tolerances, it must be appropriately located and clamped, making it imperative to develop tools that will eliminate costly and time-consuming trial-and-error designs. Proper workpiece location and fixture design are crucial to product quality in terms of precision, accuracy and finish of the machined part.
Theoretically, the 3-2-1 locating principle can satisfactorily locate all prismatic shaped workpieces. This method provides the maximum rigidity with the minimum number of fixture elements. To position a part from a kinematic point of view means constraining the six degrees of freedom of a free moving body (three translations and three rotations). Three supports are positioned below the part to establish the location of the workpiece on its vertical axis. Locators are placed on two peripheral edges and intended to establish the location of the workpiece on the x and y horizontal axes. Properly locating the workpiece in the fixture is vital to the overall accuracy and repeatability of the manufacturing process. Locators should be positioned as far apart as possible and should be placed on machined surfaces wherever possible. Supports are usually placed to encompass the center of gravity of a workpiece and positioned as far apart as possible to maintain its stability. The primary responsibility of a clamp in fixture is to secure the part against the locators and supports. Clamps should not be expected to resist the cutting forces generated in the machining operation.
For a given number of fixture elements, the machining fixture synthesis problem is the finding optimal layout or positions of the fixture elements around the workpiece. In this paper, a method for fixture layout optimization using genetic algorithms is presented. The optimization objective is to search for a 2D fixture layout that minimizes the maximum elastic deformation at different locations of the workpiece. ANSYS program has been used for calculating the deflection of the part under clamping and cutting forces. Two case studies are given to illustrate the proposed approach.
2. Review of related works
Fixture design has received considerable attention in recent years. However, little attention has been focused on the optimum fixture layout design. Menassa and DeVries[1]used FEA for calculating deflections using the minimization of the workpiece deflection at selected points as the design criterion. The design problem was to determine the position of supports. Meyer and Liou[2] presented an approach that uses linear programming technique to synthesize fixtures for dynamic machining conditions. Solution for the minimum clamping forces and locator forces is given. Li and Melkote[3]used a nonlinear programming method to solve the layout optimization problem. The method minimizes workpiece location errors due to localized elastic deformation of the workpiece. Roy andLiao[4]developed a heuristic method to plan for the best supporting and clamping positions. Tao et al.[5]presented a geometrical reasoning methodology for determining the optimal clamping points and clamping sequence for arbitrarily shaped workpieces. Liao and Hu[6]presented a system for fixture configuration analysis based on a dynamic model which analyses the fixture–workpiece system subject to time-varying machining loads. The influence of clamping placement is also investigated. Li and Melkote[7]presented a fixture layout and clamping force optimal synthesis approach that accounts for workpiece dynamics during machining. A combined fixture layout and clamping force optimization procedure presented.They used the contact elasticity modeling method that accounts for the influence of workpiece rigid body dynamics during machining. Amaral et al. [8] used ANSYS to verify fixture design integrity. They employed 3-2-1 method. The optimization analysis is performed in ANSYS. Tan et al. [9] described the modeling, analysis and verification of optimal fixturing configurations by the methods of force closure, optimization and finite element modeling.
Most of the above studies use linear or nonlinear programming methods which often do not give global optimum solution. All of the fixture layout optimization procedures start with an initial feasible layout. Solutions from these methods are depending on the initial fixture layout. They do not consider the fixture layout optimization on overall workpiece deformation.
The GAs has been proven to be useful technique in solving optimization problems in engineering [10–12]. Fixture design has a large solution space and requires a search tool to find the best design. Few researchers have used the GAs for fixture design and fixture layout problems. Kumar et al. [13] have applied both GAs and neural networks for designing a fixture. Marcelin [14] has used GAs to the optimization of support positions. Vallapuzha et al. [15] presented GA based optimization method that uses spatial coordinates to represent the locations of fixture elements. Fixture layout optimization procedure was implemented using MATLAB and the genetic algorithm toolbox. HYPERMESH and MSC/NASTRAN were used for FE model. Vallapuzha et al. [16] presented results of an extensive investigation into the relative effectiveness of various optimization methods. They showed that continuous GA yielded the best quality solutions. Li and Shiu [17] determined the optimal fixture configuration design for sheet metal assembly using GA. MSC/NASTRAN has been used for fitness evaluation. Liao [18] presented a method to automatically select the optimal numbers of locators and clamps as well as their optimal positions in sheet metal assembly fixtures. Krishnakumar and Melkote [19] developed a fixture layout optimization technique that uses the GA to find the fixture layout that minimizes the deformation of the machined surface due to clamping and machining forces over the entire tool path. Locator and clamp positions are specified by node numbers. A built-in finite element solver was developed.
Some of the studies do not consider the optimization of the layout for entire tool path and chip removal is not taken into account. Some of the studies used node numbers as design parameters.
In this study, a GA tool has been developed to find the optimal locator and clamp positions in 2D workpiece. Distances from the reference edges as design parameters are used rather than FEA node numbers. Fitness values of real encoded GA chromosomes are obtained from the results of FEA. ANSYS has been used for FEA calculations. A chromosome library approach is used in order to decrease the solution time. Developed GA tool is tested on two test problems. Two case studies are given to illustrate the developed approach. Main contributions of this paper can be summarized as follows:
(1) developed a GA code integrated with a commercial finite element solver;
(2) GA uses chromosome library in order to decrease the computation time;
(3) real design parameters are used rather than FEA node numbers;
(4) chip removal is taken into account while tool forces moving on the workpiece.
3. Genetic algorithm concepts
Genetic algorithms were first developed by John Holland. Goldberg [10] published a book explaining the theory and application examples of genetic algorithm in details. A genetic algorithm is a random search technique that mimics some mechanisms of natural evolution. The algorithm works on a population of designs. The population evolves from generation to generation, gradually improving its adaptation to the environment through natural selection; fitter individuals have better chances of transmitting their characteristics to later generations.
In the algorithm, the selection of the natural environment is replaced by artificial selection based on a computed fitness for each design. The term fitness is used to designate the chromosome’s chances of survival and it is essentially the objective function of the optimization problem. The chromosomes that define characteristics of biological beings are replaced by strings of numerical values representing the design variables.
GA is recognized to be different than traditional gradient based optimization techniques in the following four major ways [10]:
1. GAs work with a coding of the design variables and parameters in the problem, rather than with the actual parameters themselves.
2. GAs makes use of population-type search. Many different design points are evaluated during each iteration instead of sequentially moving from one point to the next.
3. GAs needs only a fitness or objective function value. No derivatives or gradients are necessary.
4. GAs use probabilistic transition rules to find new design points for exploration rather than using deterministic rules based on gradient information to find these new points.
4. Approach
4.1. Fixture positioning principles
In machining process, fixtures are used to keep workpieces in a desirable position for operations. The most important criteria for fixturing are workpiece position accuracy and workpiece deformation. A good fixture design minimizes workpiece geometric and machining accuracy errors. Another fixturing requirement is that the fixture must limit deformation of the workpiece. It is important to consider the cutting forces as well as the clamping forces. Without adequate fixture support, machining operations do not conform to designed tolerances. Finite element analysis is a powerful tool in the resolution of some of these problems [22].
Common locating method for prismatic parts is 3-2-1 method. This method provides the maximum rigidity with the minimum number of fixture elements. A workpiece in 3D may be positively located by means of six points positioned so that they restrict nine degrees of freedom of the workpiece. The other three degrees of freedom are removed by clamp elements. An example layout for 2D workpiece based 3-2-1 locating principle is shown in Fig. 4.
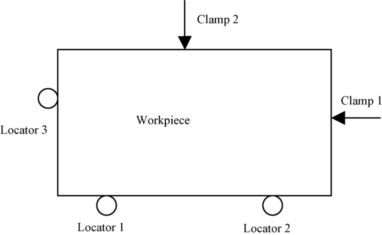
Fig. 4. 3-2-1 locating layout for 2D prismatic workpiece
The number of locating faces must not exceed two so as to avoid a redundant location. Based on the 3-2-1 fixturing principle there are two locating planes for accurate location containing two and one locators. Therefore, there are maximum of two side clampings against each locating plane. Clamping forces are always directed towards the locators in order to force the workpiece to contact all locators. The clamping point should be positioned opposite the positioning points to prevent the workpiece from being distorted by the clamping force.
Since the machining forces travel along the machining area, it is necessary to ensure that the reaction forces at locators are positive for all the time. Any negative reaction force indicates that the workpiece is free from fixture elements. In other words, loss of contact or the separation between the workpiece and fixture element might happen when the reaction force is negative. Positive reaction forces at the locators ensure that the workpiece maintains contact with all the locators from the beginning of the cut to the end. The clamping forces should be just sufficient to constrain and locate the workpiece without causing distortion or damage to the workpiece. Clamping force optimization is not considered in this paper.
4.2. Genetic algorithm based fixture layout optimization approach
In real design problems, the number of design parameters can be very large and their influence on the objective function can be very complicated. The objective function must be smooth and a procedure is needed to compute gradients. Genetic algorithms strongly differ in conception from other search methods, including traditional optimization methods and other stochastic methods [23]. By applying GAs to fixture layout optimization, an optimal or group of sub-optimal solutions can be obtained.
In this study, optimum locator and clamp positions are determined using genetic algorithms. They are ideally suited for the fixture layout optimization problem since no direct analytical relationship exists between the machining error and the fixture layout. Since the GA deals with only the design variables and objective function value for a particular fixture layout, no gradient or auxiliary information is needed [19].
The flowchart of the proposed approach is given in Fig. 5.
Fixture layout optimization is implemented using developed software written in Delphi language named GenFix. Displacement values are calculated in ANSYS software [24]. The execution of ANSYS in GenFix is simply done by WinExec function in Delphi. The interaction between GenFix and ANSYS is implemented in four steps:
(1) Locator and clamp positions are extracted from binary string as real parameters.
(2) These parameters and ANSYS input batch file (modeling, solution and post processing commands) are sent to ANSYS using WinExec function.
(3) Displacement values are written to a text file after solution.
(4) GenFix reads this file and computes fitness value for current locator and clamp positions.
In order to reduce the computation time, chromosomes and fitness values are stored in a library for further evaluation. GenFix first checks if current chromosome’s fitness value has been calculated before. If not, locator positions are sent to ANSYS, otherwise fitness values are taken from the library. During generating of the initial population, every chromosome is checked whether it is feasible or not. If the constraint is violated, it is eliminated and new chromosome is created. This process creates entirely feasible initial population. This ensures that workpiece is stable under the action of clamping and cutting forces for every chromosome in the initial population.
The written GA program was validated using two test cases. The first test case uses Himmelblau function [21]. In the second test case, the GA program was used to optimise the support positions of a beam under uniform loading.
5. Fixture layout optimization case studies
The fixture layout optimization problem is defined as: finding the positions of the locators and clamps, so that workpiece deformation at specific region is minimized. Note that number of locators and clamps are not design parameter, since they are known and fixed for the 3-2-1 locating scheme. Hence, the design parameters are selected as locator and clamp positions. Friction is not considered in this paper. Two case studies are given to illustrate the proposed approach.
6. Conclusion
In this paper, an evolutionary optimization technique of fixture layout optimization is presented. ANSYS has been used for FE calculation of fitness values. It is seen that the combined genetic algorithm and FE method approach seems to be a powerful approach for present type problems. GA approach is particularly suited for problems where there does not exist a well-defined mathematical relationship between the objective function and the design variables. The results prove the success of the application of GAs for the fixture layout optimization problems.
In this study, the major obstacle for GA application in fixture layout optimization is the high computation cost. Re-meshing of the workpiece is required for every chromosome in the population. But, usages of chromosome library, the number of FE evaluations are decreased from 6000 to 415. This results in a tremendous gain in computational efficiency. The other way to decrease the solution time is to use distributed computation in a local area network.
The results of this approach show that the fixture layout optimization problems are multi-modal problems. Optimized designs do not have any apparent similarities although they provide very similar performances. It is shown that fixture layout problems are multi-modal therefore heuristic rules for fixture design should be used in GA to select best design among others.
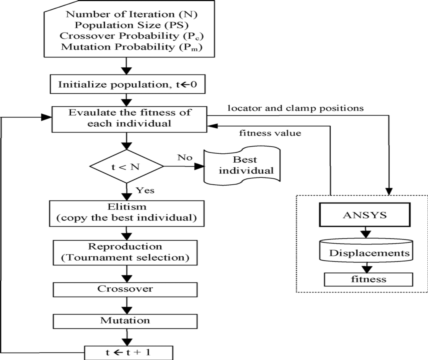
Fig. 5. The flowchart of the proposed methodology and ANSYS interface.