International Journal of Automotive Technology, Vol. 13, No. 4, pp. 615−621 (2012) Copyright © 2012 KSAE/ 065−10
DOI 10.1007/s12239−012−0059−7 pISSN 1229−9138/eISSN 1976-3832
POSSIBLE EXPERIMENTAL METHOD TO DETERMINE
THE SUSPENSION PARAMETERS IN A SIMPLIFIED MODEL OF A PASSENGER CAR
SH. LAJQI1)*, J. GUGLER2), N. LAJQI1), A. SHALA1) and R. LIKAJ1)
1)University of Prishtina, Faculty of Mechanical Engineering, Prishtina 10000, Kosovo
2)Graz University of Technology, Faculty of Mechanical Engineering, Graz 8010, Austria
(Received 14 June 2010; Revised 25 April 2011; Accepted 18 January 2012)
ABSTRACT−Currently, as well as in the past, researchers have shown great interest in developing suspension systems for vehicles and especially in the design and optimization of the suspension parameters, such as the stiffness and the damping coefficient. These parameters are considered to be important factors that have an influence on safety and improve the comfort of the passengers in the vehicle. This paper describes a simplified methodology to determine, in a quick manner, the suspension parameters for different types of passenger cars equipped with passive suspension systems. Currently, different types of passenger cars are produced with different types of suspension systems. Finding a simplified methodology to determine these parameters with sufficient accuracy would contribute a simplified and quick method to the inspection of the working conditions of a suspension system. Therefore, a simple system to determine these parameters is needed. An analysis of the suspension parameters is performed using mathematical modeling and numerical analysis conducted using the Working Model software. The result derived from the developed methodology shows small errors when compared with the generic values, and it can be concluded that the design of the suspension parameter measurement device using the developed methodology is useful, simple, and has sufficient accuracy.
KEY WORDS : Passenger car, Suspension system, Suspension parameters, Stiffness and damping coefficient
1. INTRODUCTION
of vehicles. This is a compromise between the vertical sprung mass acceleration, the suspension working space, and the dynamic tire load. When the vehicle moves over an uneven road, the vehicle is exposed to various motions and dynamic loads. The vehicle body should be well isolated from the road excitation with minimal suspension motion yet provide good handling performance.
The suspension system is the term given to the system of springs, shock absorbers and linkages that connect a vehicle body to its wheels.
The design of the vehicle’s front and rear suspension systems may be different. The springs are assumed to have almost linear characteristics while most of the shock absorbers exhibit a nonlinear relationship between the force and the velocity.
Generally, a suspension system may be categorized as apassive, a semi-active or an active system.
A passive suspension system involves the parallel mounting of the spring and the shock absorber. A passive suspension is linear in nature and is based on the principle of energy dissipation by the damper. The force acting on the vehicle body results from the relative motion and relative velocity of the suspension. A passive system does not have any control elements incorporated in the system to
improve the road vehicle comfort or road holding capability and, therefore, is cheaper to manufacture. Even though it does not fulfill all of the required conditions, this type of suspension is used in almost all types of vehicles.
The semi-active suspension system also contains a spring and a shock-absorbing device. However, the performance of these devices (stiffness and damping coefficient) can be controlled by supplying an electrical signal or other sources of external power to the system.
The active suspension system requires an external power source. Most vehicles that produce this external energy use a hydraulic actuator to generate the desired force. Despite the higher performance than vehicles equipped with an active suspension system, these systems require greater power consumption, are larger and heavier, and have high manufacturing costs, which are serious disadvantages for the use of such systems in conventional vehicles, Bouzara and Richard (2001).
2. INFLUENCE OF THE SUSPENSION SYSTEM IN VEHICLE SAFETY
A low performing suspension system can directly influence the handling performances of a vehicle, thus increasing the ability for forces from the tire to be transmitted to the vehicle body, which changes the vertical acceleration of the vehicle body, which is the main factor of rider discomfort.
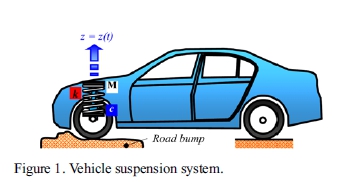
To design a well-performing suspension system, tradeoffs in the solution are required and involve the vertical acceleration of the vehicle body, the suspension working space, and the dynamic tire load, which are modulated by introducing the optimal design parameters.
There are some reports and investigations that have been performed by CITA (2010) that indicated that defects in the suspension system (mainly caused by worn shock absorbers) affect the braking performance and cornering characteristics (e.g., in lane change maneuvers). Shock absorber wear or defects can lead to a lowered damping efficiency and, hence, to greater wheel load fluctuations. The contact with the ground is, therefore, restricted, and the force transmission between the tires and the surface is limited especially on uneven or bumpy roads.
Calvo et al. (2005), in their simulation results, showed that the stopping distance of a vehicle that had worn shock absorbers increased 3% on a smooth road, whereas on an uneven road, the stopping distance increased up to 16% for the same vehicle parameters. These tendencies explain the effect of weak shock absorbers on vehicle brake performance. This is a result of the poor vertical force between the tire and road, which, in turn, dictates the maximum longitudinal force on the tire. Under such
conditions, the driving stability of the vehicle can be limited by the working conditions of the shock absorber.
Summarizing this and other driving tests performed by CITA (2010), it was found that low suspension performance affects the following driving situations:
- Lane change,
- Cornering (especially on uneven roads),
- Braking distance (especially on uneven roads),
- Braking on snow,
- Braking and cornering and
- Aquaplaning behavior.
Reduction of the damping efficiency mainly occurs over long periods of vehicle use. Determining the simplest methodology to inspect the condition of the suspension system is necessary and contributes to improving vehicle safety.
3. DETERMINATION OF THE SUSPENSION PARAMETERS USING A SIMPLIFIED SYSTEM
Determining the suspension parameters in a visual manner is almost impossible. To determine these parameters, sophisticated equipment is needed, which, in most cases, is used in technical inspections of vehicles or in laboratories, but sometimes it is necessary to more quickly determine the suspension parameters using a simple portable device.
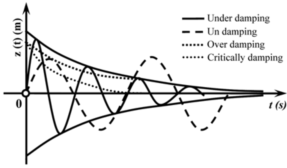
Therefore, a device should be designed that determines the suspension parameters quickly and with sufficient accuracy. Perhaps this device will be a portable one that can possibly be placed between the tire and the road.
A simplified quarter-car model is used for the analysis of these parameters. This model consists of a mass, which is connected to the tire through a spring and a shock absorber. Figure 1 shows the vehicle suspension system used to determine the vehicle’s equations of motion.
4. EXPERIMENTAL DETERMINATION OF SUSPENSION PARAMETERS
To experimentally determine the values of the suspension parameters (damping and stiffness), a passenger car was used (Opel Vectra 1.8 i) at Graz University of Technology in the Vehicle Safety Institute Laboratory. To determine the values of the spring forces and the displacement of spring,
dynamometers are fitted between the tire and road surface and measure the force. Additionally, between the center of the wheel in the front or rear axis and the vehicle body, a displacement sensor is fitted to measure the vertical displacement of the vehicle body (Figure 4).
5. CONCLUSION
To determine the suspension parameters, the values of the damping, c (Ns/m), and the stiffness coefficients, k (N/m), in an experimental manner, it is necessary to have devices that can perform measurements, such as measuring the amplitude of vibration (z1 and z2 or z1 and zn), the force, F(N), and the mass of the car, M (kg). By introducing a mobile device, the suspension parameters can be evaluated for each vehicle equipped with a passive suspension system. The error between the generic values and the WM software results for the stiffness is approximately 0.002% and for the damping the error is approximately 0.009%. The similarity of the results from the WM software and the experiment performed are, for the stiffness, 99.982% and,for the damping, 99.926%.
The displacements determined by the WM software have a micron-scale precision, and the measurements obtained in the experiments have a precision on the order of millimeters. This difference in the precision might explain why these results show this small difference, which
is allowed.
Based on these small errors, a conclusion can be drawn that the design of a device to measure the stiffness and the damping coefficients in the suspension systems in used vehicles, such as the vehicle shown here, is useful, simple and has sufficient precision.
Comparison of the values obtained from the experiments with the results that were taken from generic values (PC Crash software) for the stiffness, k (N/m), and the damping coefficient, c (Ns/m), shows that the values are different.
This difference between the two vehicles tested is considered to be the results of the analysis of the vehicle and low performance of the suspension system in the used vehicle. The values obtained are less than the suspension properties values that are considered to be soft. If the same test vehicle was used again without repairing the suspension system, the vehicle may represent a threat to the
driver’s safety.
ACKNOWLEDGEMENT−A Performed research for publication of this paper was supported by Austria Exchange .Service with program “One month stay in Austrian Universities”. Researchers are done at Graz of University Technology, Faculty of Mechanical Engineering. We are gratefully to everyone who contributes in this paper to get this form.
REFERENCES
Bouazara, M. and Richard, M. (2001). An optimization method designed to improve 3-D vehicle comfort and road holding capability through the use of active and semi-active suspension. European J. Mechanic - A/ Solids 20, 3, 509−520.
Calvo, J. A., Diaz, V., San Roman, J. L. and Garcia – Pozuelo, D. (2008). Influence of shock absorber wearing on vehicle brake performance. Int. J. Automotive
Technology 9, 4, 467−472.
CITA (2010). Performance Based Suspension Testing in PTI. Int. Motor Vehicle Inspection Committee.
Damien, M. (2011). Combined Time and Frequency Domain Approaches to the Operational Identication of Vehicle Suspension Systems. Ph. D. Dissertation. School of Mechanical and Manufacturing Engineering. Dublin City University. Dublin. Ireland. 238.
EUSAMA (1976). Recommendation for performance test specification of car vehicle suspension testing system stiffness constant. EUSAMA – TS – 02 – 76.
Jazar, R. (2009). Vehicle Dynamics: Theory and Application. Springer. New York.
Mohan, R. and Venkata, R. (2009). Parametric sensitivity analysis of heavy duty passenger vehicle suspension system. ARPN J. Engineering and Applied Sciences, Department of Mechanical Engineering, Vasavi College of Engineering, Hyderabad, India. Thomas, G. (1992). Fundamental of Vehicle Dynamics.Society of Automotive Engineering. Warrendale. 470。