摘要
变速器用于转变发动机曲轴的转矩及转速,以适应汽车在起步、加速、行驶以及克服各种道路障碍等不同条件下对驱动车轮牵引力及车速的不同要求的需要。
变速器的功用
在汽车传动系中,采用了可以改变转速比和传动转矩比的装置,即变速器。变速器不但可以扩大发动机传到驱动车轮上的转矩和转速的变化范围,以适应汽车在各种条件下行驶的需要,而且能在保持发动机转动方向不变的情况下,实现倒车,还能利用空挡暂时地切断发动机与传动系统的动力传递,使发动机处于怠速运转状态。
(1)改变传动比,扩大驱动轮转矩和转速的变化范围,以适应经常变化的行驶条件,如起步、加速、上坡等,同时使发动机在有利的工况下工作。
(2)在发动机旋转方向不变的前提下,使汽车能倒退行驶。
(3)利用空挡,中断动力传递,以使发动机能够起动、怠速,并便于变速器换档或进行动力输出。
因此变速器通常还设有倒档,在不改变发动机旋转方向的情况下汽车能倒退行驶;设有空挡,在滑行或停车时发动机和传动系能保持分离。变速器还应能进行动力输出。
两轴式变速器输出轴与主减速器主动齿轮做成一体,当发动机纵置时,主减速器可用螺旋圆锥齿轮或双曲面齿轮,而发动机横置时用圆柱齿轮,因而简化了制造工艺。
两轴式变速器,虽然可以有等于1的传动比,但是仍要有一对齿轮传动,因而有功率损失。而三轴式变速器,可以将输入轴和输出轴直接相连,得到直接档,因而传动效率高,磨损小,噪声也较小。
目前,汽车上的机械式变速器的换档结构形式有直齿滑动齿轮、啮合套和同步器换档三种。
本次设计方案一、二档和三、四档采用同步器换档,倒档使用倒档轴上滑动直齿轮换档。
倒档的形式及布置方案
本次设计采用输出轴上直齿滑动换入倒档换档方式。其优点是:结构简单,直齿轮加工要求不太高,无轴向力,成本低。但换档时容易发生冲击,产生噪声大寿命短。
变速器操纵机构方案分析
变速器操纵机构的功用是保证各档齿轮、啮合套或同步器移动规定的距离,以获得要求的档位,而且又不允许同时挂入两个档位。
变速器传动方案的设计
各齿轮副的相对安排位置,对于整个变速器的结构布置有很大的影响。各档位置的安排,应考虑以下四个方面的要求:
1、 整车总布置
根据整车的总布置,对变速器输入轴与输出轴的相对位置和变速器的轮廓形状以及换档机构提出要求。比如说是该车是采用发动机前置前驱动还是发动机前置后驱动等等,这些问题都牵连着变速器的设计方案。
2、 驾驶员的使用习惯
人们习惯于按档的高低顺序,由左到右或由右到左排列来换档,如下图b和c。值得注意的是倒档,虽然它是平常换档序列之外的一个特殊档位,然而却是决定序列组合方案的重要环节。例如在四档变速器中采用的基本序列组合方案有三种,见图2.2。其中b和c是倒档与序列不结合的方案,即挂档时,需先换位再挂倒档。倒档与序列结合与不结合两者比较,前者在结构上可省去一个拨叉和一根变速滑杆,后者如布置适当,则可使变速器的轴向长度缩短。
按习惯,倒档最好与序列不结合。否则,从安全考虑,将倒档与一档放在一起较好。
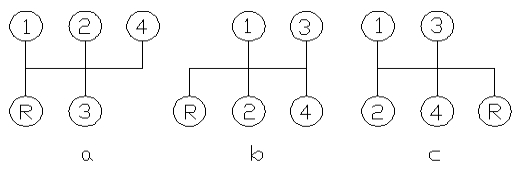
图 2.2
根据以上的要求,本次设计的档位布置方案如图2.3所示:
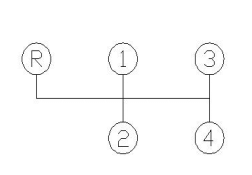
图 2.3
3、 提高平均传动效率
为提高平均传动效率,在三轴式变速器中,普遍采用具有直接档的传动方案,并尽可能地将使用时间最多的档位实际成直接档。
4、 改善齿轮受载状况
各档齿轮在变速器中的位置安排,应考虑齿轮的受载状况。承受载荷大的低档齿轮,一般安置在离轴承较近的地方,以减小轴的变形,使齿轮的重叠系数不致下降过多。变速器齿轮主要是因接触应力过高而造成表面点蚀损坏,因此将高档齿轮安排在离两支承较远处较好。该处因轴的变形而引起齿轮的偏转角较小,故齿轮的偏载也小。
本次设计传动方案如图2.3所示
传动路线:
Ⅰ档:一轴→1→2→中间轴→8→7→二轴→5、7齿轮间的同步器→输出
Ⅱ档:一轴→1→2→中间轴→6→5→5、7齿轮间的同步器→二轴→输出
Ⅲ档:一轴→1→2→中间轴→4→3→1、3齿轮间同步器→二轴→输出
Ⅳ档:一轴→1→1、3齿轮间同步器→二轴→输出
R档:一轴→1→2→中间轴→10→11→9→二轴→输出
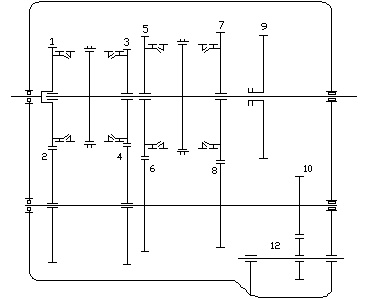
图2.4
齿轮精度的选择
根据推荐,提高高档位齿轮的性能,取Z1~Z4为6级,Z5~Z11为7级。
材料选择
现代汽车变速器的齿轮材料大部分采用渗碳合金钢,其表层的高硬度与心部的高韧性相结合,能大大提高齿轮的耐磨性及抗弯曲疲劳和接触疲劳的能力。本次设计的齿轮的材料选用40Cr。
齿轮的损坏形式
变速器齿轮的损坏有以下几种形式:
(1)轮齿折断
(2)齿面点蚀
(3)齿面胶合
2、圆柱齿轮强度的简化计算方法
(1)接触强度计算
用下列公式计算接触应力
(N/mm2) (3.21)
式中:
——法面内基圆周切向力,
=
;
——端面内分度圆切向力,
=
;
——计算转矩,N•mm;
——节圆直径;
——节圆压力角;
——螺旋角;
——轮齿材料的弹性模量;
——齿轮接触的实际宽度;
、
——主、被动齿轮节圆处齿廓曲率半径;
=
,
=
;
、
——主、被动齿轮节圆半径;
计算转矩
=
时的许用应力为:
常啮合齿轮:1300~1400 MPa
一档及倒档齿轮:1900~2000 MPa
这里
是发动机最大转矩。
(2)弯曲强度计算
直齿轮用下式计算弯曲应力:
=
(MPa) (3.22)
斜齿轮用下列公式计算:
=
(MPa) (3.23)
式中:
——圆周力,
=
,N;
——应力集中系数,直齿轮取1.65,斜齿轮取1.5;
——摩擦力影响系数,主动齿轮取1.1,被动齿轮取0.9;
b ——齿面宽
——端面周节,
=
;
——法面周节,
=
;
——齿形系数;
——重合度影响系数,
=2.0。
许用应力为400-850 MPa(直齿轮),倒档齿承受双向交变载荷作用,取下限;100-250 MPa
参考文献
[1]陈家瑞.汽车构造(下册)第2版.北京:机械工业出版社,2005年1月
[2]王望予.汽车设计 第4版. 北京:机械工业出版社,2004年8月
[3]龚微寒.汽车现代设计制造.北京:人民交通出版社,2002年5月
[4]高维山 主编.汽车设计丛书《变速器》.北京:人民交通出版社.2001年1月
[5] 濮良贵、 纪名刚主编 .机械设计 第八版. 北京:高等教育出版社,2006年5月
[6]实用机械设计手册编写组编.实用机械设计手册 (上册)第2版.北京:机械工业出版社,1994年1月